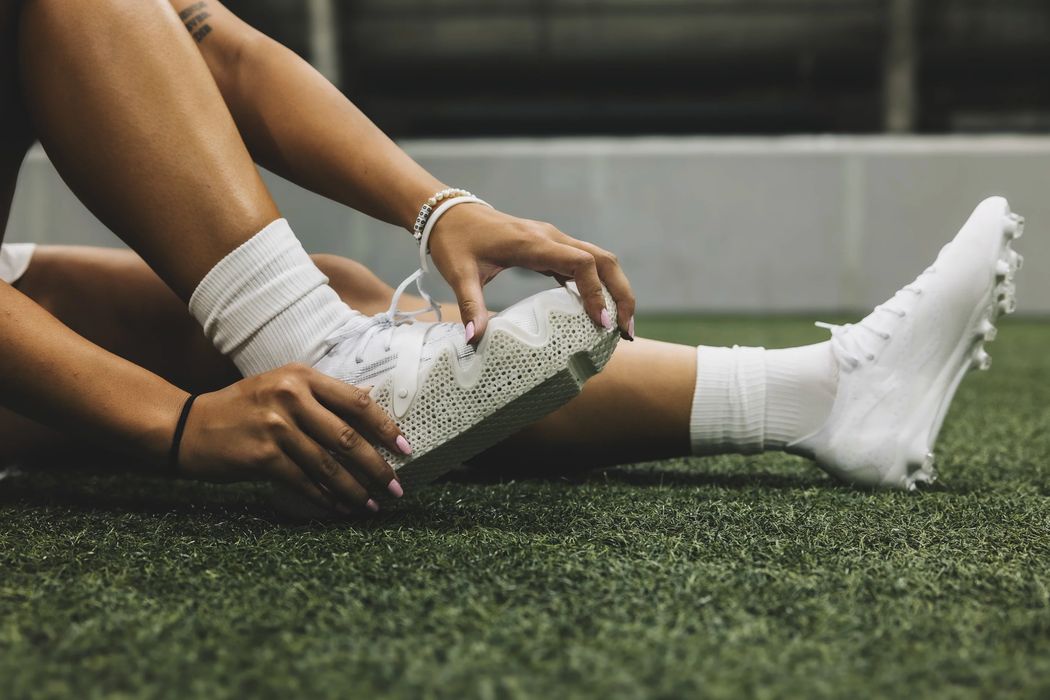
One of Carbon’s customers has come up with an interesting new 3D print application: cleat guards.
What is a cleat guard? It’s for athletic sports where the footwear includes cleats. These are rigid protrusions from the bottom of the sole designed to provide strong grip on outdoor grass surfaces. Unfortunately, they also grip manmade surfaces, too, damaging any surface the wearer walks upon.
Hypsole wants to fix that problem with custom-designed 3D printed cleat guards. The idea is to attach the cleat guard to the cleated shoe to cover up the cleats and prevent them from damaging floors.
There are analogous solutions for similar situations, such as ice skate guards. However, guards tend to be large, uncomfortable and heavy, leading to awkward steps.
Here it seems that Hypsole has a goal to make the guard “integrated” into the shoe so that the cleated shoe is transformed into something like a bulky sneaker. The idea is to make the wearer comfortable in both function and style while wearing the cleat guards.
The company was founded by former star athlete Jen Christian, which today markets a variety of cleat guards for a wide range of footwear products.
This is because the cleat guards must precisely fit each model of shoe, or it won’t work properly. Not only must the guard wrap the cleats, the guard must also form a rather tight envelope around the shoe to avoid appearing “large”.
