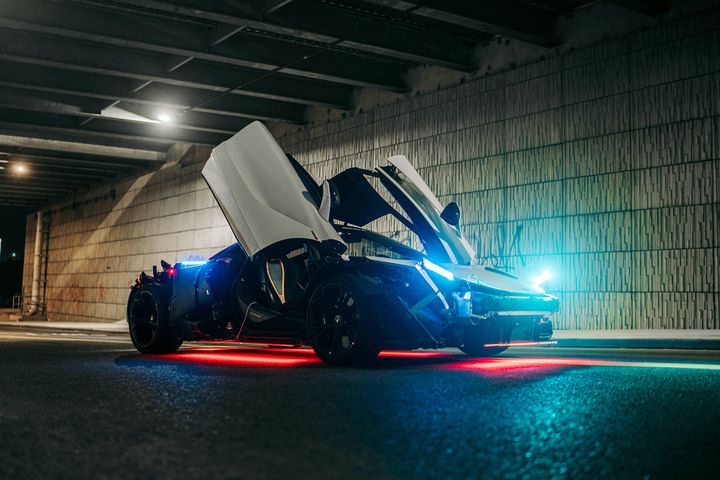
Could aftermarket parts be a niche application for 3D printing? I think it has huge potential.
I’m reading a story about an aftermarket auto parts manufacturer that leveraged 3D printing to produce more advanced forms for their latest parts set.
Aftermarket parts are made independently of the original automobile manufacturer, but are designed to enhance the looks or performance of a vehicle. Typically they’re consumed by enthusiasts looking to get the edge on their unique vehicle. Indeed, aftermarket parts can make a vehicle unique among others of the same model.
McLaren 720S Supercar
In a story in CarBuzz, Florida-based 1016 Industries was shown to be producing specialized aftermarket parts for the 2020 McLaren 720S supercar. The 720S is a pretty special car, having a 0-100kmh time of only 2.8 seconds. It will take you much longer to read this paragraph!
To get a feel for this car, watch this quick video where a reviewer cranks it up to an astonishing 330kmh:
The vehicle is also a bit pricey, at over US$300,000 for a unit, depending on options selected. Thus it’s a vehicle one might find only in a few households, and McLaren produces only a limited number of units each year.
1016 Industries is now producing what they believe are the only 3D printed aftermarket parts for the 2020 McLaren 720S. 1016 Industries Founder Peter Northrop said:
“Our focus for this project was exploring how we could employ 3D printing in the automotive world, and the results creating these McLaren 720S parts are impressive. The 3D printing process has not only allowed us to manufacture faster and more efficiently, but we’ve also improved quality. The 3D technology has allowed each 1016 Industries part to be even more accurately made, with each part printed in real scale to validate our CAD and CFD work.”
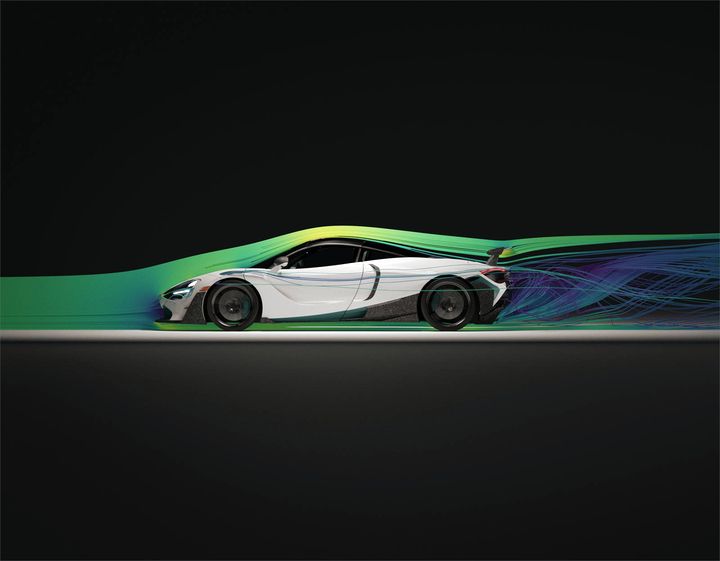
Evidently 1016 Industries used FEA to help design the complex parts for their aftermarket project.
3D Printed Aftermarket Parts
This is clearly a win for 1016 Industries, but I think there’s a larger concept at play here.
Readers will recall that at the moment 3D printing is feasible only a few select industries, including:
- Prototyping
- Dental
- Aerospace
- Certain Automotive
- Certain Healthcare
- Low-volume production
Many of these industries have only taken up 3D printing in the past few years as a result of the availability of end-use suitable materials. Aerospace, for example, could not build rocket engines unless specific types of metals were 3D printable. But now there are many choices and thus there is an increasing amount of production work being done with 3D printing technology.
The industries listed above tend to have several common characteristics that enable financially feasible use of 3D printing:
- Only low unit volumes required
- Unusual geometries required, sometimes custom per job
- Typically high cost of parts in that industry
With the major constraints on 3D printing being slow production rates and expensive parts, you can see how industries with these characteristics would not particularly be bothered by these constraints.
But now it seems that the aftermarket parts industry fits quite well into that same envelope: it is end-use production parts with low volumes; buyers typically pay higher prices for them; some parts may be custom-designed per project.
It seems to me that aftermarket parts — for many industries, not just automotive — could be a good fit for 3D printing. General aviation, automotive, appliances, home renovation, hand tools and many others could all benefit from aftermarket parts that add value.
Perhaps some of the 3D printer manufacturers could consider this area as a potential market and develop programs to assist these aftermarket parts producers entry into 3D printing?
Via CarBuzz (Hat tip to Tuan)