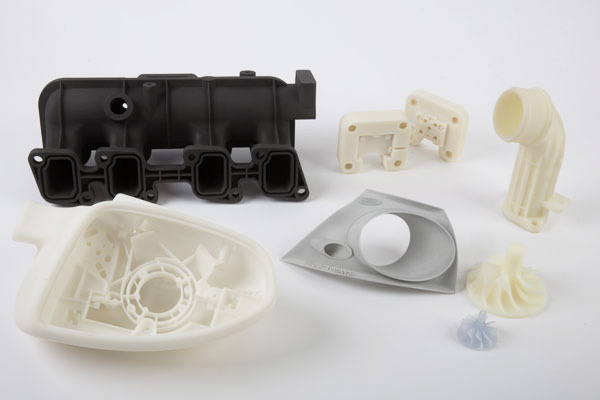
Charles R. Goulding and Ryan Donley look into the place of 3D printing in a reshaped auto part supply chain.
As the COVID-19 outbreak continues to strain the economies of the world, the auto industry is being hit especially hard. The automotive industry is experiencing an unprecedented strain on sales that could lead to an increase in costs absorbed by the industry as companies would not want to pass the rising cost onto the consumer.
Carmakers rely on thousands of individual suppliers to produce and deliver parts on tight schedules and budgets to have them instantly available on the production line as well as to dealers maintenance departments. Now suppliers are operating nowhere near their full capacity during this crisis and crucial car parts will be at a premium. Additionally, the bankruptcy to Hertz is leaving 700,000 used cars being placed into the market with unknown ramifications to the part market.
This current point in time presents an opportunity for suppliers and car makers to turn to new forms of production of parts. Insert 3D printing where parts can be produced with far less overhead and trickle-down cost savings through the chain.
Borg Warner/Delphi
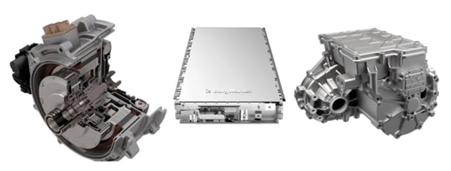
Two massive auto part manufacturers are coming together as Michigan-based BorgWarner is finalizing a deal to acquire Delphi Technologies. BorgWarner is a 90-year-old manufacturer of powertrain components while Delphi is a powertrain aftermarket part manufacturer. Delphi has been utilizing 3D printing technology for years in the production of prototypes and small-batch productions. With the BorgWarner buyout, the technology could be leveraged on a grander scale as the design freedom of additive manufacturing will grant more accessibility to engineers and designers to develop new products.
Visteon
![Text Box: Visteon Cockpit inside Volkswagen [Source: Autonomousvehicletech.com]](https://www.fabbaloo.com/wp-content/uploads/2020/06/Auto-Part2.png)
Visteon is a leading automotive component supplier of cockpit electronics and modules with numerous facilities across 26 countries. They are notably one of the highest awarded automotive part suppliers in their field. This is in large part due to their expansion into 3D printing in which the company has been utilizing EnvisionTEC’s Perfactory machines to quickly assemble modules for housing and button components of their cockpit control parts. The capability of Visteon with the use of the perfunctory machines allows the company to model parts for function overnight and have them assembled the same day.
Lear
![Text Box: Lear Smart Seating [Source: Lear]](https://www.fabbaloo.com/wp-content/uploads/2020/06/Auto-Part3.png)
Lear is a Michigan-based leader in vehicle seating and electric system part manufacturing and development. Lear began experimenting in additive manufacturing a few years ago when they were the first round of investors into NanoSteel, a company focused on nanostructured steel materials. These materials give a unique blend of high strength, enhanced formability, and lighter weight. As a result, Lear has since been experimenting with optimizing part geometries and cutting costs of normally higher production processes.
Dana Inc.
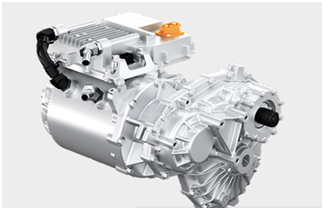
Dana Inc. is an international large scale automotive company that specializes in supplying drivetrains, sealing and thermal management technology, and energy management solutions. Dana has been experimenting with additive manufacturing for several years and have come to find new approaches to the way they design, engineer, and manufacture some of their parts compared to traditional methods. The company has found that for lower volume production parts and replacement service parts, additive manufacturing has drastically reduced their risk with these batches due to the lower cost of tooling, reduced weight parts, and speed-to-market production. Dana is continuing to further experiment with additive manufacturing to expand upon its uses for the new functionality of its parts.
3D printing of automotive parts and similar activities can be supported by R&D tax credits, which are briefly described below.
The Research & Development Tax Credit
Enacted in 1981, the now permanent Federal Research and Development (R&D) Tax Credit allows a credit that typically ranges from 4%-7% of eligible spending for new and improved products and processes. Qualified research must meet the following four criteria:
- Must be technological in nature
- Must be a component of the taxpayer’s business
- Must represent R&D in the experimental sense and generally includes all such costs related to the development or improvement of a product or process
- Must eliminate uncertainty through a process of experimentation that considers one or more alternatives
Eligible costs include US employee wages, cost of supplies consumed in the R&D process, cost of pre-production testing, US contract research expenses, and certain costs associated with developing a patent.
On December 18, 2015, President Obama signed the PATH Act, making the R&D Tax Credit permanent. Beginning in 2016, the R&D credit can be used to offset Alternative Minimum tax for companies with revenue below $50MM and, startup businesses can obtain up to $250,000 per year in payroll tax cash rebates.
Conclusion
The auto part supply industry has recently expanded its capabilities to new thresholds through experimentation in 3D printing and similar activities. The low-risk and low-cost processes of utilizing the technology and design methods are a promising sign for the future of the automotive industry as a whole even in a post-pandemic return to normalcy as major auto companies will seek new part solutions for the sake of their bottom line and helping the consumer wallet.