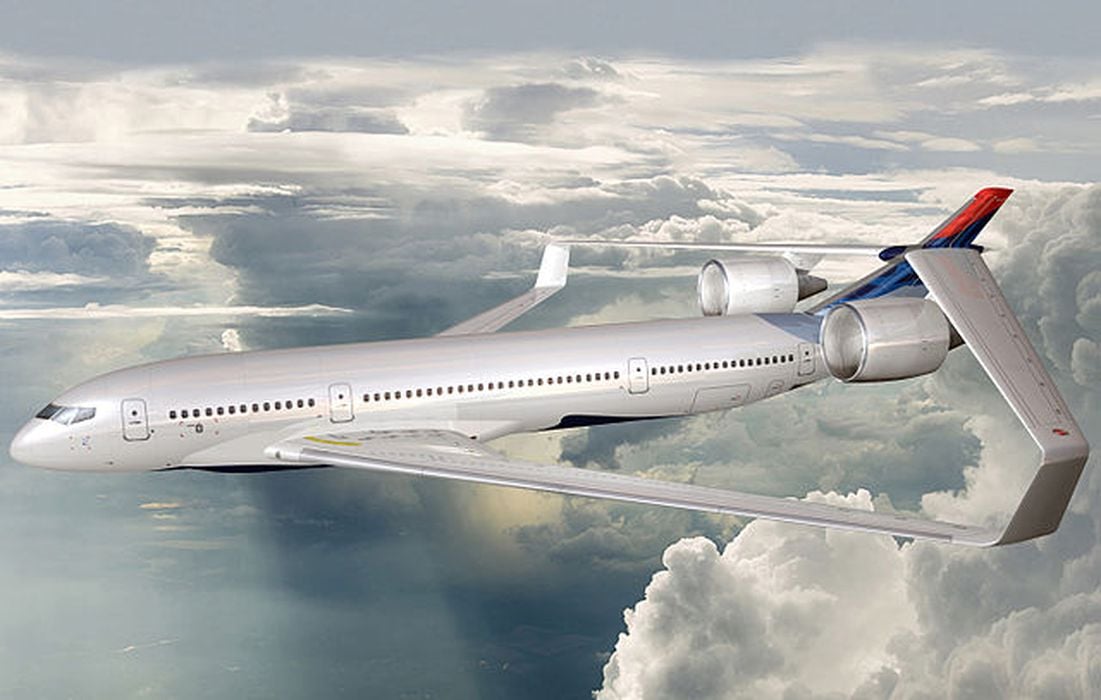
Charles R. Goulding and Preeti Sulibhavi explore how Airbus, Dassault, Rolls-Royce, and others are using additive manufacturing to drive military innovation and enhance European security.
European defense has long faced the challenge of fragmented markets and budgetary constraints. Guillaume Faury, CEO of Airbus, has highlighted the importance of consolidating efforts between FCAS (current members are Germany, France and Spain, alongside companies such as Airbus and Dassault Aviation) and GCAP (UK, Italy, and Japan alongside companies such as BAE Systems, Rolls-Royce, Leonardo, and Mitsubishi Heavy Industries) to ensure optimal use of financial and technological resources. Additive manufacturing aligns seamlessly with this vision by offering innovative solutions to streamline production and enhance collaboration across borders.
The defense industry is experiencing a paradigm shift, fueled by the innovative application of 3D printing, or additive manufacturing. This technology is increasingly pivotal in modernizing production, enhancing performance, and reducing costs in European defense. In tandem with programs like the Franco-German Future Combat Air System (FCAS) and the UK-led Global Combat Air Programme (GCAP), additive manufacturing is proving indispensable for advancing European defense capabilities.
3D printing’s ability to create complex components with reduced material waste and faster production times is invaluable for programs like FCAS and GCAP, which require cutting-edge technology to develop next-generation fighter jets, drones, and sensors. By fostering synergy between these rival programs, Europe can maximize the benefits of 3D printing and maintain its competitive edge in the global defense market.
Rolls-Royce: Pioneering 3D Printing for Aircraft Engines
Rolls-Royce, a leader in aircraft engine manufacturing, has been a frontrunner in applying 3D printing to enhance performance and reduce costs. The company has used additive manufacturing to create fuel nozzles, heat exchangers, and other intricate components for its engines. One notable success is the use of 3D printed components in the UltraFan engine, a revolutionary powerplant designed to improve fuel efficiency and reduce carbon emissions.
The UltraFan engine incorporates titanium and nickel-alloy parts manufactured through 3D printing, which allows for complex geometries that traditional methods cannot achieve. These components are not only lighter but also more durable, contributing to enhanced performance and lower maintenance costs. Rolls-Royce’s advancements in 3D printing are instrumental for programs like FCAS and GCAP, which demand state-of-the-art propulsion systems.