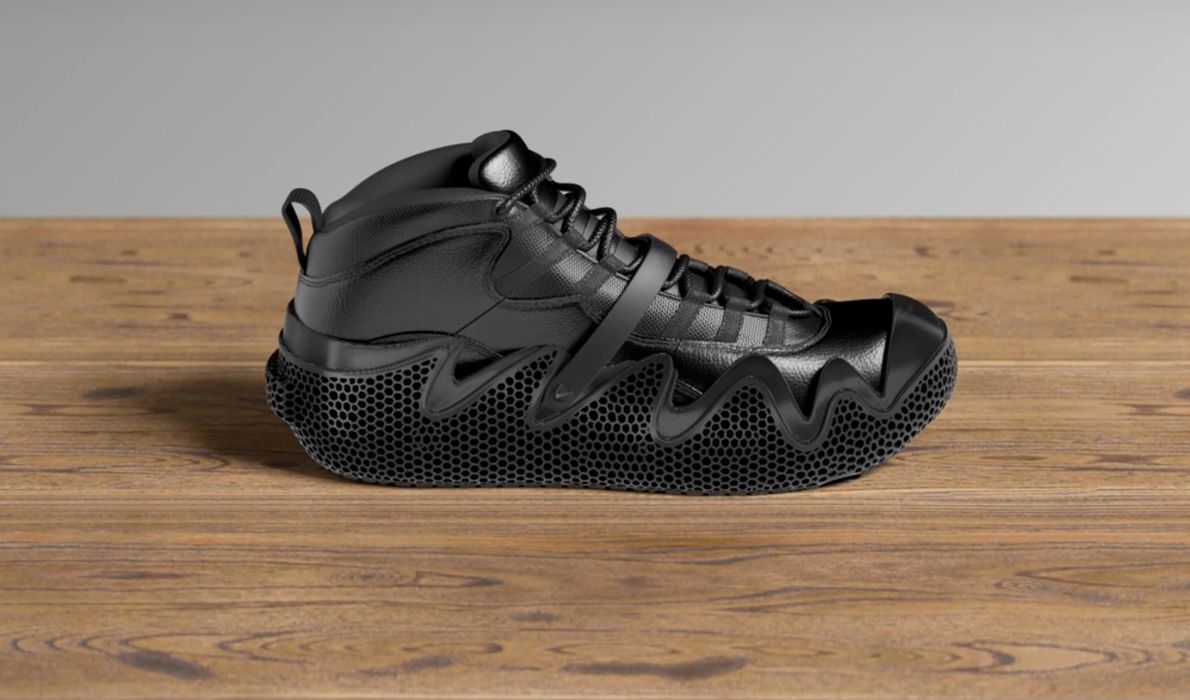
Above you can see an example of the Tidal 3D Elite cleat guard applied to a shoe. It doesn’t really look any different from a sneaker, does it? That’s because the 3D printed guard design directly integrates with the shoe style’s geometry.
Hypsole Founder and CEO Jes Christian said:
“Once the functional requirements of the product were established, the aesthetic – from fit to finish – became a top priority. I didn’t want this product to be just another piece of sports equipment – I wanted fashion and streetwear to be infused into the design visuals. I felt strongly that it needed to look good – and that we needed athletes to want it as much as, if not more than they needed it, because at the end of the day, if it works, but it’s not hitting aesthetically – then we’re going to be fighting an uphill battle with our target demo.”
That means there are an enormous number of possible variants for the cleat guard. Imagine that you’d need specific variants for each company’s shoe models, and then again for each size within those models.
This is why the product should be 3D printed: there are countless variations, and as each season passes, shoe manufacturers produce even more. I expect the Hypsole design database to be overflowing with CAD files.
There’s another reason for 3D printing these guards: weight. Adding a hunk of plastic to the bottom of your foot doesn’t sound appealing, as it would make your feet heavier. However, with 3D printing it is possible to design the guard with a lattice geometry that would provide the necessary strength without significant weight.
Hypsole uses Carbon’s software to generate these complex designs, and produces them on Carbon equipment at scale using Carbon’s EPU material. This is the same material that is often used by Carbon’s footwear customers for outsoles. The cleat guard is effectively an outsole, after all.
In this case it seems that 3D print technology is the correct way to produce cleat guards, as conventional approaches cannot match the weight advantages and would have financial challenges handling the enormous variety of designs.
I think we have another key additive manufacturing use case here.