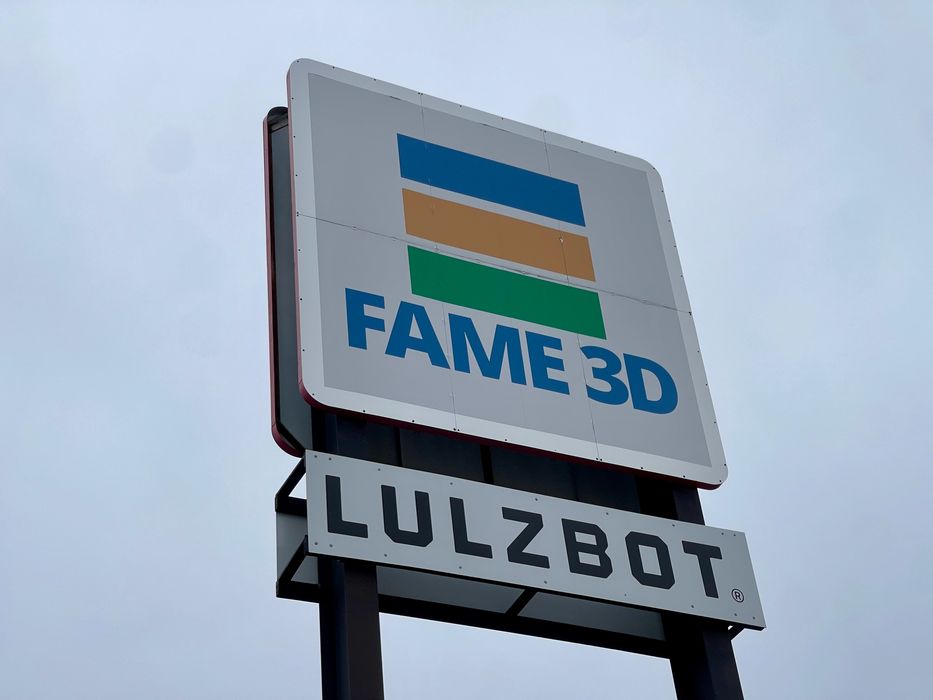
Fabbaloo went on a road trip and paid a visit to FAME 3D, the manufacturers of LulzBot 3D printers.
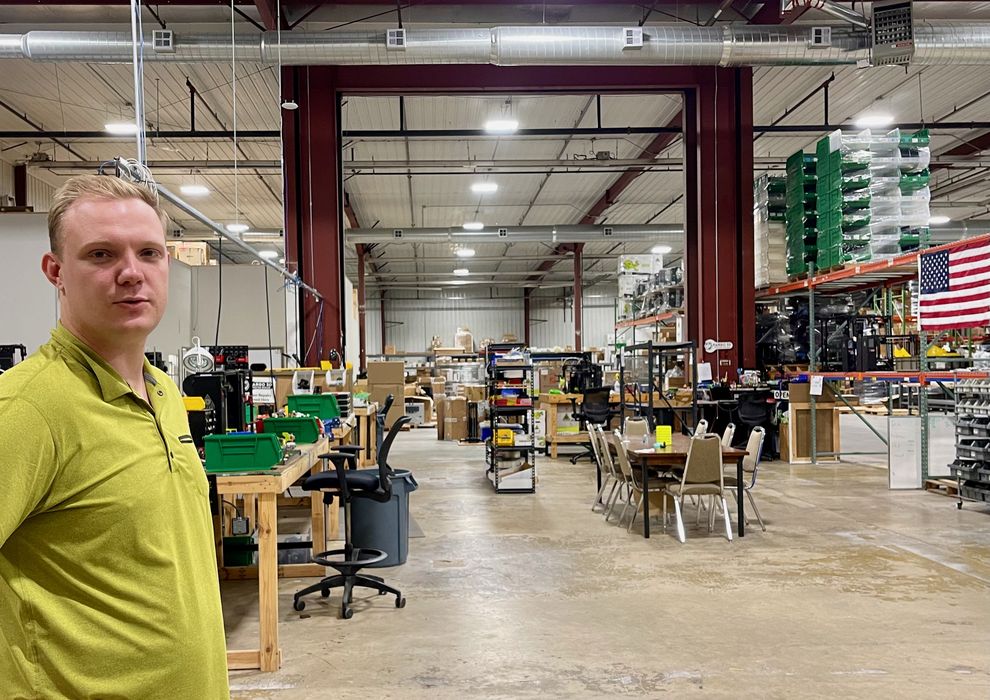
Our tour of FAME 3D was led by John Olhoft, the CEO of the company. Olhoft and team acquired the assets of Colorado-based Aleph Objects in 2020, the originators of the LulzBot brand. Since then the company has been operating quite successfully in Fargo, ND.
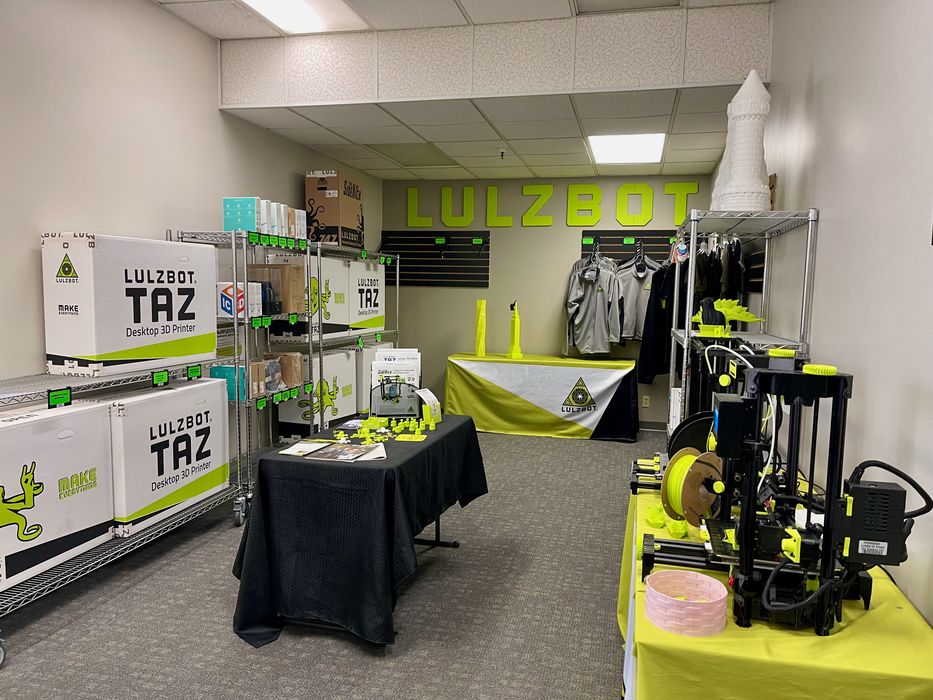
Like some 3D printer manufacturers, FAME 3D operates a retail store at the front of their vast building. Locals can drop by and pick up a 3D printer fresh off the assembly line, or materials for their equipment. Of course, the majority of the company’s sales are via online and remote orders, but the store does provide a convenient stop for those nearby.
