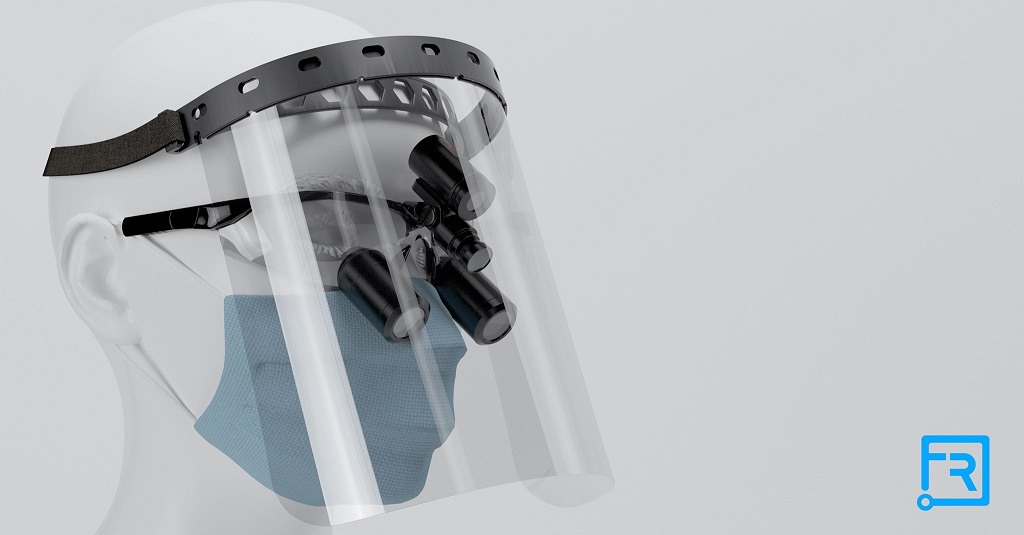
Pandemic-driven transitioning is leading to an interesting long-term reconfiguration of factory work.
I spoke with Co-Founder, Chief Fulfillment Officer, and General Manager John Nanry and Director of Marketing Lindsay Baish of Chicago-based Fast Radius for a look into how this manufacturing technology company is approaching new world conditions in 2020 and looking beyond.
Fast Radius COVID-19 Support
As the novel coronavirus began to spread in the US early this spring, Fast Radius took a step back to see how to help. After a week or two of working to understand the scene, Nanry said, “we dove in.”
“I’ve spent most of my career in manufacturing, applying technology for how orders are fulfilled,” he told me. “It’s been a really interesting ride over the last 4-6 weeks.”
Fast Radius has gained notable experience in 3D printing, alongside more traditional CNC machining, urethane casting and injection molding, over the last several years. The company has put funding toward expanding its suite of additive manufacturing technologies — and those efforts have proved to have been wise in the face of rising demand for quickly 3D printed products lately.
“The first week we were just inundated with people, wanting to know if we could help with PPE or with this ventilator component,” Nanry explained. “You know, 3D printing isn’t magic; there’s still a lot of development that goes into production. When states started going into lockdown it was really interesting for us, we were getting contacted by state agencies and private institutions just looking for help — looking for parts, looking for PPE.”
Once they dove into efforts to help, the team were all in. First came the release of an open source face mask design. Based on early talk about respirator shortages, including a high-profile 3D printing effort in Italy to supply valves, the Fast Radius team set to understand how they might help. 3D printing, though, is ultimately more expensive and even with higher-throughput industrial machines isn’t perhaps best poised for more than very immediate response: “so we realized that was not the best use of what we had.” They are still working on some exploration of 3D printing and conventional manufacturing for ventilator components.
“We started to look to face shields, where we could produce a large quantity,” Nanry continued. “We quickly set up the supply chain for the full shield assembly, and quickly designed the halo piece that has a bit of different functionality than the other ones on the market that makes it really easy to keep that halo and use it with multiple shields over the lifetime of that part.”
As of the time of writing, Fast Radius is reporting that it has shipped 15K kits and 82K shields for a whopping 880K wears. With a capacity to produce 10,000 of the kits daily — each kit containing one halo headband and two interchangeable protective shields — Fast Radius created what they call a simplified and improved face shield design; it is an FDA-registered, Class I medical device. These shields are reusable because each polycarbonate shield can be cleaned and used for up to two weeks, while the reusable halo headband — with the band 3D printed with Polyamide 12 or Digital Production Resin 10 (Black or White) and the head strap made with Nylon — allows for easy removal and swapping out of any industry-standard shield replacement. The kit function brings down the average per-wear cost of a shield from $5-9 to $1.50 per use.
Fast Radius has also been working on 3D printing nasopharyngeal test swabs and some other COVID-19 response products; more can be seen here.
“We’re working with a few players on bringing some of our capacity to bear on swabs production,” Nanry said, moving toward the bigger picture. “I think that’s one that’s exciting for us in the additive industry: 3D printed designs are more functional than legacy designs. There’s a real competitive advantage of not just fulfilling the short-term need, but the long-term need.”
