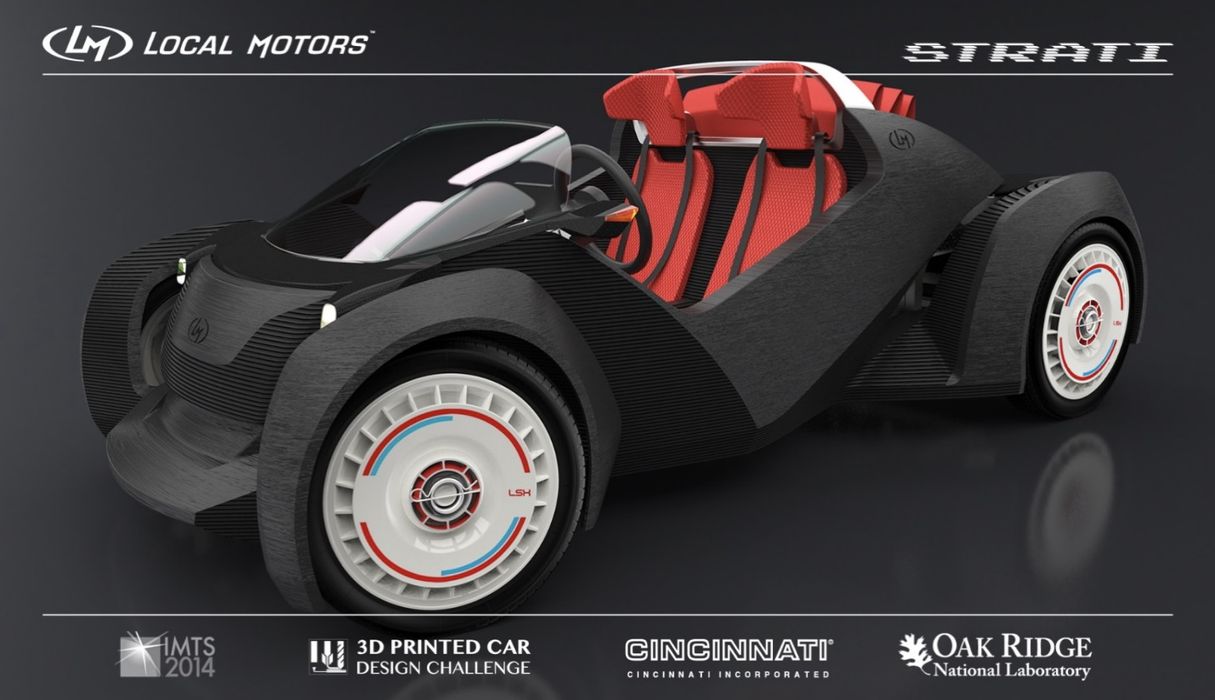
SPONSORED CONTENT
In 2014, 114,000 attendees and exhibitors at IMTS – The International Manufacturing Technology Show – witnessed the world’s first 3D printing, post-processing, and building of a car on the show floor in six days.
A box of plastic pellets and a pile of mechanical and electrical parts were assembled into a working vehicle before one’s eyes.
In early June 2014, Local Motors finished a design challenge in which an Italian designer, Michele Anoè, submitted beautiful renderings of what a 3D-printed community electric vehicle might look like. With support from AMT – The Association For Manufacturing Technology (the owner and operator of IMTS), Local Motors and teams from Oak Ridge National Laboratory, Cincinnati Incorporated (where, at the time, I worked as manager of market development), the U.S. Department of Energy, SABIC, Techmer, TW Womer & Associates LLC, AlphaSTAR, and Thermwood made the impossible happen.
Since no one had printed the structure of a car before, Local Motors developed the idea of a drive system mule. A center part of the frame was printed in smaller pieces and bonded together, and the drive system from a European city car from Renault called a Twizy was bolted on. It was surprisingly solid. A few laps in the Chandler, Arizona, Local Motors microfactory parking lot allowed the team to see the vision and move forward.
Printing the body would be more of a challenge. One big challenge was printing the fenders. These had a sizeable unsupported area. The system had no provisions for soluble support material, common on small printers. Who would want to put a car body in a swimming-sized pool to wash away supports? They devised an idea for using the reinforced ABS as the support. Where they wanted it to break away, they applied a release agent to the supports so the fender above would not stick. As it turns out, this super-secret release agent is simply baby powder. They even made a programmable dispenser to automatically apply the powder on top of the proper layers.