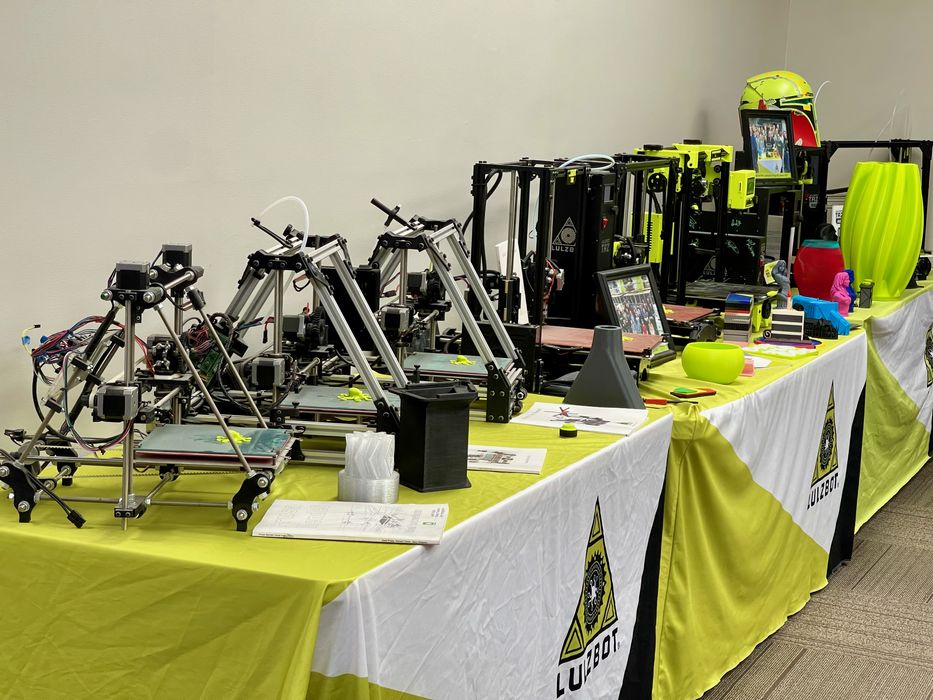
As we’d seen in our previous visit, FAME 3D maintains their “museum” of historic LulzBot devices. However, I got the impression they’re going to make some changes as they’ve been producing quite a few new models since the move in 2020.
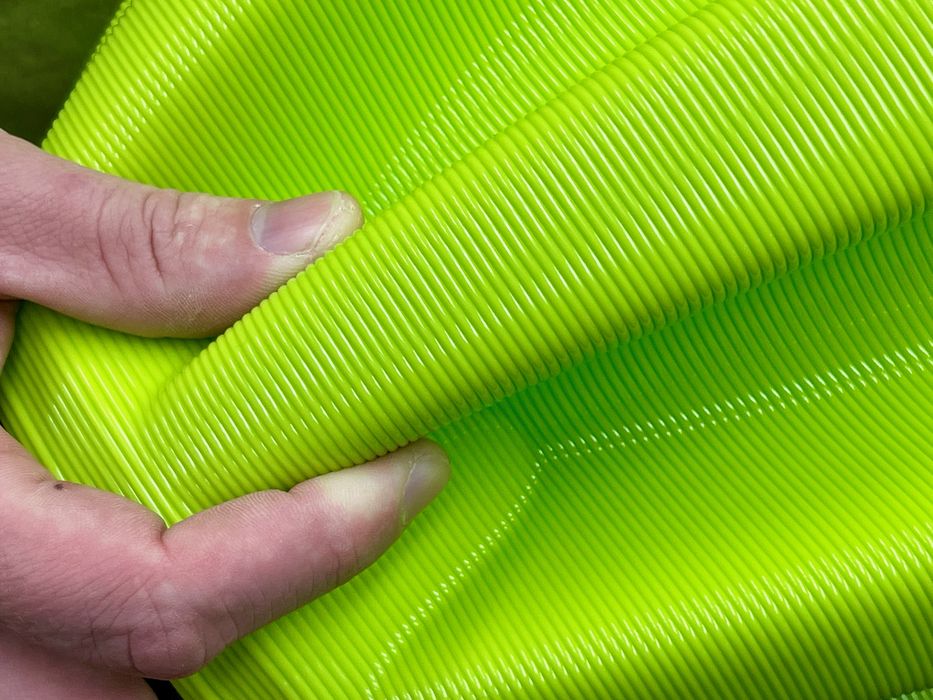
Every time I visit FAME 3D I am impressed with their ingenuity and innovations. They seem to be constantly experimenting with a range of tools, techniques and materials. Here we see a recent experiment with a super-fat nozzle on their Galaxy extruder. This system has an incredible 2.4mm diameter nozzle, and lays down layers 1.8mm thick. While the printing is quite slow due to volumetric extrusion capacities, the resulting object is extraordinarily strong.
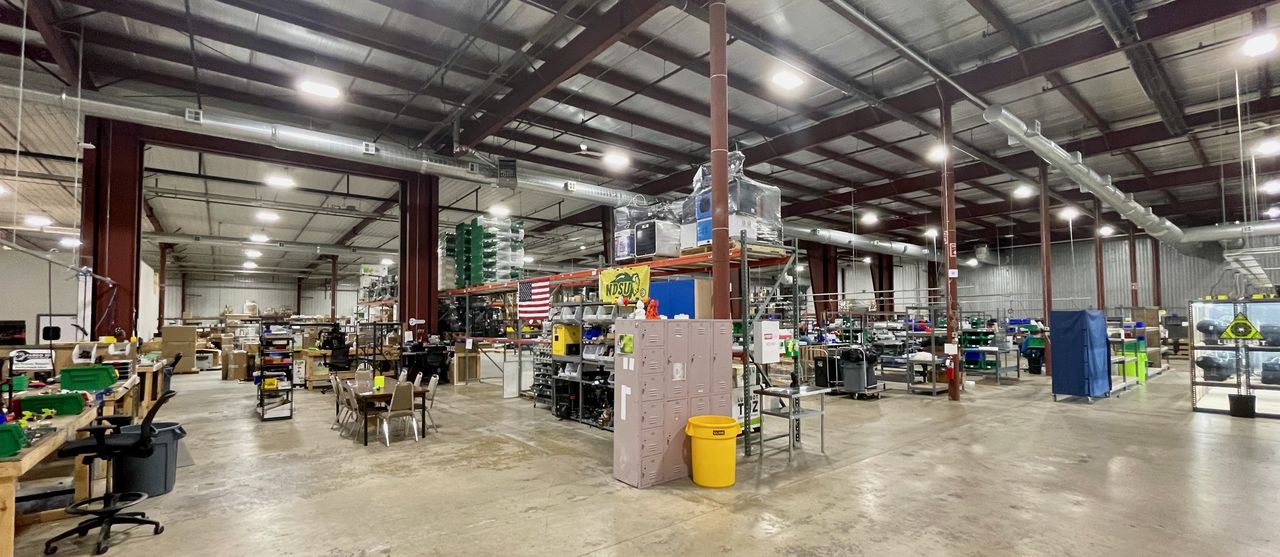
In 2020 the company took over an empty warehouse and converted it into a 3D printer factory using tools obtained from the Colorado move. It’s quite a large space, but different from our last visit. It seems that FAME 3D has done quite a bit of optimization to reduce the costs and steps required to produce their 3D printers, and has even been able to reduce the amount of labor required for the work.
