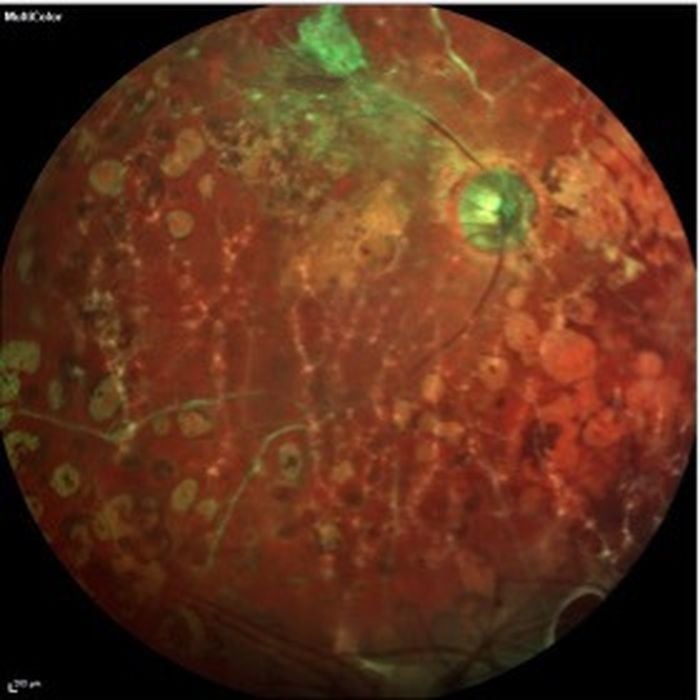
Charles R. Goulding and Preeti Sulibhavi provide insight into EssilorLuxottica’s transformative journey, highlighting their groundbreaking partnerships with Meta and advancements in 3D printing that are reshaping the eyewear and wearable tech industries.
EssilorLuxottica, a global leader in eyewear retail and manufacturing, has embarked on a remarkable journey in recent years, marked by strategic acquisitions and transformative partnerships. The company has set its sights not only on advancing the field of eyewear but also on pushing the boundaries of vision-related technology. With a market valuation exceeding US$100 billion, EssilorLuxottica is leveraging partnerships, especially with companies like Meta, and expanding into innovative technologies like 3D printing to redefine its place in the healthcare and consumer technology industries.
Meta Collaboration and AI-Powered Smart Glasses
EssilorLuxottica’s recent partnership with Meta, embodied in their collaborative Ray-Ban Meta glasses, is one of the most intriguing examples of this strategic expansion. These glasses represent more than just a sleek, high-tech accessory. They are equipped to allow users to download photos and videos from platforms like Facebook and Instagram directly to their devices. Recently launched in the U.S., these glasses also come with Meta’s AI assistant, allowing users to receive contextually relevant information by simply “seeing” something through their lenses. This new functionality allows users to, for example, identify landmarks, get real-time recommendations, or pull up information on products and locations they encounter.
With 3D printing gaining traction in both the eyeglass and wearables market, it’s reasonable to assume that additive manufacturing may play a significant role in making these smart glasses not only lighter but also more customizable for individual users. For example, 3D printing technology enables intricate and customizable designs that allow for lighter, more ergonomic frames. Meta and EssilorLuxottica could eventually leverage 3D printing to streamline production costs and improve the user experience, creating eyewear that is highly tailored to the user’s lifestyle and aesthetic preferences.
3D Printing and Customization in Eyewear Production
3D printing, or additive manufacturing, has already proven transformative in the eyewear industry, particularly for customization and rapid prototyping. EssilorLuxottica’s expansive operations are beginning to harness these technologies to provide personalized eyewear solutions, and their collaboration with innovative 3D printing firms signals a commitment to leading this trend.
Recent examples of this include EssilorLuxottica’s use of 3D printing to produce lighter, durable, and more comfortable frames that accommodate diverse styles and fits. Traditional manufacturing methods often face challenges in producing eyewear in a variety of shapes, sizes, and specifications. However, 3D printing allows for the production of frames that are perfectly tailored to individual facial features and ergonomic needs. With this technology, EssilorLuxottica could offer custom-made eyewear products, potentially reducing waste and enhancing customer satisfaction.
