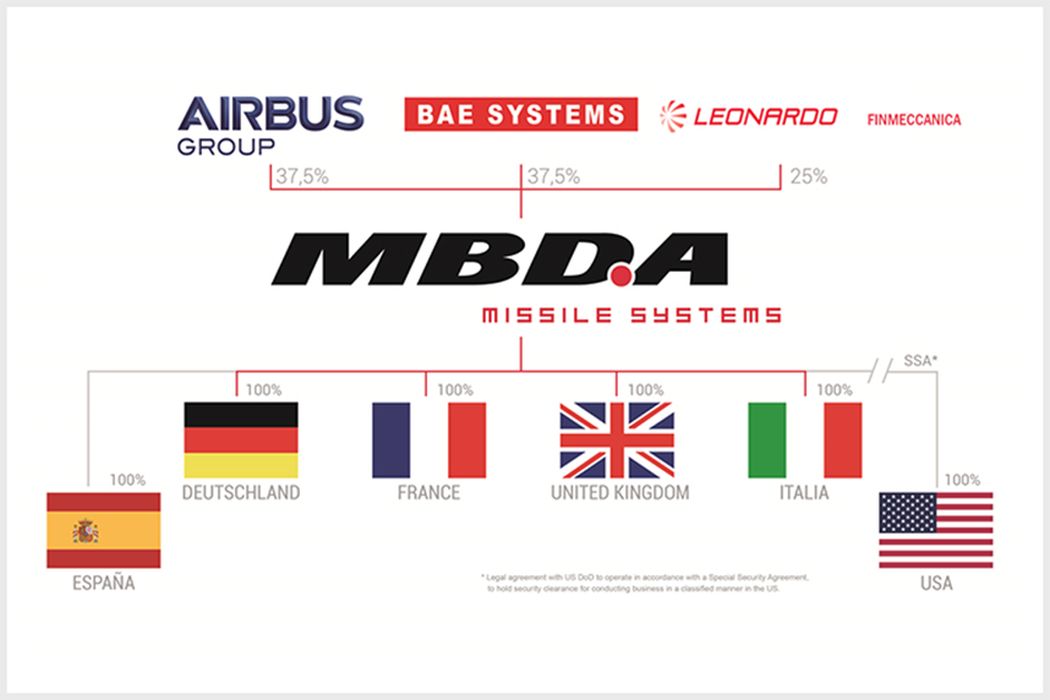
Charles R. Goulding and Preeti Sulibhavi discuss how MBDA is transforming European defense with groundbreaking 3D printing technology and strategic partnerships across the continent.
In the face of growing defense challenges and the need for enhanced military capabilities, MBDA has emerged as a leading European defense company, capitalizing on the continent’s ambitions to bolster its strategic autonomy. The company’s multi-country operational structure, reminiscent of Airbus, has enabled it to leverage the diverse capabilities and resources of its European partners, positioning it as a key player in the evolving defense landscape.
One area where MBDA has demonstrated its innovative prowess is in the realm of 3D printing. As defense needs have intensified, the ability to rapidly produce specialized components and parts has become increasingly crucial. MBDA has embraced this technology, seamlessly integrating it into its manufacturing processes to enhance efficiency and responsiveness.
Two recent examples of MBDA leveraging 3D printing technology include missile component fabrication and rapid prototyping.
Missile Components Fabrication
MBDA has been actively exploring the use of 3D printing to fabricate critical components for its missile systems. In 2022, the company announced that it had successfully produced complex metal parts for its missiles using additive manufacturing techniques. This included the development of a 3D printed heat shield for one of MBDA’s air-to-air missile models. By utilizing 3D printing, MBDA was able to streamline the production process, reduce lead times, and optimize the design of these mission-critical components, enhancing the overall performance and reliability of its missile systems.
Rapid Prototyping for Product Development
MBDA has also heavily invested in the use of 3D printing for rapid prototyping during the product development phase. The company has leveraged additive manufacturing to quickly create physical models and iterate on design concepts, allowing for faster testing and validation of new missile and defense system technologies. This has enabled MBDA to accelerate the development cycle, respond more agilely to customer requirements, and bring innovative solutions to the market at a faster pace. The company’s ability to rapidly produce prototype parts and components has been a key advantage in its efforts to maintain a competitive edge in the European defense industry.
Other Examples of European Defense Companies Using 3D Printing
BAE Systems, a major European defense contractor, has been at the forefront of 3D printing in the defense industry. In a recent development, the company has successfully implemented 3D printing to produce critical components for its Typhoon fighter jets. By utilizing this technology, BAE Systems has been able to reduce lead times and streamline the production of replacement parts, ultimately enhancing the operational readiness of its military aircraft.
Similarly, Rolls-Royce Aerospace, a renowned British engineering firm, has leveraged 3D printing to revolutionize its aerospace manufacturing. The company has been exploring the use of additive manufacturing to produce complex engine components, often with intricate designs that would be challenging to produce using traditional methods. This innovative approach has enabled Rolls-Royce to optimize the performance and efficiency of its aircraft engines, further strengthening its position in the European defense and aerospace landscape.
