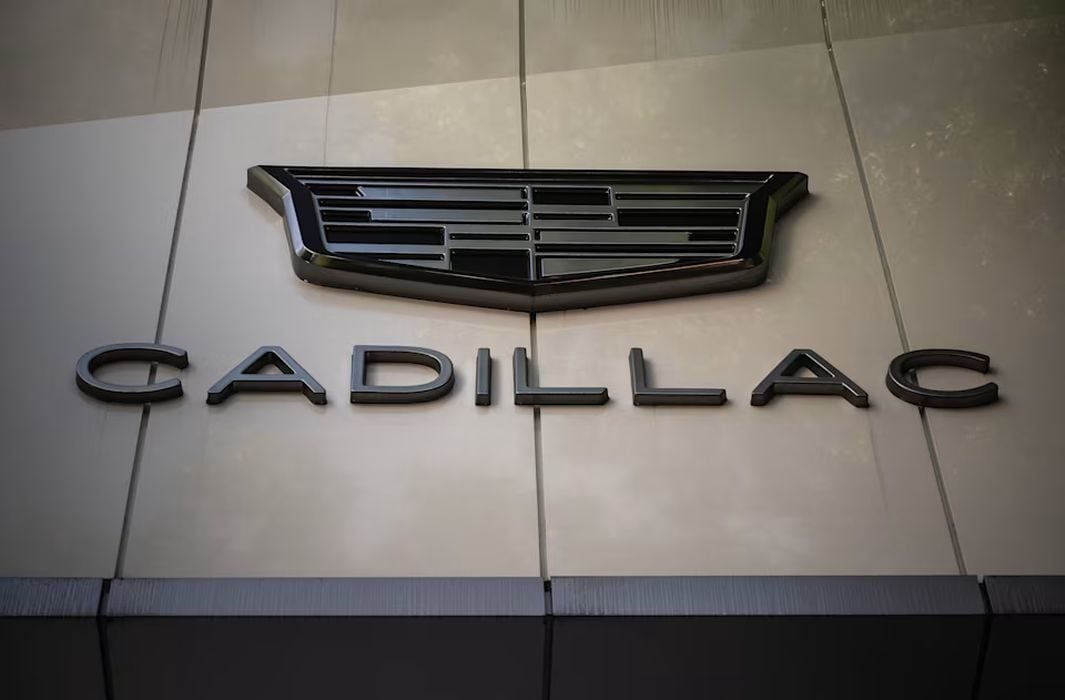
Charles R. Goulding and Preeti Sulibhavi explore Cadillac’s strategic entry into Formula 1, revealing how the automaker’s innovative use of 3D printing is transforming both its racecars and production vehicles.
Cadillac’s recent approval to join the Formula 1 (F1) grid in 2026 marks a significant milestone for both the brand and the sport. This entry not only underscores Cadillac’s commitment to motorsport but also highlights the increasing integration of advanced manufacturing techniques, such as 3D printing, in automotive design and production. The synergy between Cadillac’s F1 ambitions and its innovative use of 3D printing in models like the Celestiq and Blackwing series exemplifies the brand’s forward-thinking approach.
Cadillac’s Entry into Formula 1
After a rigorous evaluation process, Cadillac, backed by General Motors (GM) and TWG Motorsports, received official approval to become the 11th team on the F1 grid in 2026. This decision reflects F1’s expansion strategy and the growing interest in the sport within the United States. The success of recent U.S. Grand Prix events in Miami, Austin, and Las Vegas has demonstrated a robust American fan base, making Cadillac’s entry timely and strategic.
To support its F1 endeavors, Cadillac is investing in three key locations:
- Indiana, USA: A new facility is under construction in Fishers, near Indianapolis, which will serve as one of the primary operational bases for the F1 team.
- Silverstone, England: Recognizing the UK’s rich motorsport heritage, Cadillac is establishing a facility adjacent to the iconic Silverstone Circuit. This location will facilitate collaboration with European partners and provide access to a vast talent pool.
- Concord, North Carolina, USA: An US$85 million engine factory is planned near the Charlotte Motor Speedway. This facility will focus on developing and manufacturing power units, aligning with Cadillac’s goal to become a “full works” team by the end of the decade.
