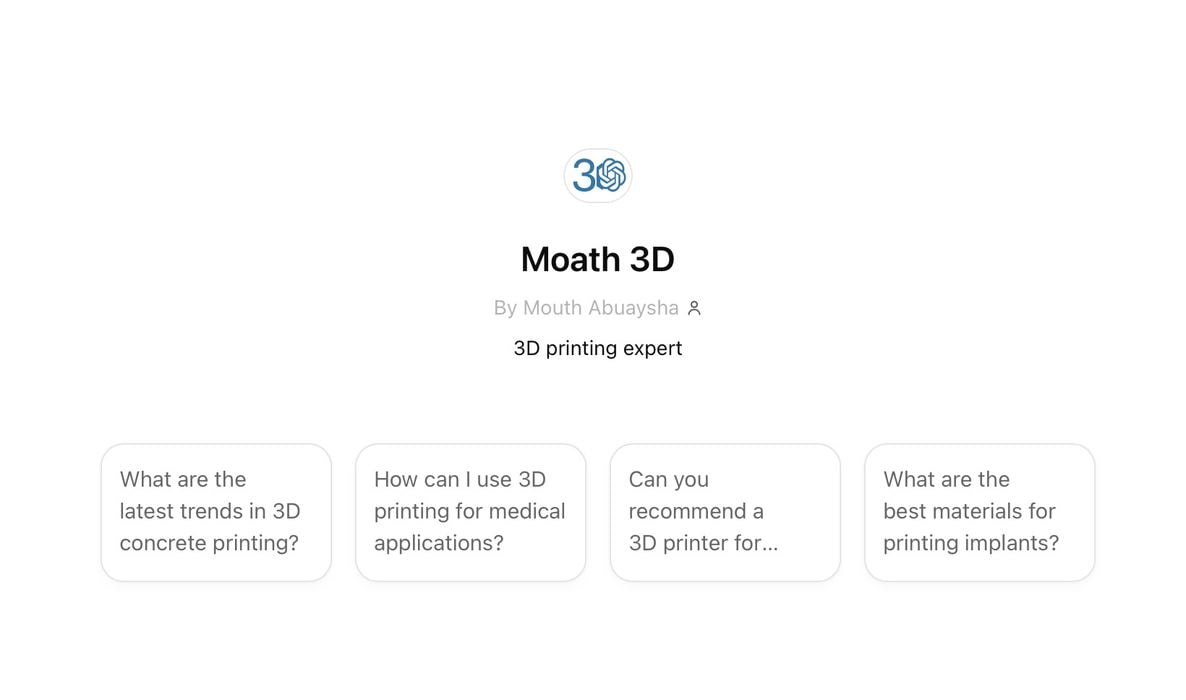
A new GPT offers the ability to chat about 3D printing.
Published as a GPT on ChatGPT by Moath Abuaysha, the chatbot seems to have a considerable amount of knowledge on the topic. According to Abuaysha, the model leverages:
- +15 years of practical experience
- +200M academic papers
- +500 leading platforms
- +100 ISO/ASTM standards
- +10,000 troubleshooting solutions
Note: A GPT is a specially tuned ChatGPT experience, where questions are focused on a particular topic. In this case, it’s 3D printing.
Does it work? I tried several question angles to see what it could come up with.
I asked this:
“I’ve never used a 3D printer before, and am a bit afraid of using one. I have two children that I’d like to introduce the idea of designing and building objects of their own. What should I do?”
The 700 word answer was pretty reasonable. It explained several key steps that the questioner should follow, including: Starting small, Introducing design, Safety, Learning together, Gradual increase in complexity and problem solving. The explanations were of the right level of detail and seemed very positive.
Where the GPT lacked was in specific product recommendations. It correctly suggested Tinkercad as a design tool, but didn’t mention MakerWorld or Printables as model sources.
Let’s try a more technical question:
“I am a metallurgist working at a metal AM provider. We’re setting up a job to produce complex hip joints in titanium, but no matter how we configure the support structure, the prints crack during post processing. What should we do?”
Moath 3D responded with an explanation of how Ti-6Al-4V is quite susceptible to cracking, and suggested pre-heating the build plate and reviewing metal powder quality. For supports, it suggested increasing support density, avoiding sudden support removal, and maximize thermal conduction.
Some of the suggestions were reasonably detailed:
“Stress relief annealing post-print: Implement a stress-relief annealing step immediately after printing. A typical temperature range is around 650-750°C for 2 hours, followed by controlled cooling. This relieves internal stresses without significantly affecting the material properties.
Hot Isostatic Pressing (HIP): Consider HIP as a post-processing step if the parts are still cracking. HIP is highly effective for eliminating internal voids and homogenizing the microstructure of additively manufactured titanium parts.”
I’m not a metallurgist working at an AM provider, but the responses seemed reasonably detailed and might help some operators: “Oh, I forgot to do that!”
Another question:
“We are developing the next technological leap in running shoe technology. What could help our project using additive manufacturing?”
Moath 3D responded with a very comprehensive list of potential benefits to this project, including detailed explanations of:
- Tailored Fit
- Biomechanical Adjustments
- Lightweight Structures
- Multi-Material Flexibility
- Recyclable and Sustainable Materials
- Quick Prototyping
- Testing in Phases
- Energy Return Optimization
- Enhanced Grip and Tread Patterns
- Ventilation and Breathability
- Smart Shoe Integration
- 4D Printing (Shape Memory)
- On-Demand Manufacturing
- Localized Production
- Waste Reduction
- Closed-Loop Production
- In-Silico Simulations
- Modular Design Testing
- Unique Aesthetics
- Personal Branding and Custom Graphics
- Shock Absorption and Durability
- Resilient Performance Materials
That’s quite impressive. The list included only aspects that were directly relatable to the shoe project, as opposed to the typical generic dump of potential AM benefits.
Another question:
“I am designing a rocket for military use, and it must be operational in -40C temperatures, while also handling the high internal temperatures. What would be the best possible materials for the fuselage?”
The GPT recommended a series of likely correct materials, with lists of advantages and disadvantages of each. Interestingly, it offered some design advice:
“In practice, the best material solution may involve layered composites or multi-material designs:
Outer shell of titanium or Inconel to withstand the environmental and aerodynamic stresses at extremely low temperatures.
Inner layers of CFRP or aluminum alloys to provide structural integrity while reducing weight.
Thermal barriers or coatings (such as ceramic coatings) in high-temperature zones to protect heat-sensitive materials and insulate the internal components.”
Finally, it concluded that titanium alloys or Inconel were the best options for this application, with a hybrid materials approach. Quite impressive!
A software question:
“I am starting a small aerospace component manufacturing company, and our designers have to decide which CAD modeling tool should be our standard. What are the options and which one should we select?”
The GPT listed the usual suspects: Siemens NX, CATIA, Fusion 360, SOLIDWORKS, PTC Creo, and Onshape, again with advantages and disadvantages. However, this time it also added a “When to Choose” scenario for each. Finally, it concluded a recommendation for each of three likely business scenarios that weren’t described in the question. Pretty good answer.
Finally, a troubleshooting question:
“I’m printing with my Ender-3 KE, and this one print always stops extruding at about 27mm high. What’s going on? I have good filament, no breaks, and it always happens at exactly this level? How do I fix this?”
The GPT provided a series of items to check, such as Z-axis blockage, stepper over-temperature, filament blocked at a certain height, GCODE problems, etc. In my experience this problem often occurs because the model’s geometry changes, causing changes in hot end temperature. I gave the GPT a bit more of a prompt on this one:
“The model’s geometry gets pretty complicated at that level, would that make a difference?”
Indeed, the GPT did list six different issues that might have something to do with the geometry and how to fix each of them. If I had this problem, I’d probably get it fixed with this answer.
I’m pretty impressed with this GPT. It was basically able to answer with reasonable detail and correct answers. However, I suspect it’s not quite up to date with current products, as they change very frequently.
I encourage you to give Moath 3D a try; it’s fascinating.