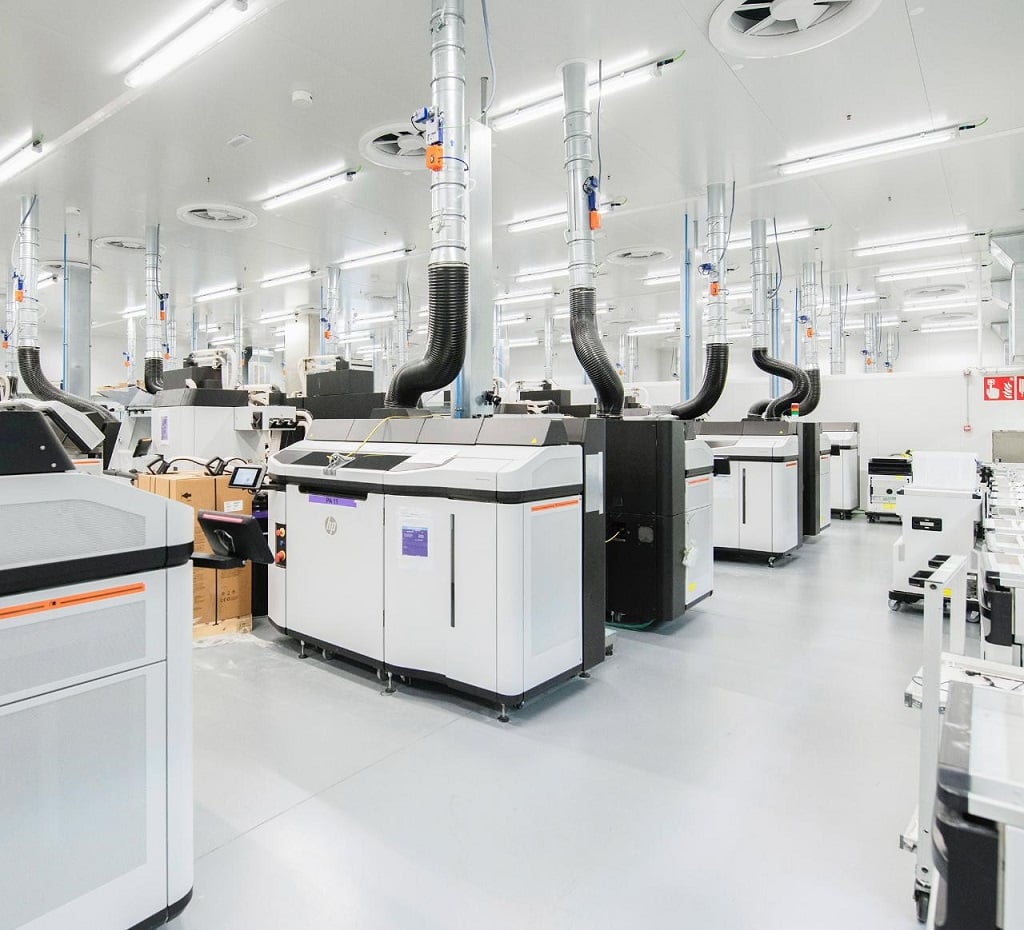
Three pillars of digital manufacturing updates from HP indicate the latest accelerations in automation, software, and services.
As ever, when HP announces an update for its 3D printing business, it’s a notable series of introductions — with a notable cast of partners and customers involved throughout. Ramon Pastor, GM and Global Head of 3D Printing and Digital Manufacturing, HP Inc., notes that these latest announcements align with the company’s overall drive to advance digital manufacturing adoption and capabilities:
“Automation, software, and data are key to delivering mass customization of parts and unlocking the full potential of large-scale additive manufacturing. We are committed to relentlessly improving our capabilities and helping customers optimize and automate workflows, enable compelling new applications, and produce sustainable, high quality parts at scale.”
HP Universal Build Manager Powered by Dyndrite

As so much of additive manufacturing / digital manufacturing must, the announcements begin with software.
For this introduction, HP worked with Dyndrite, the Seattle startup we’ve been following for some time now as they work to develop a new geometry kernel targeting performance, which is truly the heart of 3D printing. The companies announced a strategic partnership this summer, and today’s announcement builds on that foundation.
