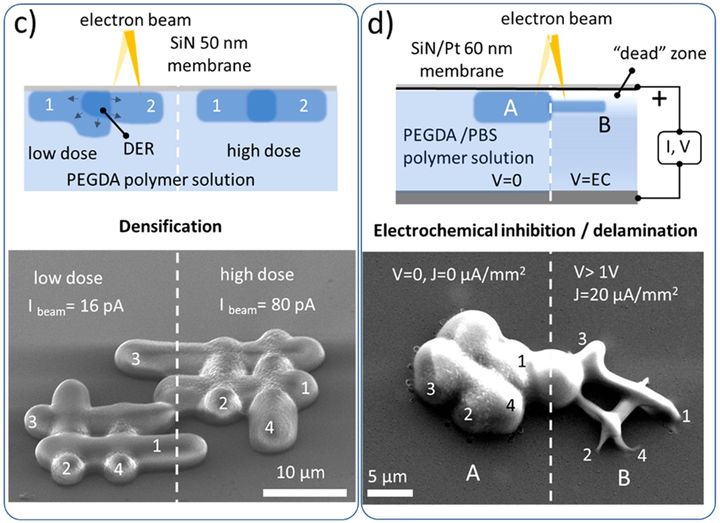
Researchers have developed a method for 3D printing microstructures using X-rays.
In 3D printing there are a few critically important attributes: strength would be one, but resolution is another. For many 3D print applications, high resolution is required. This is particularly important for the production of extremely tiny microstructures, for which there are only a few methods available to do so.
Resolution achievable by a 3D printing process often depends significantly on the active element of the system. For example, in an FFF system, the resolution is mostly governed by the diameter of the nozzle through which soft thermoplastic is extruded. In an SLA system, the maximum achievable resolution is the diameter of the laser “dot” that illuminates the photopolymer resin.
It’s possible to use lenses to shrink the laser dot, but then it’s a game of chemistry to ensure that there is sufficient energy being deposited on a given spot to provoke polymerization. Some systems are able to 3D print microstructures using a two-photon lithography approach.
However, there are limitations and constraints to this process.
Now, researchers at the National Institute of Standards and Technology (NIST) have developed a way to use electron beams, specifically X-rays, to achieve an improved 3D printing process.
To be sure, electron beams have indeed already been used in some 3D printing processes. The most notable has been Arcam, now owned by GE, which used the technique to 3D print metal powder. A few others have used EBM-like processes, including Sciaky.
The fundamental advantage here is to compare the wavelengths of light being used. In SLA 3D printing processes, the typical wavelength is in the ultraviolet range, with the most common wavelength being 405nm. In such systems, the photopolymer resin being used is tuned to react when hit with that wavelength of light.
However, X-rays are different. The range of wavelengths for this type of light are only 0.1-10.0nm, or about 40-4000X times smaller. If such a light source could be made to trigger the photopolymerization effect, then far higher 3D print resolutions could be achieved.
That’s exactly what the NIST researchers were able to do. They designed a hydrogel that was sensitive to this type of energy.
The specific nature of the hydrogel is beyond my level of chemistry, but you’re welcome to read the full paper that describes their setup in considerable detail. One notable complication was the need for a vacuum for the scanning electron microscope, which may deter commercialization of this approach in the future.
Nevertheless, the researchers were able to achieve “writing” at a resolution of 100nm within the hydrogel. For reference, that is equal to 0.0001mm, about a thousand times smaller than the diameter of a human hair.
This research did not produce a 3D printer; rather it confirmed the availability of a 3D printing effect using X-rays that could be incorporated into a 3D printing system design, but that has not yet been done.
Via ACS