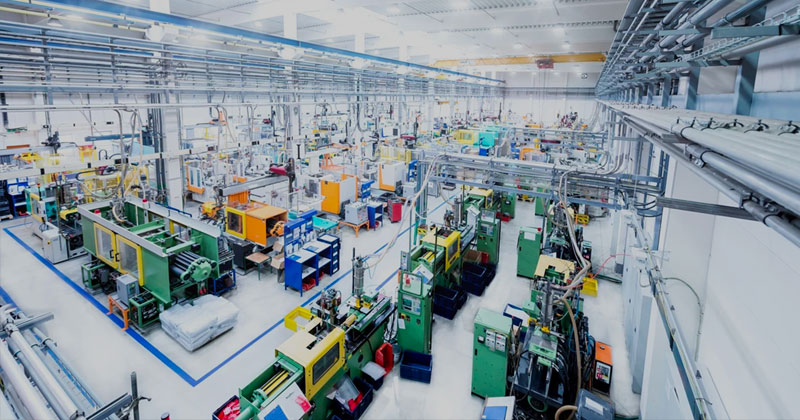
SPONSORED CONTENT
One of the biggest positives of 3D printing is that no tooling is required — but it might just be perfect for making parts including jigs, fixtures, end-use parts, and even tooling.
While additive manufacturing is coming into play for end-use parts and serial production, these types of parts remain largely the purview of traditional manufacturing technologies. High-volume manufacturing is often best served with conventional processes like injection molding that can quickly produce vast quantities of parts. Injection molding, though, like all conventional manufacturing technologies, relies heavily entirely on having a mold (a tool) in place.
Essentium Knowledge Base
In a year without in-person events, much knowledge sharing in the additive manufacturing industry has gone virtual. The team at Essentium stepped up and for months now has been offering valuable information through downloadable guides and free webinars. Earlier this year, for example, the team shared a materials handling guide that details appropriate care of 3D printing materials.
On the webinar front, the team has been focusing on actionable takeaways for the technology. One of these webinars, led by Materials Development Engineer Dr. Tom Mulholland, is titled “Toolmaking With Material Extrusion – Advantages, Materials and Designs.”
The hour-long webinar is well worth the watch, but we’ll take a look at a few of Mulholland’s key points.
Toolmaking With Material Extrusion
Extrusion-based 3D printing is increasingly coming into play for toolmaking.
The rising availability of high-performance materials can create usable tools including molds that are capable of withstanding hundreds to thousands of shots, which offers manufacturers advantages in cost and time-to-tool, as well as potentially reducing indirect costs like inventory and storage.
Among the additive manufacturing companies working to make such tooling more accessible is Essentium. The Texas-based company has been building a reputation as a reliable 3D printing company offering high-performance materials and high-speed machines — and a company that is deeply embedded in and informed about the markets it serves.
Advantages Of 3D Printing For Toolmaking
In contrast to traditionally-made tools — think molds, dies, stamps, — 3D printed tools offer lighter-weight, lower-cost, more quickly made alternatives. So long as the right material is used (more on that shortly), the 3D printed molds can offer a compelling alternative with high agility in terms of supply chain and production time, solid economics, and the ability to quickly produce new designs and iterations.
Additive tooling, as Mulholland explains, is “a natural extension of our capacity for very high-speed printing” that can be used to “dramatically reduce design cycles.” Using high-performance materials that can stand up to processes like injection molding offers a speedier production time, rather than waiting weeks on traditional tooling to be made to test each design iteration.
Design changes and modifications can be quickly 3D printed — much faster, again, than typical turnaround on traditional tooling.
Industry veterans will know that 3D printing still can’t match the tolerances and surface finishes that are typical of an injection mold. However, near, near-net-shape 3D printing, where the tool is printed with the intent to machine the important surfaces to the proper fit and finish, reduces:
- Tool changes
- Repositioning of the part
- Operator time
- Time on valuable CNC machines
- Material use and scrap
3D Printing Materials For Toolmaking
We keep coming back to “high-performance materials” — but what exactly are the criteria that should be considered for selecting these materials?
