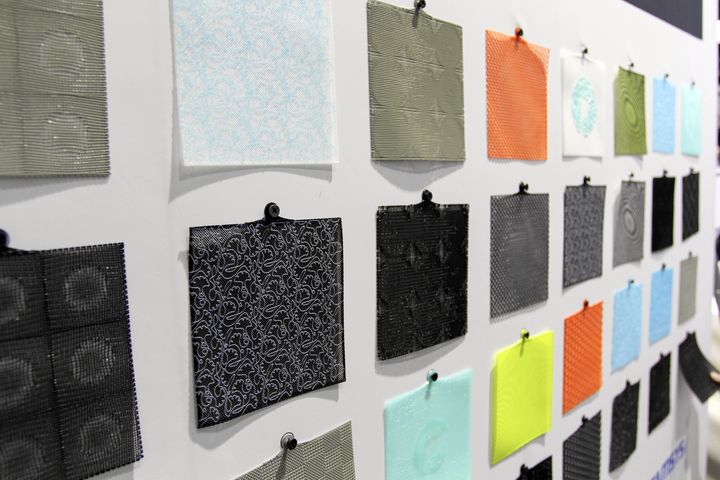
Polymaker and Covestro announced a new approach for producing 3D printed textiles, and there are huge implications.
Polymaker is a well-known Asian producer of highly-regarded 3D printer materials. They’ve been known to push the envelope in the past by developing innovative products, such as the amazing PolySmooth system, a material / device combo that can produce perfectly smooth 3D prints.
Covestro is a huge German chemical company with US$2B annual revenues. The company, like many of its competitors, has recently been delving deeper into the 3D printing world. Their “Addigy” materials line provides powder, liquid and filament-based options for 3D printers. The product line includes many different types of materials, including flexible TPU.
3D Printed Fabric
3D printed “fabric” has been around for a while, but it has been not particularly useful. Some have devised chain-mail-like objects that in some respects act like fabric. They work far better when made with higher-resolution 3D printers, like these nylon pieces:
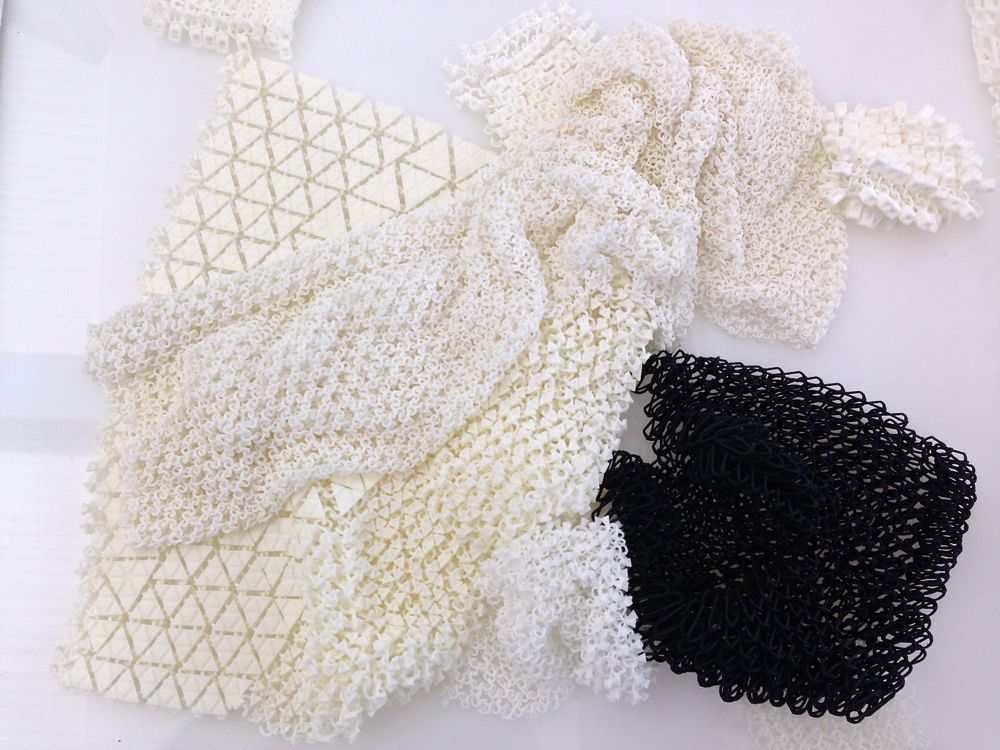
We’ve also seen some 3D printed rigid plastic on top of existing traditional fabric to produce interesting pieces, but again this isn’t really changing anything much in the fashion industry.
