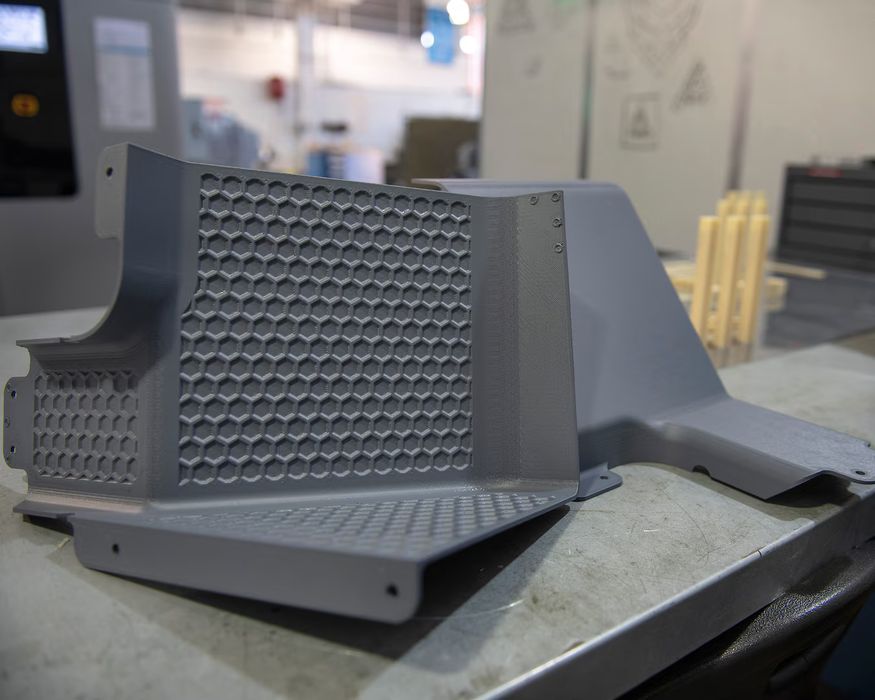
Charles R. Goulding and Preeti Sulibhavi explore how the convergence of aircraft recycling and 3D printing is driving sustainability and efficiency in the aerospace industry.
As global air travel continues to grow, the aerospace industry faces a complex set of challenges, including production constraints and supply chain disruptions. These challenges have fueled demand for replacement parts to keep existing aircraft operational, particularly as new aircraft production struggles to meet rising demand. According to Ron Epstein, senior aerospace analyst at Bank of America Securities, recent opportunities in the industry have shifted from producing new planes to supplying parts, particularly from retired aircraft.
This shift has created a booming market for recycling retired airplanes, with aircraft being dismantled to recover valuable components before the remains are scrapped. Additionally, 3D printing is emerging as a transformative tool for the aerospace maintenance, repair, and operations (MRO) sector, providing cost-effective and efficient solutions for replacement parts and new designs.
The Lifecycle of Retired Aircraft
Aircraft retirement is a growing phenomenon as fleets age and are replaced by newer, more fuel-efficient models. Each year, hundreds of aircraft are retired globally, and the dismantling of these planes provides critical data about the value and usability of their parts.
- Retired Aircraft Statistics: Approximately 600 to 700 aircraft are retired annually, depending on market conditions. These include a mix of narrow-body planes like the Boeing 737 and Airbus A320 and wide-body aircraft such as the Boeing 777 or Airbus A330.
- Recycling Economics: The value of a retired aircraft can vary widely, with typical sale prices ranging from US$500,000 to US$3 million, depending on the condition and type of aircraft. For example, an older Boeing 747 might fetch around US$1.5 million before being dismantled, primarily due to the value of its engines and other high-demand components.