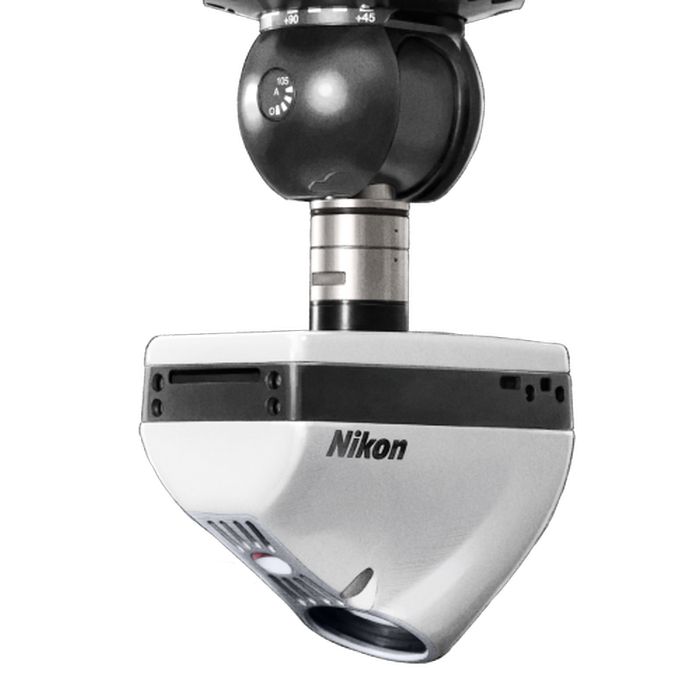
Strategic Acquisitions: Heidelberg Engineering and Nikon Investments
One of EssilorLuxottica’s most intriguing recent moves has been its acquisition of an 80% controlling interest in Heidelberg Engineering, a company known for its advanced diagnostic and surgical solutions in ophthalmology. Heidelberg Engineering is particularly recognized for its OCT (optical coherence tomography) imaging technology, which enables high-resolution imaging of the retina. This acquisition underscores EssilorLuxottica’s intention to deepen its reach in the field of ophthalmic diagnostics.
Moreover, the company has made a strategic investment in Nikon, a leader in precision optics and imaging technology. Nikon’s expertise in camera technology and precision optical instruments complements EssilorLuxottica’s portfolio, potentially enabling them to produce vision solutions that incorporate unprecedented levels of clarity and accuracy. These acquisitions and investments could open the door to innovative diagnostic tools and devices that integrate seamlessly into eyewear, potentially even allowing for real-time vision monitoring.
3D printing has begun to play an essential role in medical imaging and diagnostics, an area that Nikon and Heidelberg Engineering are actively involved in. Nikon, for example, utilizes 3D printing technology to create high-precision components for its imaging equipment, which are used in fields ranging from ophthalmology to medical diagnostics. Heidelberg Engineering could use 3D printed components for bespoke medical instruments, such as imaging devices or surgical tools, designed to support specific clinical applications.
Nuance Hearing Acquisition: Enhancing Hearing Solutions with 3D Printing
In 2022, EssilorLuxottica acquired Nuance Hearing, an Israeli startup focused on integrating hearing aid technology into eyewear. The main product, developed by Nuance Hearing, enables users to wear glasses that double as discreet, high-functioning hearing aids, bringing together auditory assistance with visual technology. This integration makes wearable solutions for those with hearing impairments more accessible and convenient, providing them with a seamless way to navigate auditory challenges without the stigma often associated with traditional hearing aids.
We have covered EssilorLuxottica’s frames made with Nuance hearing aids previously on Fabbaloo. That particular example illustrated two benefits of 3D printing: customization and functionality.
3D printing can further enhance this development by creating customized ear molds and hearing aid shells, which fit comfortably and discreetly into glasses frames. Nuance Hearing and EssilorLuxottica could harness 3D printing for these components to ensure a better fit and improved acoustic performance. Recent studies suggest that 3D printed hearing aid devices often result in better sound quality and comfort compared to traditionally manufactured alternatives. By using this technology, EssilorLuxottica could lead the market in creating the next generation of integrated hearing and vision solutions.
