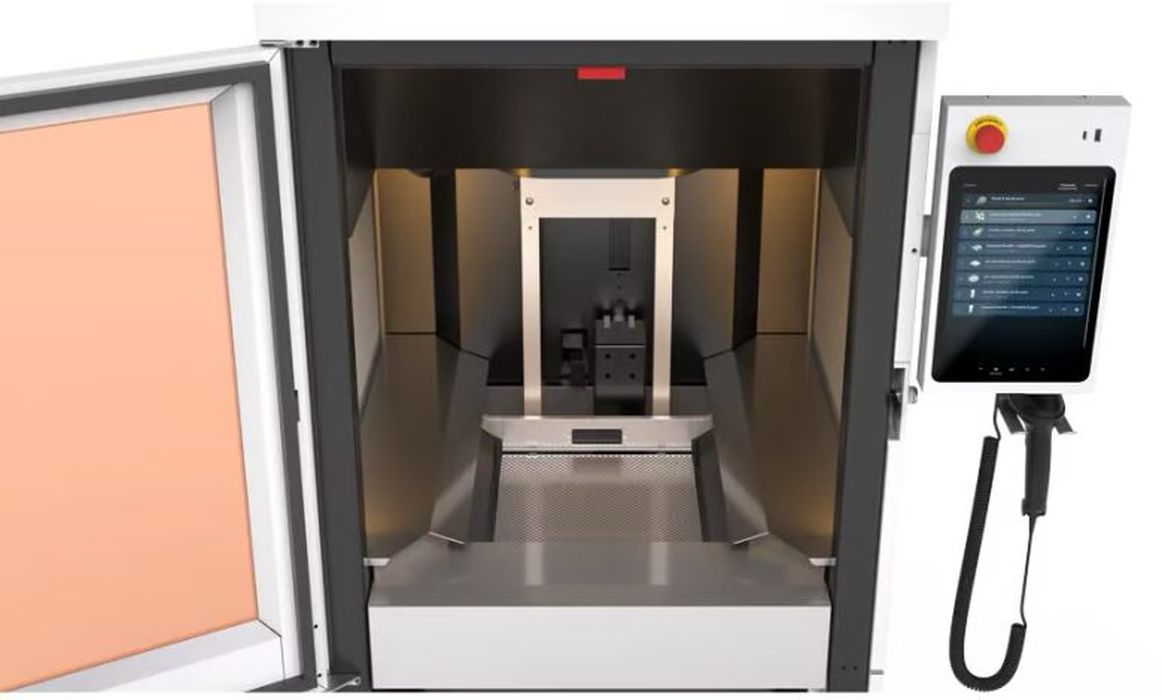
Wash and Cure solution also available with new materials for SLA, SLS and MJP.
At the upcoming Formnext fair, 3D Systems (NYSE:DDD) is introducing next-generation products in its Stereolithography (SLA) and Figure 4 portfolios, starting with the new PSLA 270, a full solution based on a DLP (projection) 3D printer. The solution includes the Wash 400/Wash 400F and Cure 400, Figure 4 Rigid Composite White and Accura AMX Rigid Composite White — to address true production applications and accelerate the time to part.
Additionally, 3D Systems has enhanced its SLS solution portfolio including new materials to drive productivity, flexibility and performance; expanded its MultiJet Printing (MJP) materials portfolio to address applications with improved efficiency and repeatability; and introduced a new powder management peripheral for its DMP Flex 200, INVAC3D, developed by Delfin Industrial Vacuums. The breadth of new technologies the company is introducing demonstrates its commitment to continuous innovation, enabling customers to transform how they deliver their products and services.
PSLA 270 for speed of light-projection
The PSLA 270 from 3D Systems is a high-speed, projector-based SLA additive manufacturing solution that efficiently delivers mid-size, high-quality parts with the most stable mechanical properties. This compact, cost-efficient, versatile mid-frame 3D printing solution provides unrivaled accuracy, and the first article success expected from SLA, with the incredible speed, and material portfolio of Figure 4 projector-based technology.
At Formnext, 3D Systems will also introduce the Wash 400/Wash 400F and Cure 400, its purpose-built post-processing solution to wash, cure, and dry parts. 3D Systems’ Wash 400 (supports non-flammable detergents) and Wash 400F (supports flammable detergents such as IPA) eliminate most of the manual cleaning of resin-printed parts.
The dual system design allows for “Dirty” and “Clean” washing workflows, a parts holder for loose parts or full-build platforms, and a piston lift mechanism for removing parts from the detergents. Both solutions have simple, intuitive user interfaces and accommodate full 400 mm build plates, making them ideal for professional and industrial workflows and facilities.
3D Systems’ Cure 400 is an advanced tool that provides scalable options for post-processing UV-curable resins. It features a rotary table for part shadow reduction, full spectrum LEDs, and a 400 x 400 x 400 mm curing volume. Cure 400 is compatible with all UV photopolymers in the 3D Systems portfolio to ensure a lasting post-processing solution.
It was designed with scalability in mind to optimize floor space and user workflows of medium-frame printer systems. Streamlined recipes control the temperature and UV exposure to achieve optimal material properties, and the rotating part platform ensures uniform UV exposure for even curing over the total cure volume.
Rigid material delivers high-stiffness parts
3D Systems’ SLA technology is renowned for being able to produce a breadth of parts in the automotive and motorsports industries. In particular, this technology, combined with 3D Systems’ materials portfolio, application expertise, and software, has allowed Formula 1 teams to build rigid aerodynamic parts for use in wind tunnel testing. The company is now also bringing these same capabilities to its Figure 4 and PSLA270 technology platforms to accelerate the time to part-in-hand.
As of today, 3D Systems is debuting Figure 4 Rigid Composite White and Accura AMX Rigid Composite White in the European market. These materials add flexibility to part production with material synergy across multiple platforms, leveraging the company’s Figure 4, SLA and PSLA technologies to produce high-stiffness parts with excellent surface quality and short turnaround times.
The materials are resistant to settling and therefore increase printer up-time through stability and significantly reduced requirement for material maintenance. The result is a more efficient workflow to create high-resolution parts. Ideal applications for these materials include parts for wind tunnel testing, small format short-run tools, jigs and fixtures, and parts exposed to fluids.
Figure 4 Rigid Composite White and Accura AMX Rigid Composite White are planned to be available in Europe in December 2024. The company intends to make both materials available in other regions during first half of 2025.
Read the rest of this story at VoxelMatters