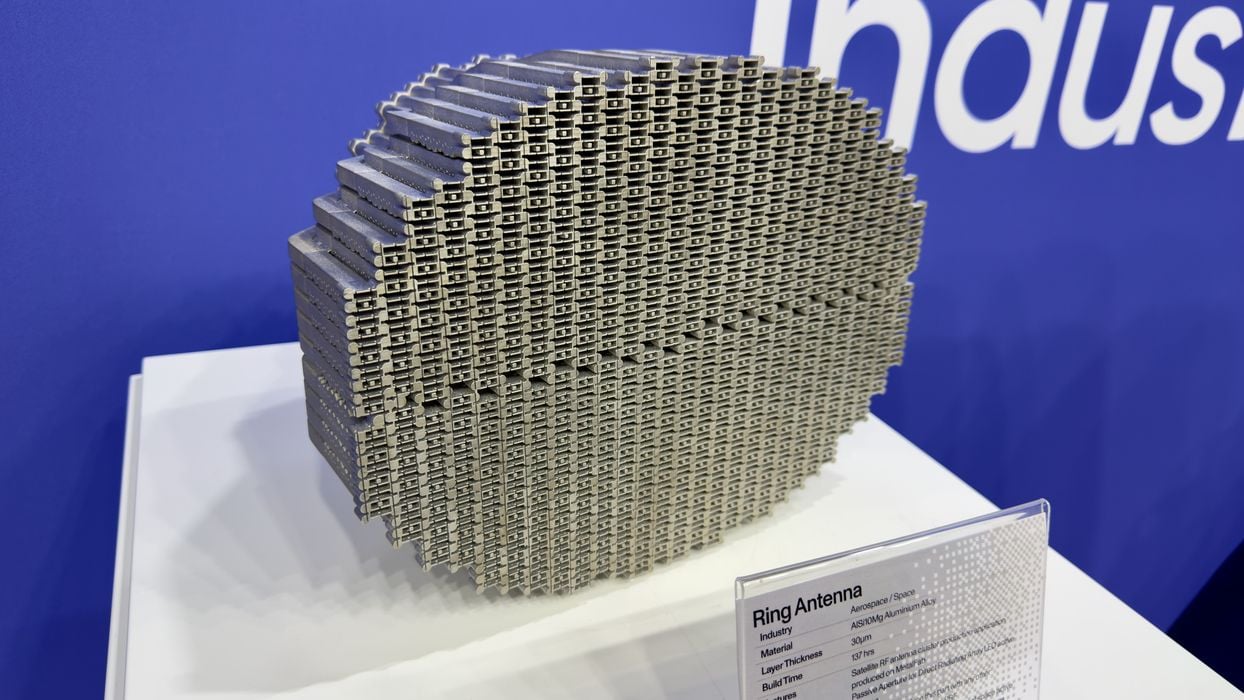
We had a look at some interesting metal 3D prints made by Additive Industries.
The most interesting by far was this RF antenna cluster designed for use in orbit on satellites. The purpose of the part is to handle a large number of simultaneous channels, which explains the huge number of components in the image.
But they aren’t components! This one, single-part, 3D printed in a single print job.
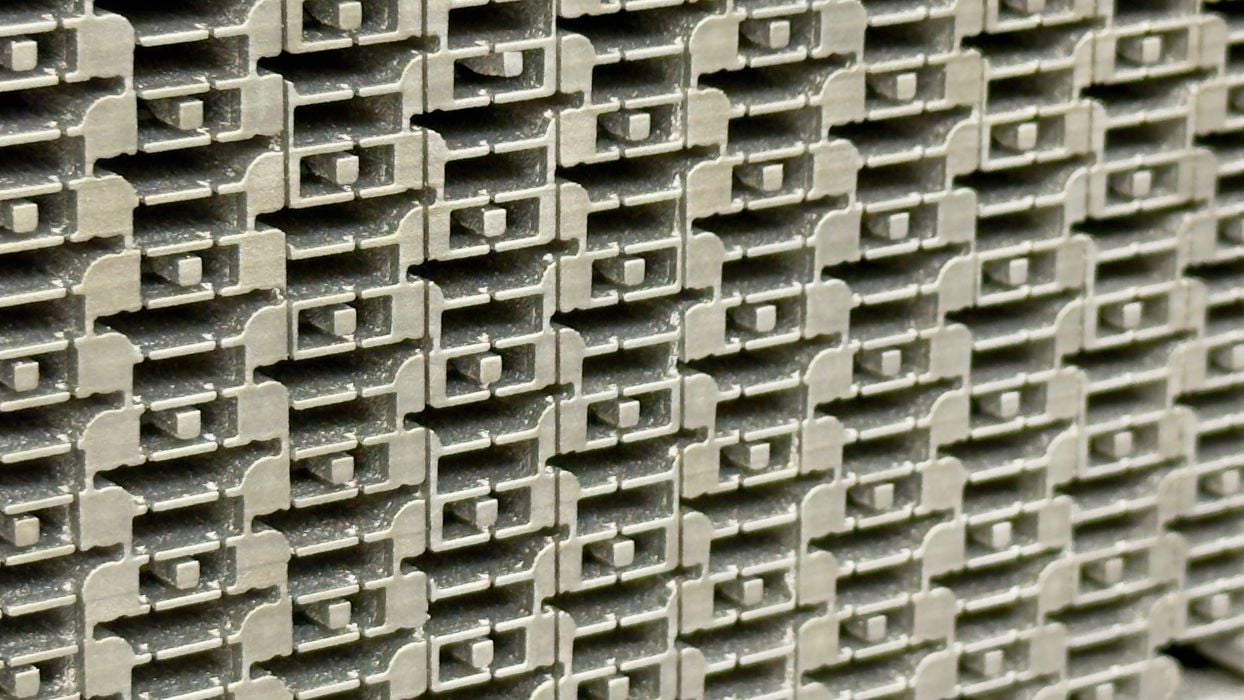
It was a long print job, to be sure. Additive Industries explained that the print, made from AISi10Mg Aluminium Alloy, took 137 hours (six days) to complete. It was printed on their flagship metal 3D printing system, the MetalFAB ONE.
