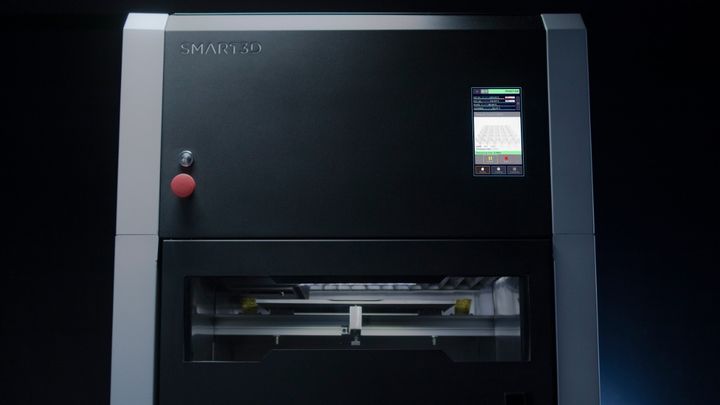
This week Smart3D International announced an interesting new industrial 3D printer, the Macro. But it turns out the software for this system is even more interesting.
Macro 3D Printer
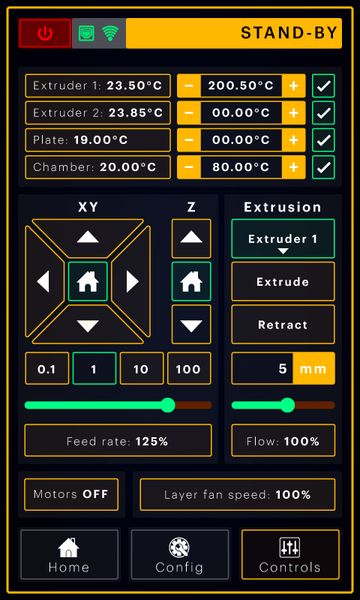
We detailed the Macro 3D Printer in a previous article, but to catch up quickly it is a combo of a prototyping unit and scalable industrial production modules. The idea is that you iteratively design your part on the prototyping machine, and then deploy it to the production units. The build chamber and extrusion mechanisms are identical between the prototyping and production units, so you can be guaranteed that production parts will match the characteristics of the intended design.
You can visualize a typical Macro configuration: a prototyping unit located in the design office, with several production units on the factory floor. The question is: how, exactly do you control them?
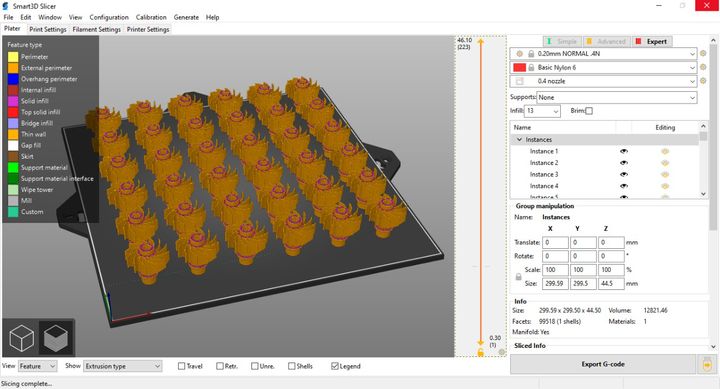
My initial assumption was that Smart3D was simply re-using their 3DPrinterOS cloud implementation on the Macro, but this turned out to be quite incorrect: Smart3D has built an entirely new and very flexible system for managing a Macro 3D printer configuration.
Smart3D’s Chief Commercial Officer, Demian Gawianski, said:
“Unlike the KODAK Portrait, the Smart3D Cloud is not 3DPrinterOS based. We needed a solution that enterprise customers can download and use locally to manage and monitor their 3D printers, as many IT departments won’t allow their IP to go to the cloud. That’s why we offer the same connectivity module in the form of either Smart3D Cloud or Smart3D LAN.”
