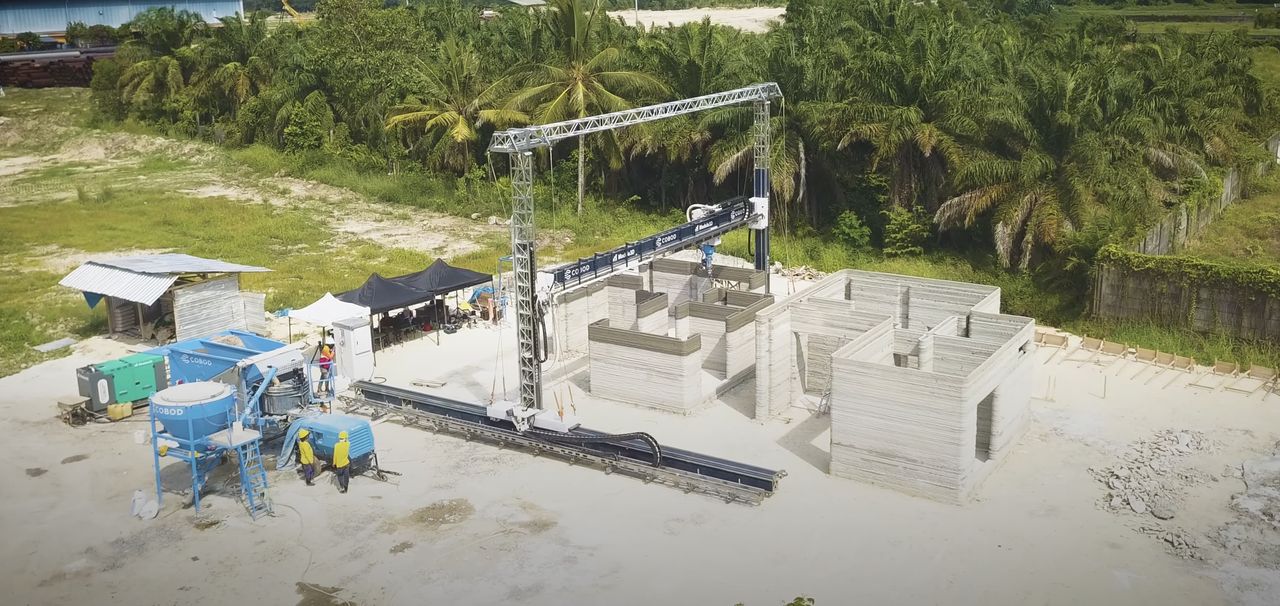
COBOD launched their latest construction 3D printer, the BOD3.
Denmark-based COBOD is one of the few companies producing large-format 3DCP equipment, and the BOD3 is their third generation device. Each generation has improved the technology, and the BOD3 continues doing so.
Like the previous 3DCP printers from the company, the BOD3 extrudes concrete to produce entire buildings — or at least the concrete portions of them. The BOD3 carries on with the gantry approach: it’s much like a desktop FFF 3D printer, except extremely large and printing concrete.
What’s different with the BOD3? The major feature is a track system for movement.
Why is this so important? It’s because of the nature of the gantry system. In previous machines, the gantry would be set up to surround the build site. The BOD2 printer would be able to “reach” anywhere within the gantry’s build volume.
If a subsequent building were required nearby, or a structure larger than the gantry’s build volume, then the entry gantry would have to be disassembled and re-assembled at the nearby site. The process of taking the machine down and up repeatedly is very time consuming and significantly adds cost and delays to larger projects.
The BOD3 seems to solve this. Basically the extrusion systems is on rails, and they can be extended as long as required. This means that a project with a larger build volume might be able to just slide the printer down the rails and continue printing. Rails can then be moved from completed areas to new extensions, providing infinite Y-axis reach.
