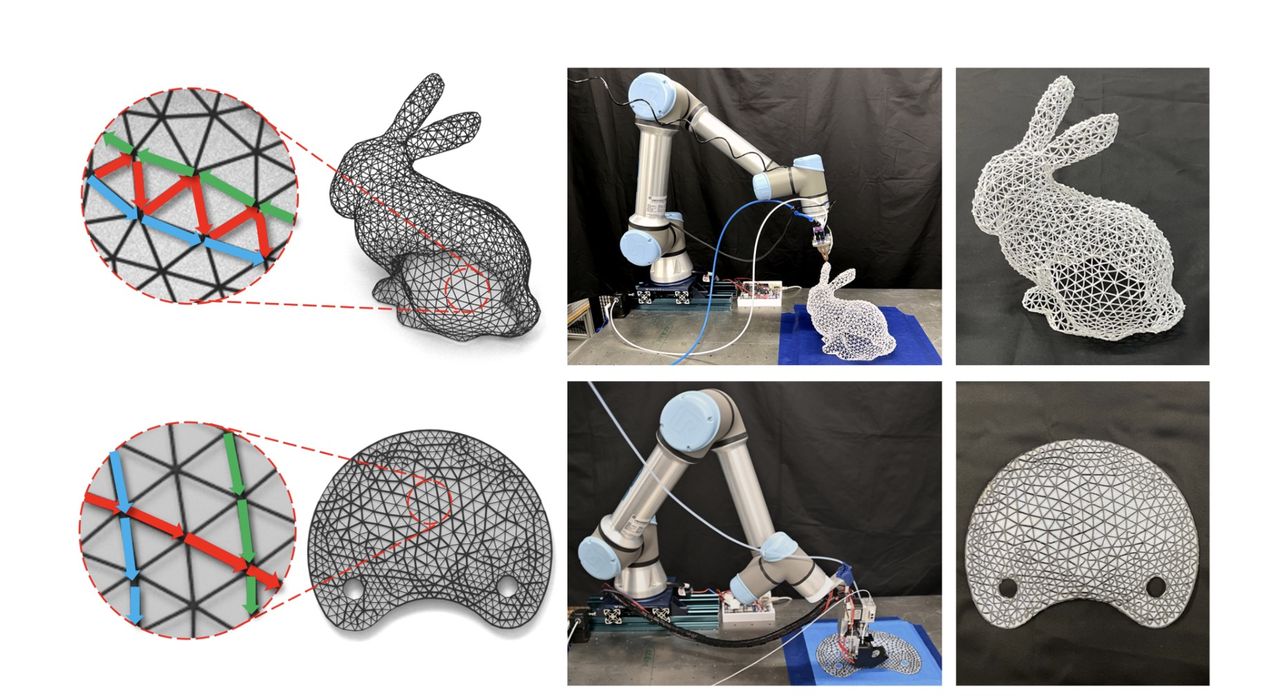
Continuous carbon fiber 3D printing may become a lot more powerful if new research is adopted by industry.
Researchers at the University of Manchester have developed a new approach to create toolpaths for 3D printing using graphs, and it turns out this could improve toolpaths for continuous carbon fiber 3D printing, among other benefits.
Continuous carbon fiber 3D printing is a niche capability current provided by only a small handful of providers. That’s because it’s hard to do. Not only does the 3D printer have to include a separate toolhead to lay down lines of continuous carbon fiber, but the software must generate toolpaths for those lines.
That is usually quite complex, as the few strands of carbon fiber must be in proper orientations to provide optimal strength. For example, if there’s a corner to be printed, should the carbon fiber be two separate strands that happen to meet at 90 degrees? Or perhaps it would be better to have a continuous fiber that gradually curves within that corner? The latter is the correct answer, but how do you detect those geometric situations and generate appropriate carbon fiber toolpaths?
The researchers used an undirected graph approach. They explain:
“Many 3DP problems can be formulated as finding an optimized path to visit nodes and edges on an undirected graph, which contains a set of edges and a set of nodes. Printing toolpaths are planned to go through all nodes while optimizing different manufacturing objectives. The resultant toolpath is represented as an ordered list of nodes, where their coordinates indicate the tip point of a printer head and their order gives the printing sequence.”
Their solution involves an on-the-fly local search graph, where the optimal choice is determined through iteration.
This is quite interesting, as their solution apparently involves different “reward functions” that associate with specific manufacturing objectives. In other words, you can tell the algorithm what you need to achieve and it should find the optimal toolpath.
Their solution was applied to the problem of continuous carbon fiber toolpaths, with a view to reduce carbon fiber usage while maintaining part strength. For this, the objectives were:
Coverage: Each edge of the input graph must be fabricated by one to two passes of CCF deposition while minimizing total material usage
Continuity: All passes are continuously connected – i.e., the whole graph can be covered by CCF in ‘one-stroke’
Sharp-turn: The CCF toolpath should avoid sharp turns
As you can imagine, these objectives would certainly provide far better carbon fiber deposition than more simple approaches. I’m hoping this research can be integrated with exiting continuous carbon fiber systems to optimize their output.
The graph-based toolpath approach was also demonstrated in two other areas. One was metal 3D printing using the LPBF process. The idea was to manage thermal stresses, which, if not accounted for, can introduce severe distortions and even cracks in metal prints.
This research tells me that today’s “advanced” slicing software is nowhere near reaching the fullest potential. Research of this type, combined with recent AI tools should at some point revolutionize 3D print slicing software, and enable everyone to print optimized parts in each and every job.
Via ArXiv