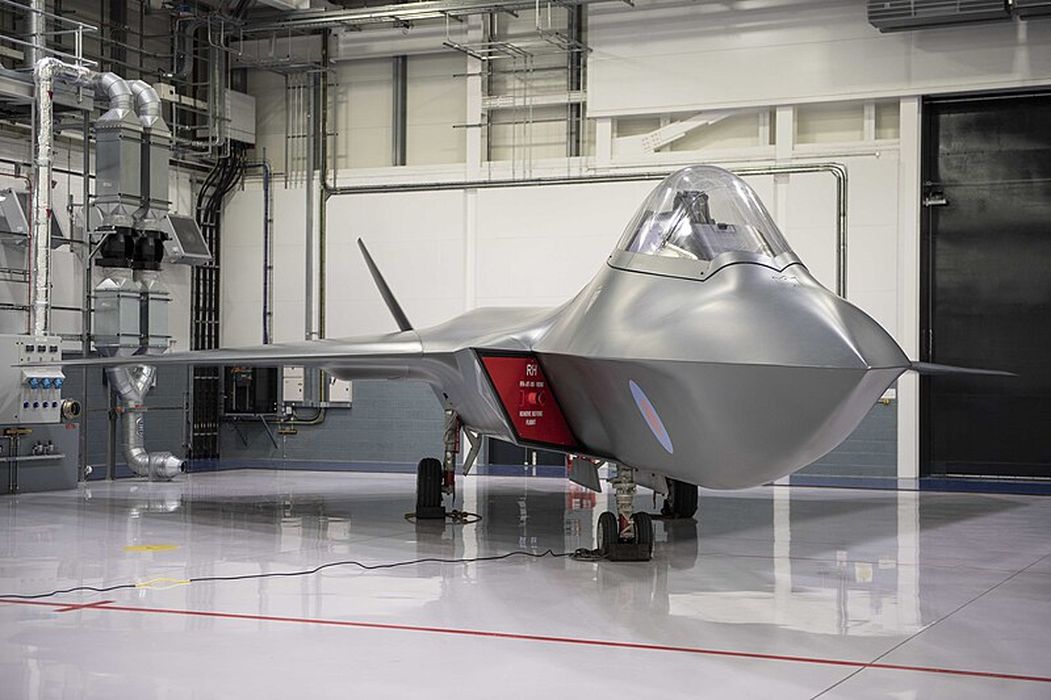
BAE Systems: Additive Manufacturing for Combat Air Systems
BAE Systems, a key player in the GCAP initiative, has embraced 3D printing to expedite development and reduce costs for advanced military systems. The company has integrated additive manufacturing into its production of components for fighter jets, including the Tempest, the centerpiece of GCAP. By using 3D printing, BAE Systems has significantly reduced lead times for producing parts, enabling rapid prototyping and testing.
One of BAE’s notable achievements is the fabrication of lightweight airframe components for the Tempest. These components are critical for achieving the agility and speed required in modern air combat. Additionally, BAE has leveraged 3D printing to produce parts for drones and unmanned systems, which are becoming increasingly important in contemporary defense strategies. The ability to quickly produce and test new designs gives BAE Systems a competitive edge in the fast-evolving defense landscape.
Dassault Aviation: Modernizing Aircraft Production
Dassault Aviation, a key partner in the FCAS program, has also made significant strides in additive manufacturing. The French aerospace giant has utilized 3D printing to produce components for its Rafale fighter jets and is expanding its use of the technology for the next generation of aircraft. Dassault’s focus on 3D printing aligns with its commitment to innovation and sustainability, as the technology reduces material waste and energy consumption.
A prime example of Dassault’s use of 3D printing is the production of aerodynamic components for its aircraft. These parts, manufactured with high-performance polymers and metals, are designed to withstand extreme conditions while maintaining lightweight properties. For the FCAS program, Dassault is exploring the use of 3D printing to create integrated sensor systems and advanced avionics, which are critical for the success of the project.