Much more detail will be revealed at tomorrow’s Dyndrite Day event, but we already know it’s something to get excited about. The new HP Universal Build Manager Powered by Dyndrite leverages both HP’s proprietary software and data innovation and Dyndrite’s Accelerated Geometry Engine — and is, as its name may indicate, universal. The companies explain:
“The new additive manufacturing build manager takes advantage of the GPU-accelerated processing and Python scriptability inherent to Dyndrite’s engine. This combination enables customers to simplify and automate build preparation across their additive manufacturing technologies at supercharged speeds.
HP is committed to supporting multi-platform additive workflows across machine fleets, including HP Multi Jet Fusion, Binder Jetting, Laser Powder Bed Fusion (LPBF), Selective Laser Melting (SLM), Direct Metal Laser Sintering (DMLS), Selective Heat Sintering (SHS), Electron Beam Melting (EBM), Selective Laser Sintering (SLS), Fused Deposition Modeling (FDM), Stereolithography (SLA), Digital Light Projector (DLP), Laminated Object Manufacturing (LOM) and Composite-based Additive Manufacturing (CBAM).”
That is: it’s not just an MJF solution.
Specifically, other technologies that will leverage this software advance include:
“HP and Aconity3D, Aon3D, Aurora Labs, EOS, Essentium, ExOne, Open Additive, Photocentric, Plural AM, Renishaw, and SLM Solutions have committed to exploring ways for the HP Universal Build Manager to support their 3D print systems. Additionally, the open-architecture platform is designed to support interoperability with complementary solutions from leading independent software vendors (ISVs) including Ansys.”
The Universal Build Manager is already in place for real-world use at Cobra Aero and Cobra Moto. These companies need their technology to work at its best, as they design and manufacture propulsion systems for high-intensity applications like racing, fire fighting, and aerospace.
“We are committed to producing the highest quality, most precise engine technology across all of our businesses. The demands on our teams are intense and highly complex. Our ability to deliver safe, top notch products relies on optimizing our systems for both productivity and reliability. We believe the new HP Universal Build Manager Powered by Dyndrite will meet our needs, help us push limits and set the standard across our entire additive manufacturing processes,” said Sean Hilbert, President, Cobra.
Per the announcement, the Universal Build Manager solution includes:
- Universal support for the most widely adopted additive processes
- Support for industry standard CAD and vendor-neutral formats enabling CAD-to-print workflows for all major MCAD applications
- High-performance GPU-accelerated geometry engine helping accelerate computational tasks such as support generation, slicing and tool pathing
- Highly scalable architecture designed to support high-part density builds to optimize throughput and minimize cost
- Powerful Python-based automation engine to capture expert knowledge, process definitions and the ability to streamline workflows and automate repetitive tasks in support of lights-out digital factory solutions
- Extensible plug-in framework making the versatility and power of the HP Universal Build Manager platform accessible to every user, machine manufacturer, and software vendor, facilitating the creation of process specific solutions without having to share potentially sensitive IP
Enhanced 3D Factory Solutions
Next in the innovation queue, HP is introducing new digital HP 3D Factory Services offerings that will offer facilities and equipment analysis, staffing and training, and help in implementing production processes.
The goal here is both simple and profound: scaling digital manufacturing management and quality. Easy to say, that is — and don’t we hear this as a goal all the time right now? — but not so easy to deliver.
Collaboration is of course the best (only?) way ahead for such an ambitious end goal, and this time HP collaborated with AMFG and customers including Henkel.
Enhanced 3D Factory Services “include offerings across facilities and equipment assessment, human capital planning and training, and design and implementation of production processes,” HP explains. “Among the advanced digital services are HP 3D Application Programming Interface (API), HP 3D Process Control, and HP 3D Center.”
AMFG, which itself is so focused on autonomous manufacturing that “our name is our vision”, will enable integration of the HP 3D API for customers like Henkel.
This will enable smoother workflows from end to end as well as allow for real-time status updates on HP Jet Fusion systems so users can work more efficiently with less machine downtime. Henkel, which has been becoming visibly more deeply rooted in the additive manufacturing industry, sees such a step as one that will accelerate innovation — perhaps an overused phrase, but ultimately an incredibly important endeavor.
“Henkel aims to provide innovative solutions for Additive Manufacturing that are accelerated by reliable partners such as HP and AMFG,” said Chris Liddiard, Market Segment Head for Automotive and Industrial Parts, Adhesive Technologies Group, Henkel. “With the help of AMFG to connect to our global infrastructure of Application Centers using HP Jet Fusion printers, we are aiding in centralizing the end-to-end workflows, from initial request to final part production. Armed with this important data, Henkel can better understand and interpret data patterns related to machine utilization, failure rate, geometrical specifications and processing parameters, allowing us to provide better manufacturing services for our clients.”