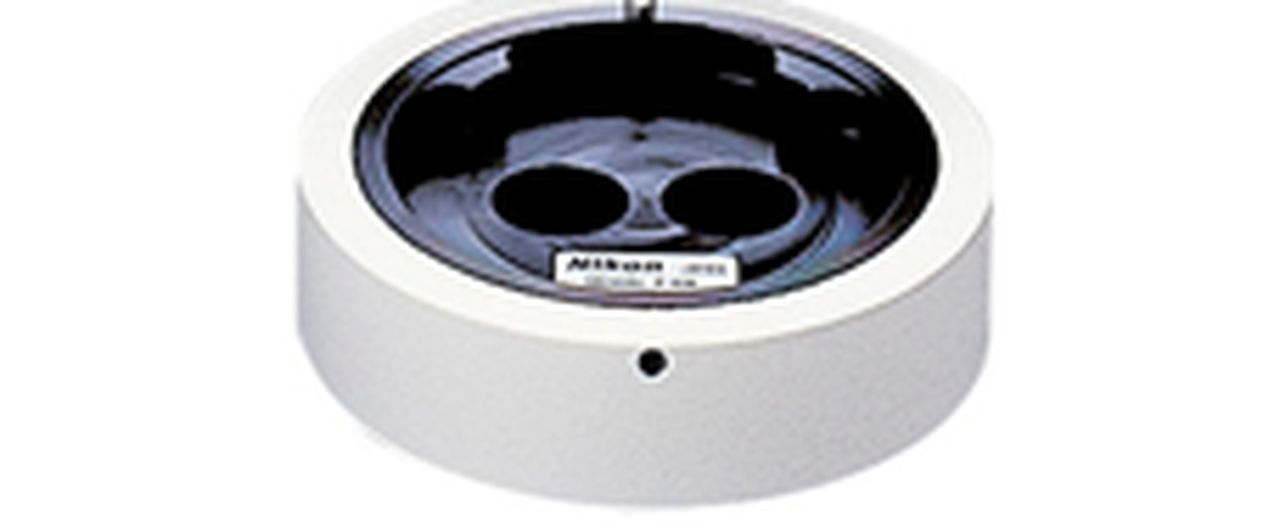
Competitive Edge: Meta, EssilorLuxottica, and the Future of 3D printed Wearable Tech
The partnership between Meta and EssilorLuxottica brings together two powerful companies with significant resources. EssilorLuxottica, with its expertise in vision products, and Meta, with its AI-driven technology, are in a prime position to drive innovation in wearable tech. As 3D printing continues to evolve, these companies can use additive manufacturing to produce unique, high-quality products that bridge the gap between fashion and function.
Meta has been exploring 3D printing applications for various devices, including smart glasses. 3D printing allows them to quickly prototype and refine complex designs, enabling faster development cycles and improving the technology embedded within these devices. At the end of 2022, Meta purchased Luxexcell, a 3D printing lens company. Luxexcel specializes in manufacturing 3D printed lenses. EssilorLuxottica’s relationship with Meta also opens up the potential for using 3D printing to integrate additional sensory features into smart glasses, in addition to prescription AR/VR glasses. This could lead to eyewear capable of real-time translation, environmental scanning, or augmented reality applications.
The Research & Development Tax Credit
The now permanent Research and Development (R&D) Tax Credit is available for companies developing new or improved products, processes and/or software.
3D printing can help boost a company’s R&D Tax Credits. Wages for technical employees creating, testing and revising 3D printed prototypes are typically eligible expenses toward the R&D Tax Credit. Similarly, when used as a method of improving a process, time spent integrating 3D printing hardware and software can also be an eligible R&D expense. Lastly, when used for modeling and preproduction, the costs of filaments consumed during the development process may also be recovered.
Whether it is used for creating and testing prototypes or for final production, 3D printing is a great indicator that R&D Credit-eligible activities are taking place. Companies implementing this technology at any point should consider taking advantage of R&D Tax Credits.
Conclusion
EssilorLuxottica’s recent moves—acquisitions of companies specializing in high-precision diagnostics, imaging, and wearable technology—highlight the company’s commitment to innovation in the health and consumer technology sectors. With the added layer of 3D printing capabilities, these developments hint at even more ambitious possibilities on the horizon.
For instance, with the expertise from Heidelberg Engineering, EssilorLuxottica could create 3D printed diagnostic equipment tailored to eye care specialists’ needs. Such equipment could revolutionize accessibility, providing more optometrists with access to high-precision diagnostic tools that are more affordable and easily customizable.
Furthermore, by partnering with companies like Meta, EssilorLuxottica can employ 3D printing to produce futuristic, AI-powered eyewear that blends advanced optics with wearable technology. The potential for manufacturing at scale is significant; 3D printing could reduce costs and turnaround times while providing endless possibilities for style and design adjustments, allowing EssilorLuxottica to reach a wider audience with tailored products.