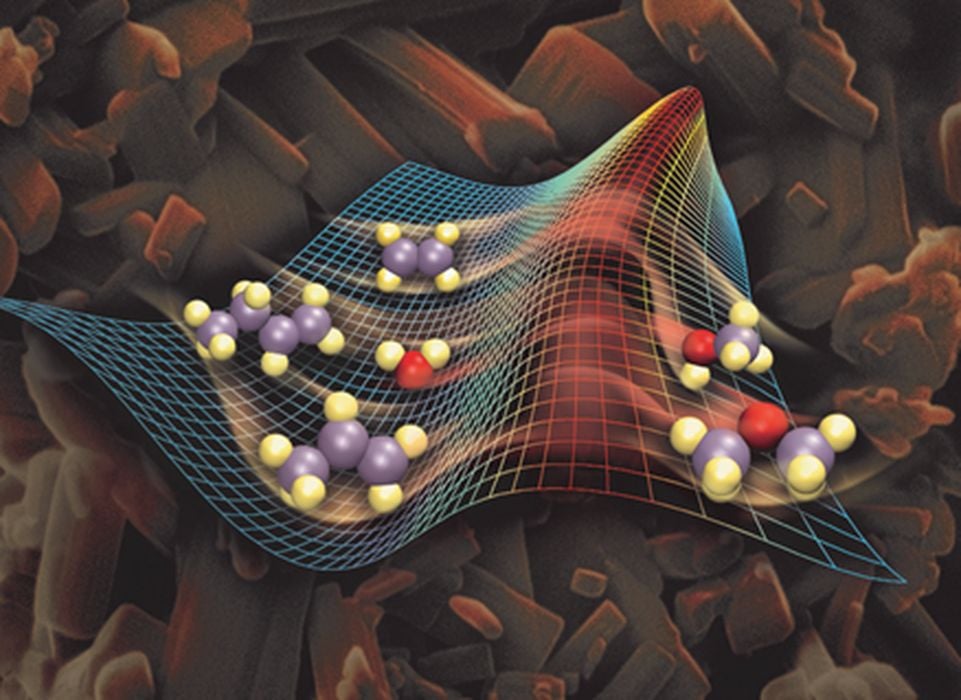
Charles R. Goulding and Andressa Bonafe explore how 3D printing is revolutionizing catalyst design, driving advancements in efficiency, sustainability, and R&D opportunities across industries.
Catalysts are substances that accelerate a chemical reaction or reduce the necessary temperature or pressure to initiate it without being consumed or permanently altered in the process. In a chemical reaction, bonds within molecules are disrupted, rearranged, and rebuilt, leading to the formation of new molecules. Catalysts enhance this process by decreasing the activation energy, which is the energy threshold that must be crossed for a reaction to occur. Lowering this barrier facilitates the breaking and forming of chemical bonds, making it easier to produce new substances.
The use of catalysts results in faster and more energy-efficient reactions. Their selectivity also helps to steer reactions toward producing a higher yield of the desired product while minimizing the formation of unwanted byproducts. This ability to generate new materials with innovative applications is transformative. In fact, over the past several decades, catalysts have become essential in various fields. They are employed to optimize chemical production processes, such as the Haber process for synthesizing ammonia and catalytic cracking for refining crude oil into valuable products. They are also critical for environmental protection, notably in catalytic converters used in vehicles, which help reduce harmful emissions such as carbon monoxide and nitrogen oxides. Moreover, catalysts are important in pharmaceutical manufacturing, as they aid in the efficient synthesis of complex compounds and drugs. In recent decades, significant advancements have been made in the development of highly specialized catalysts, which enable the creation of biodegradable plastics, ground-breaking therapeutics, and more environmentally friendly fuels and fertilizers.
Catalysts and 3D Printing
3D printing is revolutionizing the design and production of catalysts by enabling the creation of complex and precise structures that were previously unattainable. While traditional methods, such as extrusion and pelletizing, often limit the shape and form of catalysts, 3D printing overcomes these limitations, allowing for the optimization of catalyst properties, including activity and selectivity. This technology facilitates the fabrication of catalysts with intricate geometries that maximize the surface area and enhance both the mass and heat transfer, leading to improved catalytic performance.