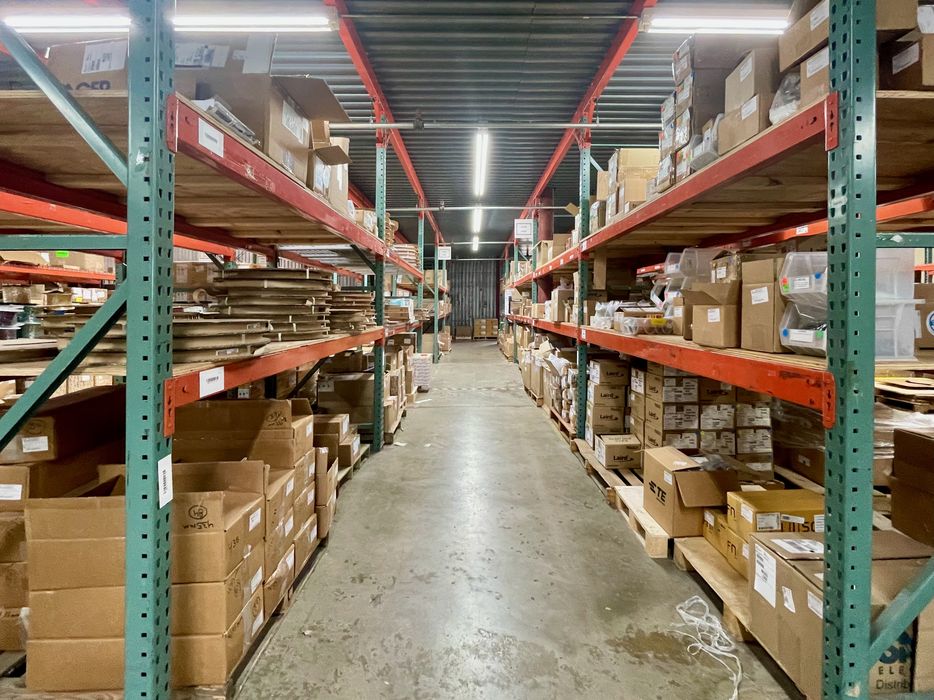
The south side of the building is a vast array of shelves containing every conceivable part and material that might be used in production. Managing part inventories is quite important in manufacturing, and it appears that FAME 3D is doing a good job.
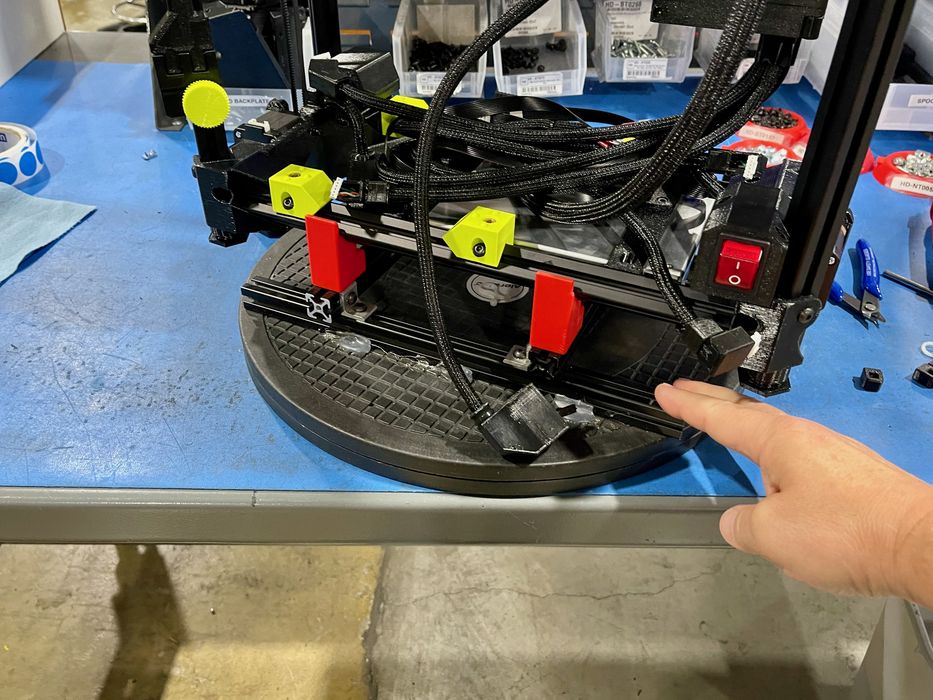
Throughout our tour we were confronted with many ingenious manufacturing aids, all developed to speed up the assembly and testing process. This one in particular was quite interesting. It’s a spinning mount on which a partially assembled unit is placed. The unit can be easily spun around by the assembler to access different areas, saving a bit more time during the work.
