The implant in a model of the patient’s skull [Image: Sanjay Pathak]
A recent case study out of India highlights the low-cost benefits of 3D printing to create personalized medical implants.
Healthcare costs are a significant factor for many individuals around the world. Newer technologies are helping more affordable solutions come to those who need them most.
While most of the time when we talk about 3D printing for medical implants we’re discussing direct 3D printing of implantable devices, this time we’re looking to a more standard workflow bringing in advanced technology: molding.
3D printed molds are being used across a variety of applications, allowing new geometries — including patient-specific — that previously would have been hard to create via mold. Many molds are used for higher-volume uses (think injection molding), rather than one-off creations, due to the costs involved with creating the molds themselves.
Personalized Implant
Sanjay Pathak of Global Health Care in New Delhi, India shares with us a story about a young man who has recently gotten a new lease on life.
The young man “lost most of his forehead and frontal skull bone,” Pathak explains, following a surgery to help him recover from an accident. Local surgeons had made him a conventional bone cement implant — but the procedure was not successful and the implant had to be removed.
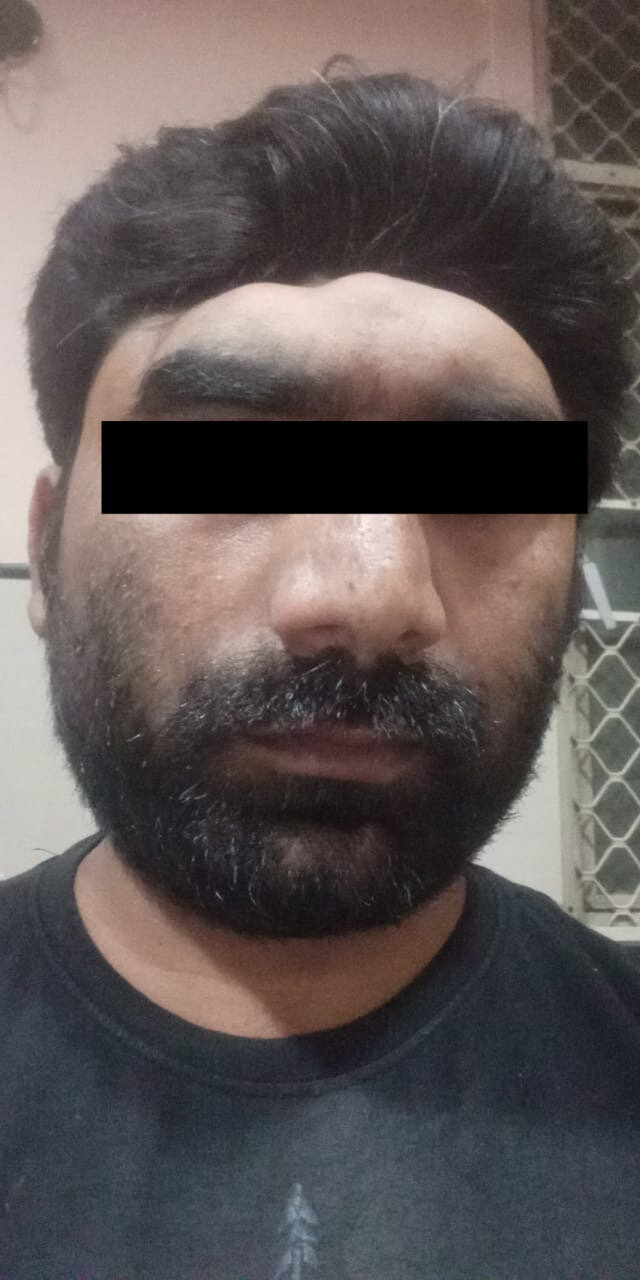
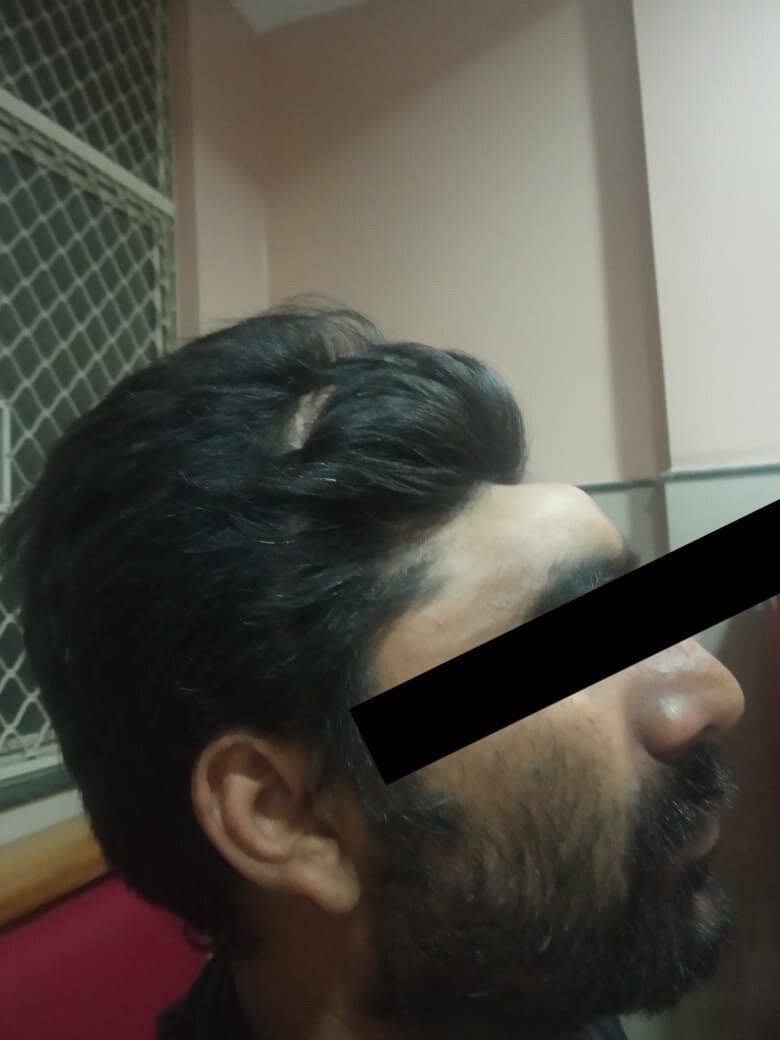
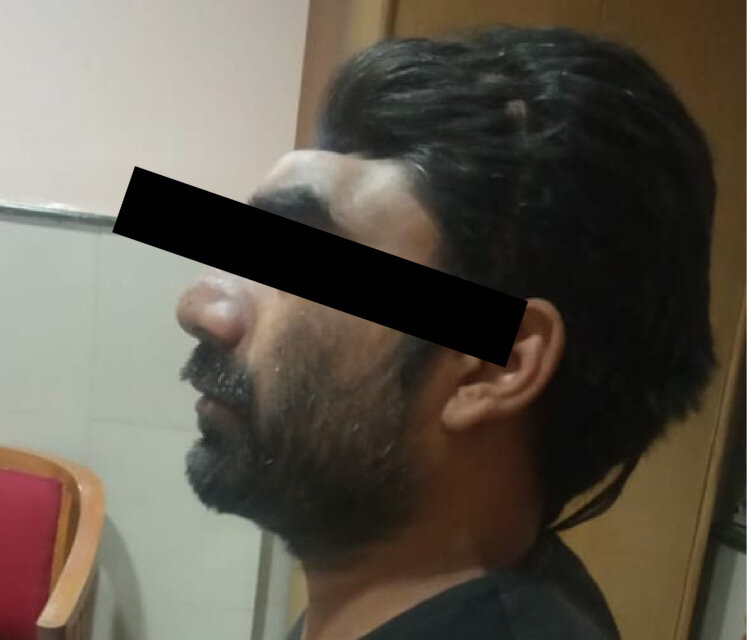
[The patient, after having an unsuccessful implant removed / Images: Sanjay Pathak]
“[The] patient is poor and could not afford a titanium or PEEK/PEKK implant,” Pathak tells us.
