SPONSORED CONTENT
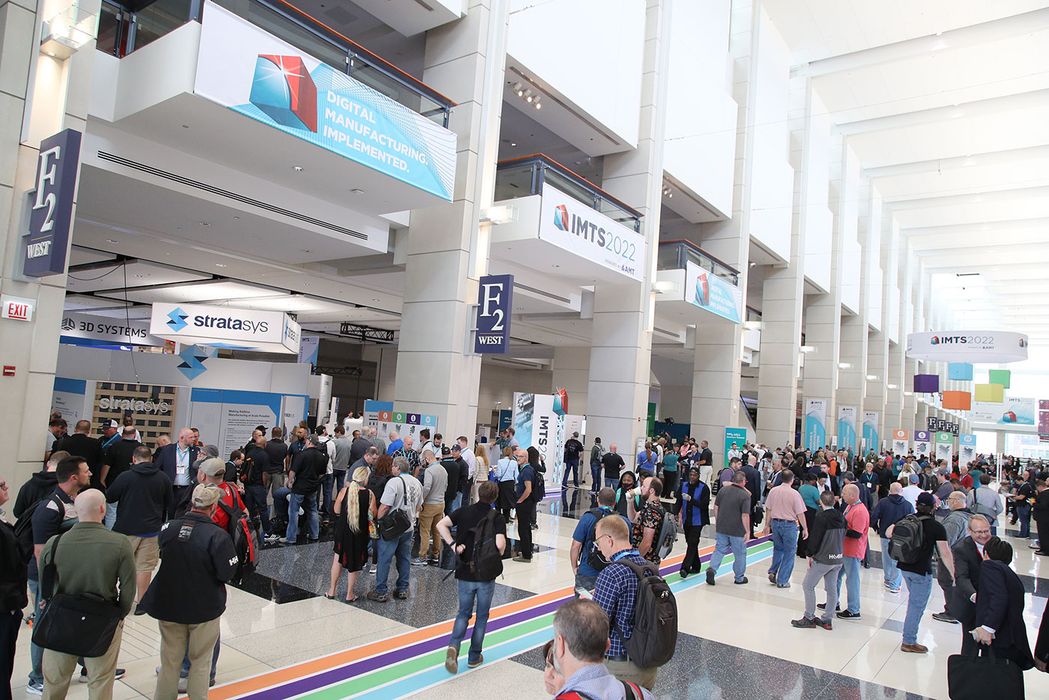
Where can an additive manufacturing adventure at IMTS 2024 take you?
For Austin Schmidt, seeing the Strati vehicle being 3D printed at IMTS 2014 eventually led him to co-found Additive Engineering Solutions, his own additive manufacturing (AM) services company (learn more).
For the 10th anniversary of the Strati, IMTS – The International Manufacturing Technology Show has brought the world’s most famous 3D printed car back to the show. IMTS 2024 runs from Sept. 9-14 at Chicago’s McCormick Place. From the novelty of the Strati, AM at IMTS has grown in the Additive Manufacturing Sector – accelerated by Formnext, which features a spectrum of AM exhibitors in the West Building, as well as AM solutions throughout the show.
