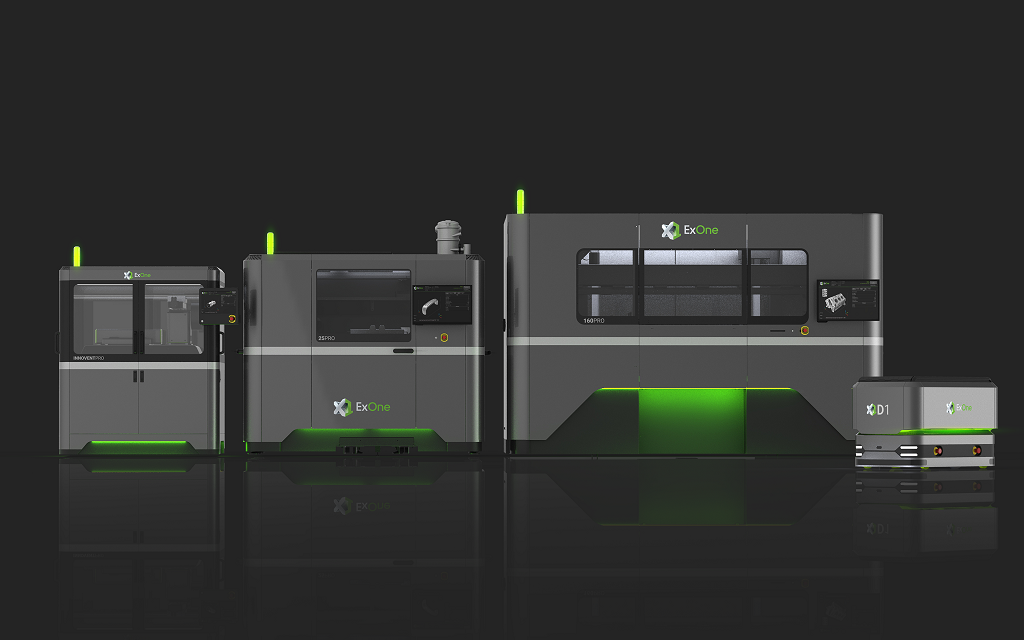
Binder jetting mainstay ExOne is introducing a new 3D printer and automation solution today.
For more context around the announcements, I spoke with company CEO John Hartner.
“We’ve been in the binder jetting world for a long time, and we’re really coming into our own,” he said in opening. “We have a range of products and introduced [the X1 160Pro] this past year as our tenth metal system. We want to keep moving forward with modularity, and to keep introducing new technologies.”
And so today we see these two new solution announcements.
ExOne InnoventPro
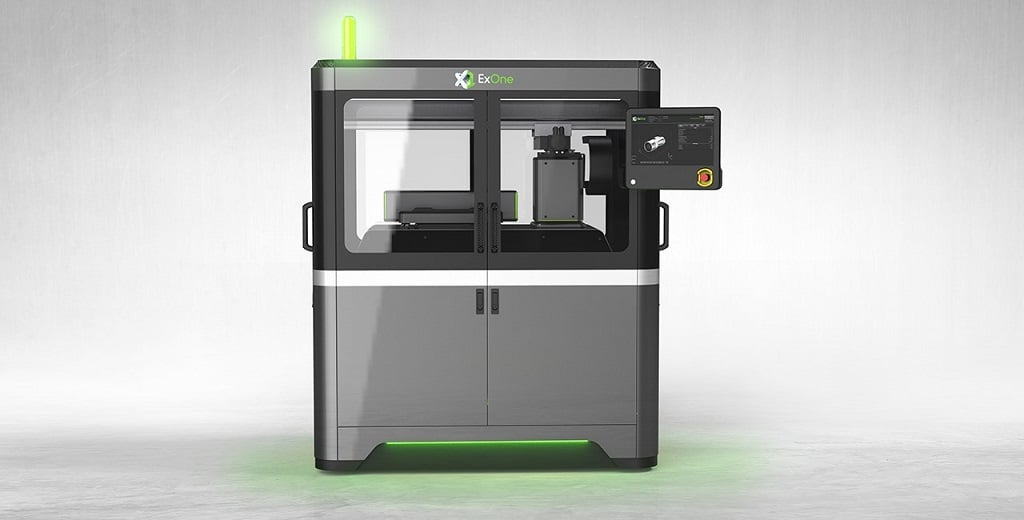
The new metal machine addition is an advanced entry-level system: the InnoventPro.
