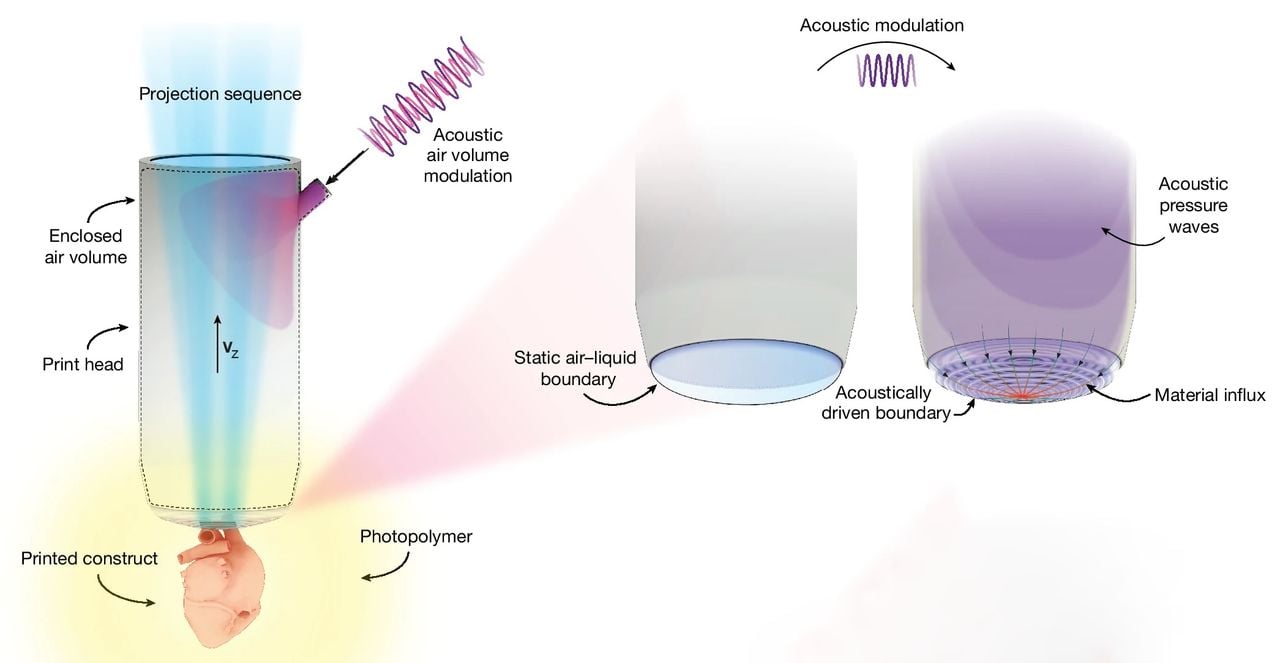
A radically new and incredibly fast 3D printing process has been developed: Dynamic Interface Printing, or “DIP 3D Printer”.
We’ve seen a series of ultra-fast 3D printing processes developed recently using volumetric techniques. These processes involve schemes that print the entire object at once, rather than layer by layer. They can print complete objects in only seconds, and I’ve seen this in person.
These systems work by projecting patterns into a vat of transparent photopolymer resin from multiple angles, solidifying the object all at once.
In spite of the incredible speeds, there are some issues with volumetric approaches. The main issue is the nature of the resin: it must be transparent to the light waves that cure the resin. This means that it isn’t always possible or easy to introduce additives that give the resin its engineering properties. Black resin wouldn’t allow light to transmit very deeply.
Enter DIP, an entirely new approach. While it also uses photopolymer resin, it does so in a completely different manner. Let me explain how this works.
- There’s a print head, which has the ability to to project a light pattern downward
- The print head has a housing on the bottom that can capture some air if vertically submerged in the resin
- The surface of the resin under the print head becomes the projection surface
This is quite unusual: there are resin 3D printers that project top down onto the flat surface of a resin vat. Gravity makes that surface flat, and it can accept the energy from above. In DIP, the projection surface is literally attached to the printhead, where it can move around in 3D space within the liquid resin.
There’s more:
- That air space under the print head forms a curved surface
- The projection must account for the curve
- The specific curve can be tweaked using an acoustic projector on the print head
- The curve can be adapted to encourage maximum flow of new material into the printing region
Because the curve’s geometry is controlled, it’s then possible to have the slicing software consistently understand the shape of the projection surface.
This is extremely interesting. Many of today’s resin 3D printers suffer from a big issue: waiting for fresh resin to flow into the spaces where new layers of printing can take place. This flow issue is perhaps the major barrier in achieving higher print speeds. However, DIP seems to have overcome this problem with an acoustic solution. They say it can increase resin flow rates by an incredible 10X.
The prototype device built by the researchers was able to print at incredible speeds, even outstripping some volumetric approaches. In their paper, they say that they measured the ability to print 10,000 cubic mm per minute! For reference, the fastest desktop FFF 3D printer, the FLSUN S1, has a volumetric flow rate of “only” 110 cubic mm per second, or 6600 cubic mm per minute. Typical desktop 3D printers are able to hit around 1800 cubic mm per second.
The most amazing thing, however, is that the resin used by DIP can have any additives you want. It’s doesn’t require transparency because it brings the “resin window” along with the print head.
One potential issue is that the system devised by the researchers has a relatively small build volume. They have successfully printed centimeter-sized objects. However, since the print head can be moved about in 3D space, it should be possible to print large objects by taking more time to move around in a bigger vat.
DIP is perhaps the most promising new 3D printing process I’ve seen in recent years. I’m sure we’re going to see a lot more about it.
Via Nature