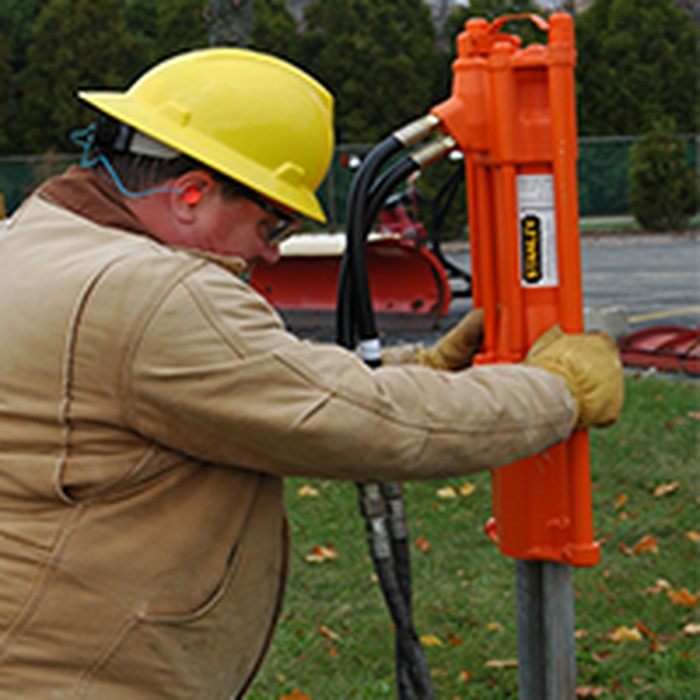
Charles R. Goulding and Preeti Sulibhavi explore how Stanley Black & Decker’s adoption of Metal X technology is transforming manufacturing efficiency and redefining industrial innovation.
Stanley Black & Decker is a titan in the global manufacturing landscape, with a rich history dating back to 1843. The company has grown into a diversified industrial powerhouse, generating over US$14 billion in annual revenue and employing approximately 60,000 people worldwide. Stanley Black & Decker’s broad portfolio includes hand tools, power tools, electronic security solutions, engineered fastening systems, and healthcare solutions. The company’s reach extends into various industries, from construction and automotive to healthcare and infrastructure, underscoring its influence across multiple sectors.
Core Tools and Fasteners Business
At the heart of Stanley Black & Decker’s operations lies its robust tools and storage segment. This division is globally recognized for its wide range of hand tools, power tools, and related accessories. Iconic brands such as DeWalt, Craftsman, and Stanley have become synonymous with reliability and innovation, serving both professionals and DIY enthusiasts. The company’s tools business continues to thrive, driven by a commitment to quality and a relentless pursuit of technological advancement.
In addition to its tools segment, Stanley Black & Decker boasts a significant presence in the fastener industry. The company’s engineered fastening systems are critical components in various manufacturing processes, particularly in the automotive and aerospace sectors. These fasteners, which include a variety of screws, bolts, and other hardware, are designed to meet the stringent demands of high-performance applications. The company’s expertise in this area has positioned it as a leader in engineered fastening solutions, further solidifying its role as an indispensable partner to manufacturers around the globe.
Commitment to Sustainability: The New Lawn Care Initiative
Stanley Black & Decker has also made strides in sustainability, particularly with its recent initiative in the lawn care industry. The company has been expanding its product line to include eco-friendly lawn care equipment, reflecting a growing consumer demand for sustainable solutions. This initiative aligns with the company’s broader commitment to environmental stewardship and its ambition to reduce its carbon footprint across all operations. By incorporating battery-powered and electric lawn care tools into its product offerings, Stanley Black & Decker is not only catering to a more environmentally conscious customer base but also positioning itself at the forefront of the green technology movement.