The new approach by Polymaker and Covestro could, however.
Polymaker Covestro Fabric
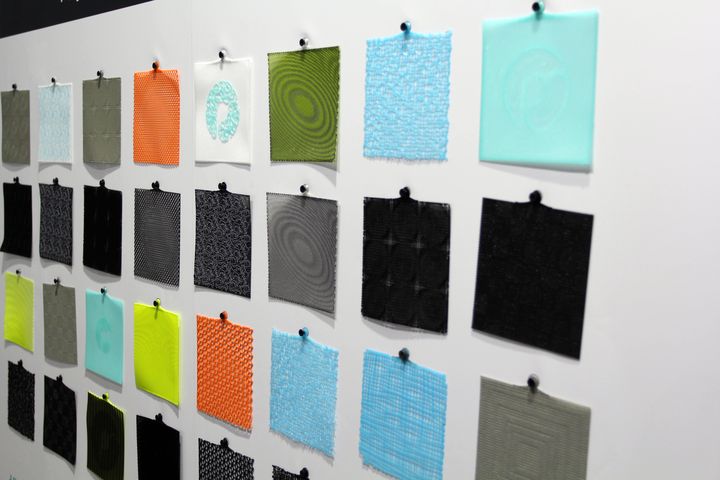
What’s happened? Polymaker and Covestro have together announced a new way to 3D print wearable fabrics. They say:
“Covestro and Polymaker have jointly developed a new processing technology with the industry’s top 3D printer manufacturers INTAMSYS and Raise3D to improve mass production and efficiency of 3D printed fabrics. The INTAMSYS FLEX 510 printer and Raise3D E2 printer are highly adapted for printing flexible materials which match the characteristics required for 3D printed fabric.”
It seems they’ve combined three key elements in their new “processing technology”: hardware (flexible-material specialized 3D printers), flexible materials and new design software specifically for fabric development.
Using the new software, designers will be able to easily create highly unusual and perfectly customized fabric solutions. They say:
“The 3D printed fabric jointly developed by Covestro and Polymaker takes a new approach to fabric manufacture by utilizing 3D printing to create a 2D fabric. This has more practical value other than waste reduction and can create patterns and style with use of computer algorithms. The 2D fabrics are then integrated into the existing workflow to create a customized 3D object such as: hats, shoes, bags, scarves, gloves and other clothing accessories.”
They also say the new process can create fabrics with density gradients, moire patterns and other effects that are effectively impossible using conventional fabric development methods.
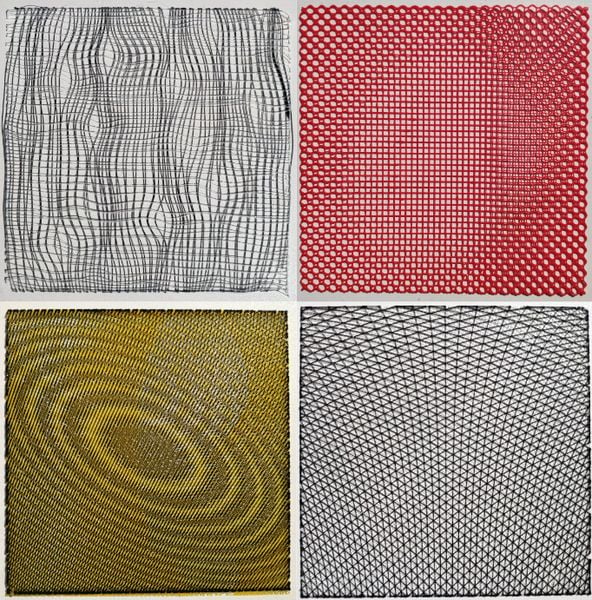
Apparently the system is also focused on production, whereby large unit counts of items can be produced on arrays of suitable 3D printers. This suggests another way to implement a mass customization solution, this time for the fashion industry.
