SPONSORED CONTENT
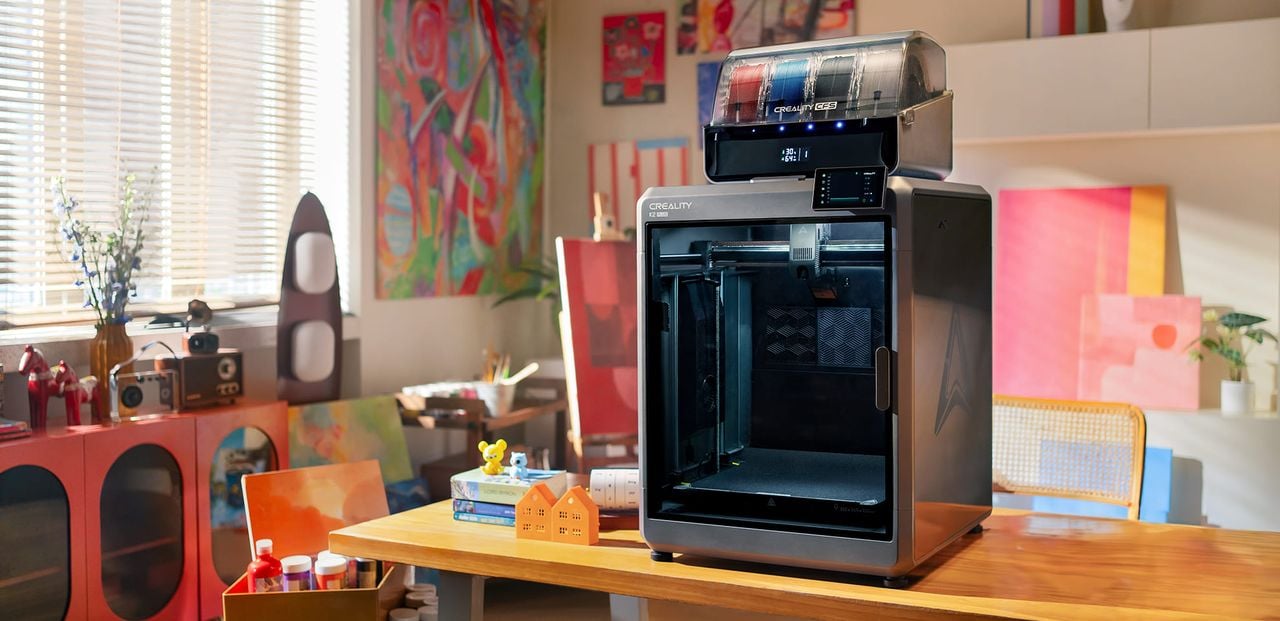
Today is the day Creality launches their long-anticipated K2 Plus Combo in their online store.
This device is quite remarkable in several ways and should be considered for professionals and even production uses.
What makes the K2 Plus Combo different? At first glance, the 3D printer is a large device, offering a build volume of 350 x 350 x 350 mm. There are other 3D printers with similar or even larger build volumes, but there are a number of very important internal differences on the K2 Plus.
Creality has supercharged the motion system on the high-speed K2 Plus by implementing several new features, such as a far more robust frame. But by far the most notable is the introduction of servo motors on all axes of motion.
Servo motors differ significantly from the stepper motors typically used in 3D printers. Servo motors use a feedback system to provide precise control over position, speed, and torque. They adjust dynamically based on sensor input, making them ideal for applications needing high accuracy and power.
Meanwhile, stepper motors move in discrete steps and do not use feedback, relying on input pulses for movement. This makes them simpler and often more cost-effective, suitable for tasks that require less precision. However, they can lose steps under load without feedback, unlike servos which correct their position.
Creality said the servo motors used have 32,768 steps on each turn and can generate printhead acceleration up to 30,000mm/s/s.