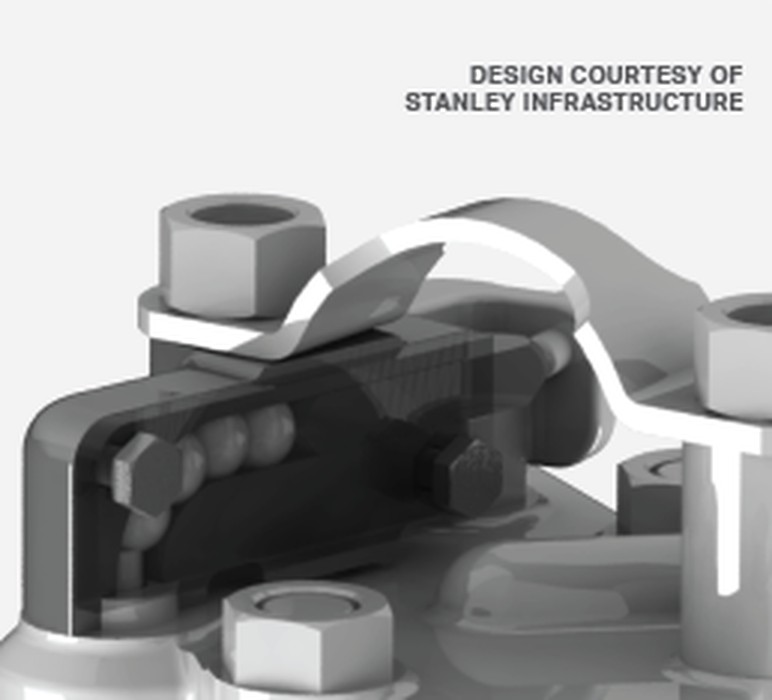
Stanley Infrastructure’s Manufacturing Challenge
Amid its diverse operations, Stanley Infrastructure, a division of Stanley Black & Decker, faced a particular challenge: manufacturing low-volume, complex parts cost-effectively. Traditional manufacturing methods like casting and machining, while reliable, often come with high costs and long lead times, especially when producing intricate parts in small quantities. For Stanley Infrastructure, which frequently needed to produce single replacement parts for devices in the field, these limitations were significant.
The Adoption of Markforged Metal X Technology
To address these challenges, Stanley Infrastructure turned to Markforged’s Metal X additive manufacturing technology. This advanced technology offered a revolutionary approach to producing metal parts, using a method called Bound Powder Extrusion (BPE). BPE involves printing metal powder bound in a plastic matrix, which is later sintered to create a fully dense metal part. This process allows for the production of complex geometries that would be difficult or impossible to achieve through traditional manufacturing methods.
Case Study: Transforming the Actuator Housing for the PD45 Hydraulic Post Driver
One of the first components to undergo this transformation was the actuator housing for the PD45 Hydraulic Post Driver. The original design of this part involved four separate components: a cast and machined main housing, a laser-cut cover plate, and two bolts to assemble the housing. This traditional manufacturing approach was not only time-consuming but also expensive due to the multiple steps involved.
By leveraging the capabilities of the Metal X, Stanley Infrastructure’s engineers redesigned the actuator housing to be produced as a single, integrated part. This redesign eliminated the need for assembly, significantly reducing both material waste and the potential for error. The new design was also 53% lighter, which improved the overall performance of the PD45 Hydraulic Post Driver. Testing revealed that the Metal X-produced actuator housing could withstand tens of thousands of cycles, demonstrating its durability and suitability for high-stress applications.
