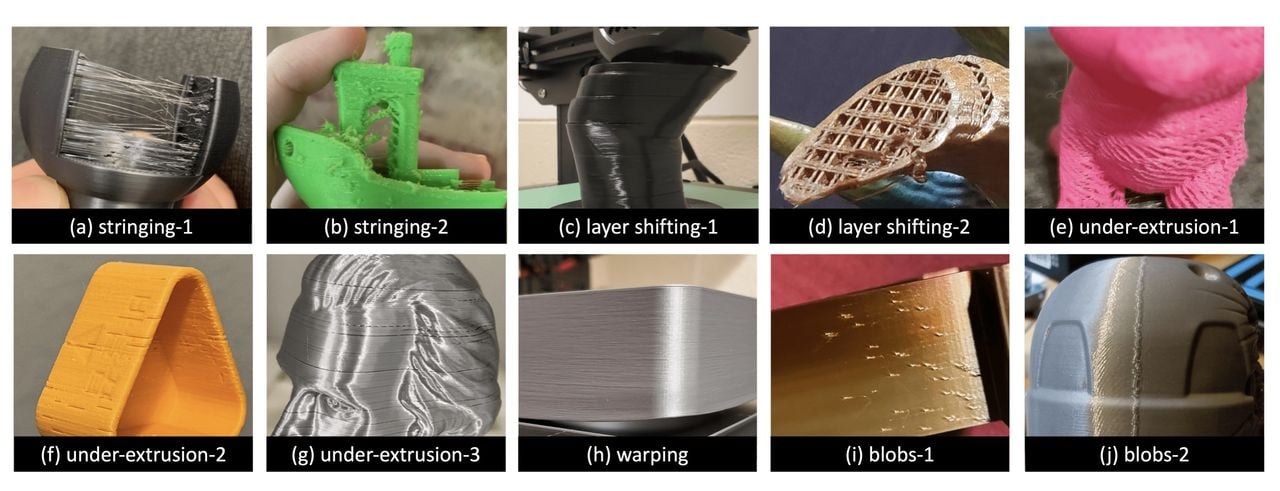
Researchers have developed a troubleshooting AI system for 3D print novices called “3DPFIX”.
The researchers were interested in learning how novices approach the often troubled world of desktop 3D printing. Everyone in the space knows there is a long period where you “learn the ropes” of 3D printing, usually involved plenty of failures and a ton of reading.
While that process is more or less expected and not considered unusual, the researchers felt that this is not optimal.
They are correct. The challenges of learning 3D printing are high enough that a significant portion of the population will simply give up. Machines can be made smarter and more reliable, but the bottom line is that there has to be an easier way to learn how to use these frequently misbehaving machines.
There are plenty of online resources available to help novices, however, so why would you need to make a new system? It turns out that these copious resources are not easily used. The researchers explain what was found when examining the workflow of 76 novice operators:
“S1 [Study one] found that users can access generic & common solutions listed in online archives, but novices had more difficulties in understanding how they can lexically explain their problem when searching. When matching their case with representative images provided for each printing failure type, their limited understanding of 3D printing and unfamiliar technical terms further constrained them. Meanwhile, we found novice users tend to rely on online communities to get custom solutions as they can inquire easily with plain languages (e.g., photos of a failed print and print settings). But there exists inevitable latency to get the answer mainly due to the unbalanced number of novices seeking help and experts who can help. Rather than doing their “homework” by reading the cumulative knowledge in the online community, we found users tend to upload the issues that have been explained in the past.”
This is absolutely true, and any busy 3D print online forum is riddled with images captioned “what happened?” This is why those posts keep happening, and illustrates the reason why a new system is really required.
They observed:
“Unfortunately, a nontrivial amount of posts are eventually left unanswered. One viable reason is that questions are repetitively overflowing the boards. Many of them share commonalities thus existing solutions can be easily found in prior posts by searching and finding similar cases, which is a practice that is not well-used by novices.”
The researchers performed a detailed survey of novice 3D printer operators in order to determine exactly how they used these resources, and thereby identify the barriers to success. They then used this information to design “3DPFIX”, an AI-powered solution.
3DPFIX includes four main functions:
- Image-based diagnosis for the easy articulation of the problem
- Visual reasoning of diagnosis for reliable relation between user-uploaded photos and diagnosed failure types
- Hover-over functions for a detailed description of technical terms
- Curated solution searching flow
What does the eventual solution look like? They explain:
“3DPFIX curates two types of solutions which leads users to follow a reasonable flow of troubleshooting to first look into the most general solution and then proceed to the custom or advanced solutions rooted in the visual information-seeking mantra. Users can begin by exploring common solutions that are likely to solve many general issues by ‘See Common Solutions’. They can also refer to the ‘clue’ to have a deeper understanding of what other phenomena could be there, which will help them self-diagnose issues. The clues about observations (e.g., popping noise while printing, the bed is wobbling) or settings (e.g., printing temperature was lower than 180 degrees when using PLA, installing new firmware) may lead users to the specific solution set.”
The concept here is quite intriguing: instead of taking technical 3D print knowledge and trying to inject it into a novice, instead we look at the novice and understand how they are able to receive and understand information. The information is then packaged in a way that they can actually understand.
This is a brilliant approach that, if widely used, would eliminate a massive amount of confusion, increase 3D printer sales, and reduce repetitive traffic on many online forums.
My question is, why wouldn’t any of the several major desktop 3D printer manufacturers take this approach to develop a system for their own equipment? That would almost certainly increase customer satisfaction and ultimately increase sales.
Via ArXiv (PDF)