As far as we know, this is the first time industry-grade servo motors have been used on a desktop 3D printer that you can purchase, and is a significant differentiator between Creality and the competition.
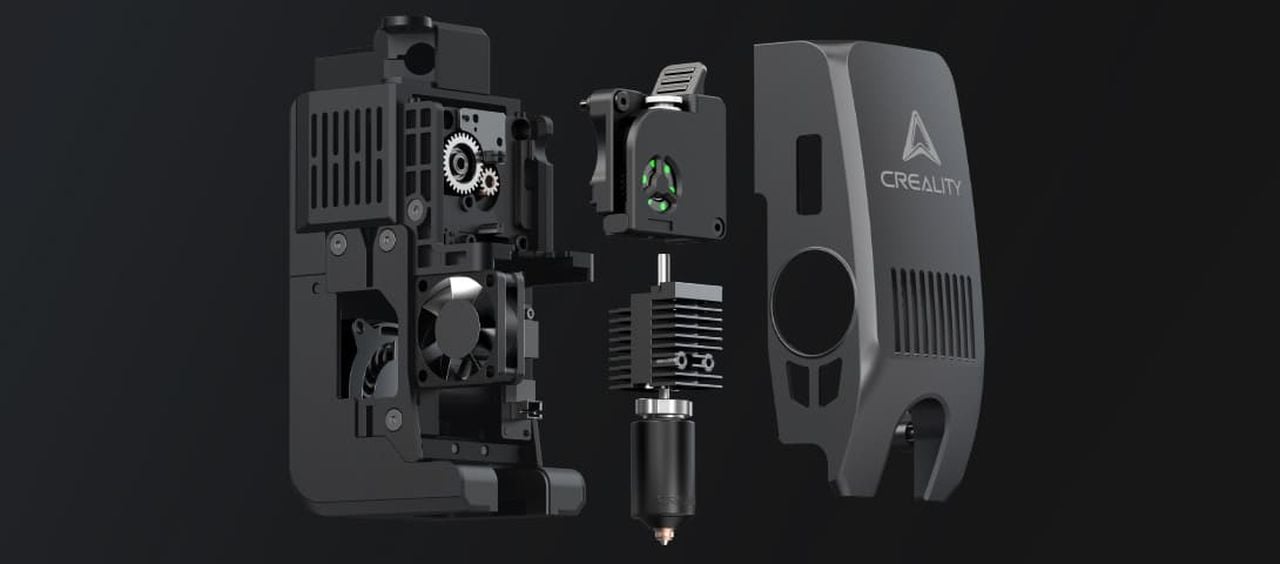
The K2 Plus is highly compatible with a wide range of materials. Its hardened nozzle can withstand abrasive filaments, including carbon fiber. The hot end can also reach 350°C, enabling the use of more engineering materials.
The build chamber of the K2 Plus is actively heated and can reach up to 60°C. This dramatically reduces the thermal gradient between the fresh and previously extruded material and should eliminate warping of many materials.
A key specification is the maximum volumetric flow rate, which is the amount of material that can be deposited by the printhead. This governs the maximum print speed. Typical high-speed 3D printers have a rate of around 30 cubic mm/s, while the K2 Plus can hit 40 cubic mm/s.
Calibration on the K2 Plus is largely automated, and there’s an interesting feature I haven’t seen previously. Creality explains:
“With two Z-axis independently motorized, it can auto-adjust bed tilt before auto-leveling. So, everyone can get an expert-level first layer hands-down.”
Finally, the K2 Plus is quite intelligent. It apparently includes 18 different sensors, which are monitored by the firmware. There are two onboard webcams, one monitoring the chamber for print failures, and the other on the toolhead looking for extrusion issues. This is the only desktop 3D printer I know of that has dual AI webcams in this configuration.