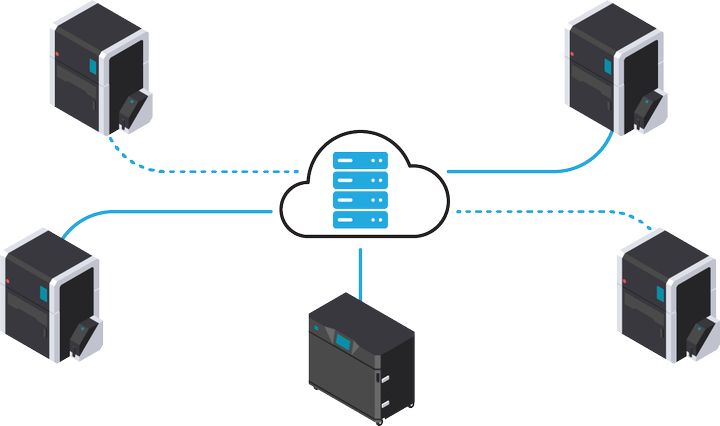
This is very interesting because there are actually TWO management solutions for the Macro. One is a cloud-based system, Smart3D Cloud, which would have each participating device connect to the cloud and coordinate activities that way.
Smart3D LAN

In contrast, the Smart3D LAN is different. Instead of going to an external cloud, it forms its own local cloud among all the participating devices. A “Smart3D Serverless Module” in each machine actually finds each other automatically and establishes this network, so long as they are on the same LAN. There’s no need for a centralized server anywhere on the LAN.
If the production units are far away and are not exactly on the same physical LAN, it’s quite possible to create virtual LANs that span distances and provide network security. This means the Macro solution could be scaled over a wide geography.

There are a number of advantages for this approach. First, you don’t have to depend on another party to ensure the cloud is running; it’s on your own premises and you can manage it yourself to whatever degree of robustness is required.
Secondly, no data leaves the building. This makes the operation far more secure than with an external cloud, where you might find proprietary 3D models traversing networks. In the Smart3D LAN concept, all data travels only on the LAN to and from the participating Macro devices.
This last point is likely critical for some additive manufacturing operations, where they are contractually obligated to maintain security and control over the data at all times. Without the Smart3D LAN feature it’s likely that such operations would never become customers.
This feature definitely puts Smart3D ahead of many other 3D printer manufacturers competing for the industrial market; it’s easy to set up and should be quite secure. Interestingly, Ultimaker successfully used the same “self-configuration” strategy in their big move into the corporate world. Perhaps Smart3D will also be similarly successful?
Macro ERP
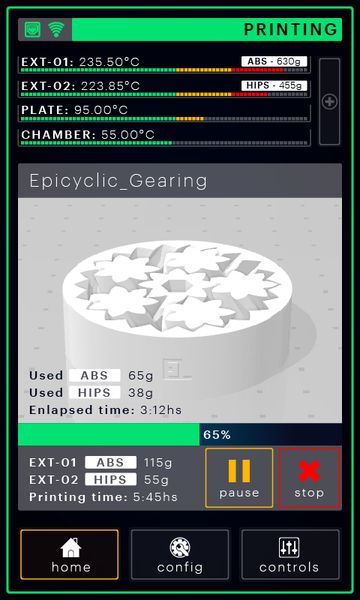
Finally, it seems that Smart3D has also included features that I really haven’t seen properly implemented in any other 3D print industrial solution as yet: proper tracking.
When a production system runs — and the Macro is intended to be a production system — there must be a complete accounting of what was produced, what materials were used, when it happened, and so on, simply to be able to account for the costs and profit for the production run. In almost all cases I’ve seen one does this manually, typically with spreadsheets.
For example, a Stratasys Fortus in our lab requires you to manually download the “machine log” and then import it into a spreadsheet where you might eventually figure out who is being charged what for the recent print jobs. That works, but is really awkward.
Gawianski explained how the software system works:
“We have integrated our software with an ERP solution developed by engineers instead of accountants and specifically for additive manufacturing. It has over twenty optional packages to integrate AM to the factory’s full workflow. For instance, it can assign an SKU to each printed part, report the customer it was printed for and follow it across the assembly, inventory, invoicing and logistics cycles. It can also easily integrate to the company’s current ERP and offers additional modules for related technologies that may be present in such a plant, such as heat treating, powder coating, etc.”
This sounds like Smart3D has developed an amazing level of integration that could easily work with existing processes in a production environment.
Like the automated networking, it appears that Smart3D is doing something similar with the software: making it easy for a customer to use the device.
I believe Smart3D has spent considerable time evaluating real-life situations and then devised the solution in the form of their Macro system. It should be very interesting to see how this affects their future, and indeed that of their competitors.
Via Smart3D