“This next system continues the game as far as what we can deliver for customers to be able to do from a technological standpoint. Innovent has been a very popular entry-level system, with papers published across the world,” Hartner said in introducing the new machine.
This system is positioned as a substantial upgrade to the Innovent+, which was introduced in 2017 as itself an upgrade to the original 2016 Innovent. The continued upgrades point to an important factor to the Innovent: it is, ExOne says, “the world’s best-selling metal binder jetting system since 2016.”
The InnoventPro is right now a preview of what the company calls “the world’s most advanced entry-level binder jetting system for printing metals, ceramics and composites.” Among the upgrades are to “make it a little larger with a 3-liter and a 5-liter version, make it a little faster,” Hartner told me. When he says “a little faster” he means it; print speeds are reported to top 700 cc/hour.
“What’s really beneficial for users is the ability to hone their use of the process, then scale up as they move into production 3D printing,” Hartner continued. “This is a natural evolution where we’re raising the bar in binder jetting.”
That scaling up can start a customer on a journey from entry-level with the InnoventPro up to mid with the X1 25Pro, then up to the X1 160Pro for production 3D printing.
An interesting factor in the InnoventPro is the technology upgrades, as well, particularly with its NanoFuse binders. I spent a little while reading a 2018 patent granted to ExOne (pdf) for “Powder particle layerwise three-dimensional printing process” but turned to Hartner and the company for a more down-to-Earth explanation. The release explains:
“First patented in 2018, with related patents pending worldwide, ExOne’s ‘inkjet-printable nanoparticle suspensions’ are slated for commercial deployment in the InnoventPro. This all-new class of ExOne NanoFuse binders advances the field of binder jet 3D printing in critical ways.
Because nanoparticles fill in the interstices between powder bed particles and can bond at lower temperatures, they enable stronger green parts. In turn, this enables 3D printing of larger parts and finer features, delivering sharper corners and edges. These new binders can also improve the resolution and sinterability of high-demand metals, such as copper and aluminum.”
The nanoparticles used in the binder jets represent something “we’ve done for a while,” Hartner said, noting that “I don’t think anyone’s as focused on that as we are.” ExOne, he continued, has put a lot of work into “enhancing powder density and material properties,” which the use of their proprietary nanoparticle technology enables.
The recirculating printhead modules seen on the X1 25Pro and X1 160Pro systems will also appear on the InnoventPro. Those printheads are key, Hartner noted: “We start with industrial printheads, not consumer or other repurposed printheads” — and because of this, “we can expand the range of binders we use.” Use of these printheads across systems will also help ease the scaling up from R&D to serial production.
These printheads are an interesting intersection between binder jetting and material jetting — usually serving more as two different branches on the additive manufacturing technology tree.
They also further open up the material palette possible. ExOne currently works with 22 materials, and is continuing to look toward more requested offerings. Aluminum and copper in particular are showing “a high interest rate from our customers,” Hartner added.
“We’re introducing the concept at this point, and plan to be showing a production unit in 2021. We’re aiming to ship in 2021 or early 2022,” he said.