With the fender problem solved, the team at ORNL started printing the entire car. It ran around the clock for about 100 hours. Whenever a layer stopped, the head would pick up, leaving a nub of carbon fiber-reinforced plastic sticking up. When the head came around on the next layer, it would tear off the tamper foot. They had a team of people with long tools that would reach over the safety enclosure and knock down the nubs before the head came back around.
When they were finished, there was a problem. When printing large parts, you have to print slowly enough that the part does not get too hot. The layers have to cool off enough to be firm enough to support the layers above them. If they go too slow, the layers below will be too cool, and the new bead will not stick properly. With a 100-hour build, the base layer was too cool for the new layers to stick. The car delaminated between layers.
How to print faster? First, they removed the fenders. They could easily print fenders on their sides without the support material and bolt them on later. This removed not only the time to print the fenders, but also the time to print the support material.
Next, they looked at modifications to the extruder to see if they could get more output. A consultant, Tim Womer, looked at the commercial extruder and had a lot of questions. The extruder screw was not conventional. The European design extruder was used to weld plastic sheets together. The design could use pellet feedstock, or it could use a plastic rod. The top of the screw was fluted to grind up the rod. Tim redesigned the screw and built a new one that was tested on the show floor at IMTS in the days just before the Strati was printed.
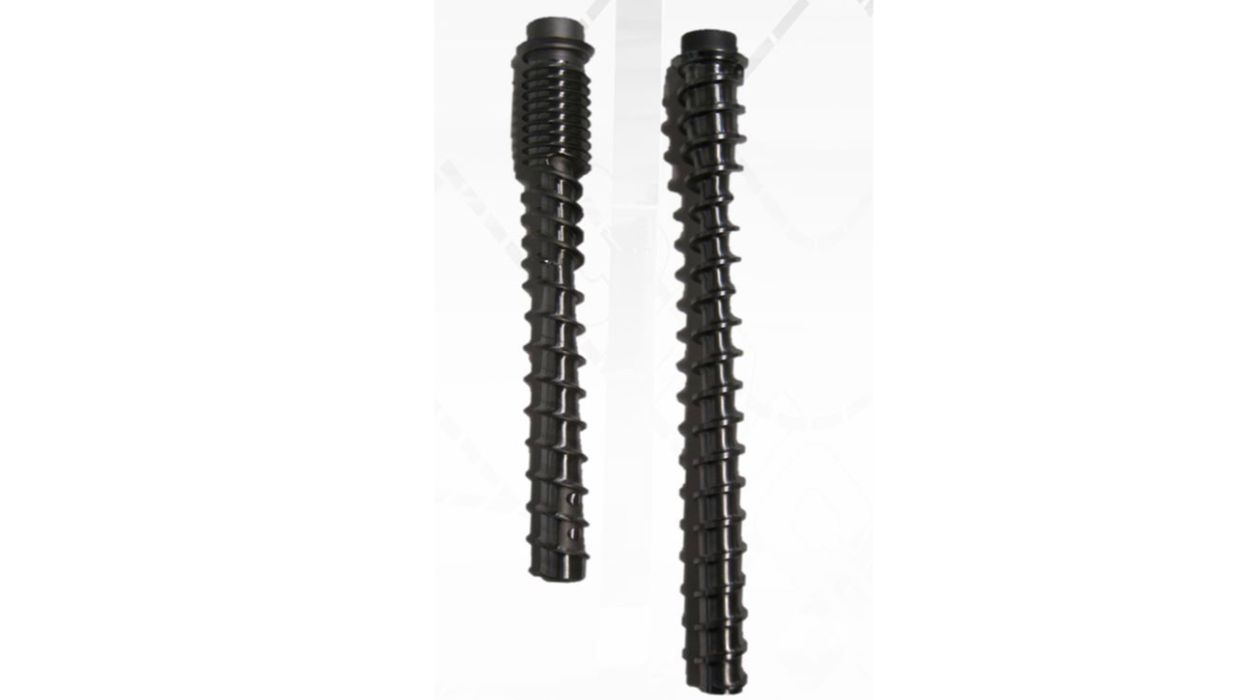
It was calculated that the extruder could double the output from the original, but would this be fast enough? ORNL, working with a finite element analysis company, ALPHAStar, simulated the entire building process, including the cooling rates of the material. They showed that the residual stress in the body would be so much less that they had some confidence that it would work.