Often these higher-durability materials are the go-to solution of choice for 3D printing, with which Pathak and his team have developed great expertise. The team has previously created personalized titanium spinal and hip implants, seeing good results in their patients’ recovery. This time, though, titanium wasn’t an option.
“I created a new gentamicin infused bone cement implant,” Pathak says of this case. “This was done by printing a PLA implant, use it as master to create a silicone mold for making the bone cement implant. The implant was created super fit in sterile environment in a dental laboratory. It fitted like lock and key and surgeons were very happy. This case was done in All India Institute of Medical Sciences, New Delhi.”
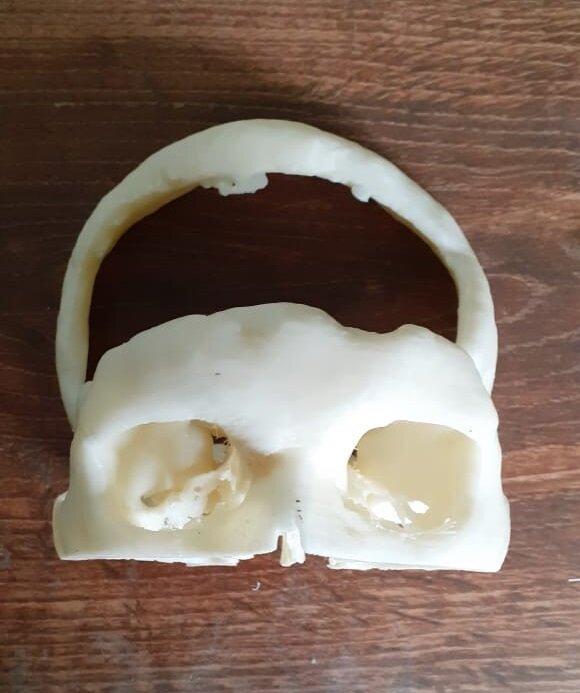