Thales, a prominent French defense and technology company, has also embraced the potential of 3D printing. The company has been utilizing this technology to produce customized solutions for its military customers, such as specialized mounting brackets for its communications equipment. By leveraging the flexibility and rapid prototyping capabilities of 3D printing, Thales has been able to respond more swiftly to the evolving needs of its clients, enhancing their operational effectiveness.
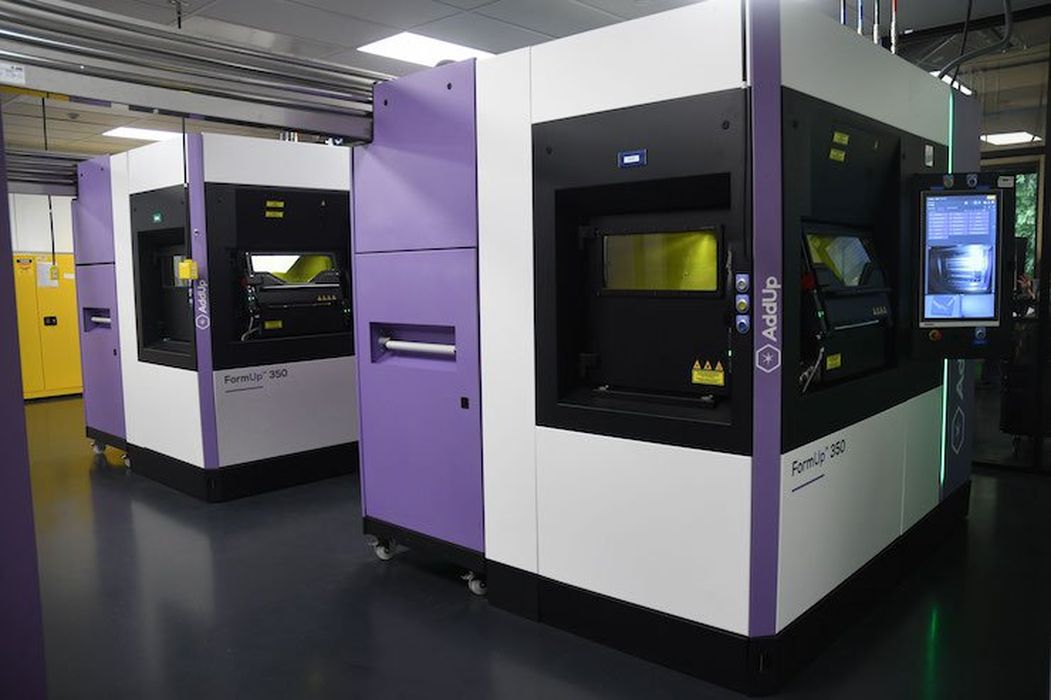
The increased defense budgets of NATO countries, coupled with the delays in U.S. funding for Ukraine, have further empowered the European defense and aerospace industry, including the integration of 3D printing technology. As nations seek to bolster their military capabilities, the European defense sector has seized the opportunity to showcase its innovative prowess and strategic importance.
Moreover, the current challenges faced by Boeing, a major player in the global aerospace market, have presented a window of opportunity for European defense and aerospace companies to strengthen their positions. MBDA, with its robust 3D printing capabilities and its ability to adapt to the changing market dynamics, is well-positioned to capitalize on this shift.
The multi-country operational structure of MBDA, like that of Airbus, has been a key factor in its success. By leveraging the expertise and resources of its European partners, the company has been able to develop innovative solutions that cater to the diverse needs of its clients. This collaborative approach has not only enhanced MBDA’s technological capabilities but has also fostered a sense of strategic autonomy within the European defense sector.
The integration of 3D printing technology has been a crucial element in MBDA’s success. By embracing this disruptive technology, the company has been able to reduce lead times, optimize production processes, and respond more effectively to the evolving demands of its customers. The recent examples of 3D printing applications by BAE Systems, Rolls-Royce Aerospace, and Thales further underscore the potential of this technology in the defense and aerospace industries.
As the European defense landscape continues to evolve, MBDA’s role as a leading European defense company is likely to become even more pronounced. The company’s ability to adapt to changing market conditions, leverage the strengths of its European partners, and harness the power of 3D printing will be instrumental in shaping the future of European defense and aerospace.
The Research & Development Tax Credit
The now permanent Research and Development (R&D) Tax Credit is available for companies developing new or improved products, processes and/or software.
3D printing can help boost a company’s R&D Tax Credits. Wages for technical employees creating, testing and revising 3D printed prototypes can be included as a percentage of eligible time spent for the R&D Tax Credit. Similarly, when used as a method of improving a process, time spent integrating 3D printing hardware and software counts as an eligible activity. Lastly, when used for modeling and preproduction, the costs of filaments consumed during the development process may also be recovered.
Whether it is used for creating and testing prototypes or for final production, 3D printing is a great indicator that R&D Credit-eligible activities are taking place. Companies implementing this technology at any point should consider taking advantage of R&D Tax Credits.
Conclusion
MBDA’s rise as a leading European defense company is a testament to the continent’s ambitions to bolster its strategic autonomy. The company’s multi-country operational structure and its embrace of 3D printing technology have positioned it as a formidable player in the global defense market. As the European defense sector continues to evolve, MBDA’s innovative approach and its ability to collaborate with its European partners will be crucial in maintaining the continent’s competitive edge and ensuring its military readiness in the face of emerging challenges.