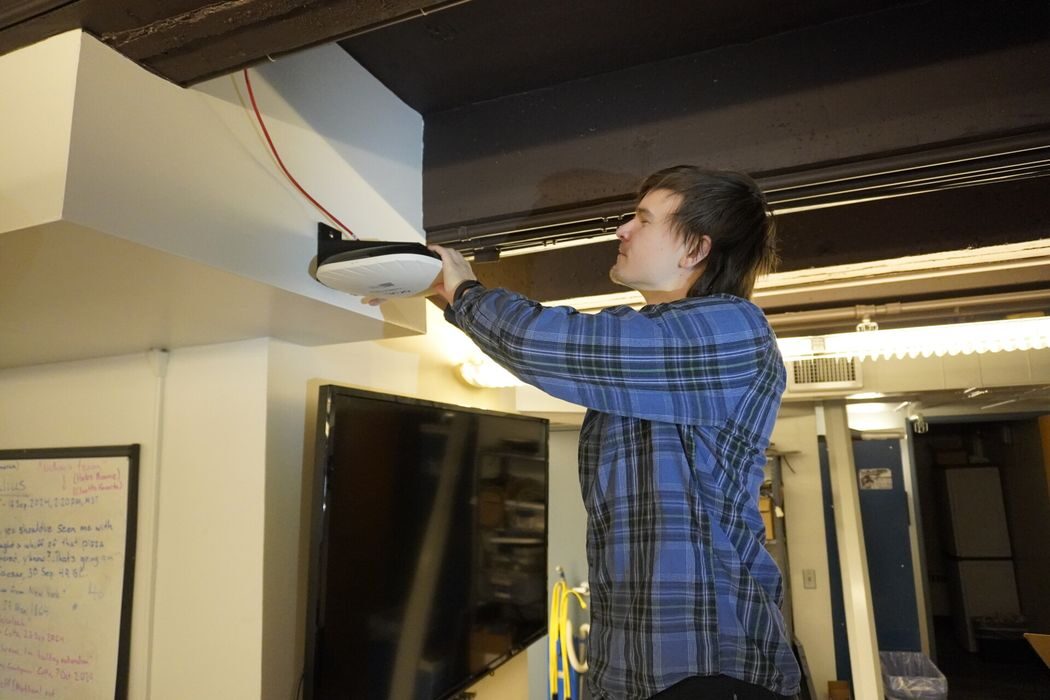
Ingenuity combined with 3D printing solved a networking problem at Colorado State University.
Students at the university consistently encountered problems with the campus WiFi network. Network coverage seemed poor, resulting in all manner of annoying issues, particularly in these days where everything is online.
This shouldn’t have been the case, since WiFi routers were installed everywhere. An investigation ensued, and the problem was identified. There were two types of WiFi access points installed on campus: ceiling and wall-mounted. These two types of access points have different coverage zones, each designed for their mount orientation.
Unfortunately, it turned out that a number of ceiling-style access points had been installed vertically on walls. This meant their coverage was heading up and down instead of sideways down hallways and rooms as intended.
A solution was devised by student and staff technicians. They designed a replacement mounting bracket that would reorient the errant access points, pointing the signal towards occupied areas.
But could they really work? A major concern was whether the 3D-printed brackets could hold the weight of the commercial access points.
Third-year student technician Devin Kaufman explained:
“I had zero expectations going into the weight testing. Seeing our prototype hold around 45 pounds was incredibly exciting. It feels good to contribute something meaningful and leave a mark on the college before graduating.”
This project was not only a technical success but also a financial one. The brackets were printed at a cost of around US$2 each, compared to US$100 commercial alternatives. With 850 access points involved, this amounted to a savings close to US$100,000.
This is the benefit that can be achieved when one truly leverages the ability to produce parts on demand using 3D printing. Individuals often design and print replacement parts on their home 3D printers, sometimes saving a bit of money.
But the real advantage is when businesses recognize an opportunity to solve a problem at scale, just as the Colorado State University technicians did.
What 3D print opportunities exist in your organization?
Via CSU