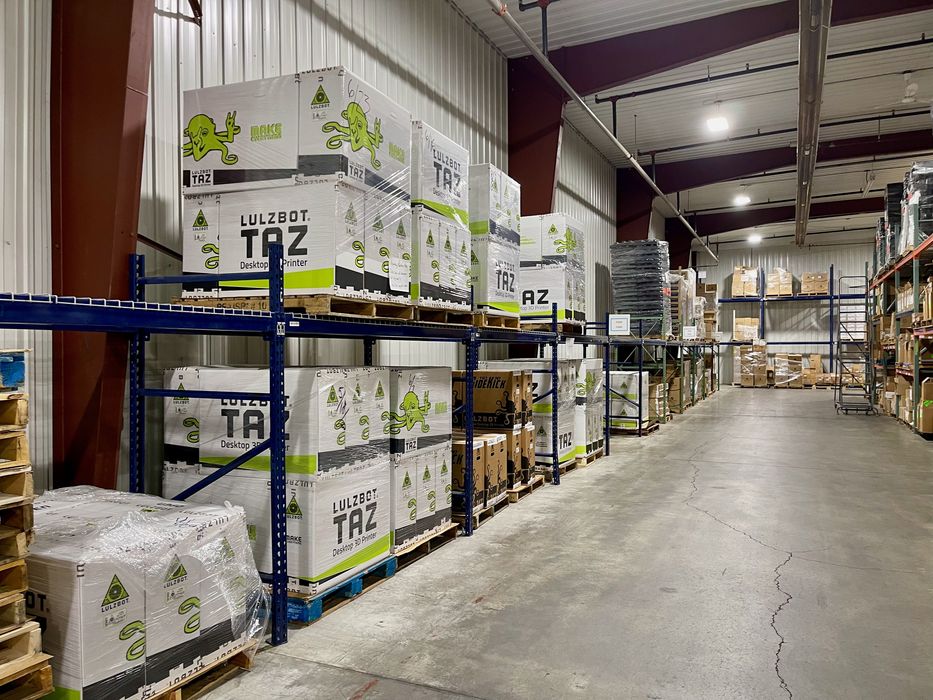
Once machines are made, they’re packaged up for shipment to parts unknown. There weren’t that many units waiting for shipment because the company has been focusing on just-in-time manufacturing.
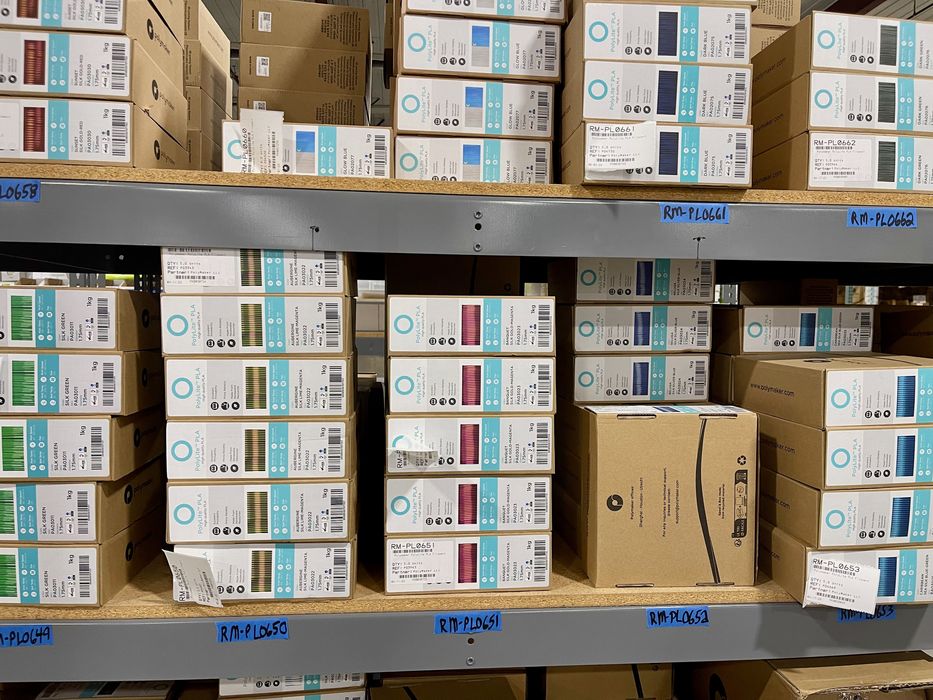
FAME 3D also happens to be a distributor for several major filament manufacturers. As such there were vast shelves filled with every conceivable material. Here you see a selection of Polymaker spools.
FAME 3D uses their own 3D printers to produce parts to make more 3D printers, a practice commonly done among manufacturers. However, FAME 3D has quite an interesting approach for some parts. Due to the design of the machine, some parts must be made in materials with greater strength and thermal resistance, like ABS. To increase the quality of prints made in ABS one would typically use an enclosure to raise the ambient temperature and reduce the thermal gradient that causes warping.

FAME 3D’s solution is quite ingenious: they have a “hot room”, where they place all the printers making ABS parts. This room, which we briefly entered, was very warm, 98F (37C). It’s also faster to print because you have far less wait time for the print surfaces to heat up. This approach greatly increases the precision of parts produced — and negates the need for enclosures entirely.
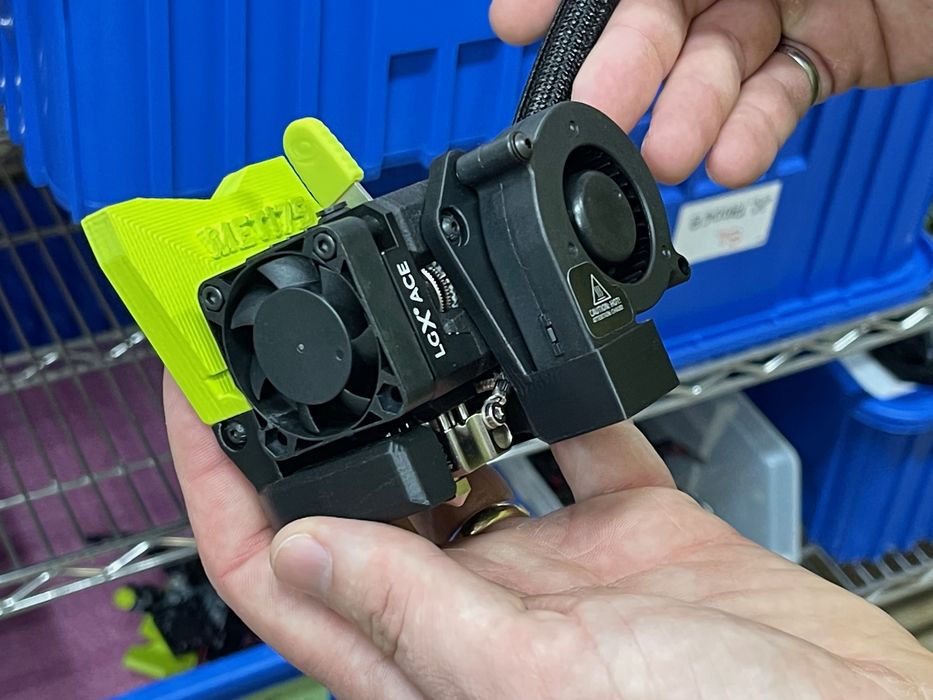
The company is constantly improving their toolheads, which are easily installed in the open source LulzBot machines. They’re really designed to be modified, so FAME 3D has a selection of constantly improving toolheads. For example, the Galaxy toolhead can be quickly swapped with only three bolts to remove. Above we see the company’s latest Meteor toolhead.
