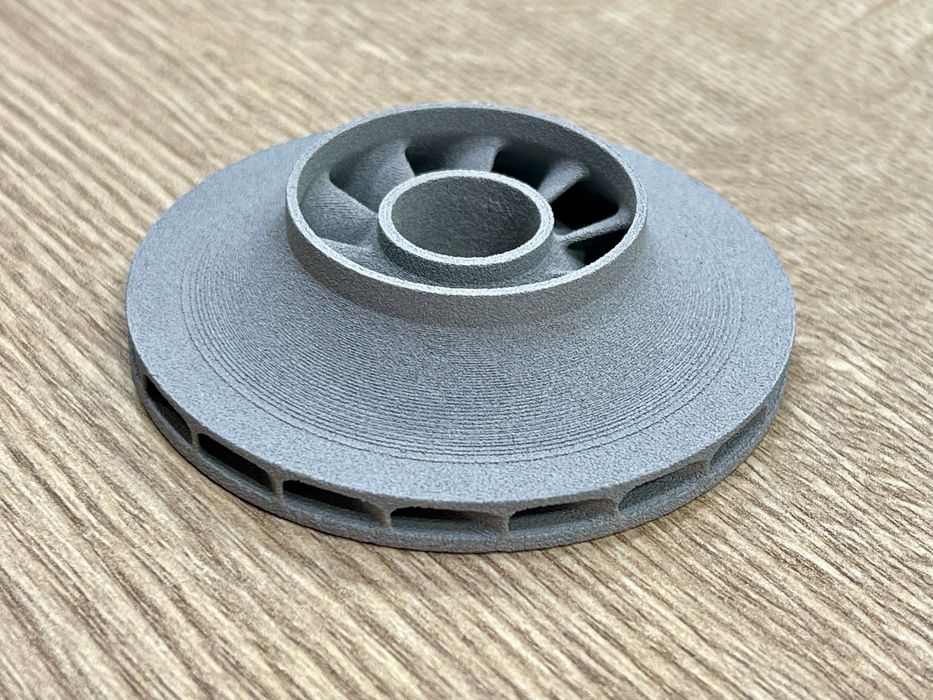
Could metal be the next material frontier for desktop 3D printing?
Desktop 3D printers are exclusively printing polymer materials these days. Both resin and FFF devices handle an increasing variety of thermoset and thermoplastic materials.
Because of the lowered cost of desktop 3D printers, a vast number of people, likely millions, now operate their own 3D printers. They’re producing all manner of parts, toys and widgets with them — almost always in polymer materials.
More advanced operators delve into 3D CAD tools and create their own designs, often posting them for comments on a variety of online forums. There is an endless stream of polymer gadgets being posted, many of them quite intriguing.
However, in recent weeks I’ve seen something quite unusual: some of these parts are made of metal!
Metal is an extremely difficult type of material to 3D print due to the high temperatures involved. Many of today’s metal 3D printers tend to be large commercial units costing six figures, and requiring the use of expensive metal powder. These devices also require special environments to handle the toxic and sometimes explosive metal powders. This is simply not feasible for small workshops and home setups.
A slightly less expensive approach is to use robotic motion systems with a welding wire approach. Sometimes called DED or WAM, these approaches still require expensive robotic systems and fancy software that’s well beyond the capabilities and budget of casual operators.
There is one way for desktop operators to achieve metal 3D printing, however. It is the use of “metal filaments”. These are not filaments literally made of metal, but instead a standard polymer mixed with metal powder. One of the most popular metal filaments is BASF’s Ultrafuse.
The printing occurs as normal on a FFF 3D printer, although the nozzle had better be hardened to withstand the abrasive metal particles passing through. This print will be a “green” part consisting of both polymer and metal.
The green part must then be passed through a second (or even third) process to remove the polymer and sinter the remaining metal particles together. This will require a fancy sintering furnace to perform the heating required. The loss of the polymer also causes the metal part to shrink notably, sometimes up to 20% in each dimension.
The problem is that most small operators don’t have access to the required sintering furnace, so the green part might have to be sent out for processing at another facility.
The final — and recommended — option for accessing metal 3D print capability is to simply use a service. These 3D print services will operate the large and expensive equipment and you’ll pay only for your print and associated processing. The final print is then delivered to you some days later.
Using a service has the advantage of getting good quality results, which often are not the case when using the FFF metal filament process. Services also typically offer a selection of different metals, usually well beyond what one could source with metal filaments.
If you’ve been designing your own parts and now have some that deserve 3D printing in metal, your best approach is to select one of many competent metal 3D print services and have them do the job.