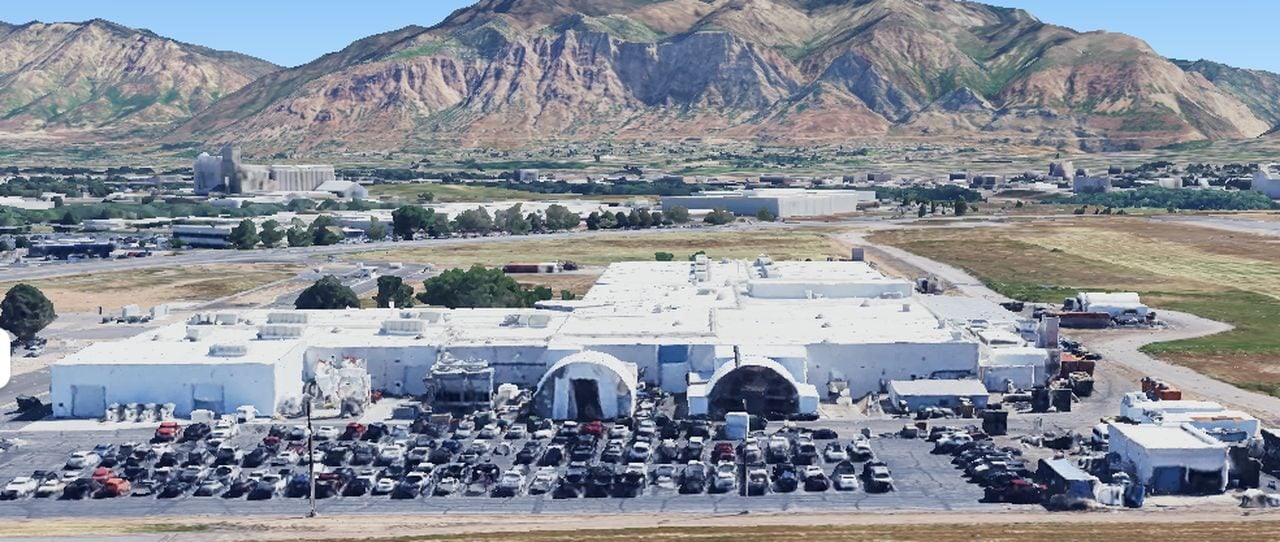
Charles R. Goulding and Preeti Sulibhavi explore how Williams International’s Weber County expansion, turbine expertise, and 3D printing innovations are driving advancements in aerospace, motorsports, and beyond.
Williams International, a prominent OEM supplier of turbine engines, is expanding its operations in Weber County, Utah. This expansion marks a significant investment in the region, with plans to enhance manufacturing capabilities and increase employment opportunities. The company’s specialization in turbine engines has earned it a strong presence in the aerospace sector, particularly as an engine supplier for business jets such as the Textron-owned Citation series.
Williams International’s Expertise in Turbines
Williams International has built a reputation for its advanced turbine engine designs, providing lightweight yet powerful solutions for the aviation industry. As an OEM supplier, Williams supplies engines for various private jet models, ensuring efficient performance, reliability, and compliance with rigorous safety standards. This specialization has positioned Williams as a trusted partner in the aerospace sector.
