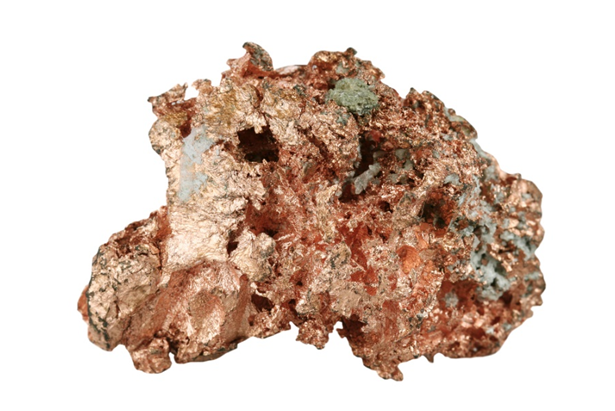
Charles R. Goulding and Peter Favata consider copper’s use in additive manufacturing.
Copper was discovered over 10,000 years ago and is the first metal used by man. Recently an old copper workshop dating back 6,500 years ago was discovered in the Negev desert’s Beer Sheva. This workshop included a small tin furnace for smelting copper. This comes not too long after the discovery of a 1,000-year-old precursor to stainless steel.
Copper plays a large role in one of the major phases in human history known as the Bronze Age. The Bronze Age lasted from 3500- 1500 BCE. During this period bronze, which is created by smelting together copper and tin, replaced all other metal tools because of its added strength and durability as opposed to tools made only from copper. Following the Bronze Age, copper continued to be used throughout history in jewelry, home decor, and cookware just to name a few. Today the number one use for copper is electrical equipment such as wires and motors due to it being a great conductor of electricity and heat.
3D Printing Copper
Metal additive manufacturing has a large part in the industrial world today with multiple advantages over traditional manufacturing. Some of these advantages include shorter production times and reduced operating costs.
Some companies have turned to 3D printing copper in order to produce the inductors for electrical uses. This enables unique designs in CAD programs that can then be printed and sent straight to quality control, greatly shortening the production time compared to traditional methods.
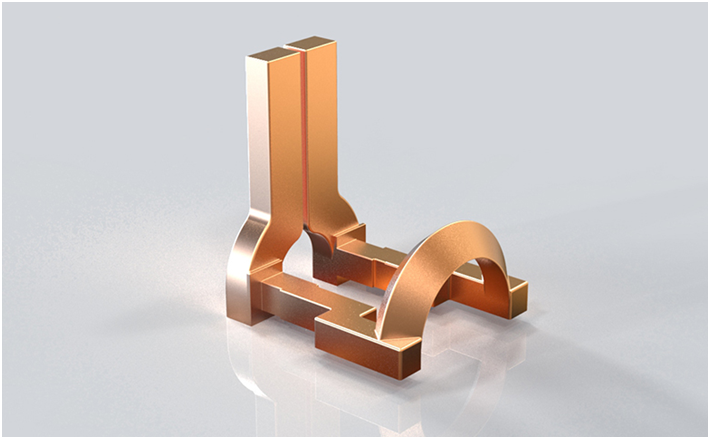
Additional uses for 3D printing copper include wiring and circuit boards. 3D printing allows for extremely detailed designs giving the designer more freedom when needing to create these circuit boards.
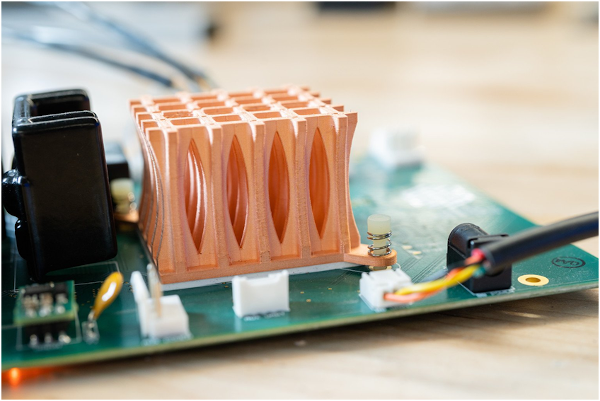
How This Came to Be
3D printing with copper was not easy for the industry to achieve. Even when metal 3D printing technology was improving, experts could not figure out why, when attempting to 3D print copper with the powder bed method, it would crack or the finished product would be deformed and less durable. It was determined that this was occurring due to the conductive properties of copper causing the laser to reflect off the material instead of absorbing the heat that would normally cause the bonding of the metal.
Within the last couple of years, researchers in Germany were able to create a method to efficiently 3D print using copper. It was determined that switching from a traditional infrared laser to a green laser would greatly reduce instances of durability or deformation. They also determined that pre-heating the copper before the print would help prevent any cracking that would accrue due to drastic temperature spikes.
Australia-based SPEE3D has developed its own supersonic spray system to 3D print copper. The company uses copper parts for mining and other hearty applications, and has also recently used copper’s antibacterial properties to quickly 3D print copper coatings for surfaces.
A German electric motor company named Additive Drives GmbH has recently signed a deal to 3D print the copper coils that are a major part of all-electric motors. One benefit of this is reducing down the time it takes to produce a prototype. Traditionally it would take up to seven months to produce a prototype for an electric motor. With 3D printing that gets cut down to only a few days.
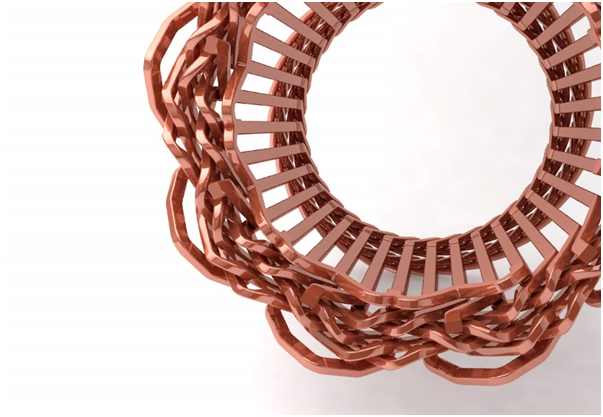
Manufacturers and technical designers utilizing 3D printing copper may be eligible for R&D Tax Credits.
The Research & Development Tax Credit
Whether it’s used for creating and testing prototypes or for final production, 3D printing is a great indicator that R&D credit-eligible activities are taking place. Companies implementing this technology at any point should consider taking advantage of R&D Tax Credits.
Enacted in 1981, the now permanent Federal Research and Development (R&D) Tax Credit allows a credit that typically ranges from 4%-7% of eligible spending for new and improved products and processes. Qualified research must meet the following four criteria:
- Must be technological in nature
- Must be a component of the taxpayer’s business
- Must represent R&D in the experimental sense and generally includes all such costs related to the development or improvement of a product or process
- Must eliminate uncertainty through a process of experimentation that considers one or more alternatives
Eligible costs include US employee wages, cost of supplies consumed in the R&D process, cost of pre-production testing, US contract research expenses, and certain costs associated with developing a patent.
On December 18, 2015, President Obama signed the PATH Act, making the R&D Tax Credit permanent. Since 2016, the R&D credit can be used to offset Alternative Minimum Tax (AMT) or companies with revenue below $50MM and, startup businesses can obtain up to $250,000 per year in cash rebates that can be applied directly to payroll taxes.
Conclusion
With continuous improvements in 3D printing copper, the technology is becoming more accessible than ever. As 3D printers and materials become more affordable there is the opportunity for electricians to print parts on-site for repair instead of waiting for parts from original equipment manufacturers. The added freedom and speed of production using 3D printing will enable copper to continue its storied innovation history.