Growing a Business
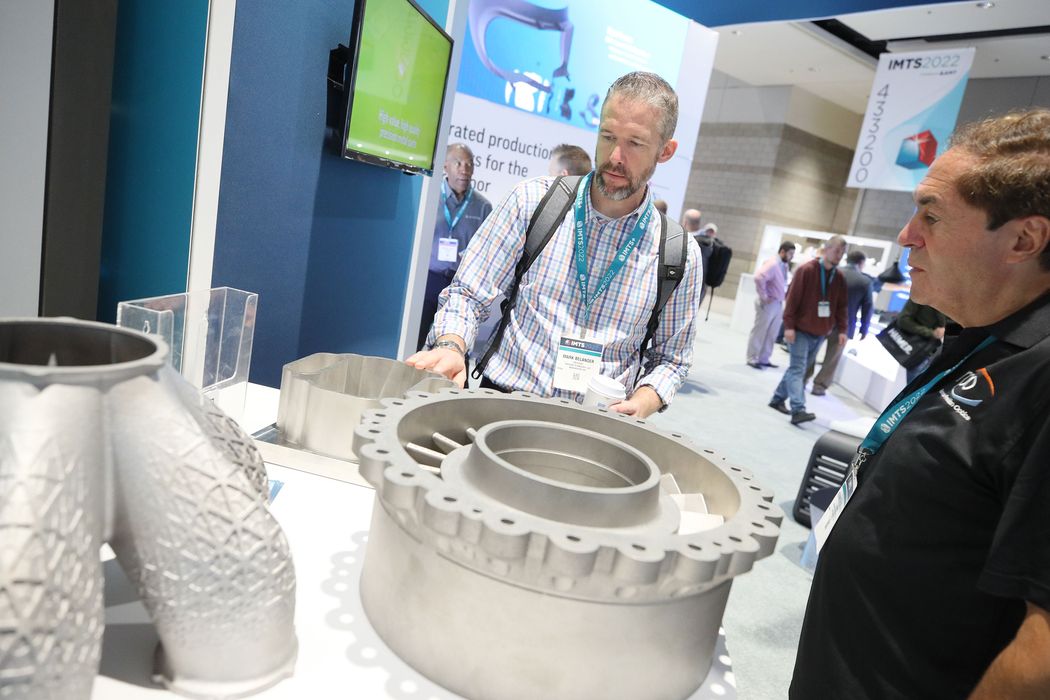
Seeing the potential of the Large Format Polymer Additive Manufacturing (LFAM) technology used to print the Strati, Schmidt decided to build a company that now operates five LFAM systems. Schmidt is an early pioneer of additive manufacturing as a service for large format applications, a business model that embodies the entrepreneurial spirit that remains core to the manufacturing industry.
“The manufacturing-as-a-service business model continues to thrive in additive manufacturing,” says Dayton Horvath, director of emerging technology and investments at AMT. “Technology providers recognize more and more that aerospace, defense, energy, and other industrial applications prefer to partner and outsource certain AM production needs to companies with deep expertise.”
As one of many growth examples, Horvath cites Incodema3D, which just acquired 10 more EOS M 300-4 Laser Powder Bed Fusion (LPBF) systems, bringing its total to 34 metal AM systems. The company has a 60,000-sq.-ft. manufacturing space with about one-third dedicated to AM and a metrology room, one-third to metal removal for post-process work, and one-third available for growth.
Also, I3D MFG purchased twelve EOS M 400-4 systems that will be delivered over the next two years, bringing the company’s Oregon facility to 36 metal AM systems. And, in April, Sintavia announced an additional $25 million in funding to expand its manufacturing facility in Hollywood, Florida.
“Metal AM has become repeatable and dependable and is ready for production parts,” says James Hockey, director of business development at Incodema3D (learn more). He says metal AM is changing the way engineers think so they can design more functional parts, such as increasing the surface area for better cooling of electronic components while also lightweighting them and reducing the number of assemblies.
“We need people working smarter, so at IMTS 2024 we’ll be looking at AI, automation, and robotic carts to move parts from one part of the facility to another,” says Hockey. “In everything we do, we match the right technology to elevate our production capabilities for our customer programs.”
Onome Scott-Emuakpor, Ph.D., founded Hyphen Innovations to explore the possibilities of leveraging AM technologies for vibration suppression, which could disrupt traditional turbine engine blade manufacturing and repair (learn more). Hyphen Innovations collaborates with service provider Laser Fusion Solutions to conduct LPBF research, and it has a laser wire directed energy deposition AM system from Meltio in house.
“The Additive Manufacturing Sector at IMTS was probably one of the most diverse and largest that I’ve seen in any additive manufacturing conference within North America,” says Scott-Emuakpor. “IMTS is a one-stop shop for anybody who is into additive manufacturing.”