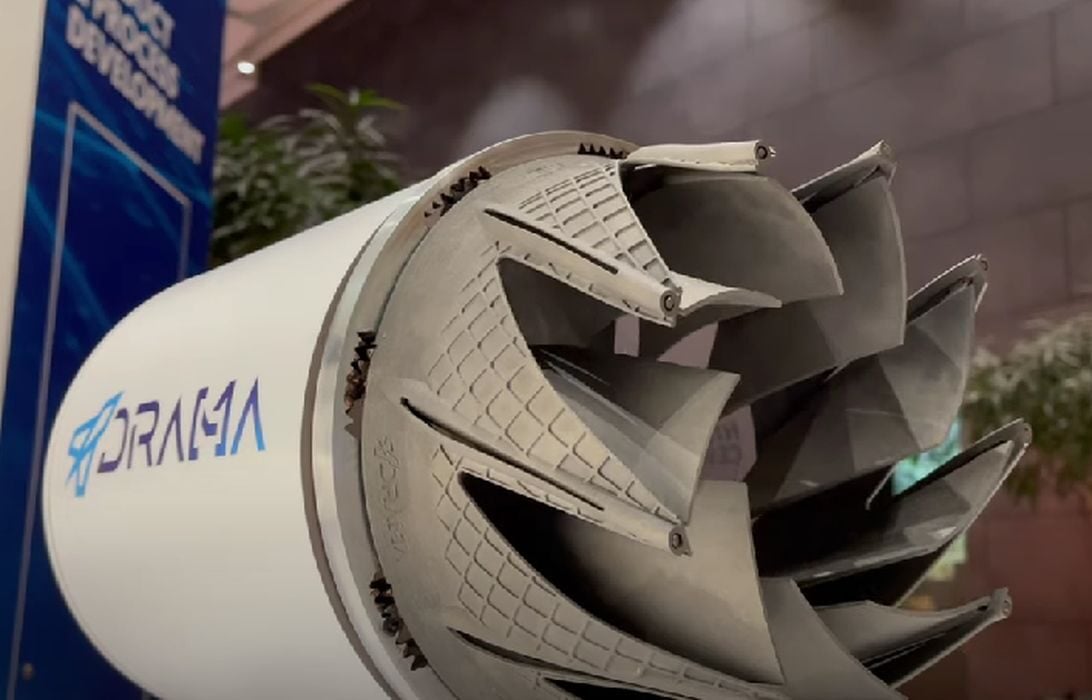
3D Printing Innovations: The Airbrake Example
Williams International’s adoption of 3D printing technology has significantly advanced its manufacturing processes. One notable example is the company’s development of a sophisticated airbrake component using additive manufacturing. By leveraging 3D printing, Williams has been able to produce intricate designs with improved durability and reduced weight. This innovative approach not only enhances performance but also streamlines the production process, reducing costs and lead times.
University of Utah’s 3D Printing Resources
Williams International has tapped into the University of Utah’s robust 3D printing resources, particularly in metallurgy. The university’s advanced research facilities specialize in metal-based additive manufacturing, offering cutting-edge solutions for complex aerospace components. This partnership enables Williams to explore new design possibilities and improve the structural integrity of its turbine engine parts. The University’s expertise in metallurgy has been instrumental in refining Williams’ manufacturing methods, enhancing precision and durability.
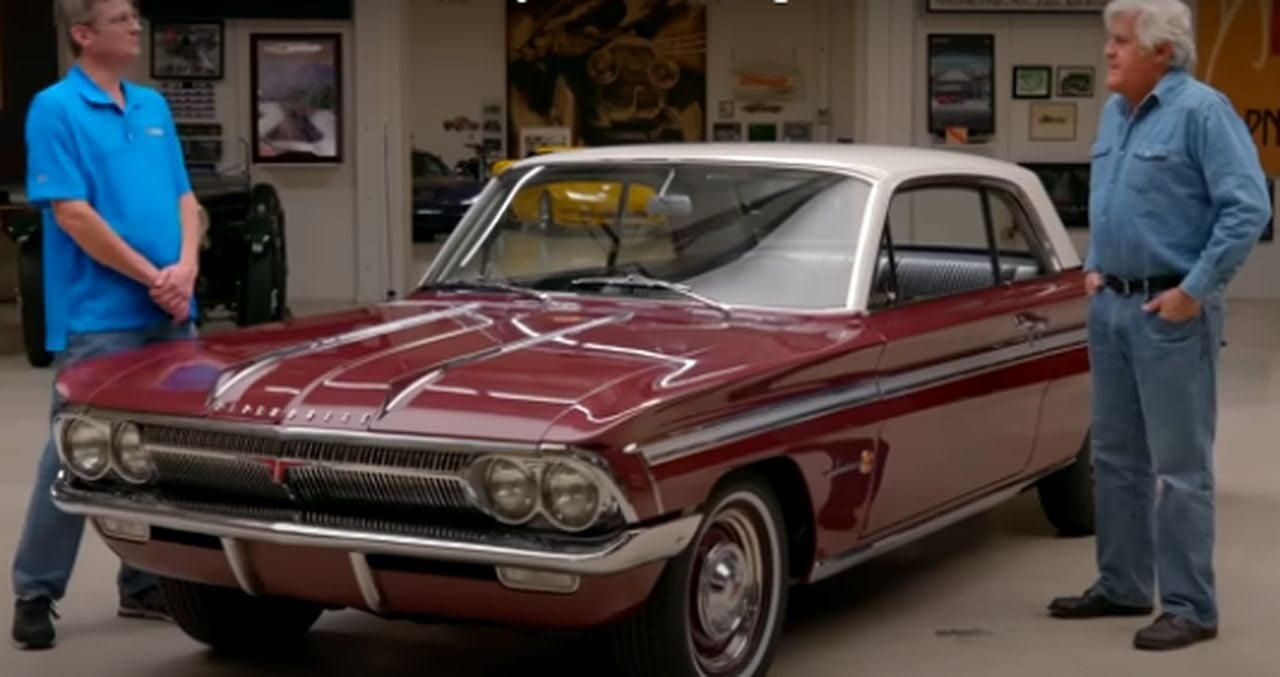
Williams International and Formula 1 Innovation
Williams International’s involvement in Formula 1 racing has also propelled its 3D printing capabilities. The company’s racing division is renowned for pioneering lightweight, high-performance vehicle components using additive manufacturing techniques.
One notable example is Williams’ development of a heat exchanger using 3D printing. This part offers improved thermal efficiency, which is crucial for optimizing engine performance under the extreme conditions of Formula 1 racing. Another example is the use of 3D printed suspension brackets, which reduce weight while maintaining structural strength. These innovations demonstrate how Williams leverages 3D printing expertise to push engineering boundaries in both motorsports and OEM manufacturing.
Jay Leno’s Restored Ford Williams Turbo Engine Car