What’s astounding about this part is the comparison to traditional manufacturing techniques. Normally, this antenna cluster is made by making each element individually and then attaching them together. The catch is that the antenna elements need to be perfectly aligned in order to properly communicate with the target. Due to the enormous distances involved, even a slight misalignment can throw off signals.
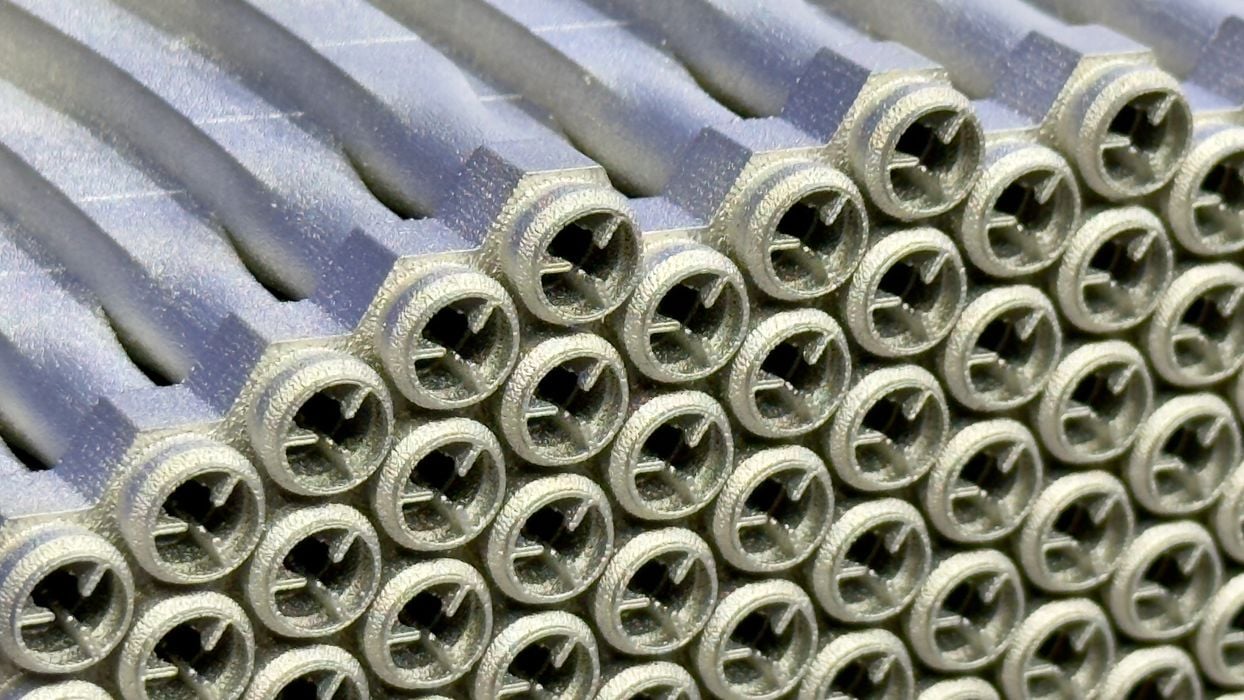
That required considerable effort when manually building this cluster.
However, when 3D printing the cluster, it’s all one part and is automatically perfectly aligned. This requires far, far less effort to produce. It’s literally just printed and requires minor post-processing.
Additive Industries explains:
“Impossible to produce this part with any other production technology than LPBF. Game changer for the next generation of space active antennas for LEO and MEO satellites constellations.”
I’m not sure it’s impossible, but it would be far more expensive and error-prone to make with other processes. Making this part using additive manufacturing is so utterly compelling that it would be difficult to see the manufacturer choosing any other method to produce it.
With this part, it seems that Additive Industries has secured a long-term client that will make this type of part using additive manufacturing going forward.
What other highly complex parts deserve additive manufacturing treatment?