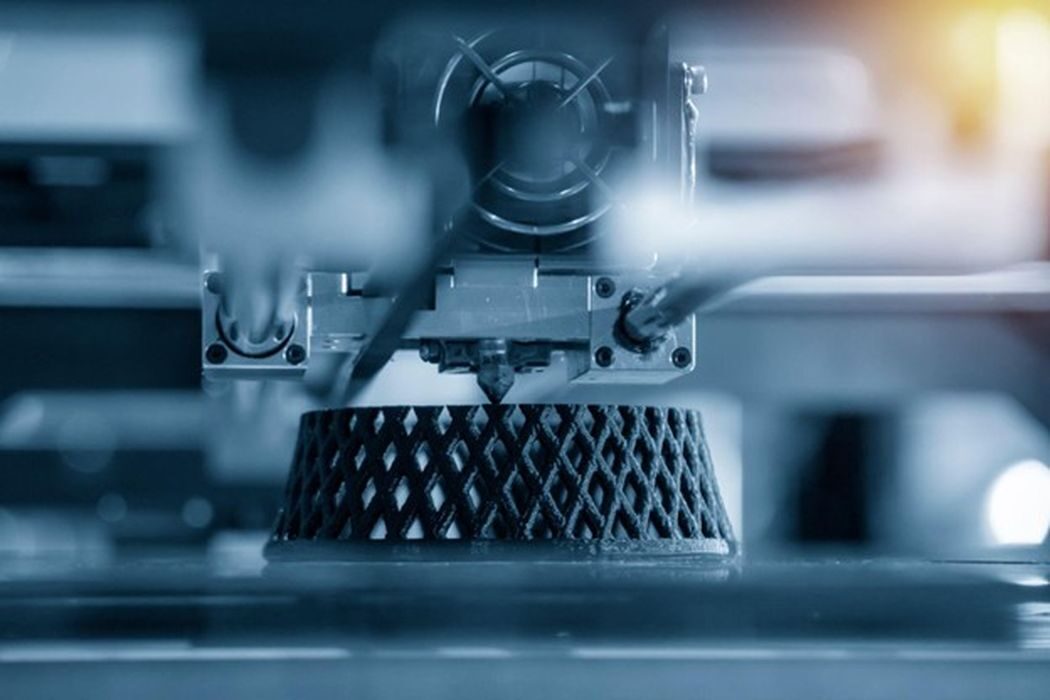
Why differences in speed, cost, and other considerations are not as simple as you might expect.
Over my 24+ years in custom manufacturing, I have witnessed many changes, while some things have remained the same. Many hoped for 3D printing to replace traditional manufacturing methods like injection molding, but that reality has not yet come to fruition. Looking back on the early days of my career, I had expected that tipping point to have already passed by now.
With so much interest in additive manufacturing taking over as our first choice for producing new products, what went wrong? It turns out injection molding offers distinct advantages over additive manufacturing, especially for larger-scale production, with which 3D printing has yet to compete. While there are circumstances where additive manufacturing makes more sense, traditional injection molding remains the dominant method for the production of most plastic products.
This article discusses common misconceptions about each process and compares them to determine when each is most appropriate to use. By reviewing the speed, setup, and running costs, as well as the material prices for each process, it will clarify when each technology has the advantage.
Misconception 1: Additive manufacturing is ALWAYS faster
3D printing is known for its speed. If you need to get a few designs made for testing and confirmation, there is no quicker way than 3D printing. The issue comes when you need to ramp up to production quantities.
Where a 3D printer can make a handful of parts in a couple of days, producing a large number of parts can take a good bit longer. Even with a process like MultiJet Fusion (MJF) that allows for nesting to maximize printer utilization without support removal, a 4” x 2” x 1” hollow box would take 3-5 days to build and cool only 200 parts. Add to this the time it would take a technician to break the parts out of the build bed, bead blast, and dye all of the parts and you could easily be looking at several weeks for 600 parts. Other 3D printing processes would take even longer, like stereolithography (SLA) and fused deposition modeling (FDM), due to the need to remove supports after building and removing them from the build platform.
Injection molding, on the other hand, is believed to be a really lengthy process that could never compete with additive manufacturing for speed and efficiency. This may be true for large production tooling with 32 cavities that would take between 10 and 16 weeks to produce. Still, if you are considering additive manufacturing as a solution, you aren’t likely to need the millions of parts that this type of tooling would produce.
With the lower volume projects that additive manufacturing would compete for, you would likely be looking at a single cavity injection mold, which could be built in 2-3 weeks in many cases. So, let’s take our sample part from above and see how quickly we could expect 600 parts from injection molding. The tooling would take 2.5 weeks for building and sampling. Once approved the parts could be produced with a 30-second cycle time per part, but to be conservative, let’s assume 1 minute per part. This means we can produce 60 parts per hour or have the 600 parts from the example above in less than 1 day.
Then, when it comes to future orders, there is really no comparison. Injection molding would allow the tooling to be set up and run in around 1 week for subsequent 600-part orders, but additive manufacturing would require the same 3 weeks as the original order. A larger follow-up order would only exacerbate the differences between the processes.
Misconception 2: Additive manufacturing is cheaper until you are making more than 10,000 parts
3D printing does hold the advantage that you don’t have to create a tool in order to produce your parts, which for small quantities makes it the obvious choice. However, the belief that this is tens of thousands of parts before injection molding cuts in is not true for many projects, or our example.
The cost per part for additive manufacturing is mostly built on material costs, machine overhead, and labor for finishing. All three of these are pretty consistently high, which means that the economies of scale for additive manufacturing are not very good. For our example part, the cost per unit for 50 parts would be around $13.45 each, and for our 600-part order, it would cost around $12.01 each. So, our original order of 600 would be $7,206 to print.
If we look at injection molding the same parts, we do have to consider not only the cost of the material, machine overhead, and labor to run the parts but also the cost of the tooling to produce the design. This cost is perceived to be very high but in reality it can be a lot more reasonable than many people think. For this simple tool, we would be looking at a tooling price of $5,050 with overseas production. This tooling would be a single cavity steel mold capable of producing 100,000 parts or more before it would need extensive maintenance or grooming.
Since the materials for injection molding generally are not as specialized as 3D printing, the price per volume can be much lower. In our example, a kg of printing material can be over $100, but for moldable thermoplastic around $3-5. Add to this the fact that the parts run faster with less labor, and you have a recipe for much cheaper parts. At 600 parts the price per part would be $1.34 for a total for parts of $804.
Once we add the tooling into the parts and amortize it on a per-part basis, you can get injection molded parts for $9.76 per part compared to additive manufacturing at $12.01 each. That leaves a $1,352 advantage for injection molding our 4” x 2” x 1” box over printing them at a quantity of 600 parts The cost curve below illustrates the difference between the processes at a sampling of different quantities, with the break-even being around 500 parts.
Read the rest of this story at ENGINEERING.com