![Fortify Founder and CEO Josh Martin holds up a part to show me during our Zoom chat [Image: Fabbaloo]](https://fabbaloo.com/wp-content/uploads/2020/05/joshmartinfortifyprint_img_5eb067df5bb96.png)
Fortify Founder and CEO Josh Martin holds up a part to show me during our Zoom chat [Image: Fabbaloo]
Fortify recently introduced its new Continuous Kinetic Mixing (CKM) module; now, the company’s CEO fills us in on its importance and on plans for the future.
I caught up with Josh Martin to discuss the latest introduction from the Boston-based company, as well as their plans to start releasing their 3D printers into the field this summer.
Fortify’s use of magnetic 3D printing in their FluxPrint technology offers some truly intriguing properties for fortified parts. By utilizing magnets, they can selectively orient additives. On a show-and-tell level, that means the same additives can be present throughout a part, but oriented for visibility — like the company’s trademark “F” design, as Josh holds up in the photo above from our Zoom chat.
FluxPrint x CKM
So what does CKM add to this?
“What this means is this mixing process will increase our abilities,” Martin explained. “It really gets at that pain point of a lot of the materials at the limit on processability — for materials that are viscous, where you’re looking to do more than aesthetics or make a prototype part, that really require a vaster array of tools from a materials selection perspective. This CKM allows us to process those harder and more valuable materials for manufacturing.”
One of Fortify’s application areas of focus is injection molding tooling. Their technology allows them to keep very dense ceramic reinforcing particles in suspension “in ways you wouldn’t be able to process using an alternative 3D printer,” Martin went on.
This has been resulting in new performance metrics in terms of strength, stiffness, and temperature tolerances, for example.
Opening Up Applications, Material Types
“It’s allowing us to get into other areas that require unique functional performance,” Martin told me. “Look at heavily filled systems for high-frequency electronics — this is a pretty new space for additive manufacturing that we’re going to be talking about a lot more in the upcoming months. We’ve validated initial systems that I would say are new for the light-based printing space.”
The CKM process is also a big part of the company’s work in enabling new material types, it seems. For example, a liquid resin — “that prints like most DLP systems” — can be reinforced with ceramic fibers, with the resulting print fired as would be done in traditional ceramic 3D printing.
To highlight the capabilities, the team also shipped me a part made of steel particle-reinforced resin.
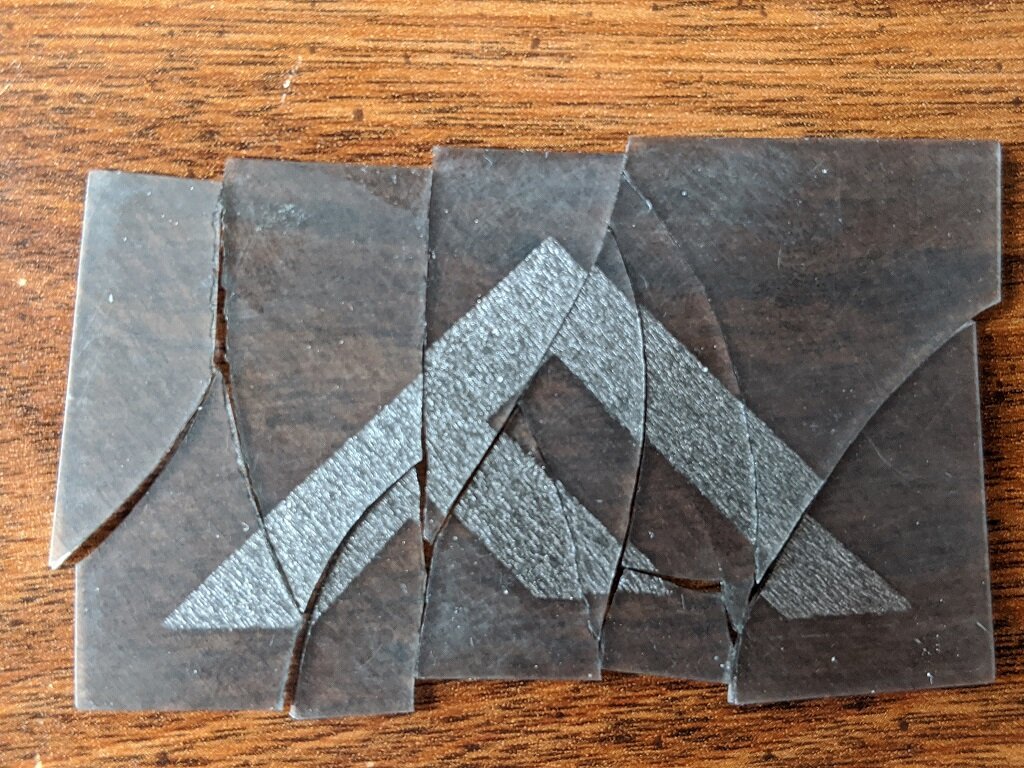
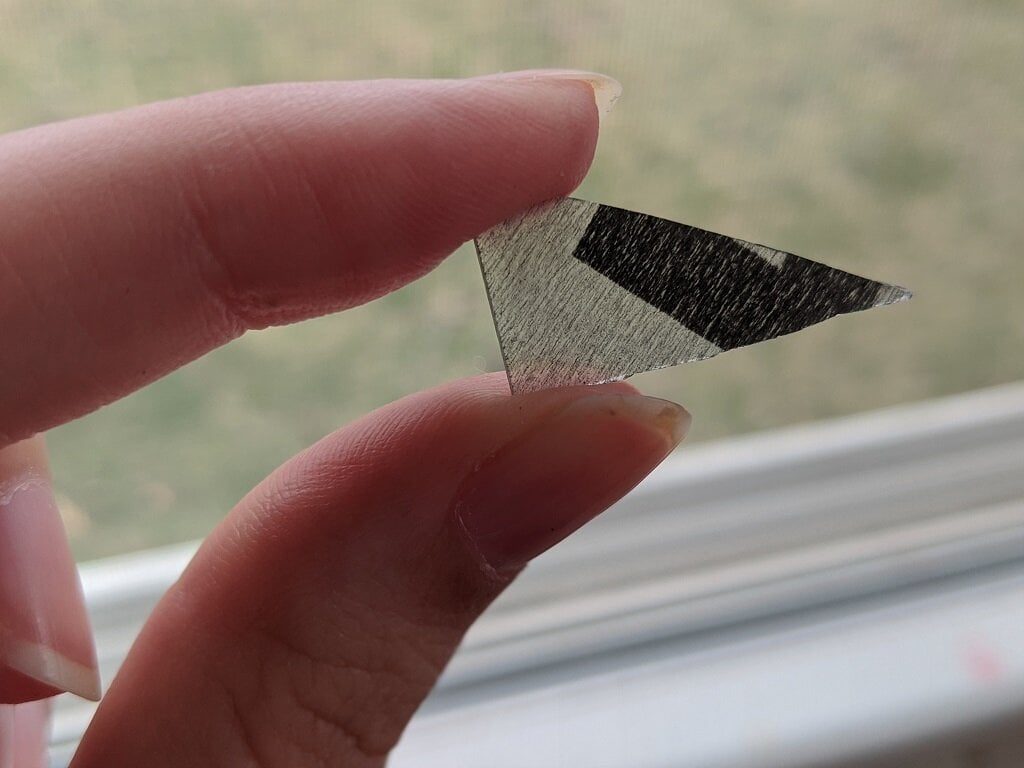
Unfortunately the relatively thin, flat part did not survive its USPS experience intact (but at least I got to do my #StayHome puzzle, as these seem to be a very popular activity just now; fortunately mine wasn’t anywhere near 1,000 pieces). While at a standard tradeshow I would have had access to a part that didn’t probably get sat on, stepped on, or at the bottom of a bunch of heavy shipping parcels, even getting hands-on with the shards of the piece do show its strengths and the oriented fibers — as seen in the shard held up to the light.