One of the significant advantages of 3D printing in catalyst design is the ability to create hierarchical structures with multiple levels of porosity. These structures can mimic natural catalytic environments, such as those found in enzymes, leading to enhanced reaction rates and selectivity. For example, catalysts with macro-, meso-, and micropores can be designed to facilitate the diffusion of reactants and products, reducing diffusion limitations and improving overall catalytic efficiency. This level of control over the catalyst architecture is challenging to achieve with conventional manufacturing techniques. Furthermore, 3D printing allows for the precise placement of active sites within the catalyst, ensuring uniform distribution and optimal performance.
[Source: Richard P. Feynman Center for Innovation]
Another exciting opportunity in the additive manufacturing of catalysts is the integration of multiple functions into a single structure, which streamlines production processes and reduces costs. By leveraging the flexibility and precision of 3D printing, researchers and engineers can design more efficient and effective catalysts, thereby driving advancements in various chemical processes and energy applications. Additionally, 3D printing can facilitate rapid prototyping and testing of new catalyst designs, accelerating the development of innovative catalytic materials and processes. This capability is particularly valuable in research and development, where quick iterations and adjustments are often necessary to optimize performance. The following sections present examples of major global companies that are engaged in the additive manufacturing of catalysts.
BASF’s X3D®
In 2022, BASF unveiled X3D®, an innovative 3D printing-based catalyst manufacturing technology aimed at enhancing catalyst performance and efficiency while reducing energy use. This new technology allows catalysts to be produced with an open structure that lowers pressure drop across reactors, while a high surface area boosts catalyst performance.
With broad potential across industries, X3D® enables more flexible catalyst design than traditional methods, allowing for customization according to specific operational needs, such as adjusting infill patterns, fiber diameter, and orientation. These advancements increase reactor output, improve product quality, and reduce energy demands, delivering robust performance proven in both BASF’s plants and external commercial settings. This adaptability makes it possible for BASF to fine-tune catalyst properties to support efficiency and sustainability goals in customer operations.
The X3D® technology can be applied to a range of catalytic materials, including base and precious metals, as well as various carriers. Having successfully operated commercial plants using X3D catalysts for several years, BASF recently announced that it will invest in additional production capacity to drive green transformation projects. A first-of-its-kind plant for producing catalysts on an industrial scale is scheduled to open in 2026 in Ludwigshafen, Germany.
Shell’s Unique Catalyst Design
To fulfill its catalyst requirements, Shell partnered with 3D printing experts specializing in porous ceramic materials to create catalyst prototypes for applications such as gas-to-liquids (GTL) technology and environmental catalysis. By combining Shell’s knowledge of catalyst design, structure, and post-processing with the printers’ expertise in porous ceramics, the collaboration highlighted the potential of 3D printing to enhance catalyst performance. This breakthrough, achieved at the Energy Transition Centre in Amsterdam, is a significant step toward advancing 3D printing technology in catalyst production.
According to Ed Ganja, Shell’s Vice President for Catalyst and Analytical Technology, “3D printing is a key enabler for the development of advanced catalytic materials, which are essential to the energy transition. This rapidly advancing field presents numerous opportunities to improve mass and heat transfer, leading to enhanced catalytic performance.”
Shell is committed to supporting the evolving needs of its customers, both in traditional areas, such as ethylene oxide and hydroprocessing, and in new efforts that are crucial to the energy transition. 3D printing opens pathways for accelerating catalyst innovation, making possible chemical reactions that were previously too complex.
The Research & Development Tax Credit
The now permanent Research and Development (R&D) Tax Credit is available for companies developing new or improved products, processes and/or software.
3D printing can help boost a company’s R&D Tax Credits. Wages for technical employees creating, testing and revising 3D printed prototypes can be included as a percentage of eligible time spent for the R&D Tax Credit. Similarly, when used as a method of improving a process, time spent integrating 3D printing hardware and software counts as an eligible activity. Lastly, when used for modeling and preproduction, the costs of filaments consumed during the development process may also be recovered.
Whether it is used for creating and testing prototypes or for final production, 3D printing is a great indicator that R&D Credit-eligible activities are taking place. Companies implementing this technology at any point should consider taking advantage of R&D Tax Credits.
Conclusion
The global catalyst industry generates around $20 billion annually and is crucial to the chemical industry. In recent years, 3D printing technology has advanced significantly, enabling the production of catalysts with custom geometries that can overcome many of the traditionally found limitations. However, further work is needed to fully explore the possibilities and address the remaining challenges in designing and 3D printing innovative catalysts. R&D Tax Credits are available to support companies engaged in the additive manufacturing of catalysts and their applications.