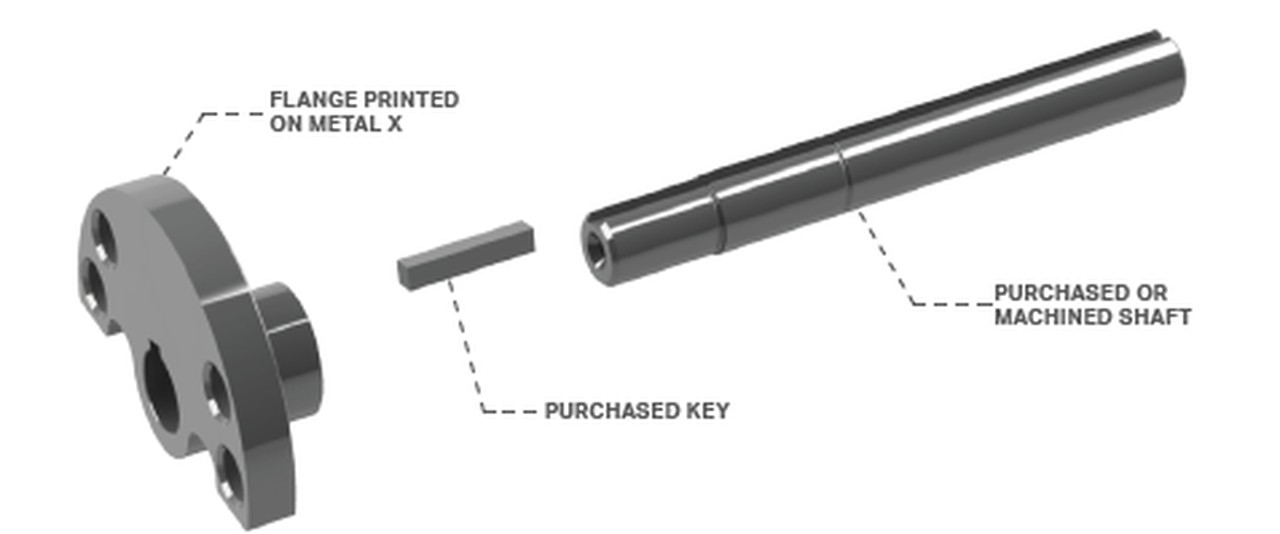
Case Study: Enhancing the Wheel Shaft for the PG10 Profile “Frog” Grinder
Another component that benefited from the Metal X technology was the wheel shaft for the PG10 Profile “Frog” Grinder. Similar to the actuator housing, the wheel shaft was traditionally manufactured through a complex and costly process. The adoption of Metal X allowed Stanley Infrastructure to simplify the design and manufacturing process, producing the wheel shaft in a single step.
The results were impressive: the Metal X-produced wheel shaft maintained the required strength and durability while being produced at a fraction of the cost of traditional methods. This success highlighted the potential for additive manufacturing to revolutionize the production of low-volume, complex parts, providing Stanley Infrastructure with a powerful tool to enhance efficiency and reduce costs.
Cost Performance: A Game-Changer in Manufacturing Efficiency
One of the most significant benefits of adopting Metal X technology was the dramatic reduction in both cost and lead time. By replacing traditional manufacturing methods with the Metal X, Stanley Infrastructure was able to save between 34% and 48% on manufacturing costs for the actuator housing and wheel shaft. Additionally, the lead time for producing these parts was slashed by an astonishing 69%.
The savings were even more pronounced in scenarios where Stanley Infrastructure needed to produce single replacement parts. Traditional methods required batch production, which was both time-consuming and expensive. In contrast, the Metal X allowed for single parts to be printed on-demand, making the process 12.5 times cheaper and 20 times faster than casting and machining.
This pay-per-part model, as opposed to a pay-per-batch approach, further underscored the flexibility and cost-effectiveness of Metal X technology. By enabling Stanley Infrastructure to produce high-quality parts on demand, the Metal X not only reduced costs but also improved the company’s ability to respond quickly to customer needs.
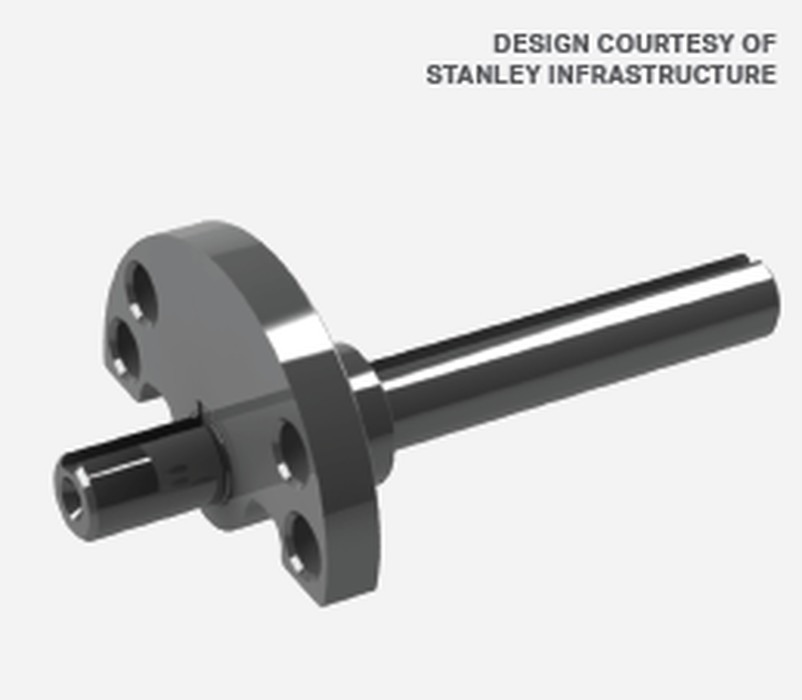
Analysis: The Strategic Value of Metal X in Industrial Manufacturing
The successful integration of Markforged’s Metal X technology at Stanley Infrastructure illustrates the transformative potential of 3D printing in industrial settings. By intelligently designing parts for additive manufacturing, minimizing print time, and incorporating off-the-shelf components where possible, companies can produce high-quality parts more cost-effectively than with traditional subtractive manufacturing methods.