New Possibilities
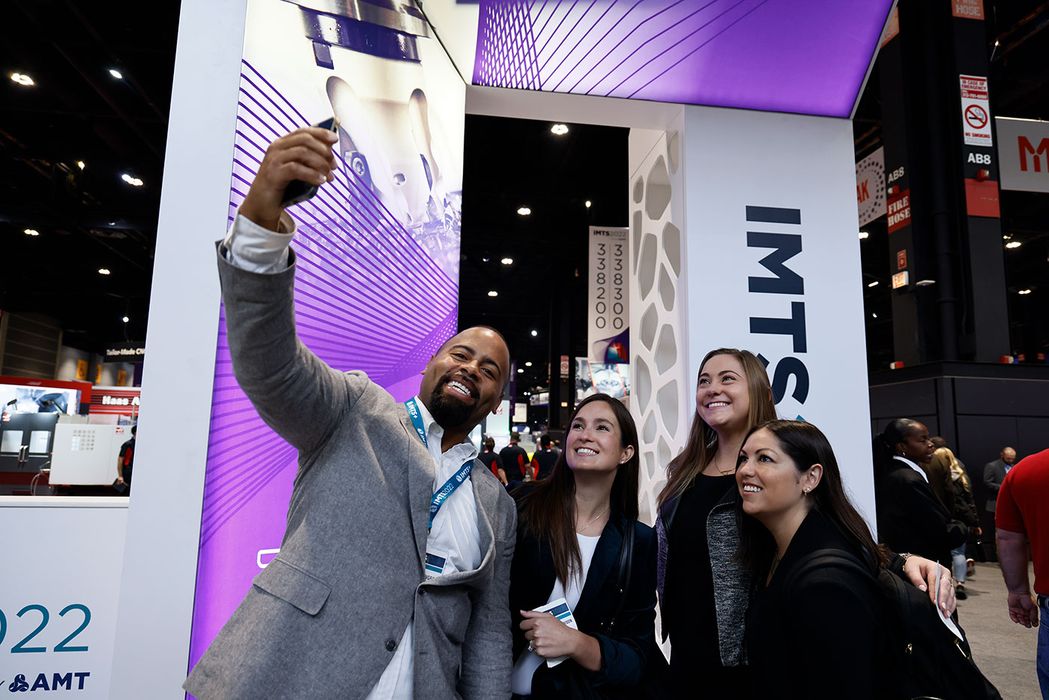
“In addition to LFAM and LPBF technology, which are becoming mainstream, contract manufacturers and OEMs should explore hybrid manufacturing cells that combine subtractive and additive manufacturing with in-situ inspection,” says Horvath. “Applications include repair, remanufacture, and feature enhancement to extend a part’s life cycle often by depositing high-performance materials onto lower-cost substrates.”
The AMT Emerging Technology Center (IMTS booth #236700) at IMTS 2024 will feature an integrated multi-process convergent manufacturing cell developed by an interdisciplinary team at Oak Ridge National Laboratory. The cell integrates existing technologies in an innovative configuration that includes a robotic wire-arc additive manufacturing (WAAM) using metal AM technology from Lincoln Electric, Arc Specialties, Open Mind, Yaskawa, Roboris (Eureka Robot); a machining center from Okuma and cutting tools supplied by Kennametal; a Fastems pallet tower for extended periods of unattended operation; a heat-treating system for microstructure enhancement from Ajax Tocco; and a 3D laser scanning metrology station from Zeiss.
“IMTS offers so much to explore that time management at the show becomes a necessity,” says Horvath. “My suggestion for visitors looking to explore AM technology begins with themes and representative examples; let the exhibitors be the arrow to your next stop by asking them if anyone else is exhibiting the same process category as them.”
Horvath offers up the following themes and exhibitors as a starting point:
- Electron beam melting (JEOL, Wayland Additive, Colibrium Additive) and how it compares to laser powder bed fusion (Velo3D, Additive Industries, Colibrium Additive, EOS, AddUp, Xact Metal, TRUMPF, Renishaw, 3D Systems, SLM Solutions,).
- How software integration across the design-to-manufacturing workflow is improving (Materialise, Oqton, Siemens, Moduleworks).
- Unique additive manufacturing technologies driving new capabilities and applications (Tritone Technologies, Impossible Objects, Fabrisonic, 3DEO, Mantle, Hybrid Manufacturing Technologies).
- How contract manufacturers are differentiating themselves (Xometry, GKN Additive, Endeavor 3D, REV A MFG, 3DEO).
“Our customers are looking for extensions of their team,” says Emily Elpes, chief of staff and vice president of marketing for 3DEO, which developed a proprietary process called Intelligent Layering and is a leading contract manufacturer. “They’re basically saying they can’t do it themselves and struggle to find a partner that can help.”
To start a conversation at IMTS, Elpes notes manufacturers often want to make something that they have never made before or something they didn’t think could be made. As an example, she cites a design 3DEO developed that reduces a train assembly from 14 parts to two additively manufactured parts and two off-the-shelf parts.
