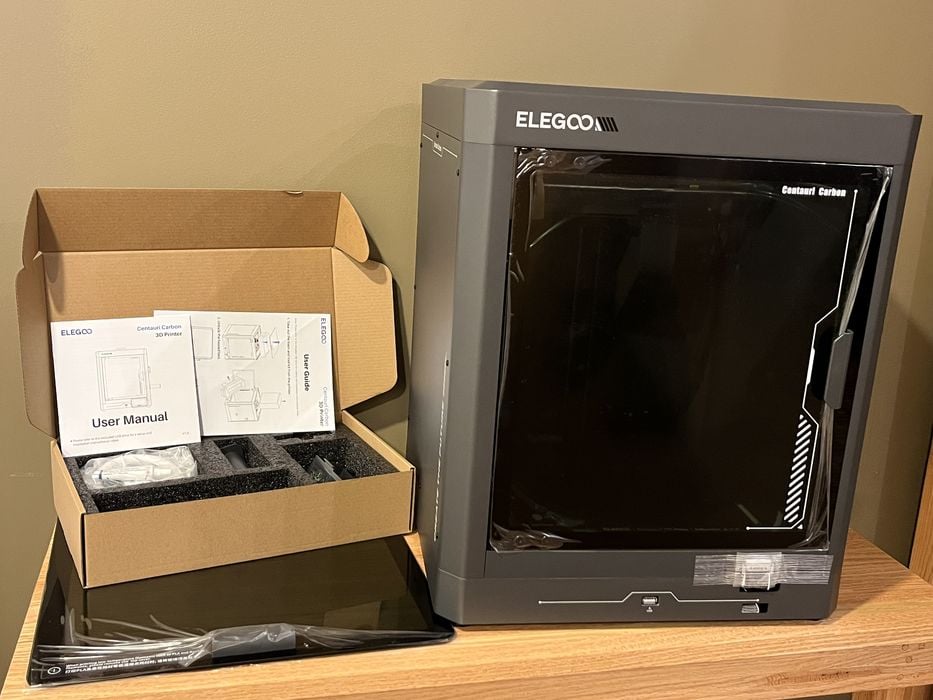
We’re testing the brand-new Elegoo Centauri Carbon desktop 3D printer.
This is part one of a three-part series; please read parts two and three.
Elegoo Centauri Carbon Background
Founded in 2015 in China’s Silicon Valley, Shenzhen, Elegoo has been busy designing and manufacturing both resin and FFF printers in its FFF line. The Centauri Carbon is their latest release and is positioned to compete against several similar enclosed, high-speed CoreXY devices on the market.
The new Centauri Carbon includes some rather fancy capabilities, and we were quite excited to learn that they were sending one over to our lab for us to test.
Elegoo Centauri Carbon Specifications and Features
The Centauri Carbon marks Elegoo’s entry into the CoreXY domain of 3D printing, following several other high-profile product launches by other competitors. Elegoo has packed quite a few features into the 398 x 404 x 490 mm enclosure, which weighs in at a somewhat hefty 17.5 kg. As this device is enclosed, it is heavier than open gantry machines, which seem to be rapidly going out of style.
The beefy chassis of the printer is built with integrated die-casting featuring four reinforced aluminum alloy pillars with attached SPCC side panels, making the build quite solid. There’s a lot of metal in this machine, partly explaining the weight.
The Elegoo Centauri Carbon arrives mostly prebuilt, with minimal assembly required from the operator.
The build area of the Elegoo Centauri Carbon is decently sized at 256 x 256 x 256 mm, quite similar to competitive machines of this class.
The build chamber comes equipped with a temperature regulator fan, an auxiliary part cooling fan, and “Nano-Mineral Crystal Filters” air filtration.
The enclosure isn’t actively heated, but can reach ambient temps of up to 40°C during a print, if you seal it with the hinged door and removable top cover – both of which are crafted from durable tempered glass. Additionally, there is a camera & light to help with keeping an eye on the progress of a print job, or to create fun timelapse videos.
The timing belts for the X, Y, and Z axes all feature a semi-automatic belt tensioning mechanism, ensuring consistent belt tension as components age. A built-in accelerometer allows for vibration compensation, which is then paired with pressure compensation, ensuring stable and smooth extrusion for each and every print.
The heated print bed can reach temps of up to 110C and uses a double-sided flexible magnetic build plate with standard textured PEI on one side and a low temp PLA-specific surface on the other — what’s often referred to as a “cold plate”.
To assist with calibration and the all-important first print layer, this 3D printer employs “4-Strain Gauge Automatic Leveling” in combination with checking a huge 121 points across the surface of the build plate to increase levelling accuracy.