For a touch of automotive nostalgia, Williams International’s engineering brilliance extends beyond the aerospace and racing sectors. Jay Leno’s renowned car collection features a restored Ford vehicle powered by a Williams turbo engine. This unique collaboration highlights Williams’ engineering versatility, as the turbine engine integrates seamlessly into the classic car design. The combination of vintage aesthetics and modern turbine power showcases Williams’ innovative approach to performance engineering.
The Research & Development Tax Credit
The now permanent Research and Development (R&D) Tax Credit is available for companies developing new or improved products, processes and/or software.
3D printing can help boost a company’s R&D Tax Credits. Wages for technical employees creating, testing and revising 3D printed prototypes are typically eligible expenses toward the R&D Tax Credit. Similarly, when used as a method of improving a process, time spent integrating 3D printing hardware and software can also be an eligible R&D expense. Lastly, when used for modeling and preproduction, the costs of filaments consumed during the development process may also be recovered.
Whether it is used for creating and testing prototypes or for final production, 3D printing is a great indicator that R&D Credit-eligible activities are taking place. Companies implementing this technology at any point should consider taking advantage of R&D Tax Credits.
Conclusion: Balancing Innovation with Usability
Williams International’s expansion in Weber County reflects its commitment to innovation and manufacturing excellence. By blending its turbine expertise with 3D printing advancements and leveraging partnerships with institutions like the University of Utah, Williams continues to enhance its position as a leader in advanced manufacturing. From aerospace engines to Formula 1 breakthroughs and classic car restorations, Williams International’s engineering ingenuity continues to leave an impressive mark across industries.