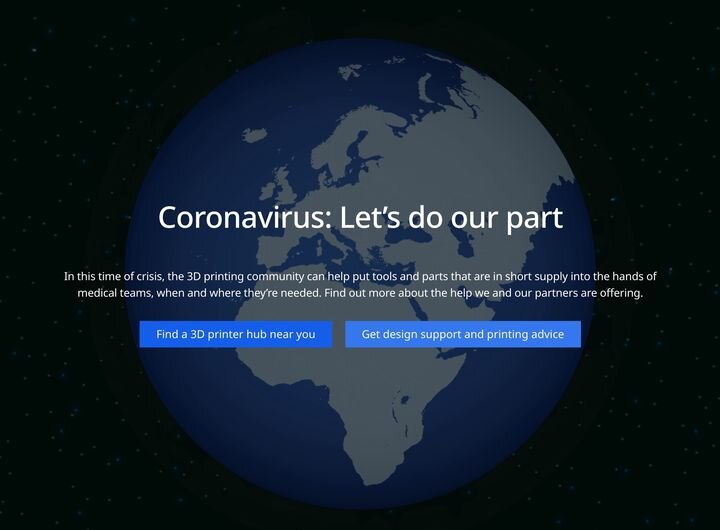
Ultimaker’s front page today shows their new 3D printing network
Our mailbag is filling up with COVID-19 notices of all sorts, but some companies are contributing in unique ways.
Most of the correspondence deals with internal company protocols. A company may say that they are “all working from home”, or “have instituted a stringent safety regime at the factory and are staying open.” Depending on the type of 3D print business, there are different approaches.
At Fabbaloo we are simply working remotely as we always do (minus the travel), but that’s not really an option for a manufacturer. You can’t make products remotely, and these companies have to severely adjust their workflows in order to keep production going.
Most companies are doing something in that regard, while there may be a few that still insist on business as usual. To them, I say that business is most definitely NOT as usual and you should reconsider your strategy for everyone’s sake.
3D Printing Company Aid
Several 3D printing companies have gone above and beyond mere internal adjustments and have organized different types of benefits for the public to help with the crisis.
We’ve already written about the incredible work done by Prusa Research, which has to be the most outstanding in the industry. But there are others also providing interesting services.
MatterHackers put together an extensive list of links to different initiatives and resources working on the problem from different angles. Unlike other lists, this one is short and sweet; it’s easy to find the major resources using it.
Ultimaker Crisis Response
Another company that’s doing something very interesting in this area is Ultimaker, who announced a network of 3D printers.
Ultimaker’s most recent machines are tightly bound to their cloud service. This is done primarily for managing groups of 3D printers within and distributed around an organization, as well as an ability to centralize things like print profiles. They have made it quite easy for a company to manage a fleet of 3D printers.
Those in charge at Ultimaker must have realized they could leverage the networking capability of their equipment across the globe in a way to respond to the crisis.
Some initiatives are trying to “do it all”, resulting in very confusing Facebook groups, Slack channels and discussion lists. Ultimaker has taken a more defined approach by selecting one capability and focusing on that.
![Map of European Ultimaker nodes ready to make COVID-19 equipment parts [Source: Fabbaloo]](https://fabbaloo.com/wp-content/uploads/2020/05/image-asset_img_5eb065daaf649.jpg)
Map of European Ultimaker nodes ready to make COVID-19 equipment parts [Source: Fabbaloo]
It involves their networking capability. Ultimaker has created a kind of locator system for Ultimaker-equipped 3D print services around the world. Thus, if someone in need requires a part or parts quickly manufactured locally, they can find a party close by using Ultimaker’s network map.
Ultimaker says:
“To help the effort, Ultimaker just announced a global network of 3D printing hubs and experts available to hospitals around the world in need of tools and applications as they manage the challenges of the COVID-19 pandemic.
Through Ultimaker.com, medical professionals can locate 3D printers, contact 3D printing experts and create and obtain the parts they need most.“
Their networked 3D print service consists of two parts: the locator system and a design assistance service. They say:
“Ultimaker’s team of designers and application engineers are available to support hospitals that need assistance in designing, printing and testing parts and tools.”
Importantly, they are NOT providing specific 3D model files. The idea here is to simply provide a way to produce the designs once they are created or obtained.
I believe this is a very smart approach by Ultimaker, as they are focusing what they do best: 3D printing. Designing safe and functional medical equipment is far more complex than most people realize and Ultimaker wisely does not want to get into that design space.
I’m hoping more 3D print companies step forward and provide a contribution to solving the crisis. Just make sure it’s something clear and achievable.
Via Ultimaker