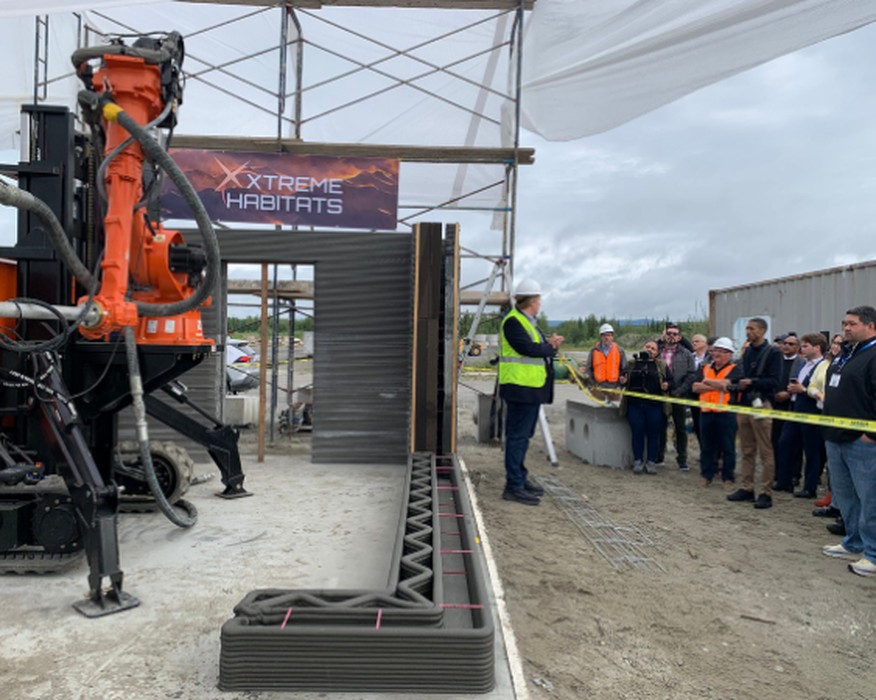
Charles R. Goulding and Preeti Sulibhavi explore how 3D printing technology is reshaping affordable housing solutions across the U.S., from HUD’s initiatives in Alaska to cutting-edge projects in Texas and beyond.
The affordable housing crisis is a persistent issue in the United States, with millions of families struggling to find homes within their budget. Traditional construction methods often fail to meet the growing demand for housing due to high costs, lengthy timelines, and limited resources. However, 3D printing is poised to revolutionize the way homes are built.
Presidential candidate, Kamala Harris has presented her affordable housing plan recently. Currently, the U.S. Department of Housing and Urban Development (HUD) is actively exploring how 3D printing technology can help address the affordable housing shortage. Through partnerships with universities, private companies, and local governments, HUD aims to boost the supply of affordable homes using this innovative approach. One such project is currently underway in Alaska, where 3D printing is being tested as a solution to construct sustainable, affordable housing in extreme climates.
The Promise of 3D Printing for Affordable Housing
3D printing, also known as additive manufacturing, allows for the creation of structures by layering materials in precise, computer-controlled patterns. When applied to housing, this technology has the potential to significantly reduce both the cost and time required to build homes. A typical 3D printed house can be constructed in just a few days, as opposed to the several months it takes using traditional methods.
The key benefits of 3D printing for affordable housing construction include:
- Cost Efficiency: 3D printing requires fewer materials, reducing waste and overall expenses. Labor costs are also minimized, as much of the work is automated.
- Speed: Homes can be printed quickly, with some companies capable of producing the walls of a small house in as little as 24 hours.
- Customization and Flexibility: The technology allows for customizable designs, which can be adjusted based on the needs of specific communities or climates.
- Sustainability: By using locally sourced and sustainable materials, 3D printing can lower the environmental impact of construction.
- Energy Efficiency: 3D printed homes can be designed with energy efficiency in mind, helping residents save on utility bills over time.
HUD’s Push for Innovation in Alaska
Alaska needs an estimated 27,500 new housing units over the next 10 years to alleviate overcrowding and unsanitary conditions, according to the Alaska Housing Foundation Corporation.
That is why in Fairbanks, Alaska, HUD leaders, in collaboration with the University of Alaska, are exploring how 3D printing can address housing challenges in sub-arctic regions. During a recent demonstration, HUD showcased a mobile 3D printer that is being developed to build affordable, energy-efficient homes using local resources.
