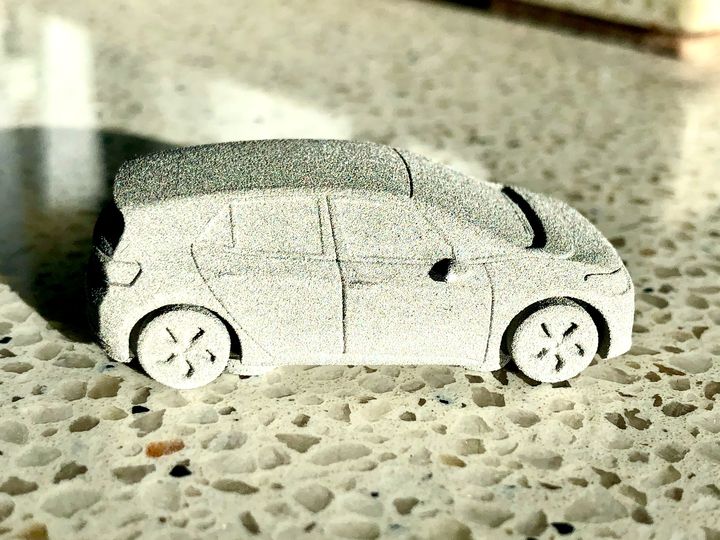
The pandemic is far from over, but its effect on 3D printing business is becoming clear.
As a result of the global turmoil, it seems there are several new business models emerging from the crisis that could open up new opportunities for 3D printing businesses.
For a short period (which varied by geography), time stopped in business as lockdowns prevented many types of business activity. Even essential services were affected to varying degrees. This disrupted manufacturing and supply chains, among other functions in today’s society.
In the resulting scramble it seems that several new business models for 3D printing have emerged.
Emergency Manufacturing Backfill
One of the most immediate effects of the pandemic was the breakdown of supply chains. Most parts sourcing for manufacturing in the West occurs overseas and thus is highly dependent on factories operating and long-distance transport.
Unfortunately, in the initial stages of the pandemic in Asia, both of these temporarily broke down. Transport in particular was affected as emergency medical components often took priority on the fewer flights that were operating. This situation demonstrated that while the carefully organized supply chains had been financially efficient, they were woefully fragile.
The result of all this was manufacturers in the West suddenly missing components. In many cases this caused temporary assembly shutdowns while awaiting parts delivery. However, in some cases it was possible to 3D print the required parts locally or even on site.
Obviously this could not be done for any arbitrary components, but for some it was indeed possible. Some manufacturers, facing no other options, finally considered using 3D printing as a means to produce certain parts.
This is immensely important as a significant portion of manufacturing management still felt that 3D printing was “for prototyping”, and not for end-use parts. That’s all changed, and now these companies know it.
The new business model is for 3D printer manufacturers to leverage this opportunity to establish on-premises 3D printing factories at manufacturers to produce parts locally, or alternatively for 3D print services to establish relationships to provide these parts. In either case it makes for a somewhat more resilient supply chain.
Manufacturer
Due to poor planning many jurisdictions suddenly found themselves short on pandemic supplies, notably PPE and test swabs. While these relatively simple products could be produced in enormous quantities by traditional manufacturing technologies, there was the slight problem of setup time.
In a pandemic, every day counts, and a day without equipment is another day for more cases to propagate. There was no time for waiting, yet manufacturers could not begin production of the required goods for weeks or even months.
As it happened, several 3D printer manufacturers found themselves with an inventory of machines that weren’t likely to be sold for a while. Ingeniously, some of these manufacturers put those devices to work 3D printing pandemic supplies.
And why not? 3D printers don’t require weeks of setup time; you merely need to configure a number of them in parallel and “push print”. Very quickly we saw several organizations producing thousands, hundreds of thousands or even millions of parts per week.
This development shocked the manufacturing world, and demonstrated beyond any doubt that 3D printing is in fact a technology not only for prototyping but actual manufacturing at scale.
The new business model here is that 3D printer manufacturers can themselves become manufacturers not only of their own equipment, but also end-use products. I expect to see several companies launch new manufacturing divisions as a result of this discovery.
Hospital Fabrication Labs
In the height of the crisis many hospitals simply ran out of consumables and equipment due to the massive inflow of COVID-19 patients. Unfortunately this is still happening in several areas around the world.
Individuals in the 3D print communities around the world sought to help by swiftly producing what they could: ear savers, face shields and other simple PPE that was desperately needed by medical facilities.
This demonstrated the flexibility to quickly create new parts to address an immediate situation. As the crisis unfolded attempts were made, discoveries occurred and designs for 3D printing emerged, were modified and even certified in some cases.
The new business model here is the opportunity for hospitals or regional hospital authorities to establish their own fabrication labs so that they can more directly address emergency situations with the capacity to near-instantly produce parts as required. Such facilities could provide value not only during crises, but also during “peacetime”, where they could act as an innovation anchor in the institution for stakeholders to experiment with new approaches.
It may be that an advanced hospital of the future may be required to have such a facility.
3D printer manufacturers could develop products and packaging specifically for this market.
Work-At-Home
The crisis forced many to work from home, some for the very first time. Many discovered they were not properly set up for home work, as networks, VPNs, laptops and other necessary items were not available or configured properly. Eventually, most people and companies figured it out.
Today we still find many people working from home and enjoying it, although there are some who don’t.
One group that had particular challenges were designers. These are people who would spend time in CAD designing new parts, artwork or other items and then require a prototype. Normally this would be produced on a workgroup 3D printer shared by the design team. But if one is working at home, that’s not going to work so well: physical 3D prints cannot be digitally transmitted to a residence.
But today’s pricing of 3D printers is such that it is more feasible for work-at-home designers to operate their own 3D printer at their residence. The prices of the equipment have fallen and the availability of useful materials has increased. It’s now theoretically possible to design and 3D print prototypes at home, at least in some cases.
Don’t get me wrong here: there are countless individuals successfully operating 3D printers at home. But almost all of them are technically-inclined folks who are able to find their way through tricky software and debug misbehaving machines. That’s definitely not the case for a random office person who may find these thing challenging.
The business model here is for 3D printer companies to organize a “work-at-home package” for these individuals. While a 3D printer and material are obvious components of the package, there would have to be improvements in workflow, troubleshooting and ease-of-use to ensure almost everyone could easily use the system.
Four New Business Models
That’s four new business models we will likely see persist after the crisis ends, and it’s all good news for 3D printing.
Do you know of any more new business applications?