HP Automatic Unpacking Station
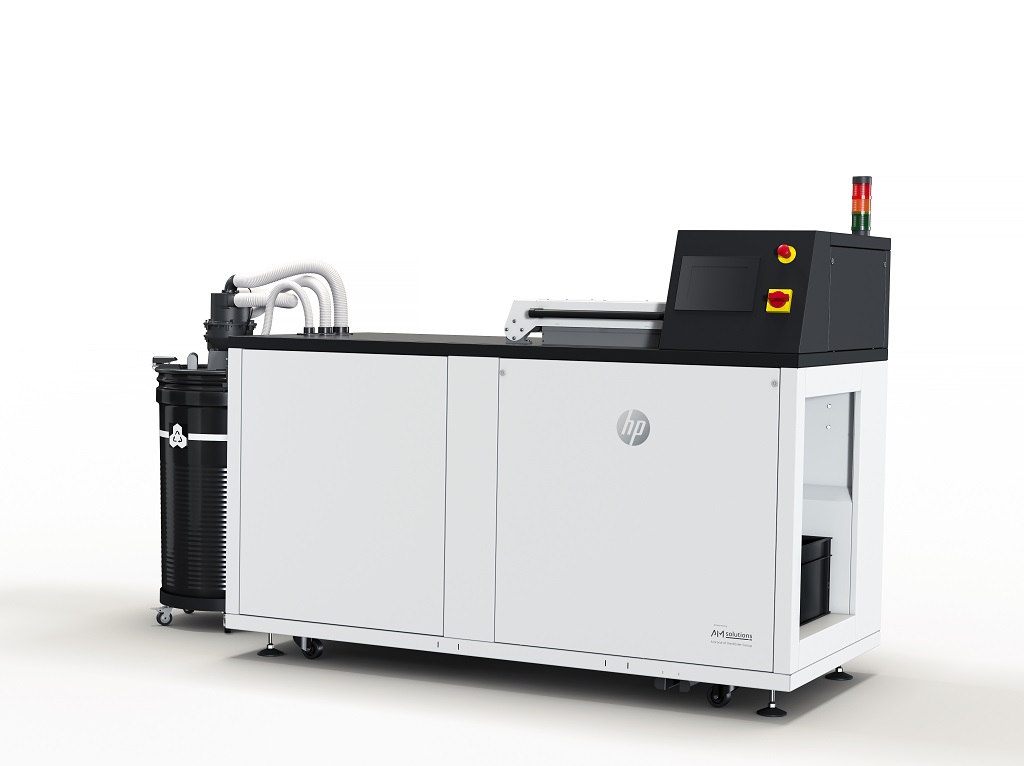
There’s obviously a lot to unpack in all these announcements — and it’s rather fitting that, indeed, the last of the three pillars is regarding a new unpacking station.
This time around, the partnership that led to the development was with Rösler Group’s AM Solutions.
Post-processing is an area of additive manufacturing where automation greatly enhances productivity. Thankfully, in recent years these processes have been gaining attention and garnering new solutions.
This one is the industrial-grade HP Automatic Unpacking Station. Geared for the Jet Fusion 5200 systems, the Unpacking Station is designed to “reduce costs, achieve greater build consistency, and improve part quality across workflows.”
Italy-based Weerg is among the initial customers here. The company operates a full-on fleet of Jet Fusion 5200 systems, so upping the automation is certainly a major step toward better industrial efficiency.
“We are excited for the continued automation advancements from HP and its partners like AM Solutions,” said Matteo Rigamonti, Founder, Weerg. “As we expand our business and manage a growing fleet of HP Jet Fusion systems these enhanced capabilities are designed to help us meet customer demand, and improve our turnaround times for high volume production parts.”
HP Advances
On top of these three key pillars, HP continues its ongoing collaboration with its extensive network of partners to provide innovative new materials and post-processing options for customers.
HP has joined forces with AMT to make its chemical vapor smoothing systems, called PostPro, compatible with HP’s entire portfolio of Jet Fusion printers and materials. And, in addition to its recently announced polypropylene (PP) and Ultrasint TPU enabled by BASF, HP and Evonik announced a co-branded TPA, a high-performance elastomeric specialty powder.
These announcements all trace back to again one central point: HP sees digital manufacturing, including additive manufacturing, as very serious business indeed. They and their partners and customers will continue to drive advances to make these production processes more efficient — which we need to continue to see for additive manufacturing to really begin to realize its full potential in the greater manufacturing industry.
Via HP