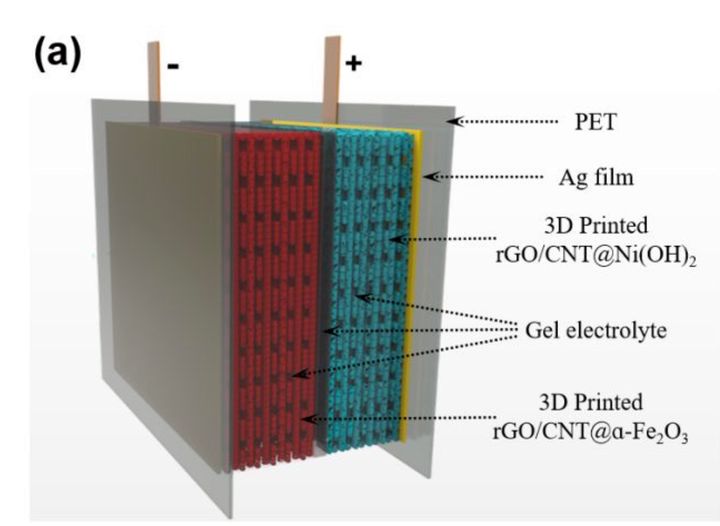
A team of researchers in Singapore and China has developed a unique process to produce compressible batteries using 3D printing.
We’re all familiar with batteries, as they seem to be present in any smart devices within reach, but some know the dangers of bending them. Lithium-ion batteries in particular have a habit of smoking, or even exploding in a pillar of flame, if their physical structure is disturbed. Just try hammering a nail through one of those batteries. On second thought, don’t do that at all!
The problem is that these batteries cannot be twisted, compressed or flexed in any significant way. However, that could all change with some new research that shows a way to make batteries with those characteristics.
The researchers were able to produce the batteries by 3D printing layers of carefully designed and processed microstructures designed to copiously soak up ions. These were assembled together in stacks up to 8mm in height, and surrounded by layers of silver and PET materials.
The advantage of 3D printing here is that the technology allows the researchers to “write” very specific structural designs into the print that enable the overall object to be completed.
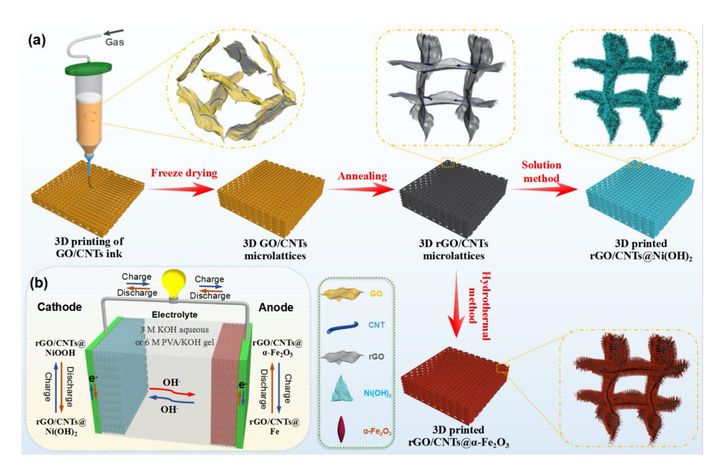
Battery technology here was in fact not the common lithium-ion type, but instead the researchers chose to use Ni-Fe, which offers some cost advantages. However, that combo also introduces some challenges, but they were overcome by leveraging the ability to 3D print specific electrode designs.
After building experimental batteries, the researchers subjected them to a number of tests, including power capacity, rechargeability and more. Of particular interest was the amount of compressive force that could be withstood by the battery and how well it continued to perform.
They found they were able to compress the experimental battery as much as 60%, which is quite significant — try that with a lithium-ion battery sometime. Actually, don’t.
They explain some of the charge testing:
“Relative to the initial capacity, the capacity retention can remain at above 84.5 % after suffering from different strains during 2000 [recharge] cycles. When the device recovers its original state, the capacities can revert to 92.5 % with 89.1 % capacity retention after 500 cycles, again implying the 3D printed QSS-NFB devices can effectively buffer and alleviate the mechanical compression/releases.”
They found power output and recharge ability varied somewhat during compressive sequences, but not in significant ways. Thus it would appear they have developed a method for making compressible — and flexible — batteries.
With this technology commercialized it would be more possible to develop wearable devices that are subject to mechanical stress. It could in theory also make all devices more safe by not exploding during a compressive event.
But at this point this is merely research, and there would have to be many more steps before this is commercialized.
Via ACS Nano