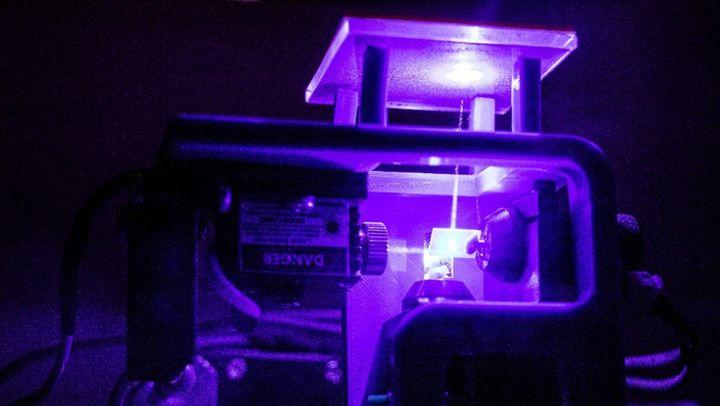
Researchers at Columbia University have developed a unique form of powder 3D printing that is inverted.
SLS 3D Printing
Typical processes for 3D printing with powder follow the PBF (Powder Bed Fusion) approach, in which a flat bed of powder is selectively energized. After this layer is completed, a fresh layer of powder is applied on top, and the process repeats. Eventually the completed object is buried in the powder and can then be extracted.
While this approach has been quite successful in both polymer and metal 3D printing systems, there is a significant limitation: only one type of powder can be used for a 3D print. Some PBF operators will mix powders together beforehand to create unique composites or alloys, but that’s not really addressing the problem.
You want to create objects with multiple materials, and that’s generally not feasible with PBF approaches.
Inverted Laser Sintering
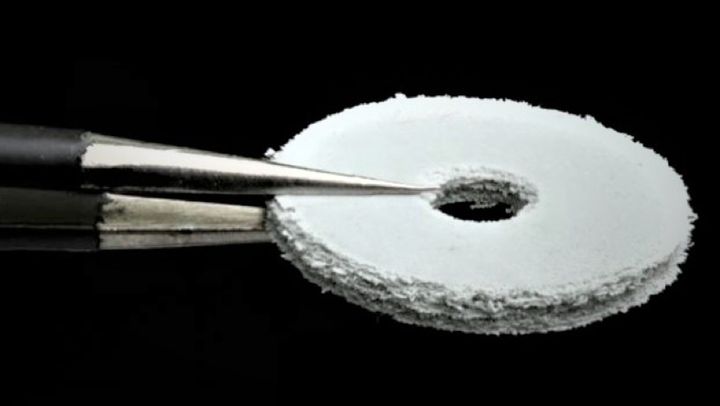
The new approach, called “Inverted Laser Sintering”, or “ILS”, was developed by John Whitehead and Hod Lipson, who has made his way into our pages on several occasions, including his breakthrough book, “Fabricated”, which explored the “New World of 3D Printing” back in 2013.
Lipson et al have been quite active in 3D printing and it’s not a surprise to see him associated with this research.
ILS is intended to reimagine the SLS process, which is a form of PBF for polymer powders. ILS works as it is named: rather than having a top-down laser beam, the laser points upwards. Shining through a clear plate, the laser selectively solidifies a thin powder layer that’s pressed flat by a prescribed weight pressing on a substrate. The solidified portion adheres to the substrate and can then be separated from the unsolidified powder.
Here’s where the magic can happen. This substrate can be transferred to another workstation where a different powder is present. This powder can be solidified into the voids created by the first workstation. By using a series of such workstations, it would theoretically be possible to 3D print several different powdered materials within the same print job.
You can see how this works in their video:
ILS Analysis
This is quite an intriguing approach, as it mimics the familiar SLA process, which is also inverted — except it uses photopolymer resin, not powder. Curiously, SLA is also a 3D printing process that can use only one material at a time.
As far as I can tell, ILS could work only on polymers, as there would be some issues with metal powder. First, I am not sure what kind of transparent plate could be used with metal that would not melt under the tremendous energy emitted by a metal-melting laser. How long would its clarity last under such stress? I’m also unsure what kind of substrate could be used to pick up fused metal powder.
The only other multi-material powder 3D printing approach I’m aware of are those from Aerosint, who are able to handle two different powders (including multiple metal capability) and have developed a fully functional commercial product. If ILS becomes commercialized, then there could be more options.
Nevertheless, this is a very interesting development that should definitely undergo further refinement. I’m curious about two aspects in particular:
What level of print quality can be achieved? Layer and XY resolution should be at least as good as conventional SLS systems.
Secondly, I’m curious about costs. It’s fine to be able to successfully achieve a 3D printing capability, but in order to be commercially successful, the process must be economical, reliable and be sufficiently speedy. A deficiency in any of those factors could doom a commercialization effort.
But these are clearly early days and there is likely a great deal of experimentation left to do with ILS.
Via Columbia