There’s also ways to “program” the 3D printed fabric:
“In order to meet different elasticity, strength, and hardness requirements, in addition to the performance of the material itself, the texture design and printing method of the fabric also have a critical impact. Polymaker and Covestro have explored and developed valuable methods and experience in this regard using algorithms to generate organic texture where strength is needed while allowing more breathability in areas of less stress. This allows designers to optimize their fabric and create tailored 2D patterns in the most lightweight and efficient way, in high-stress applications such as the printing of running shoe patterns this advantage becomes obvious, where lower stress fabrics can make use of the aesthetic advantages.”
Fabric 3D Printing Implications
My head is spinning after hearing this.
Up to now 3D printed fabrics have essentially been science experiments that had little practical value. Having personally attended several 3D printed fashion shows, I can see this form of 3D printing is quite different from the constrained, expensive and impractical fashions previously presented.
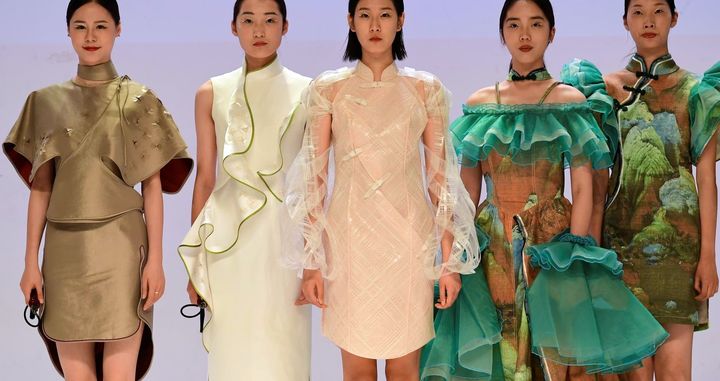
Here you can see an image from Covestro showing apparently 3D printed fashions. These items appear quite practical and also fashionable, and thus this suggests opening up the possibility of actual end-use production using this process.
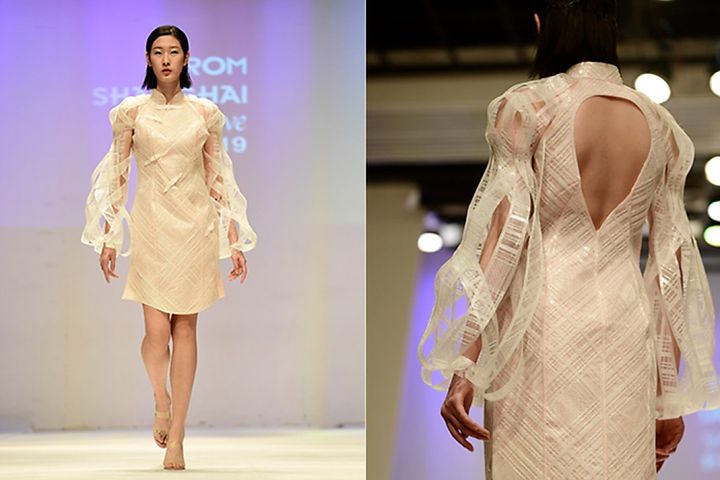
I recall seeing a large 3D printed headpiece at a fashion show years ago that supposedly cost over US$30,000. That price level relegates 3D printing to the experimental zone, and I hope that’s not the case with the new Polymaker / Covestro system.
We don’t yet know the pricing for this process, but if it is reasonable, then we may expect to see leading fashion designers begin experiments with the technology and produce custom-fit pieces. More than likely the initial products will be expensive as the fashion designers using the system will want to recover their setup costs.
But over time I can easily see a staggering variety of fashions emerge from the minds of designers who, up to now, have been constrained by the limitations of traditional fabric.
Unleash the designers!