Initially, Cadillac will utilize Ferrari power units but aims to develop proprietary engines as its facilities become operational.
This phased approach ensures competitiveness while internal capabilities are being established.
3D Printing in Cadillac’s Production Models
Cadillac’s commitment to innovation is evident in its adoption of 3D printing technologies across various models, enhancing design flexibility, reducing weight, and streamlining production processes.
Cadillac Celestiq
The Celestiq stands as a testament to Cadillac’s dedication to craftsmanship and technology. This luxury electric sedan integrates 115 3D printed components, marking GM’s most extensive use of additive manufacturing in a production vehicle. Notable 3D printed parts include:
- Steering Wheel Center: Produced using metal laser powder bed fusion (LPBF), this component is the largest metal part GM has printed for a production vehicle.
- Window Switches and Grab Handles: These polymer parts showcase the customization potential of 3D printing, allowing for intricate designs and rapid prototyping.
- Structural Seatbelt D-Rings: Significantly, these are GM’s first 3D printed safety-related parts, underscoring the reliability and strength achievable with additive manufacturing.
Additionally, the Celestiq’s production leverages one of the world’s largest sand 3D printers for casting car parts, highlighting GM’s investment in cutting-edge manufacturing technologies.
Blackwing Models (CT4-V and CT5-V)
The Blackwing variants of the CT4-V and CT5-V models represent Cadillac’s performance-oriented lineup, where 3D printing has been strategically employed to enhance vehicle capabilities:
- HVAC Ducts: Two nylon-12 HVAC ducts are 3D printed, contributing to optimized airflow and reduced component weight.
- Electrical Harness Bracket: An aluminum bracket used to secure a wiring harness is 3D printed, exemplifying the functional applications of additive manufacturing in structural components.
These applications in the Blackwing models highlight Cadillac’s ability to integrate advanced manufacturing techniques to achieve performance enhancements and design efficiencies.
Implications for the Automotive Industry
Cadillac’s integration into F1 and its pioneering use of 3D printing reflect broader trends in the automotive industry:
- Technological Synergy: Participation in F1 serves as a catalyst for technological advancements, with innovations often trickling down to consumer vehicles. Cadillac’s F1 involvement is expected to accelerate the development of new materials, aerodynamic designs, and energy-efficient technologies applicable to its commercial lineup.
- Manufacturing Evolution: The extensive use of 3D printing in models like the Celestiq sets a precedent for the industry, demonstrating the feasibility of additive manufacturing for both aesthetic and structural components. This approach can lead to reduced production times, cost savings, and the ability to offer personalized features to consumers.
- Economic Considerations: The establishment of new facilities in the U.S. aligns with current tariff environments that favor domestic production. Investments in states like Indiana and North Carolina not only bolster local economies but also position Cadillac to navigate global trade dynamics more effectively.
In light of the recent Trump tariffs, President Trump and GM CEO, Mary Barra, met in March to discuss the automaker’s investment plans amid this “trade war.” The result of this meeting included exempting compliant automakers from tariff hikes and GM investing about US$60 billion in additional US plants for production.
The Research & Development Tax Credit
The now permanent Research and Development (R&D) Tax Credit is available for companies developing new or improved products, processes and/or software.
3D printing can help boost a company’s R&D Tax Credits. Wages for technical employees creating, testing and revising 3D printed prototypes are typically eligible expenses toward the R&D Tax Credit. Similarly, when used as a method of improving a process, time spent integrating 3D printing hardware and software can also be an eligible R&D expense. Lastly, when used for modeling and preproduction, the costs of filaments consumed during the development process may also be recovered.
Whether it is used for creating and testing prototypes or for final production, 3D printing is a great indicator that R&D Credit-eligible activities are taking place. Companies implementing this technology at any point should consider taking advantage of R&D Tax Credits.
Conclusion
Cadillac’s forthcoming entry into Formula 1 and its innovative application of 3D printing in production vehicles underscore the brand’s commitment to technological advancement and performance excellence. By investing in state-of-the-art facilities and embracing additive manufacturing, Cadillac is poised to influence the future trajectory of automotive design and engineering. As the 2026 F1 season approaches, enthusiasts and industry stakeholders alike will be keenly observing how these strategic initiatives translate into on-track success and consumer-ready innovations.