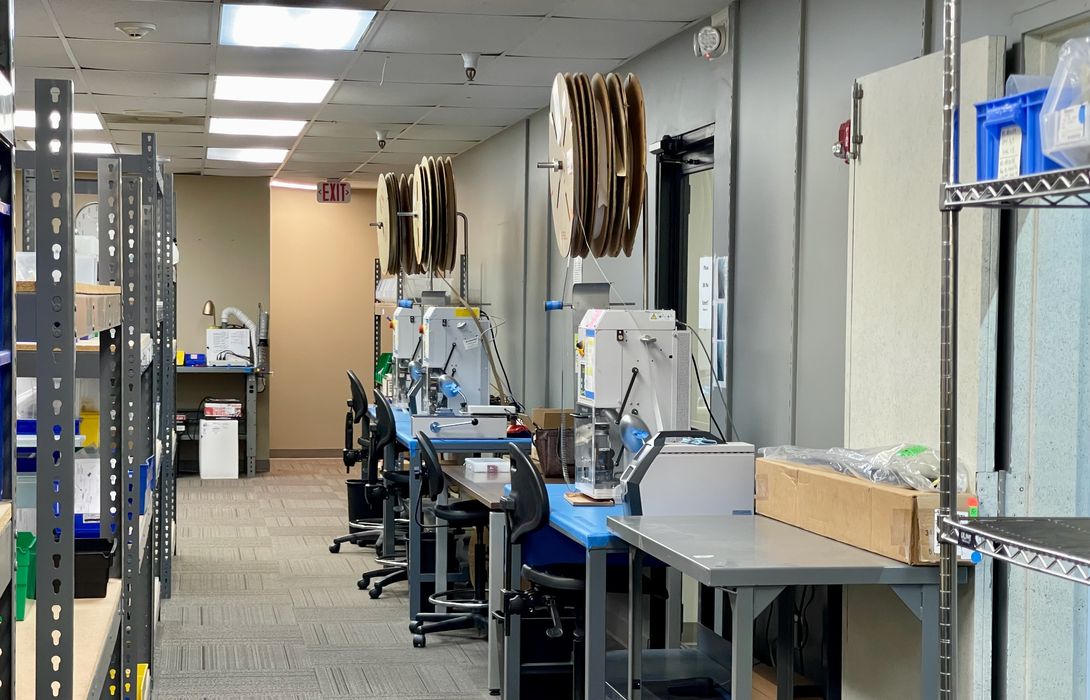
This area is used to create the wire harnesses used in building the 3D printers. Olhoft explained the wire harness production rate must match the rate of 3D printed parts being made for 3D printer production. Manufacturing is a game of ensuring everything is where it has to be at the proper time.
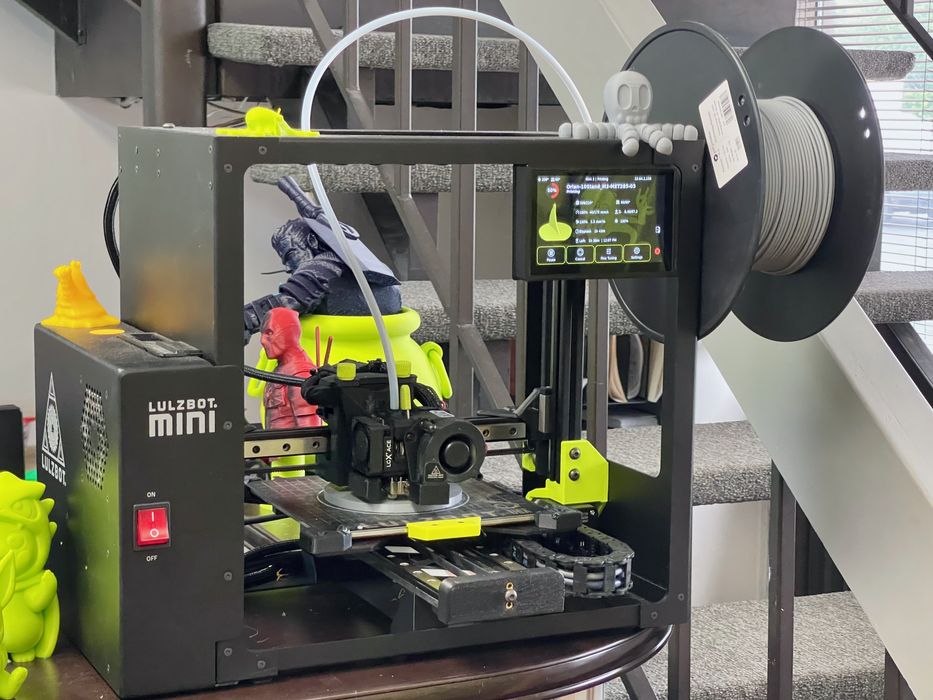
This is the company’s latest desktop FFF 3D printer, the Mini 3. It offers 3X faster print speeds, and has a rather large and easy-to-read touchscreen. The major change is that the machine uses a CoreXZ motion system, a method that’s becoming more popular among desktop devices. Even better, it’s fully assembled and ready to print.
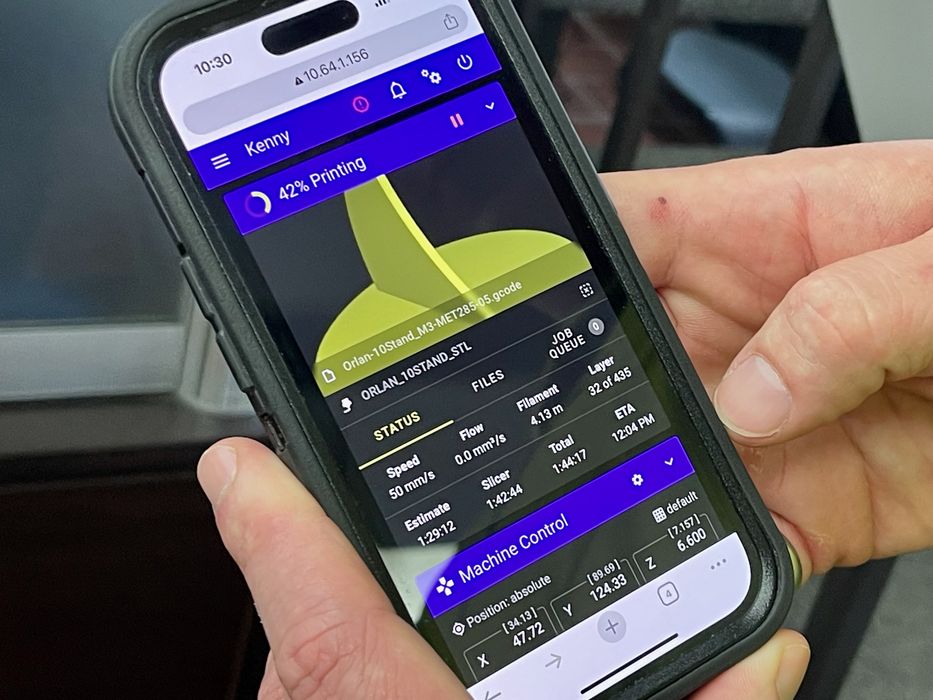
The Mini 3 also can be controlled remotely through the use of the new smartphone app.