This project is particularly important for Alaska, where harsh weather conditions and high construction costs make it difficult to build affordable housing. HUD’s partnership with the City of Nome, Penn State University, and other key organizations is focused on designing and engineering homes that can withstand the extreme climate while remaining affordable and sustainable.
Specifically, the interdisciplinary team of Penn State researchers led by José Pinto Duarte, Stuckeman Chair in Design Innovation and director of the Stuckeman Center for Design Computing (SCDC) in the College of Arts and Architecture’s Stuckeman School, is looking to alleviate some of that stress with a US$376,000 U.S. Department of Housing and Urban Development (HUD) grant.
This funding will support the development and testing of a prototype 3D printed home designed for sub-arctic conditions. The project team aims to use local materials in the construction process, which could further reduce costs and create jobs in the community.
HUD’s investment in Alaska is part of a broader effort to promote innovative construction techniques that can help address the housing shortage nationwide. The department’s “Road to Innovation” tour, which highlights cutting-edge housing solutions across the country, has made stops in cities like Detroit, Minneapolis, Seattle, and New York City. These visits showcase the potential of technologies like 3D printing to revolutionize the housing sector.
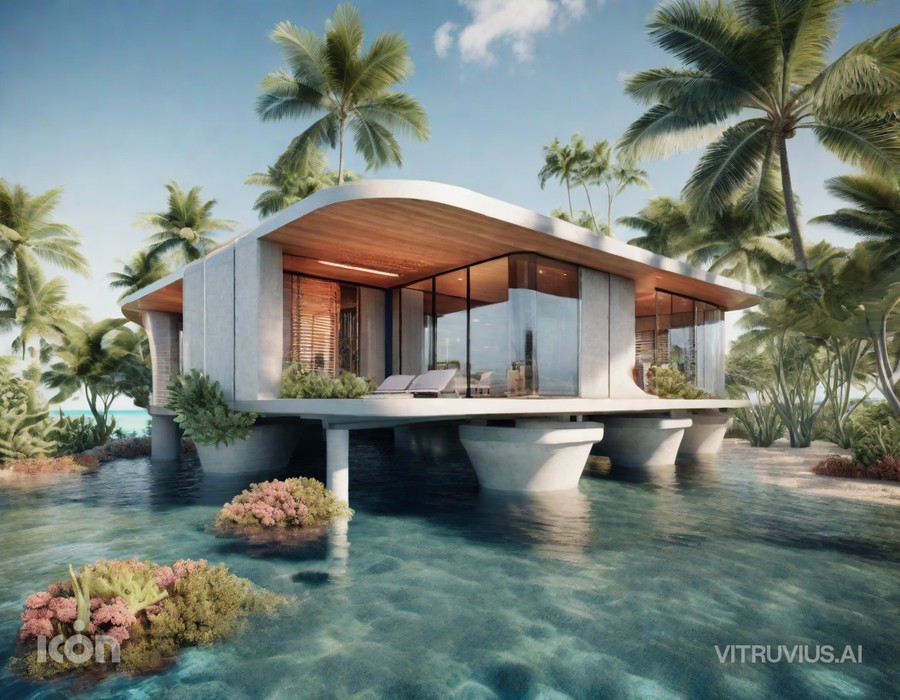
Examples of 3D Printing in Housing Across the U.S.
The use of 3D printing for housing construction is not limited to Alaska. Across the U.S., various companies and organizations are testing and implementing 3D printing technology to build affordable homes. Here are some noteworthy examples:
1. Austin, Texas: ICON and Community First! Village
One of the most prominent examples of 3D printing in affordable housing comes from Austin, Texas. ICON, a construction technology company, partnered with a local non-profit, Mobile Loaves & Fishes, to create 3D printed homes for the Community First! Village. This village provides permanent housing to individuals experiencing chronic homelessness.
The 3D printed homes are designed to be affordable, durable, and quick to construct. ICON’s technology can print the walls of a home in just 24 hours, and the cost of construction is significantly lower than traditional methods. The success of this project has drawn national attention, and ICON continues to expand its efforts in 3D printing housing.
2. Virginia: Habitat for Humanity and Alquist
In 2021, Habitat for Humanity partnered with Alquist, a 3D printing construction company, to build the first 3D printed house in Virginia. This project aimed to provide an affordable home for a low-income family in Williamsburg.