COBOD Chief Innovation Officer Michael Holm explained:
“The advanced ground-based track system was developed as a response to our customers’ needs to increase efficiency and productivity. Now the 3D construction printer can be easily extended, and multiple consecutive structures can be printed with minimal repositioning and zero downtime between projects, making 3D construction printing more efficient than ever before.”
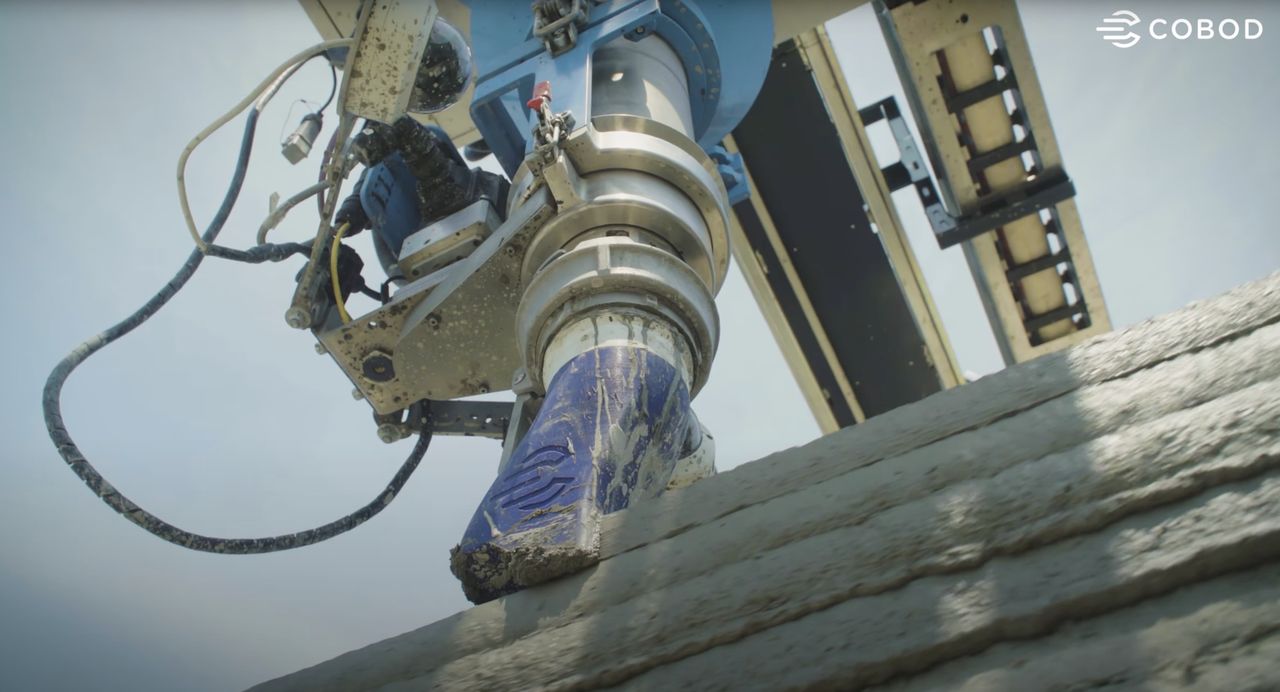
That’s not all. The BOD3 also includes a new Advanced Hose Management System (AHMS) that is able to deliver material and additives in a variable manner. This allows operators to finely tune the concrete mix for different regions of a structure. COBOD explains:
“The Advanced Hose Management System (AHMS) transports 3D printable material from the materials delivery system to the printhead via hoses secured within E-chains, minimizing physical labor and optimizing material flow. With the addition of the dual dosing system for additives, operators can better control the concrete and adapt it to onsite environmental conditions. By introducing additives directly at the printhead, the system reduces drying time between layers, speeding up the overall construction process.”
The BOD3 appears to be a major step forward for the company, as it will lower the costs to for building even larger structures. They should be able to attract more customers with the BOD3.
Via COBOD