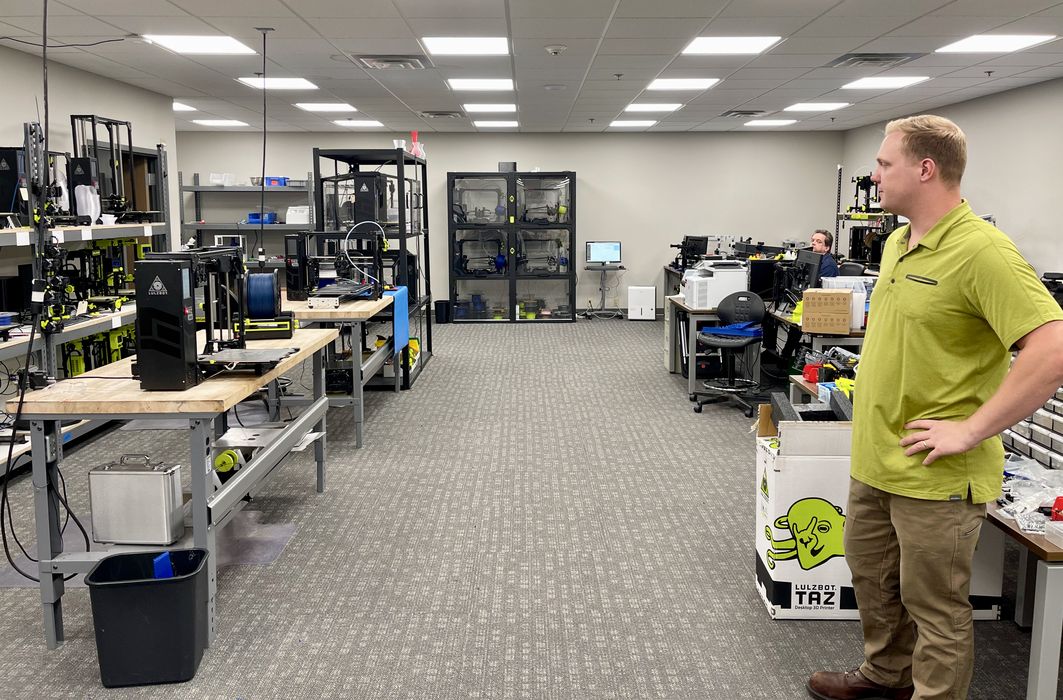
FAME 3D provided a pretty open-ended tour of their research and development lab, something few 3D printer manufacturers would offer to the media. There we saw a number of new items under development, and some experimental projects.
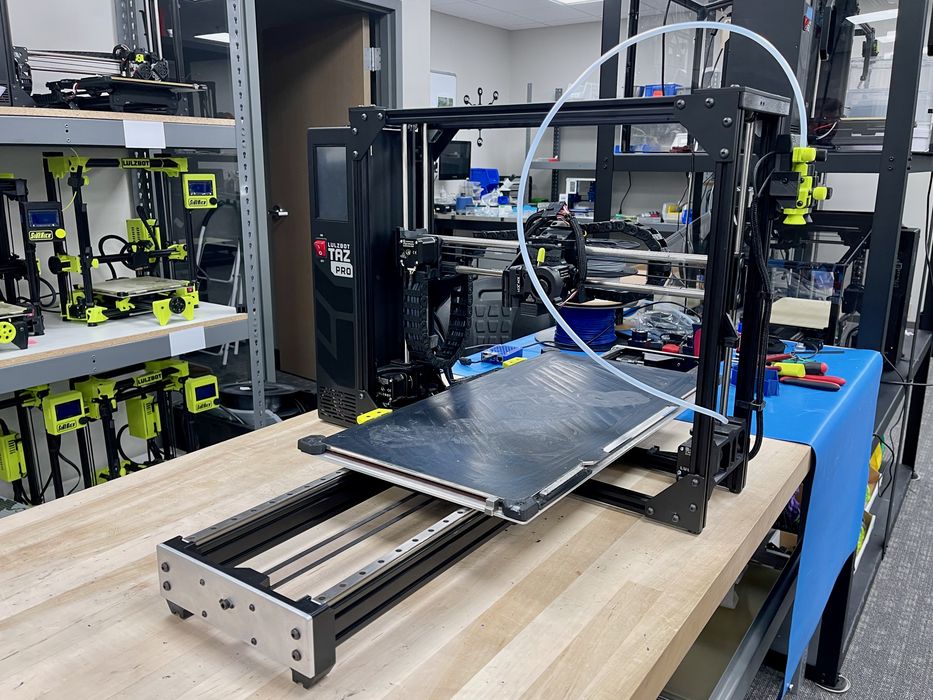
The company’s TAZ Pro Long Bed system is quite unique on the market: it’s a standard 3D printer but with an extremely long bed. This allows the production of very long parts, up to 582mm, and longer if you go diagonal.
The machine has been on the market for a couple of years, but as one would expect, FAME 3D has been making improvements to the design with their upcoming V2 Long Bed. The main changes are the use of linear rails, a much thicker belt (9mm), and dual stepper motors for the long bed.