The Centauri Carbon’s stock hot end is a single 0.4mm brass & hardened steel nozzle (above 60HRC) and can reach a maximum operating temperature of 320C via a 60W ceramic heater. This is combined with a hardened steel dual-gear extruder with a reduction ratio of 5.2.
A robust 5020 high-speed model fan helps out with the important task of quickly cooling extruded filament. All of this allows for a printing accuracy of ±0.1mm and layer thickness of 0.1-0.4 mm (Elegoo recommends 0.2 mm).
For filament compatibility, Elegoo recommends 1.75mm PLA, PETG, TPU, ABS, ASA & PLA-CF, but they also mention that the Centauri Carbon is compatible with PETG-CF, ABS-CF, ASA-CF, PET-CF, PA-CF, PET, PC & PA, giving the printer a very large range for materials, including many engineering materials. This could make the Centauri Carbon useful in a professional environment.
For filament management, there is an automated filament cutter on the extruder, a rear waste purge bin, and a silicon nozzle cleaning brush station – all working together to make filament changes quick and easy.
For your convenience, the spools attach to the right-hand side of the printer, instead of in the back of the Elegoo Centauri Carbon as is often the case, and a filament run-out sensor is included so print failures don’t occur due to an empty spool. Side-mounted spools are becoming more popular because operators really don’t want to reach around the back of the machine, which in some setups is awkward.
The brains of the printer is a dual-core high-speed motherboard with silent stepper drivers, which is controlled via a 4.3” full-color capacitive touch LCD screen. Connectivity choices include direct USB stick or WiFi. Over-the-air firmware updates are possible, and there is the ability to recover after a power loss.
Last but not least, there is the speed of the printer itself, which Elegoo boldly advertises as being 500mm/s for print speed and 20,000 mm/s for acceleration.
Print speeds like these are only for PLA and are typically not included in any factory-supplied slicing profiles. As you will see ahead, the speeds provided in supplied slicing profiles are much more modest than the advertised speeds, which are left for an operator to experiment with.
Elegoo Centauri Carbon Unboxing and Assembly
Like most 3D printers these days, the Centauri Carbon ships in a sturdy cardboard box, which in our case arrived safe and sound with no visible damage. It seems that 3D printer manufacturers have mostly figured out how to safely ship equipment, and we now very rarely see shipping damage.
Opening the box, we were greeted by a friendly message printed directly onto the cardboard box inner flaps that kindly suggested that we keep the box and packaging, “Just In Case”.
We found the printer’s delicate glass lid carefully nestled into the first layer of soft foam packing. Below that, we found the entire chassis of the printer packed tightly into a large sealed poly bag, which we found very convenient to grab and lift up and out of the box, all in one go.
We removed the printer from the bag and pulled several pieces of foam packing out from the enclosure. These bits of foam had worked well to keep the XY axes from moving around during the various bumps and jostles of shipping. We also found a small cardboard box full of goodies.
We placed the printer onto our work table and emptied the contents of the goodie box beside it, spreading everything out on the table surface to have a good look.
There was an LCD touchscreen, power cord, filament spool holder, a few screwdrivers and Allen wrenches, a needle for clearing the nozzle, a scraper blade, nozzle wiper, grease for lubricating the printer, and a USB drive.
Also included was the user manual and a quick start user guide that showed how to unbox and set up the printer – which would have been handy to have been included on the first layer of the box, instead of being buried deeper in the box.
Curiously missing was the typical small pair of cutters used to prepare the filament for loading, often found with other 3D printers.
The first instruction in the user manual was actually in the form of a QR code, which we made sure to check out. It turned out to be a great little YouTube video showing the unboxing and setting up of the printer.
Again, it would’ve been quite handy if that had been on the first layer of foam, or even better if the code had been printed on the inner flaps of the shipping box.
The video gave much more concise instructions compared to the user manual and showed a few things that weren’t even included in the manuals, such as clipping and removing a zip tie from around the extruder assembly and removing a small piece of foam from the purge bin, but these were fairly intuitive tasks.
In addition to the items mentioned above, there wasn’t much to do with assembling the printer. We removed three well-marked screws to unlock the Z-axis. A piece of tape was removed, exposing a small ribbon cable for attaching the LCD screen, which we did before clipping the screen firmly into place on the front of the printer.
After that, we twisted a filament spool holder into a hole on the right side of the Elegoo Centauri Carbon.
The final thing we did was to check for and remove any protective films on glass— always a satisfying process.
With the influx of enclosed machines with walls, we’re doing a lot more peeling these days.
This is part one of a three-part series; please read parts two and three.
Via Elegoo