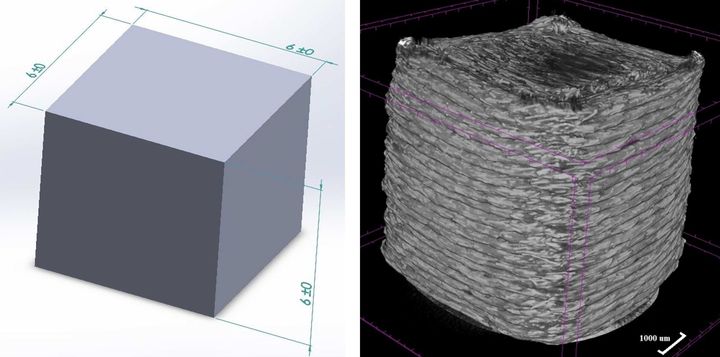
Researchers have found a way to reverse engineer a 3D printed part by examining its microstructure.
This may sound like overkill, as one might think you could reverse engineer a part by 3D scanning its exterior to capture the geometry. That 3D geometry could then be used to 3D print the part.
Or at least a visually similar object.
Problems 3D Scanning Internals
The problem here is that such exterior scanning methods do not have any visibility into the interior and microstructure of the part. If you can see it, you can scan it with conventional 3D scanners. But the interior remains a mystery.
The interior structure of a 3D printed part is critical, however, as its microstructure generally helps determines the strength and mechanical properties of the part when in production use.
The interior design is even more important when we consider the introduction of composite materials. These are unlike typical 3D prints that involve mono-materials, where you implicitly know what’s going on inside, material-wise. With composites there are two or more materials that could be arranged in any conceivable way inside the object.
Those using composite 3D printing, particularly continuous carbon fiber machines, will know that the organization of fibers is critical to achieving the design goals of a part. While it’s possible to reproduce a part with continuous carbon fiber, how could you know whether you’ve met the mechanical strength objectives? You could “overkill” the carbon fiber component, but then you’d burn your per-part budget.
There’s another aspect. Apparently it is possible to design 3D printable parts that won’t function unless the composite materials are in a precise configuration. In fact this approach can be used as a security measure to protect against others attempting to replicate the part.
CT Scan 3D Microstructure
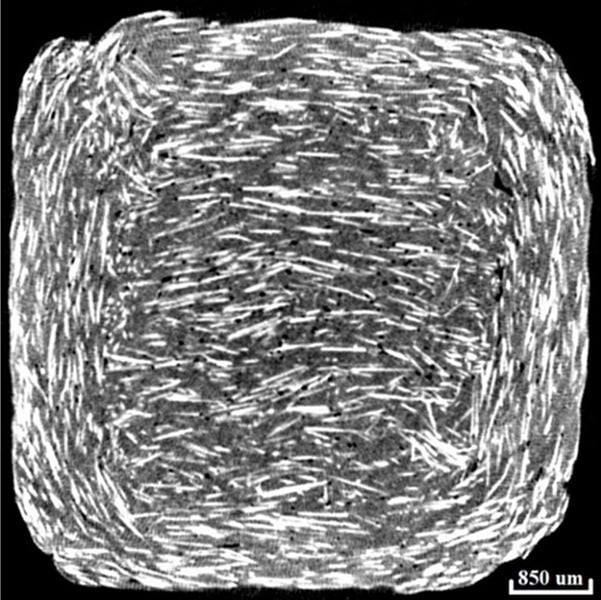
Now researchers from NYU’s Tandon School of Engineering seem to have figured out a method to overcome these challenges.
Their approach was to CT scan a 3D printed part. This produces a 3D model of the object, including its interior. By “slicing” the captured scan, they produced “layers” (which don’t yet correspond to actual 3D printed layers as we know them).
These scan layers were then exposed to a machine learning system that could interpret their appearance and re-develop the original toolpath used to create the object. The researchers were able to reproduce parts with only a 0.33% difference in microstructure by replaying the toolpath.
Reverse Engineering Microstructure
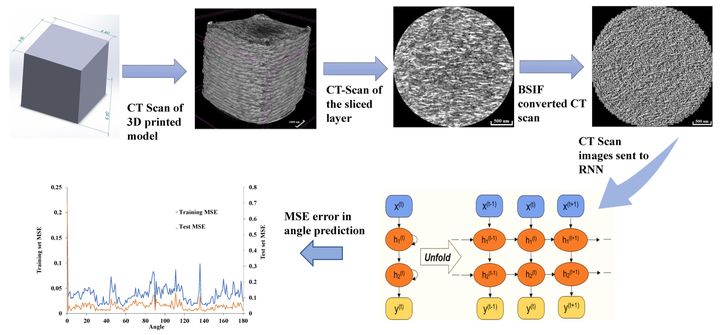
Now to be clear, the researchers were only testing with simple 3D printed cubes and cylinders with desktop 3D printing gear, and did not throw highly complex parts at their process. However, they’ve clearly proved an important point.
If you know the toolpath and the materials used, you basically know how to reproduce the object in its entirety: both exterior AND interior.
So much for the idea of using the toolpath as a security measure.
The implications of this research are simply that ultimately no part can be secure: if given access to a part, it can be very closely replicated.
Please design accordingly.
Via Science Direct