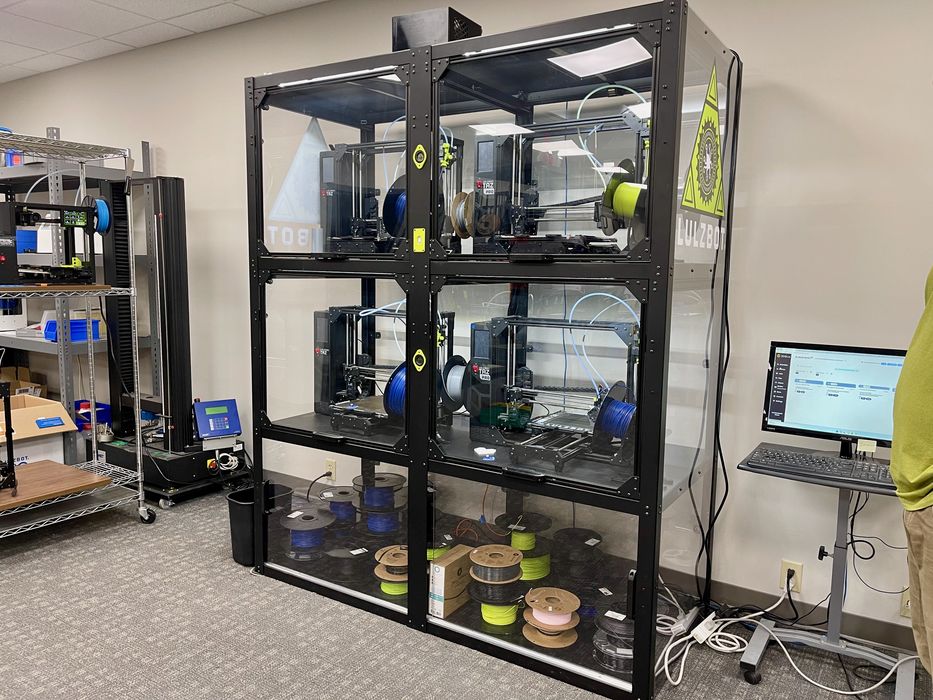
Here we see the print farm system, where an array of LulzBot devices can be managed from a single point. The system can handle up to 64 machines from a single controller, the “brain box”.
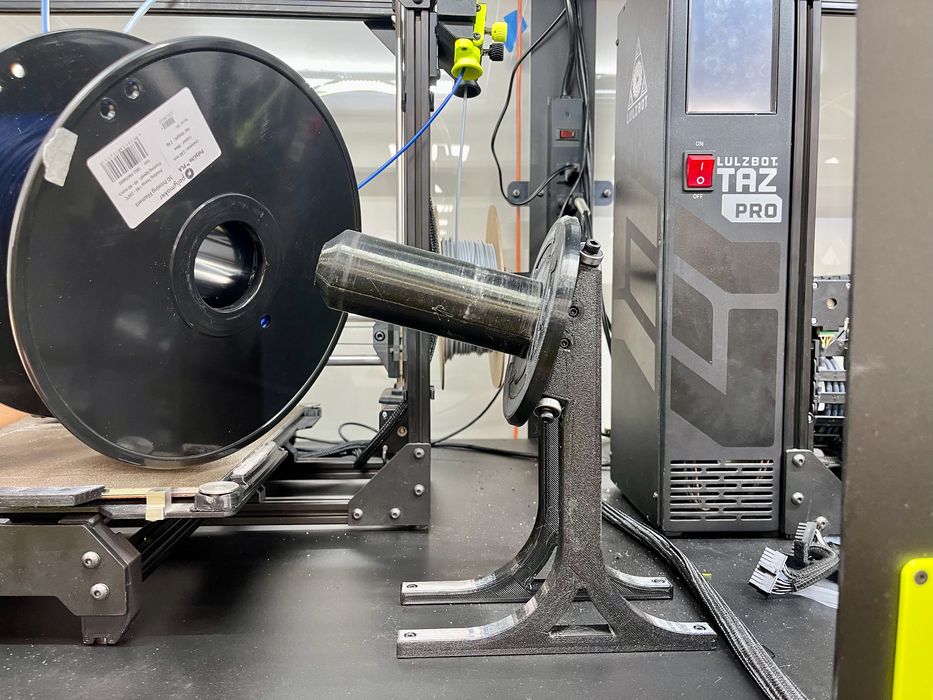
One interesting tidbit of the array design are these spool mounts. Apparently they were originally 3D printed, but FAME 3D had to switch to stainless steel because “cardboard spools eat plastic mounts.”
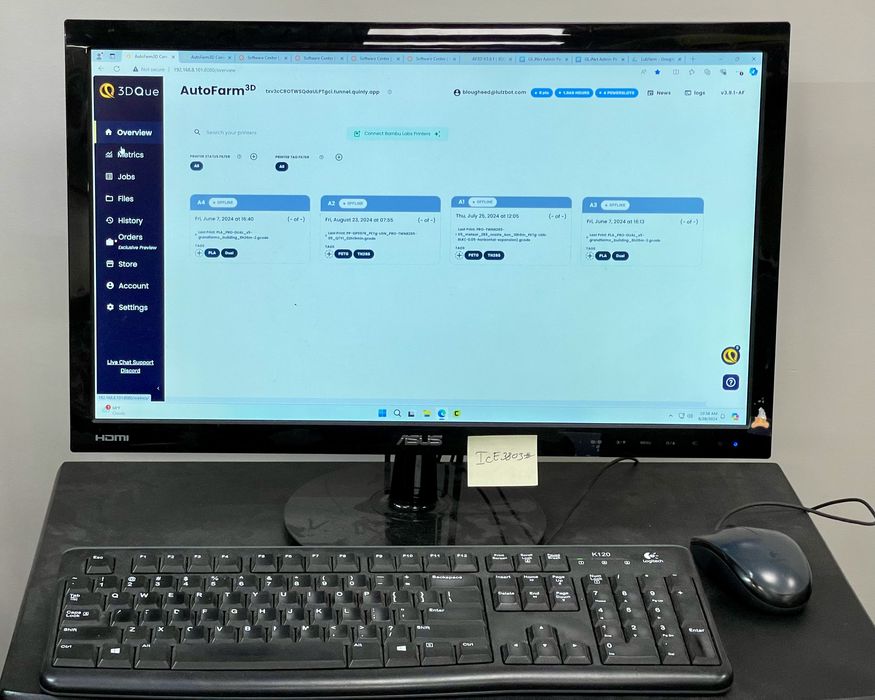
FAME 3D partnered with 3DQue to use that company’s powerful AutoFarm3D system to manage the devices.