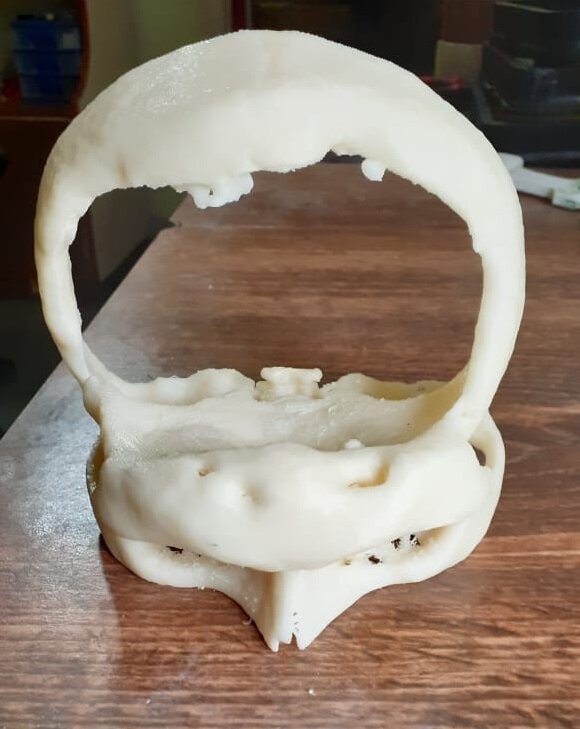
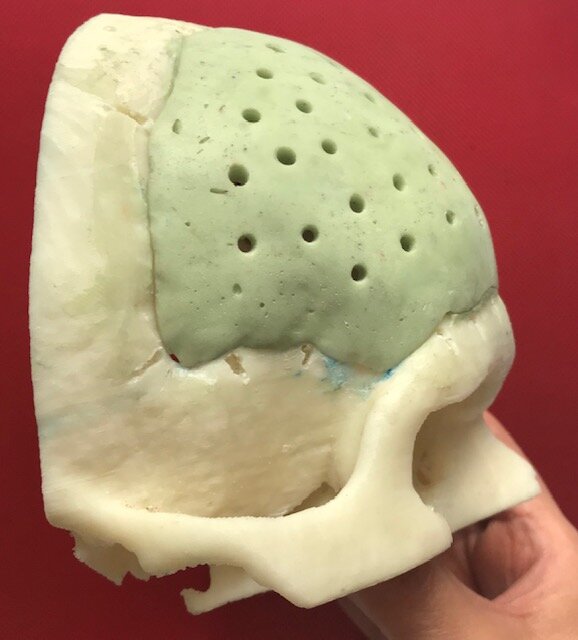
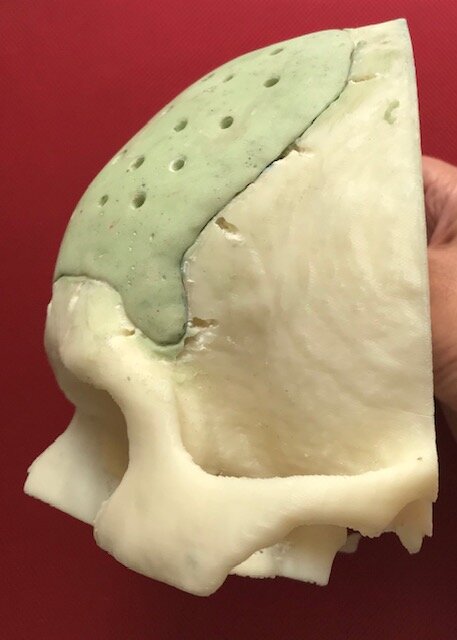
[A model of the patient’s skull prior to (above) and with (below) the molded implant / Images: Sanjay Pathak]
While Pathak also acknowledges, “I know this is not uncommon nowadays,” that very point is part of what makes the case remarkable. That 3D printing is becoming more of a go-to medical solution around the world is notable.
As for the patient?
His total project cost was less than $1,000 — and, Pathak reports, “the patient is happy and plans to get married soon.”
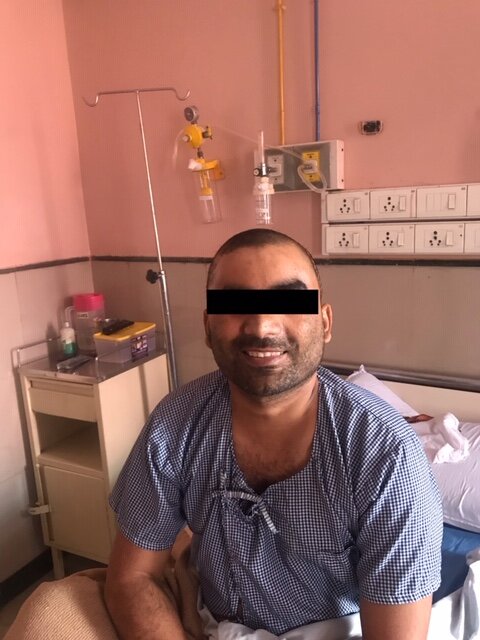
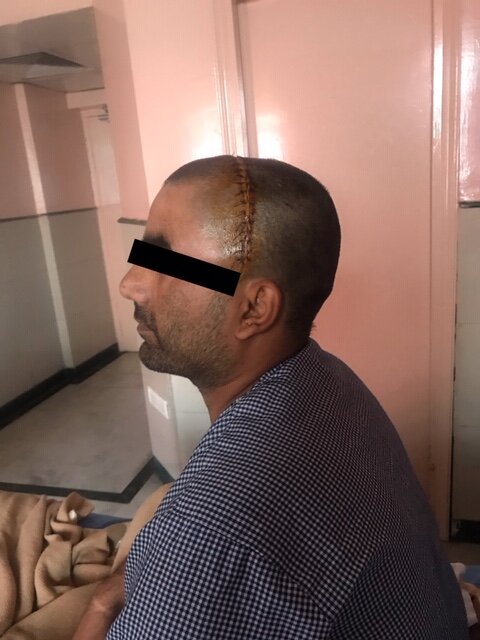
[The patient, happier in recovery with his well-fitted cranial implant in place / Images: Sanjay Pathak]