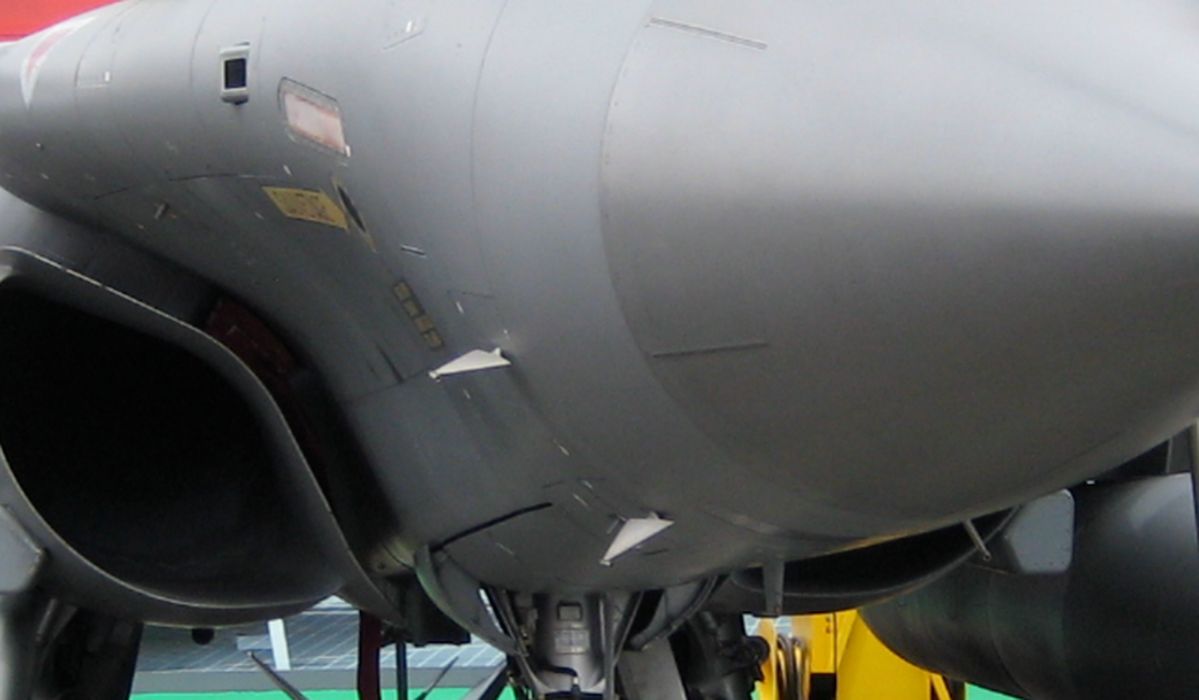
Applications in FCAS and GCAP
The Franco-German FCAS and UK-led GCAP programs represent Europe’s ambitions to develop next-generation combat air systems. Both initiatives aim to integrate cutting-edge technologies, including artificial intelligence, stealth capabilities, and advanced sensors. 3D printing plays a crucial role in these endeavors by enabling the rapid development of prototypes and the production of highly specialized components.
For FCAS, 3D printing is being used to create drone parts and modular components for manned-unmanned teaming. These capabilities are essential for the program’s focus on network-centric warfare, where multiple platforms must operate seamlessly together. Similarly, GCAP benefits from 3D printing in the development of high-performance jet engines, advanced airframes, and sensor housings.
Beyond specific components, 3D printing allows both programs to adopt a more agile development approach. Engineers can quickly iterate designs, test new concepts, and produce custom parts on demand. This flexibility is vital for addressing the complex challenges of developing next-generation combat systems within tight budgets and timelines.
Broader Applications of 3D Printing in European Defense
The benefits of 3D printing extend beyond FCAS and GCAP to other areas of European defense. Additive manufacturing is being used to produce spare parts for military vehicles, reducing downtime and logistical challenges. For example, the German Bundeswehr has experimented with 3D printing to create replacement parts for tanks and armored vehicles, ensuring operational readiness in remote locations.
In the naval domain, 3D printing is being employed to produce components for submarines and warships. The ability to manufacture parts on-site or near operational theaters reduces dependency on traditional supply chains and enhances resilience. European defense companies are also exploring the use of 3D printing for missile components, enabling faster production cycles and improved performance.
The Research & Development Tax Credit
The now permanent Research and Development (R&D) Tax Credit is available for companies developing new or improved products, processes and/or software.
3D printing can help boost a company’s R&D Tax Credits. Wages for technical employees creating, testing and revising 3D printed prototypes are typically eligible expenses toward the R&D Tax Credit. Similarly, when used as a method of improving a process, time spent integrating 3D printing hardware and software can also be an eligible R&D expense. Lastly, when used for modeling and preproduction, the costs of filaments consumed during the development process may also be recovered.
Whether it is used for creating and testing prototypes or for final production, 3D printing is a great indicator that R&D Credit-eligible activities are taking place. Companies implementing this technology at any point should consider taking advantage of R&D Tax Credits.
Challenges and Future Outlook
Despite its advantages, 3D printing in defense faces several challenges. Material certification and quality control are critical issues, as components must meet stringent safety and performance standards. Additionally, the high initial costs of 3D printing equipment and the need for skilled operators can be barriers to widespread adoption.
However, the potential of 3D printing in defense is immense. As technology advances, the range of materials available for 3D printing is expanding, enabling the production of increasingly complex and high-performance components. Collaboration between European nations, as advocated by Airbus’s CEO, Guillaume Faury, can further accelerate the adoption of 3D printing by pooling resources and expertise.
In the coming years, 3D printing is expected to play a central role in shaping the future of European defense. From enhancing the capabilities of programs like FCAS and GCAP to improving logistics and sustainability across the defense sector, 3D printing is revolutionizing how Europe designs, manufactures, and deploys its military systems. By embracing this transformative technology, European defense companies and nations can ensure they remain at the forefront of innovation and preparedness.