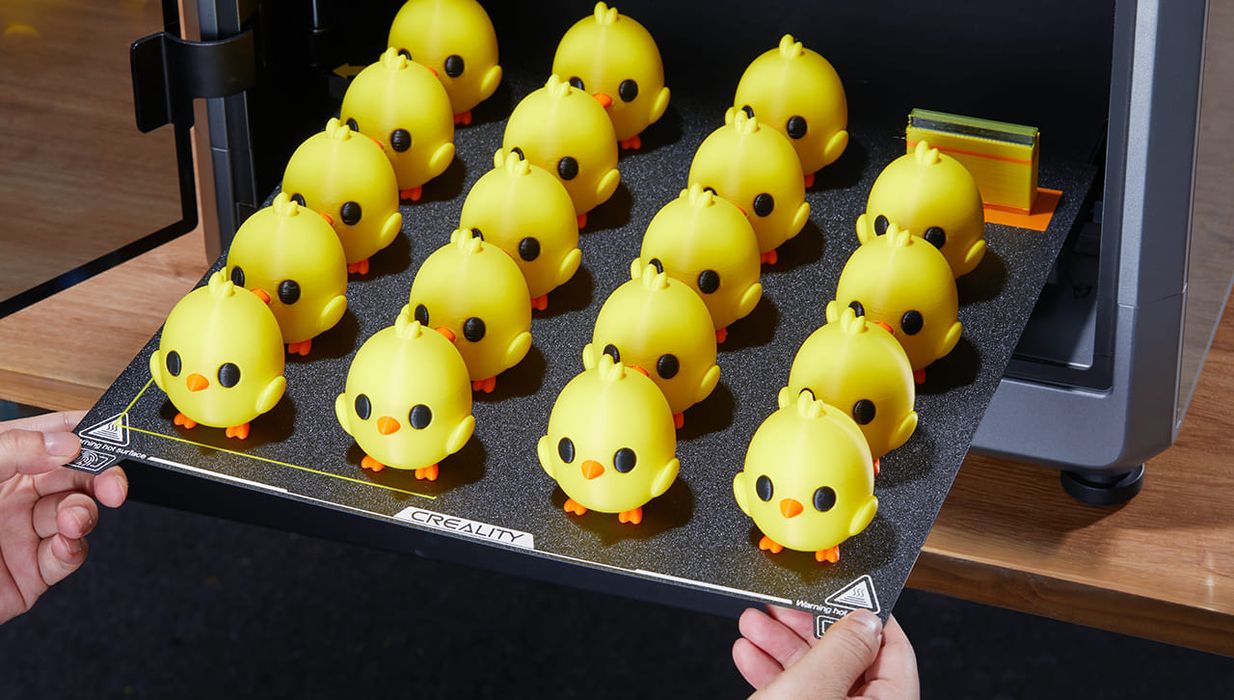
The K2 Plus is the 3D printer, but the “Combo” portion of the bundle adds the CFS, “Creality Filament System”. This is an accessory that provides for filament swapping in mid-print, enabling multicolor 3D prints. There are some slowdowns in print jobs due to the time required to swap filaments, but multicolor objects can easily be created.
The CFS system holds up to four 1kg standard filament spools, and these can be different colors or the same color. Why use the same color? The machine is able to automatically swap to a second spool of the same filament should the first spool run out. This is a very valuable feature on a large-format machine like the K2 Plus: The machine keeps going even if a spool runs out.
It’s also possible to add more than one CFS to a K2 Plus. The system supports up to four CFS units — which can be stacked together. This means a single print job could theoretically be made from up to 16 different colors.
There’s another twist to the CFS story: the spools don’t have to be different colors — they can be different materials. If the hot end temperatures are not very different, it’s possible to mix materials on a single print job.
The key use case for this would be the use of a support material, either breakaway or soluble. As the print proceeds, the top layer of the support structure can be printed with the support material, enabling both smooth surfaces and easily removed support structures.
The K2 Plus Combo looks to be a very powerful system for many professionals. It’s now available at these online stores: