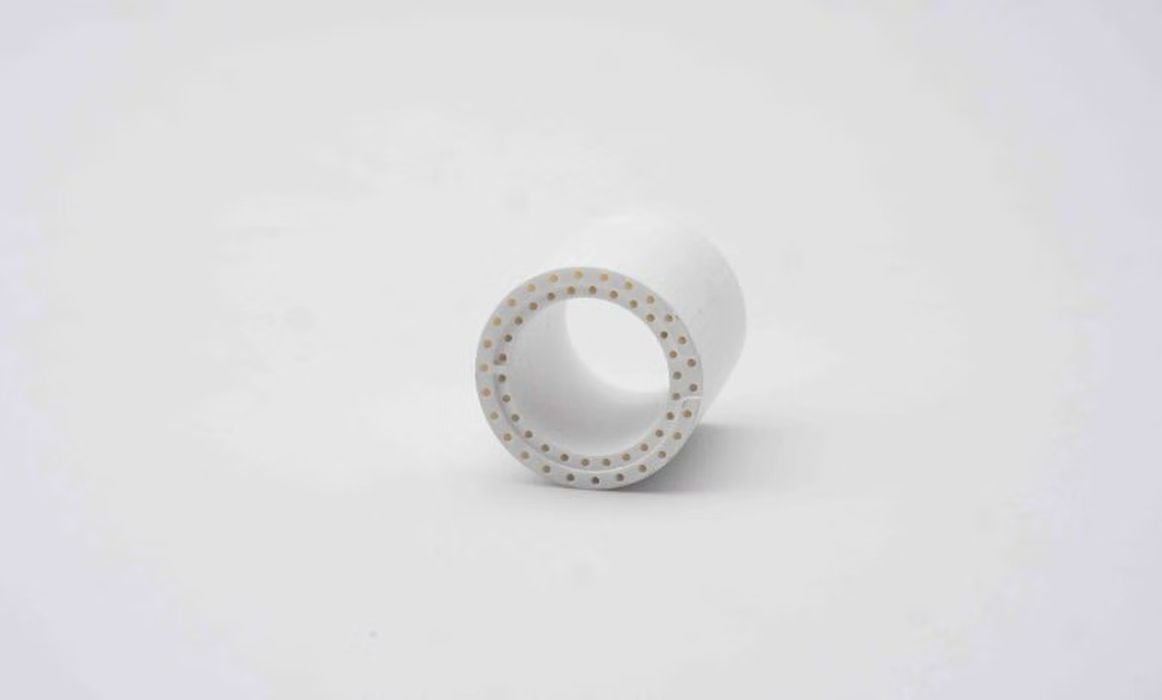
CERAM PRO: Prodways deepens commitment to ceramic AM.
At its facility in Montigny-le-Bretonneux, France, Prodways Machines has developed its most advanced ceramic additive manufacturing system to date, the CERAM PRO. The platform, first unveiled in May 2024, is based on the company’s patented MOVINGLight DLP technology and was engineered to meet the requirements of industries like aerospace, automotive, and investment casting.
As we’ll see in more detail throughout this feature, the CERAM PRO is the result of years of experience in ceramic additive manufacturing and is a key step in Prodways Machines’ strategy to focus increasingly on the ceramic market. As Prodways Machines Marketing Manager Sébastien Jacoberger, told us: “While we had in the past wax and SLS 3D printers, we have decided to deepen our focus in specific markets like ceramic and dental and to focus on one technology: MOVINGLight.”
Honing in on MOVINGLight
Prodways’ MOVINGLight is a proprietary digital light processing (DLP) technology that is based on a top-down approach. This method allows for greater precision and accelerates printing times by positioning the projector above the vat of resin and eliminating the need to detach each layer from the print window—as is necessary in a bottom-up approach. The process is also characterized by its mobile projector (aka the moving light), which enables greater print speeds, consistent print accuracy, and high detail across the build, regardless of whether the print is at the center of the projection or the edge of it.
Prodways Machines has adapted different versions of its MOVINGLight technology: it has a series of MOVINGLight dental 3D printers, including the ProMaker LD10 and LD20, as well as a series optimized for processing ceramic resins. This series includes various versions of the CERAM PRO, like the CERAM PRO 365, CERAM PRO 385, CERAM PRO 385+, and CERAM PRO 405+.
The CERAM PRO series does bear a number of similarities to the ProMaker MOVINGLight platforms, however it also has some key differences. The ceramic-specific machines have a higher-end projector than the dental systems, with specific wavelengths and optical quality optimized for processing technical ceramic resins like silica and alumina. For example, the CERAM PRO 365 has a wavelength of 365nm, while the CERAM PRO 405 has a wavelength of 405. In terms of resolution, the CERAM PRO 365 is equipped with a single high-power DLP unit and is capable of achieving a very high native resolution of 31 μm per pixel. On the larger CERAM PRO 385 and 405 systems, it is possible to have dual projector capability and achieve tolerances of 42 μm.
Prodways’ latest platform is also notable for its build capacity: the CERAM PRO 365 measures up to 264 x 328 x 350 mm, while the 405 has a maximum build capacity of up to 300 x 445 x 350 mm. As Jacoberger says: “We have one of the biggest ceramic AM platforms and the Z-height is one of the highest existing on the market, which gives an advantage for printing a lot of parts in a single build. But we also have a modular platform, so the build envelope can be more compact for smaller production runs.”
An open-parameter solution
An important thing to know about Prodways’ ceramic AM systems is that they have open parameters, enabling customers to work with their own materials or their ceramic resins of choice. This is the case with Prodways Machine customer Renaissance Services, which has been using the company’s ceramic resin 3D printing technology for over six years now.
Back in 2017, the Fairborn, Ohio company—an enterprise systems integration company primarily working with aerospace and defense companies—adopted Prodways’ ProMaker L5000 system to produce ceramic parts for the investment casting industry. This included the production of ceramic cores, molds, and filters that would be used by foundries in the production of aircraft, engines, and support equipment for aerospace and defense clients.
At the time, a particularly valuable application for ceramic AM was making castings for legacy military systems, which would facilitate the production of otherwise obsolete parts like gearboxes and housings dating as far back as the 1950s.
“For many of these castings there is scant technical data and the tooling no longer exists,” Renaissance Services co-founder Robert Morris said at the time. “New tooling typically costs six figures and takes months to produce. We pursue a concept of ‘CAD as tooling’ to produce a ceramic mold using our own patent-pending process. We then work with the foundry to produce a casting just like the original, filling a critical cost and lead time gap. We recently used our capability, working with a production foundry, to go from CAD model to a finished legacy engine gearbox casting in 26 days. This is a marked contrast from the two-year lead times that we have heard about from the military sustainment community.”
The open nature of Prodways’ ceramic AM platforms—even prior to the CERAM PRO—has enabled Renaissance to work with its own technical ceramic-filled photopolymer resins that meet the requirements of the company’s casting-specific applications.
Qualified SINTX resins
In addition to being able to use their own materials, Prodways clients can also rely on technical ceramic resins that have been qualified for the company’s hardware. These qualified materials are developed and supplied by advanced ceramics company SINTX, which has been working with 3D printing since 1998 and has been a key player in advancing ceramic AM, and its subsidiary Technology Assessment and Transfer, Inc., which has been a long-time partner of Prodways. The company, which has been using Prodways ceramic 3D printing technology since 2018, recently entered into a formal technical partnership to supply ceramic slurries for Prodways’ latest hardware solutions.
So far, SINTX’s silica and alumina slurries have been qualified for use on the CERAM PRO 365. “Prodways has had a very early exposure to ceramics 3D printing,” explained Vincent Icart, CTO and COO of Prodways. “Before this partnership, we were only supplying customers with internal capabilities development. We are thrilled to bolster our specifically developed MovingLight machineries with SINTX slurries, as our joint expertise will allow us to be an end-to-end solution provider for the most demanding ceramic printing applications.”
The silica-based slurry, available under the product name SILICA SiCast 1200, was engineered for investment casting applications and in particular the investment casting of super alloys. The ceramic slurry is characterized by its high hardness, and corrosion and temperature resistance.
It also demonstrates good green strength and minimal densification after sintering. Specific applications for the technical ceramic include casting cores, ceramic shell casting, aerospace brakes, engine components, investment casting patterns, electrical insulation coatings, and more. SILICA SiCast 1200 is qualified for use on the CERAM PRO 365.
Read the rest of this story at VoxelMatters