In short, the top considerations come in the form of mechanical properties, temperature performance, functional performance, and chemical resistance. The first two of these are the most critical for toolmaking, and Mulholland goes in-depth on these considerations. Consider, for example:
- Mechanical properties
- Tensile strength
- Tensile modulus (Mulholland notes as the most important mechanical property for making tooling, as “very high stiffness gives the low deformation needed to maintain tolerances in molded parts”)
- Elongation at break
- Flexural strength
- Flexural modulus
- Izod impact
When it comes to temperature performance, Essentium has a pyramid of engineering plastics to better visualize their offerings, sectioned into amorphous or semi-crystalline polymers. The intermittent use of these materials in environments over 200°C and/or continuous use over 150°C indicates that an application would be best-suited with one of Essentium’s High-Performance or Ultra High-Performance materials. Heat deflection temperature (HDT) and continuous use temperature, that is, are especially helpful indicators.
Some of the specific examples Mulholland points to in his presentation include HTN-CF25 (high-temperature nylon with carbon fiber) being a strong fit for thermoforming, blow molding, and injection molding applications. Semi-crystalline, fiber-reinforced plastics are a good option for these high-temperature and high-pressure uses.
Essentium also has a handy blog post that details some of their materials and typical applications for them; they explain:
- Standard filaments including PCTG and PLA are general purpose materials that offer a good blend of stiffness and impact resistance to provide durability with affordability. Strong enough for lightly loaded fixtures, their low melting points support fast production for things like handheld tools, guides and gauges.
- Nylon and Carbon Fiber-reinforced Nylon filaments such as PA and PA-CF are extremely impact, chemical and abrasion resistant. Nearly indestructible with superior tensile strength and stiffness, they are excellent for low friction gears and bearings, automotive parts, as well as check sockets for prosthetics.
- ESD-safe filaments in our Z Collection consist of a number of non-marring electrostatically dissipative materials specifically formulated for electronic manufacturing applications. ESD-safe filaments in a number of durometers are used to prevent damage to electrical components or circuit boards during assembly, for example, as well as to print tools used in environments with a high risk of combustion.
- Flexible filaments including TPU 95A and TPU 80A are made from thermoplastic urethane rubbers that balance superior elasticity with strength and tear resistance. Excellent for applications requiring a snug yet gentle fit such as soft robotic grips, gaskets and flexible hosing. TPU filaments are also great for masking tools and sneaker soles, and Essentium even offers an ESD-safe version to wrap flexibility and electrostatically dissipative properties into one material.
- High Temperature filaments such as PEEK and high temperature nylons (HTN) are meant for the most demanding applications. An alternative to Delrin, HTN filaments are available in ESD-safe and carbon-fiber reinforced versions to deliver all the benefits of standard nylon materials plus increased temperature resistance and reduced moisture absorption. This allows 3D printed jigs and fixtures to be used in harsh environments where parts are baked in ovens, bathed in chemical processes like electroplating, or exposed to solvents, fuels and hydrocarbons as part of everyday use.
Designs For 3D Printing Tools
Once the decisions have been made to 3D print tools and the appropriate materials to use, there’s only one piece of the puzzle to be finished before actually 3D printing those tools: designing them.
Whether for blow molding, injection molding, vacuum forming, or other means of production, each manufacturing process has its own unique sets of parameters to consider when it comes to designing appropriate tooling. Broadly, though, certain characteristics of 3D printing do lend themselves neatly to these applications.
Complexity of design is much more possible using 3D printing than any subtractive technology. For example, complex molds requiring internal structures like conformal cooling can be easily built up with additive manufacturing, enabling more complex structures within a single part. This goes hand-in-hand with the advantages of additive manufacturing; design for additive manufacturing (DfAM) is principally concerned with leveraging those advantages, after all.
The full webinar is available on-demand from Essentium, as Mulholland goes in-depth into these areas and more with specific examples and detailed explanations.
Via Essentium