Changing The Factory
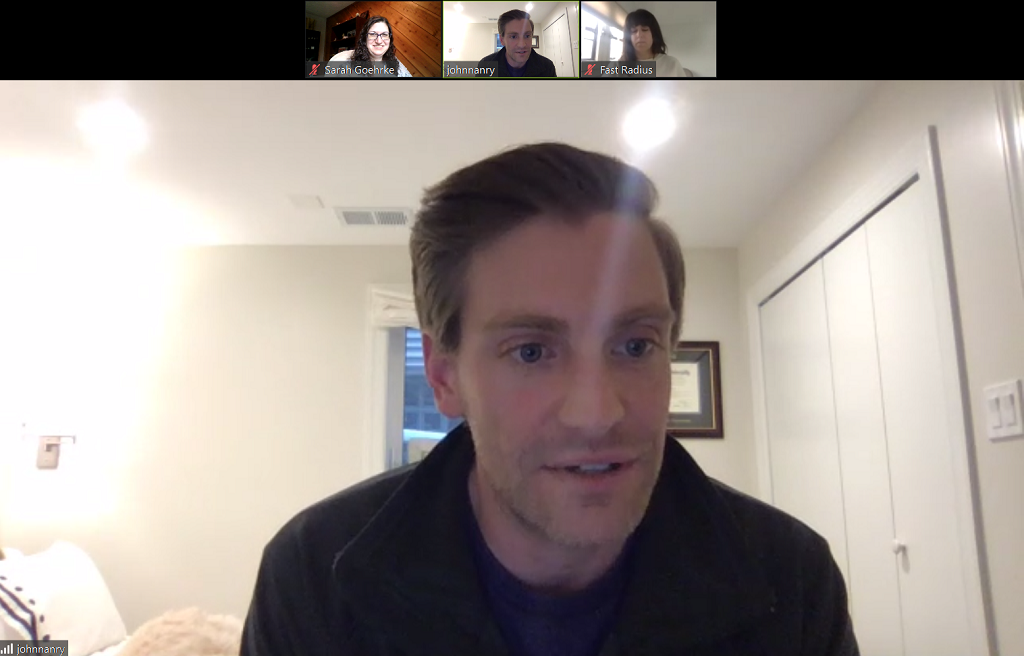
Looking toward that long-term need, Fast Radius found that it was asking the million-dollar question becoming so common among service providers: what now? What next?
Nanry and the Fast Radius team have clearly been considering these implications, and what crisis response might mean for manufacturing operations.
“Looking more broadly, companies historically invest in R&D and new product development when broader economic downturns happen. They’re looking for new products, looking to innovate themselves out of the downturn,” Nanry said.
“You always want to be the company that goes against some of the broader economic downturn, and then when the economy comes back up you have these new products to drive demand. What we see as an opportunity for us is, we often help customers with new product development and quickly help them to iterate new designs and take them to market in a quick way — in a way that additive manufacturing uniquely enables. We think we are uniquely positioned.”
Fast Radius has had customers start coming to them to start examining options to innovate new products. They are, as Nanry puts it, “innovating themselves out of the downturn.”
Along with the obvious health impacts of pandemic, there has been significant impact to the global economy over the last few months. While producing PPE is keeping many a manufacturing service afloat right now, and keeping them more than busy, there is need to look beyond crisis and into that lingering question of the Next, of that period beyond pandemic, hard as it may be to fathom at present.
“There’s a lot of uncertainty, too,” Nanry continued. “It’s unclear when folks will start to get back to the office. We have a lot of customers that have furloughed a lot of their staff. There’s more uncertainty about when some of this innovation inundation will happen at a broader scale.”
There’s been some impact at Fast Radius too, of course, as unusual times have derailed business as usual. Baish pointed toward some upcoming news the team had been preparing to share out — but this has become a time of more metered, cautious messaging. We’ll have some to share on that front when they’re ready to talk about it more openly, including work in virtual warehousing and a transitioning of airline tools to additive manufacturing, as well as serial production with additive manufacturing.
“When I started in 2018, I was employee 28; now we’re almost 140,” Baish said of working at Fast Radius. “The company’s been growing incredibly fast. I wouldn’t say we’re entirely paused on that growth, we’re well positioned. There’s more on the horizon as we’re growing and building out more of that factory capability.”
Closing out once more on a theme of looking ahead, Nanry noted that he initially had some worry about the place of 3D printing in the public eye.
“Five weeks ago, I was a bit concerned there would be this wave of hype and disappointment of ‘let’s 3D print everything.’ Again. It’s actually really exciting for me to see things like the swabs getting lots of coverage, though. There’s a lot unique to additive happening, with the face shields, with all these supplies really in the market.”
3D printing is proving its value in terms of crisis response — and becoming well poised indeed for that time post-pandemic as it proves its quality as a viable manufacturing technology. With more production becoming localized as global supply chains necessarily reconfigure during pandemic-induced shortages and slowdowns, additive manufacturing is ready to decentralize production, fulfilling promises long since made earlier on the hype curve.
Via Fast Radius