More than Exhibitors
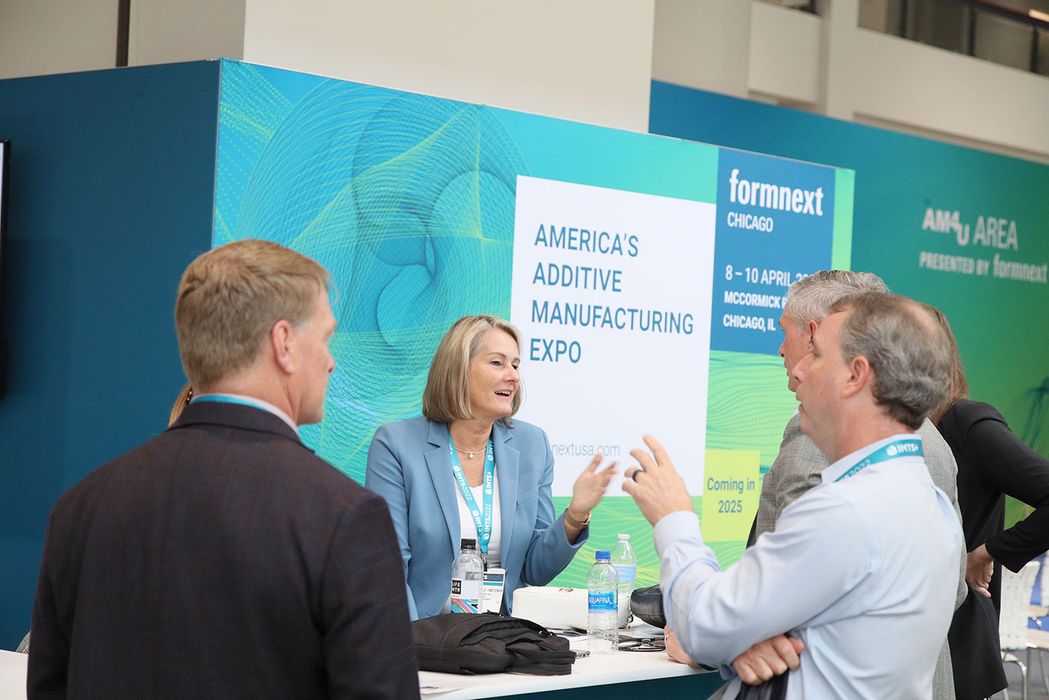
IMTS also provides visitors the opportunity to learn more about AM through its Conferences (including the “Succeeding with Powder Bed Fusion Workshop”) and through the Formnext Stage, located at the entrance to the West Building. On the Formnext Stage, presenters from AMT, Gardner Business Media, Mesago, and leading organizations will discuss entrepreneurship and business models, as well as adopting industrial AM into production processes.
To keep track of the AM companies you plan to meet with, use the Show Planner function to create a personalized agenda, schedule meetings with exhibitors, gain special offers, see recommendations, “bookmark” companies of interest and recall their location on the floor plan, and make notes about the company.
Make your plans to attend IMTS 2024, Sept. 9-14 at McCormick Place in Chicago. Register at IMTS.com/Register.
And, mark your calendar for Formnext Chicago, April 8-10, 2025 at McCormick Place in Chicago.
New Products
Exhibitors use IMTS as an opportunity to launch and showcase their new products. Here are just a few recent announcements from IMTS exhibitors that showcase the range of offerings in the Additive Sector this year.
- Meltio’s M600 system featuring its Blue Laser deposition head that increases printing speed as a result of the increased absorption of the short wavelength light. The system also removes common touch points such as manual laser alignment, and programming is a matter of minutes as the result of a dedicated slicer.
- GE Additive has relaunched as Colibrium Additive – a GE Aerospace company. The company has unveiled EBMControl 6.4, a significant upgrade to its core electron beam melting (EB-PBF) software.
- Formlabs’ Form 4, which prints two to five times faster than the Form 3+ depending on material, enables same-hour iteration or batch production with masked stereolithography (MSLA) technology.
- Xact Metal’s initiative “Breaking the Mold: The Xact Solution to Better Tooling” aims to change the approach to metal 3D printing in the tooling industry by reframing the technology as a valuable option for rapid and cost-effective parts deployment in a moldmaker’s toolbox.
- Mantle has announced the release of its 420 Stainless Steel material. The company’s 3D printers are an efficient way to produce mold and die inserts with the accuracy, surface finish, and tool steel properties demanded by toolmakers.
- 3D Systems new EXT 800 Titan Pellet extrusion system, which has a build volume of 800 x 600 x 800 mm, harnesses the speed, reliability, and efficiency of the company’s large-format EXT Titan Pellet systems.