Alquist’s 3D printer produced the exterior walls of the 1,200-square-foot home in just 12 hours, dramatically reducing construction time and labor costs. The house also incorporates energy-efficient features, helping the family save on utility bills in the long run. This project is part of a broader effort by Habitat for Humanity to explore innovative construction methods that can help address the affordable housing crisis.
3. California: Mighty Buildings and Palari Group
In Southern California, Mighty Buildings, a construction technology company, has partnered with Palari Group to create a community of 3D printed homes. The first development, located in Rancho Mirage, will feature 15 eco-friendly homes constructed using Mighty Buildings’ 3D printing technology.
These homes are designed to be energy-efficient and sustainable, incorporating solar panels and other green technologies. By using 3D printing, Mighty Buildings can reduce construction waste by up to 95%, making the project both affordable and environmentally friendly. The Rancho Mirage project is just the beginning, as Mighty Buildings and Palari Group plan to expand their efforts to other locations in California.
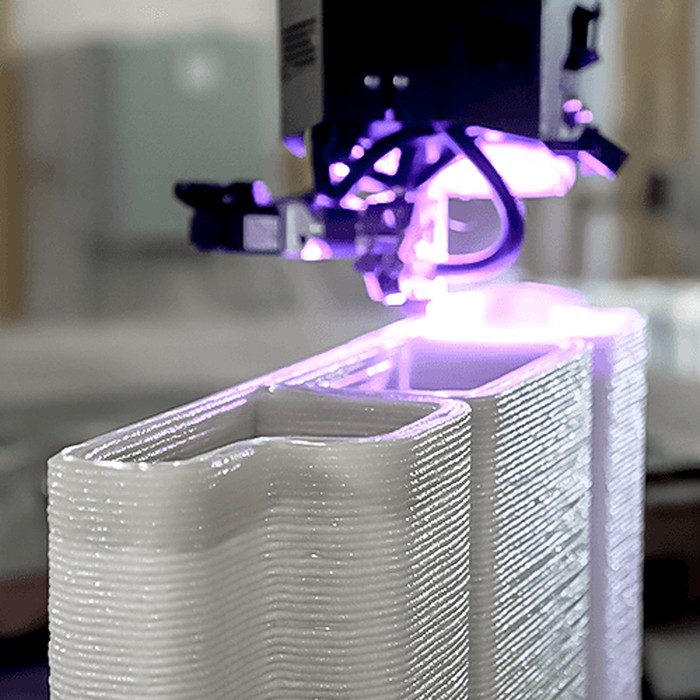
Overcoming Challenges and Scaling the Technology
While 3D printing holds tremendous potential for addressing the affordable housing crisis, there are still challenges to overcome. One of the main obstacles is scaling the technology to produce homes on a larger scale. While 3D printers can construct homes quickly, building entire neighborhoods using this technology requires significant investment and coordination.
Additionally, building codes and regulations vary by state and municipality, which can make it difficult to implement 3D printing across the country. HUD’s efforts to update regulations, as seen in their proposed changes to the HUD Code, are a step in the right direction. These updates will allow for the use of modern materials and designs that facilitate 3D printing, helping to accelerate the adoption of the technology.
The Research & Development Tax Credit
The now permanent Research and Development (R&D) Tax Credit is available for companies developing new or improved products, processes and/or software.
3D printing can help boost a company’s R&D Tax Credits. Wages for technical employees creating, testing and revising 3D printed prototypes can be included as a percentage of eligible time spent for the R&D Tax Credit. Similarly, when used as a method of improving a process, time spent integrating 3D printing hardware and software counts as an eligible activity. Lastly, when used for modeling and preproduction, the costs of filaments consumed during the development process may also be recovered.
Whether it is used for creating and testing prototypes or for final production, 3D printing is a great indicator that R&D Credit-eligible activities are taking place. Companies implementing this technology at any point should consider taking advantage of R&D Tax Credits.
Home, Sweet Home…
As the U.S. continues to grapple with an affordable housing shortage, innovative solutions like 3D printing are becoming increasingly important. HUD’s investment in 3D printing, particularly in challenging environments like Alaska, demonstrates a commitment to exploring new ways to build affordable, sustainable homes.
Projects across the country—from Texas to Virginia to California—showcase the potential of 3D printing to revolutionize the construction industry. By reducing costs, speeding up construction times, and incorporating sustainable materials, 3D printing offers a promising path forward for creating affordable housing for all Americans.
As technology advances and partnerships between government, private companies, and academia continue to grow, 3D printing may become a key tool in solving one of the most pressing issues of our time: the lack of affordable housing.