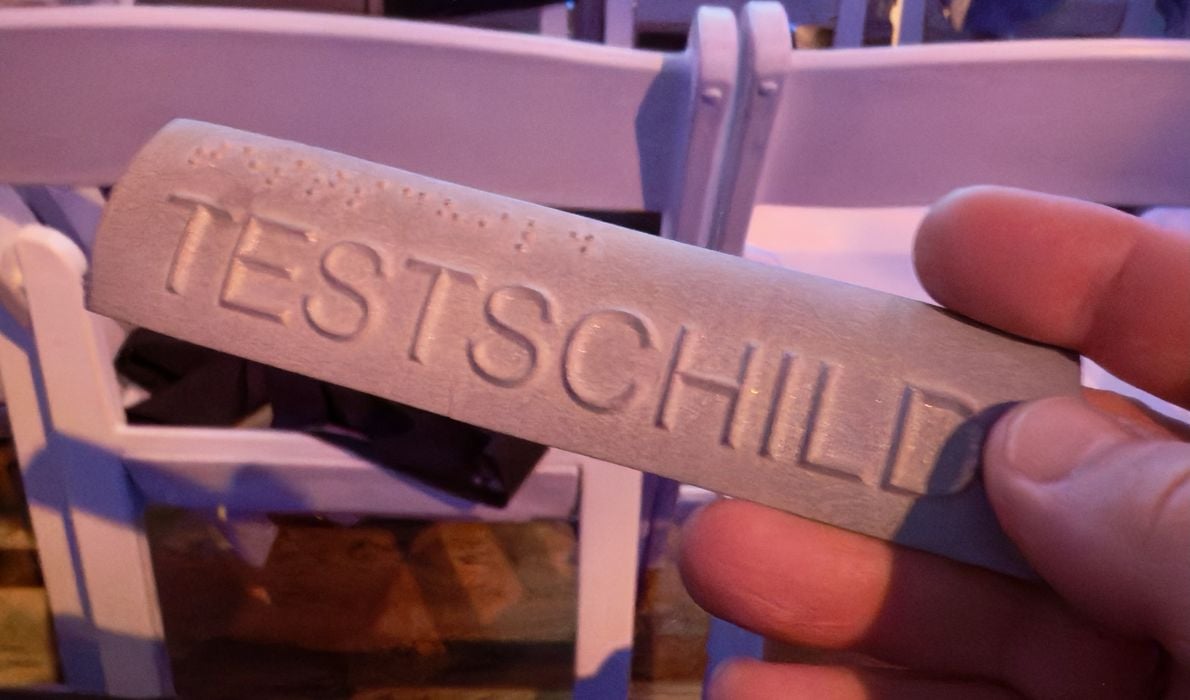
Digital inventory is a goal sought by many large organizations, but is anyone succeeding?
It turns out at least one major company is doing so. I heard a talk at AMS 2025 from Stephanie Brickwede, the Head of Additive Manufacturing at Deutsche Bahn. If you’re not familiar with “DB”, they are the railway in Germany, operating hundreds of trains daily.
But what is a digital inventory? It’s a new concept that is largely enabled by additive manufacturing. In the past, companies like DB would have to maintain vast warehouses of spare parts at great expense.
This is because of manufacturing constraints. Imagine a new rail car is produced. The factory lines that make the parts for this car are set up, and enough parts to make the required number of cars. However, the lines also produce a quantity of spare parts before they are taken down, and this is where the inventory comes from.
Once the lines are gone, it is extremely difficult and expensive to produce the same spare parts. Now consider that the rail car that was just produced is intended to operate for, say, 40 years.
DB would have to stock 40 years’ worth of spare parts for that specific rail car model.
It’s even worse: the next year, a different rail car model is produced, which ALSO requires 40 years of spare parts.
If this isn’t bad enough, the goal is to ensure there is always a spare part available during the lifetime of the car. This means that there will inevitably be many spare parts that are never used, even though they were stored for decades.
Physical inventories are ridiculously expensive for many large organizations.
Enter digital inventory: some of those parts can be 3D printed, so why not print them on demand and simply store the digital files instead? That’s a digital inventory.
The approach works for any part that can be 3D printed, and there’s some work required to identify which parts are relevant. Older parts may not even have a digital design file, so that’s also a huge problem.
Moving to a digital inventory, while financially attractive, is an enormous amount of work. Nevertheless, DB has been pursuing this goal for quite a while now, and they have achieved significant results.
According to Brickwede, DB is now saving “in the two-digit million range”. That’s quite notable.
DB started digitizing their spare parts inventory in 2015, with only ten parts. By 2024, they have 150,000 digitized parts, produced in twelve different AM technologies for 700 different applications.
At the top you can see one of them: it’s a physical label that is pasted on bars inside passenger rail cars. This part is easily 3D printed and can be produced on demand.
The digital inventory has made DB a bit more nimble in their future designs, as they can take advantage of 3D print technology. Brickwede explained that new part designs can adopt radically new designs that reduce material consumption, and eliminate joints. She stated that it might be possible to reduce the weight of car bodies by as much as 40%.
That would have benefits far beyond spare part handling, as the amount of energy required to pull lightweight trains would be substantially reduced.
Digital inventory clearly requires a massive amount of work to implement, but the benefits are very significant. Today we still see the old style of physical spare part inventories everywhere, but I’m hopeful that new products will increasingly adopt digital inventory approaches.