For industrial customers like Stanley Infrastructure, the key to maximizing the benefits of additive manufacturing lies in understanding its strengths and limitations. Additive manufacturing is particularly advantageous for producing complex, low-volume parts that would be prohibitively expensive or time-consuming to produce using traditional methods. By focusing on these types of applications, companies can achieve significant cost savings while also enhancing their ability to innovate and respond to market demands.
Below is a table that presents the ever-increasing research and development (R&D) investments that Stanley Black & Decker has made in the last four years.
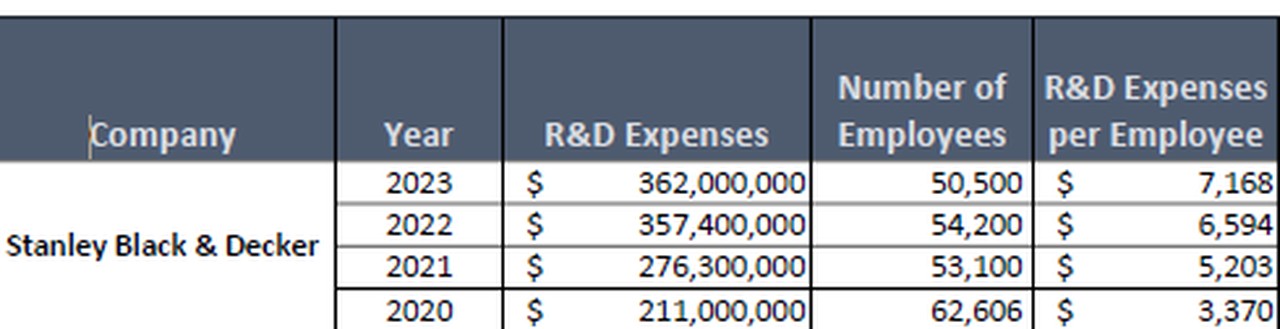
The Research & Development Tax Credit
The now permanent Research and Development (R&D) Tax Credit is available for companies developing new or improved products, processes and/or software.
3D printing can help boost a company’s R&D Tax Credits. Wages for technical employees creating, testing and revising 3D printed prototypes can be included as a percentage of eligible time spent for the R&D Tax Credit. Similarly, when used as a method of improving a process, time spent integrating 3D printing hardware and software counts as an eligible activity. Lastly, when used for modeling and preproduction, the costs of filaments consumed during the development process may also be recovered.
Whether it is used for creating and testing prototypes or for final production, 3D printing is a great indicator that R&D Credit-eligible activities are taking place. Companies implementing this technology at any point should consider taking advantage of R&D Tax Credits.
Conclusion: A New Era of Manufacturing at Stanley Black & Decker
The adoption of Markforged’s Metal X technology represents a significant step forward for Stanley Black & Decker, particularly for its Stanley Infrastructure division. By embracing this advanced manufacturing process, the company has reduced costs and lead times and positioned itself at the forefront of innovation in the industrial sector.
As Stanley Black & Decker continues to explore new ways to leverage additive manufacturing and other advanced technologies, it remains committed to delivering high-quality products that meet the evolving needs of its customers. The success of the Metal X initiative is a testament to the company’s ability to adapt and thrive in an increasingly competitive global market, ensuring that it will continue to be a leader in the industry for years to come.