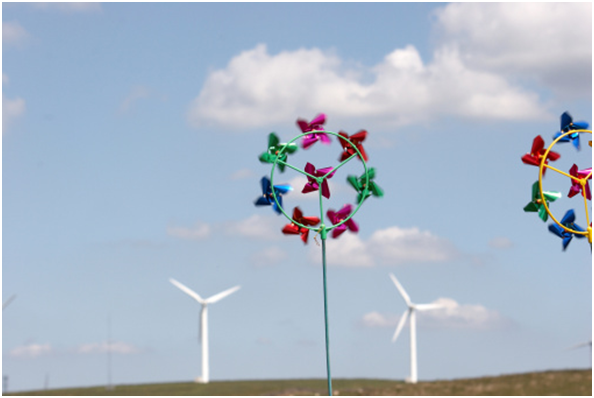
Charles R. Goulding and Preeti Sulibhavi consider a link between three leading companies leaning on 3D printing.
Mads Nipper, the CEO of the world’s largest pump manufacturer Grundfos, is going to become the CEO of Ørsted, the biggest offshore wind developer. Ørsted has announced that it wants to become the world’s first “green super major.”
Before Grundfos, Nipper had spent more than two decades at Lego, rising to CEO. What is fascinating for the 3D printing community is that despite being in entirely different businesses, all three companies are the largest in their respective industries and make extensive use of 3D printing.
3D Printing at Grundfos
Grundfos has stated that 3D printing enables them to:
- Take design time down from two months to two days
- Utilize entirely new advanced materials
- Customize products to meet customer’s specific needs
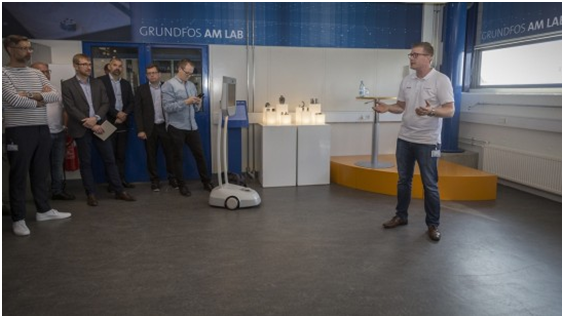
3D Printing at Lego
Mads Nipper is given credit for being part of the team that transformed LEGO from near financial collapse in 2003 to the huge success it is today. LEGO utilizes 3D printing in more ways than one would suspect. A wide variety of LEGO 3D printing models are available, which enable future designers, architects, and engineers to concurrently learn conventional design concepts and work on their 3D printing skills. 3D printed LEGO pieces include super-sized figures and inventive variations of existing products.
3D Printing at Ørsted
We have recently published Fabbaloo articles about 3D printing use at Ørsted and the sale of its oil and gas business to INEOS, in pursuit of its alternative energy transformation. 3D printed metal parts are first digitally visualized, computer-simulated, then printed on a metal substrate for a non-thermal variable, more homogenous metal part. This is where DTU Mechanical Engineering, the Danish Technological Institute, 3D printing, and Ørsted come together to advance wind energy technology.
Research and Development Tax Credits are available for the eligible U.S.-based, 3D printing pump, toy and windmill activities that companies engage in.
The Research and Development Tax Credit
Whether it’s used for creating and testing prototypes or for final production, 3D printing is a great indicator that R&D Credit eligible activities are taking place. Companies implementing this technology at any point should consider taking advantage of R&D Tax Credits.
Enacted in 1981, the now permanent Federal Research and Development (R&D) Tax Credit allows a credit that typically ranges from 4%-7% of eligible spending for new and improved products and processes. Qualified research must meet the following four criteria:
- Must be technological in nature
- Must be a component of the taxpayer’s business
- Must represent R&D in the experimental sense and generally includes all such costs related to the development or improvement of a product or process
- Must eliminate uncertainty through a process of experimentation that considers one or more alternatives
Eligible costs include US employee wages, cost of supplies consumed in the R&D process, cost of pre-production testing, US contract research expenses, and certain costs associated with developing a patent.
On December 18, 2015, President Obama signed the PATH Act, making the R&D Tax Credit permanent. Beginning in 2016, the R&D credit has been used to offset Alternative Minimum Tax (AMT) for companies with revenue below $50MM and, startup businesses can obtain up to $250,000 per year in payroll tax cash rebates.
Conclusion
The rise of the 3D printing industry is evident when three industry leaders in three different business sectors make extensive use of additive manufacturing technology. No one needs to convince Ørsted’s new CEO about the potential of 3D printing.