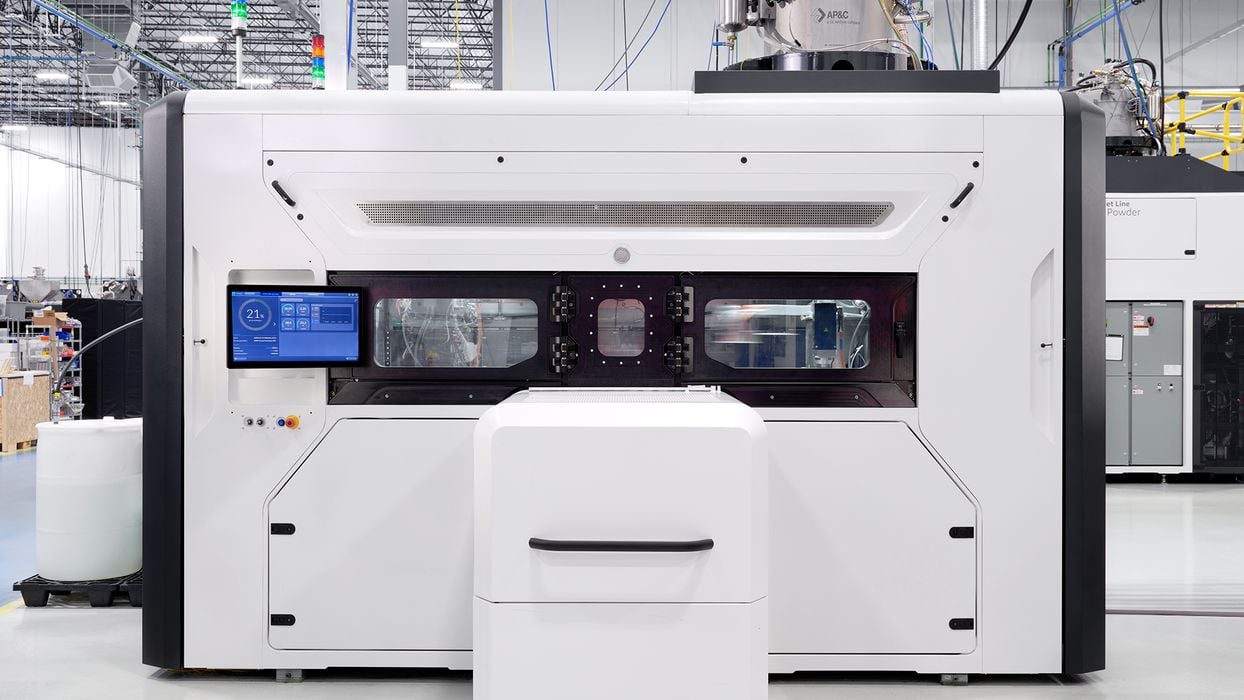
Colibrium has released details about their new Series 3 binder jet metal 3D printing system.
The company, formerly GE Additive, is known for their two lines of metal 3D printers they acquired some years ago: ARCAM, which prints with electron beam technology, and Concept Laser, which uses an LPBF process. The new addition is a binder jet system that offers a third process for building metal objects.
Why introduce a third process? It’s because there are different goals for this machine, specifically to enable large-scale manufacturing using 3D print technology. Up to now large-scale manufacturing has been very challenging for several reasons:
- Print durations are long
- Materials are expensive
- Machines are expensive to operate
- Considerable post processing is required
- Complex air handling is required for safety
Colibrium’s new binder jet technology addresses each of these challenges with its very different design. The binder jet process involves sweeping a large toolhead over a bed of powder and selectively dropping binder. Layer after layer, an object is built up and then undergoes a de-binding and sintering process to finalize the object.
I was able to handle one of the green parts that came fresh of the binder jet, and found that it was incredibly hard as compared to most green parts. Typically green parts are quite fragile and require careful handling. That’s not the case with Colibrium’s process, which should allow for more effective handling of printed parts.
The key to the binder jet system is its material handling system, which dramatically simplifies the work required and increases safety.
Operators need only deliver drums of material powder to a central MHS, which then uses a closed-loop network of ducting to send materials to machines requiring powder. In other words, the operator never needs to load materials into the machine directly.
Even better, the MHS and ducting network is fully capable of handling reactive powders. Colibrium explains:
“The Series 3 is designed to UL and CE standards, has an inert and sealed environment and powder-free exposure (closed loop), is intended to be fully capable of handling reactive and flammable binders and powders, and does not require hazard zoning.”
That’s very different from most LPBF operations.
Another difference is operational cost. Colibrium has committed to driving the cost per volume down as low as possible for this technology. The pricing depends on the specific material being used.
Finally, there’s scalability. The MHS is able to handle multiple 3D printers by distributing powder, and Colibrium is hoping to enable configurations of more than 100 3D printers in a single installation. If achieved that will most definitely be large-scale manufacturing using 3D print technology.
Via Colibrium