An intern, Andrew Messing, at ORNL, looked at the problem of the plastic nubs at the end of each layer. He thought they could eliminate the head crashes if they could use the tamper foot on the BAAM to tamp down the nubs while they were still hot. He wrote a subroutine to move the head around in a circle before picking up. The tamper would nicely tamp down the nubs. It was first tested again on the show floor at IMTS, and it worked. The problem of crashing the head was eliminated during the actual print with a simple programming change.
Once the part was printed, the next job was to machine the smooth sections and accurately machine where the drive components would be added. As part of the contract of the machine sale of a sizeable 5-axis router to Local Motors, Thermwood agreed to supply expertise to machine the Strati on the show floor. In front of hundreds of people, they had to write and test the program to machine the body. As it cooled, it shrank a little, so, to accurately machine a surface, you first had to locate it. Without the expertise of Brent East at Thermwood, the Strati could have been destroyed by post-processing machining.
The assembly of the Strati was one of the most manageable parts. A big team could do most of the work in about a day. They unbolted some parts and bolted them back on during the week to keep the demonstration fresh. One big problem was with the fenders. When they bolted on the fenders, they realized the tire hit the front fender when the steering wheel was turned. The team jumped into action, and with the magic of 3D printing, they could redesign and reprint new fenders in hours.
One of the most frequent questions at the show was the car’s crashworthiness. Strati, of course, had not crash-tested one, as there was only one. One of the Local Motors salespeople took a hammer out of a toolbox and pounded on one of the extra fenders to show the durability. It was surprisingly loud, and the fender seemed unphased. This quickly put questions of crashworthiness to rest.
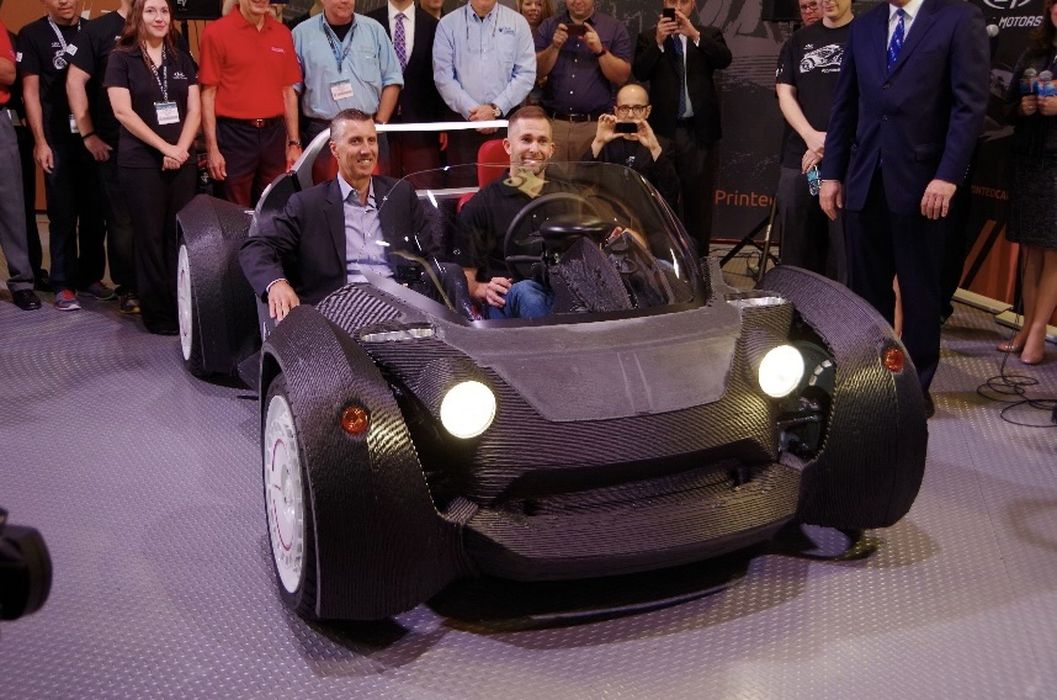
Saturday of IMTS 2014 was the big day. With Jay Rogers, Local Motors CEO, at the wheel and Doug Woods, AMT president, in the passenger seat, Strati left the exhibit, drove across the bridge to the East Hall of McCormick Place and out into the real world, where an anxious press and fans on the plaza in front of the venue greeted them.