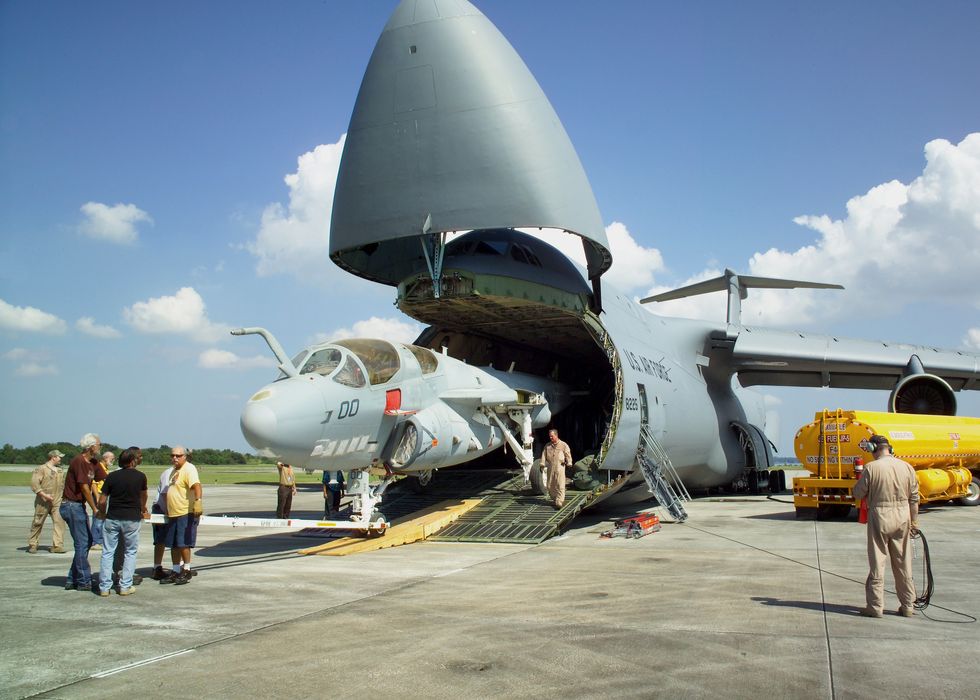
Categories and Value of Aircraft Parts
An aircraft contains thousands of parts, many of which hold significant value even after the plane is decommissioned. Broadly, these parts fall into three categories:
- High-Value Parts
- Engines: Aircraft engines are among the most valuable components, often making up over 70% of the value of a retired plane. A single engine from a Boeing 777, for example, can sell for US$3 million to US$6 million, depending on its condition and remaining service life.
- Landing Gear: The complex and robust systems that allow planes to take off and land safely are also in high demand, with prices ranging from US$500,000 to US$1 million per set.
- Moderately Valuable Parts
- Avionics: Electronic systems such as navigation and communication equipment can fetch high prices, especially for modernized systems compatible with newer aircraft.
- Cabin Interiors: While seats themselves hold limited value on the secondary market, high-end cabin elements such as premium seats, galleys, and lavatory modules can be repurposed or refurbished for other planes.
- Low-Value or Non-Reusable Parts
- Standard Seats: Economy-class seating often has limited resale value due to wear and customization issues. However, the advent of 3D printing has enabled manufacturers to design and produce lightweight, ergonomically optimized seats for new aircraft.
- Structural Components: While the aluminum or composite fuselage might not fetch high prices as a whole, these materials are often recycled as scrap metal, fetching US$500 to US$1,500 per ton.
The Role of 3D Printing in Aircraft Recycling and Replacement
As the MRO market grows, 3D printing is becoming a critical technology for addressing the high demand for replacement parts. The following highlights how additive manufacturing is reshaping the industry:
Cost-Effective Part Replacement
The high prices for new parts in the MRO market present opportunities for 3D printed replacements. For example:
- Cabin Components: Additive manufacturing is already being used to produce lightweight cabin interiors, such as armrests, tray tables, and seat frames. These parts meet regulatory requirements while offering weight savings that enhance fuel efficiency.
- Tooling and Prototyping: 3D printing is invaluable for creating tools and prototypes for repairs, accelerating the maintenance process and reducing costs.
Customization and Rapid Production
Unlike traditional manufacturing, 3D printing allows for rapid production of custom parts tailored to specific aircraft models or operational needs. For instance:
- Specialized Fixtures: Components such as brackets, ducts, and covers can be produced on-demand, minimizing downtime for airlines.
- Engine and Structural Parts: While regulated and requiring certification, some non-critical engine components and structural reinforcements are now being 3D printed.