X1D1 Automated Guided Vehicle
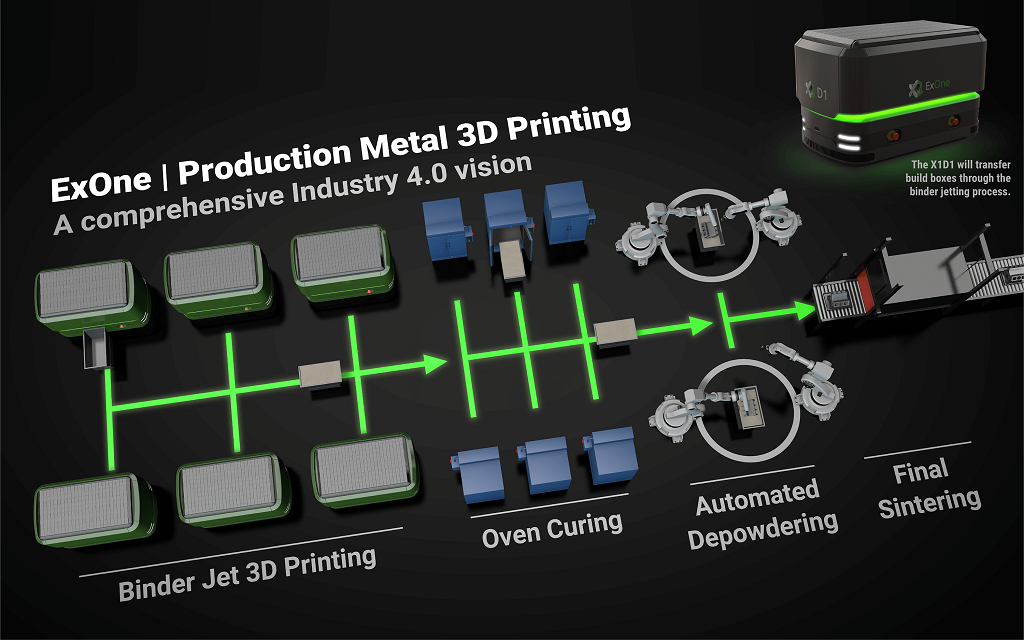
Also introduced today is a new automated guided vehicle (ADG) to enhance the automation of additive manufacturing in the ExOne workflow.
“One thing we see with the 160 is customers scaling for production on multiple machines, which have different material handling systems,” Hartner told me of this introduction. “This automates that. We’ve had enough customers asking the question of what’s the most automated they could get with multiple systems, with 5-10 machines.”
The render of the plan is very “Industry 4.0” as the concept of the work cell continues to play out for high-volume production in additive manufacturing setups. The X1D1 is designed to “enable efficient transport of 3D printed build boxes through the binder jetting process,” the company explains:
“The X1 160Pro extra-large production metal 3D printer, which begins shipping to customers later this year, will be offered with either a standard conveyance system or the new X1D1 to provide manufacturers with greater layout flexibility and efficiency. The AGV can support multiple 3D printers and processes efficiently, reducing the total footprint of the system and simplifying timed movements between processes.”
And:
“The new X1D1 AGV will lock into place at the front of the 160Pro, and will be able to roll a build box into and out of the machine. With a build volume of 160 liters, a full build box of metal powder will often weigh more than 700 kilograms, or more than 1,500 pounds. After printing, the X1D1 will transport the build box to a curing oven, where the parts are dried, before moving to an automated depowdering and cleaning station, enabled by robot arms and other yet-to-be-announced innovations, before final sintering.”
Further Industry 4.0-ing the setup is the ExOne Scout app for real-time machine monitoring, because it’s not Industry 4.0 without some IoT. ExOne Scout uses Siemens MindSphere, an IoT operating system.
ExOne System Solutions
Overall, the two introductions have a full workflow consideration in common. Understanding the scaling up of not just R&D to high-volume production, but also how to then handle high-volume production, indicates keen awareness of exactly what’s needed for a full digital manufacturing ramping up.
ExOne has long been a key player in binder jetting — but now that more players are arriving on the binder jetting scene, there’s a call to action for even the established entities to be upping their game.
“We’re taking a total view. We’re starting at entry level and scaling all the way to production; it’s not just a printer, but a whole system. We understand the materials, the technology,” Hartner told me as we wrapped up our chat.
“Our vision is sustainable manufacturing without limitations. These announcements help us get there. But we’re never done; it’s a vision, it’s something we’re always pursuing. We want to help our customers enhance their solutions, help to derisk their supply chains… We’re happy that other people are recognizing that binder jetting is the right production metal technology, and we welcome the competition. We think it helps us get better faster.”
Via ExOne