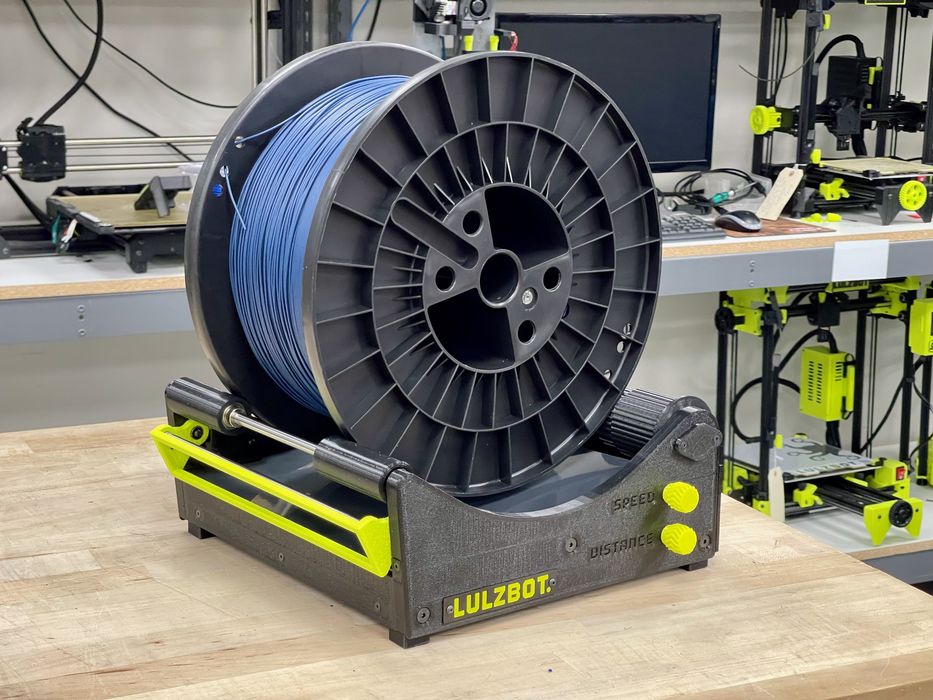
This is a very unusual experimental product, a spool feeder. It turns out that when you’re using very large spools they don’t turn nearly as easily as small 1kg spools, and this can cause problems when feeding a 3D printer. The idea here is to motorize the operation and turn the spool when more filament is required.
How does that happen? This is the ingenious part: that green lever at the bottom front is pulled upwards when the filament (which travels under it) tightens. This means we have a large-spool filament feeder that’s compatible with basically any FFF 3D printer.
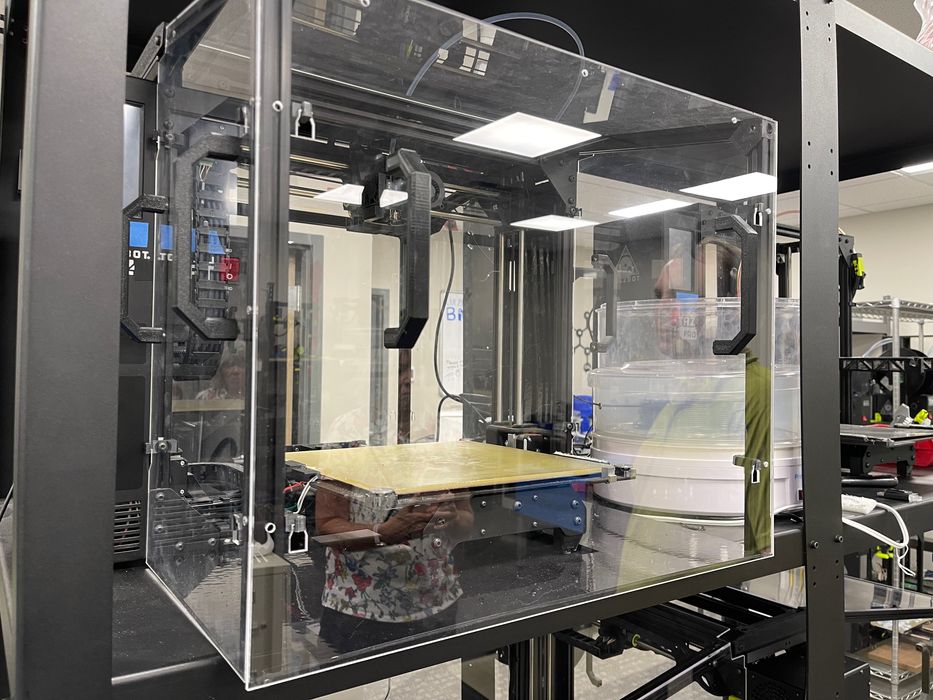
FAME 3D is also experimenting with enclosure designs for several of their 3D printers. Here we see one design being tested.

Here’s another approach for one of their smaller devices.
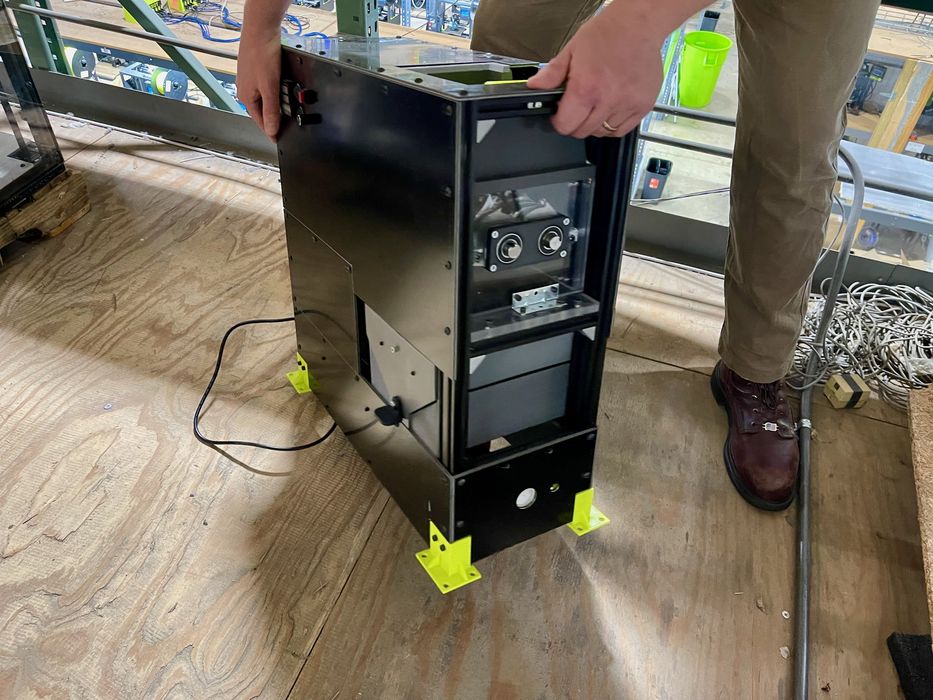
This experiment is a plastic shredder, which could be used to chop up used filament, support scraps and failed prints. The idea is to start developing ways to deal with the inevitable piles of plastic that accumulate when 3D printing.

Finally, we can see FAME 3D experimenting with metal 3D printing. They’re using available polymer/metal filaments in the FFF process to produce green parts, which are then sintered to produce fully metal final parts. This has been previously done on LulzBot equipment, but I wonder if this exploration may eventually lead to a more prominent metal 3D print capability for LulzBot equipment.
You might not hear as much about LulzBot and FAME 3D as some of the other FFF 3D printer manufacturers, but there is indeed quite a bit happening behind the scenes at the company.
Via LulzBot