Regulatory Challenges
The aerospace industry is heavily regulated, and parts critical to flight safety, such as engine components and landing gear, must meet stringent certification requirements. While 3D printing technology has advanced significantly, its use in these categories remains limited to approved applications. However, as certification processes evolve, the role of 3D printing in producing flight-critical components is expected to grow.
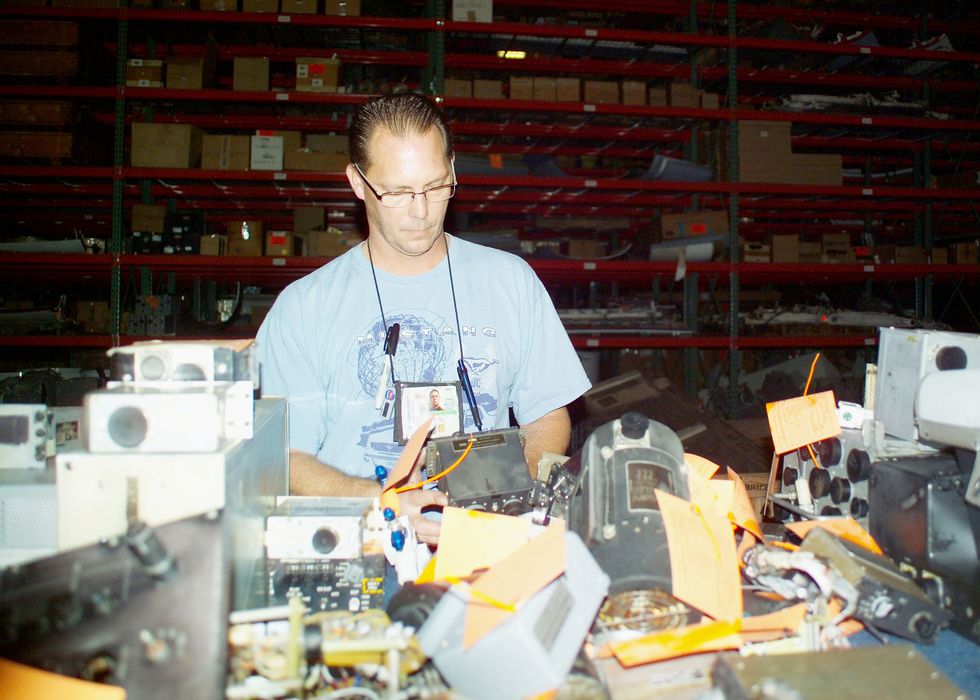
Recycling and 3D Printing Synergy
The overlap between aircraft recycling and 3D printing lies in their shared goal of sustainability and efficiency.
- Material Recovery: Recycled materials from retired aircraft, such as aluminum and titanium alloys, can be used as feedstock for additive manufacturing, closing the loop in the production cycle.
- Future Innovations: By analyzing data from retired aircraft, 3D printing can be used to produce parts that address common wear-and-tear issues, enhancing durability and performance.
The Research & Development Tax Credit
The now permanent Research and Development (R&D) Tax Credit is available for companies developing new or improved products, processes and/or software.
3D printing can help boost a company’s R&D Tax Credits. Wages for technical employees creating, testing and revising 3D printed prototypes are typically eligible expenses toward the R&D Tax Credit. Similarly, when used as a method of improving a process, time spent integrating 3D printing hardware and software can also be an eligible R&D expense. Lastly, when used for modeling and preproduction, the costs of filaments consumed during the development process may also be recovered.
Whether it is used for creating and testing prototypes or for final production, 3D printing is a great indicator that R&D Credit-eligible activities are taking place. Companies implementing this technology at any point should consider taking advantage of R&D Tax Credits.
Conclusion: A Dynamic Future for Aerospace
The convergence of aircraft recycling and 3D printing underscores the adaptability of the aerospace industry to changing market dynamics. As new airplane production normalizes, the high demand for used parts and the recycling of retired planes may decline. However, 3D printing is positioned to remain a cornerstone of innovation in the sector, enabling efficient and cost-effective solutions for both existing and next-generation aircraft.
By leveraging these technologies, the aerospace industry can optimize its resources, improve sustainability, and address evolving market conditions, ensuring its continued growth and relevance in a rapidly changing world.