To learn more about the journey and meet the individuals who made it possible, visit IMTS 2024 and explore firsthand the magic that unfolded in Chicago in a special 10th Anniversary exhibit of the Strati.
Make your plans to attend IMTS 2024, Sept. 9-14 at McCormick Place in Chicago. Register at IMTS.com/Register.
And, mark your calendar for Formnext Chicago, April 8-10, 2025, at McCormick Place in Chicago.
About IMTS 2024
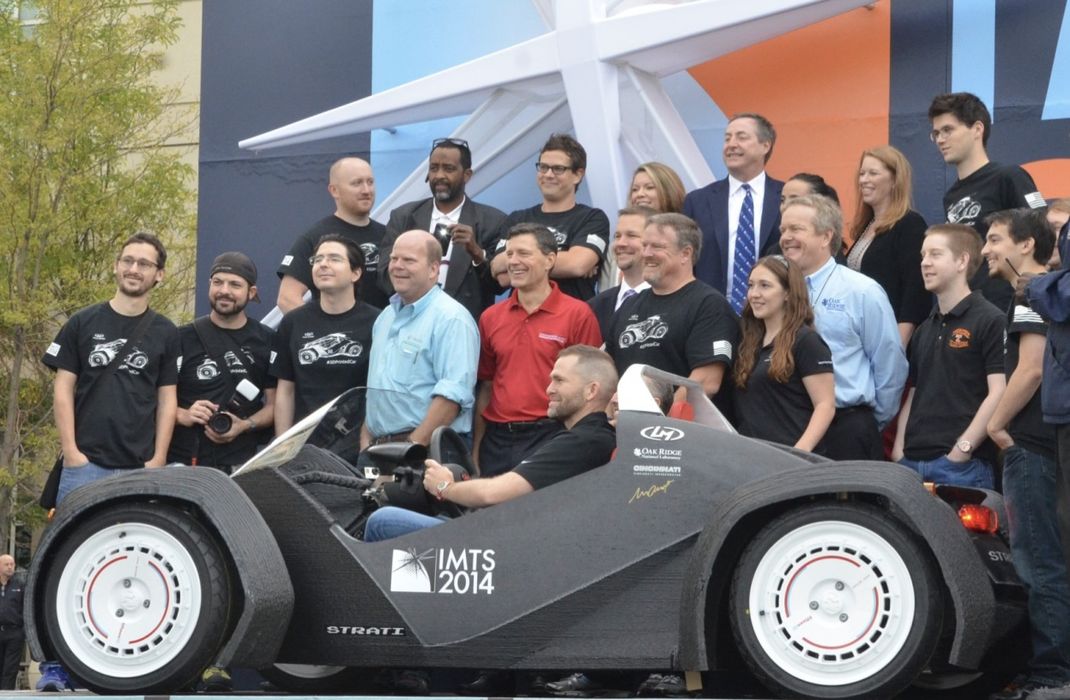
Teammates from AMT, Local Motors, Oak Ridge National Laboratory, the U.S. Department of Energy, Advanced Manufacturing Office, and Cincinnati Incorporated pose with Strati on McCormick Square [Source: AMT]
IMTS – The International Manufacturing Technology Show is where the creators, builders, sellers, and drivers of manufacturing technology come to connect and be inspired. Attendees discover advanced manufacturing solutions that include innovations in CNC machining, automation, robotics, additive, software, inspection, and transformative digital technologies that drive our future forward. Powered by AMT – The Association For Manufacturing Technology, IMTS is the largest manufacturing technology show and marketplace in the Western Hemisphere. With more than 1.2 million square feet of exhibit space, the show attracts visitors from more than 110 countries. IMTS 2022 had 86,307 registrants, featured 1,816 exhibiting companies, saw over 7,600 people attend educational events, and included a Student Summit that introduced the next generation to manufacturing. Be the change at IMTS 2024, Sept. 9-14, 2024. Inspiring the Extraordinary. IMTS.com.