“The ability to use metal within a polymer in this case allows us to approach ESD ratings, which is big for the tooling, jigs, and fixtures industry,” Martin told me of the sample part. “Using mixing, heating, dispensing, and magnetic alignment technology allows us to not only print these composites, but order them in a way that maximizes performance.”
![The fortified Fortify print before it was unkindly treated by the postal service [Image: Fortify]](https://fabbaloo.com/wp-content/uploads/2020/05/fortifyunbroken_img_5eb067e09711e.jpg)
The fortified Fortify print before it was unkindly treated by the postal service [Image: Fortify]
A big takeaway that he underscored is that this means the Fortify team will be opening up “a whole suite of materials that are pretty common and sought after in traditional manufacturing.”
“Fiber-reinforced plastics are typically of high value; you’ll see a lot being molded for certain applications,” Martin said. “The key tenet we’re trying to bring to the field is reinforced plastics without going through an expensive process.”
Most currently available 3D printing materials are focused on pure polymer formulations. The CKM is enabling Fortify’s offering to be a “much more rugged material system,” Martin underscored, “which we think is one of the key bottlenecks to 3D printing being adopted at scale, not only throughput, but the performance of parts that can be made.”
System Release
Fortify has been 3D printing parts for customers, but soon customers will be printing their own parts.
The next big release for the company — at least that they’ve announced so far — is the commercial launch of their 3D printer to select customers.
To prepare new users, the Fortify team will be offering demos regarding what materials can be processed and what the system looks like; with the lack of in-person events, they’re currently retooling those for digital release.
Modular Strategy
The CKM module is just that — a module.
Martin notes that they see CKM “as a base technology for all the units we’re rolling out.” Modularity is proving an increasingly popular strategy for 3D printing hardware, as it allows for user customization of exactly the capabilities they require — no more, no less. So it’s quite promising that this is the tack Fortify is planning to take.
“This module not only allows for new materials to be processed, it takes materials you might be familiar with today and provides a higher degree of viability,” Martin said of the CKM. “The reality is that right now every day or so somebody has to go into the reservoir and manually stir things up. We think that keeping everything automated will allow for more reliable processing, more reliable parts, and less user interface required to keep the machine running. This is a big part of our suite of printers.”
We spoke a bit about their upcoming plans, and there’s a lot to look forward to with their Digital Composite Manufacturing (DCM) process — but for now we’ll just have to say stay tuned for more from this inventive team.
Via Fortify