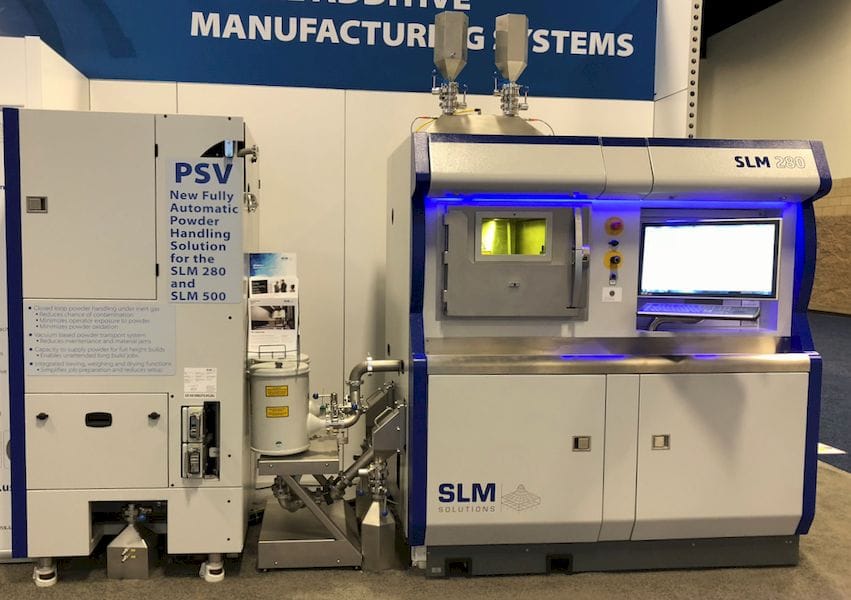
SLM Solutions has been slowly adding ease of use features on their 3D metal printing systems.
The company currently markets three base models using their selective laser melting process (hence “SLM”) that vary in build volume. The numbers in the SLM 125, SLM 280 and SLM 500’s product names refer to the length of the maximum axis on their respective build volumes.
The midrange model SLM 280 is their most popular selling system, as its build volume and pricing seems to match best with clients.
Recently they’ve been adding a number of feature to their systems to make things easier to operate. While they’ve already increased the printing performance, by, for example, raising the laser power levels and including dual lasers for far faster print speeds, there is a lot more to deal with when operating 3D metal printers. They’ve also devised a dual-direction recoating system that speeds printing by not requiring a second movement after each layer of powder is applied.
Powder management is a key aspect of most 3D metal printing operations, as the purity of the powder directly relates to the quality of the prints made with it. It’s critical to not expose the powder to the environment where it could quickly be contaminated by humidity or even oxygen in the air.
In past years, this was a problem left to the operator, who had to rely on third party solutions to solve the issues. Now SLM Solutions markets their own powder management system, the modular PSV, which can be directly attached to any of SLM Solutions’ units.
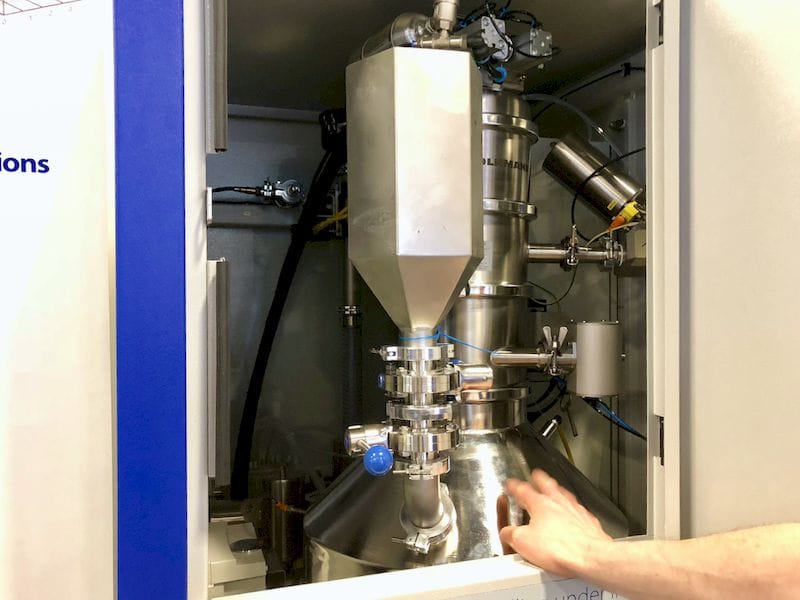
The PSV enables closed loop control of the powder within the SLM machine throughout the entire printing process. This ensures that the powder is not only secured from the environment, but also is properly reused by an included ultrasonic sieving system. Conveyor systems move powder between three locations in the system: the printing reservoir, the sieve and powder storage.
But powder management is not the only ease of use improvement SLM Solutions has recently added. They’ve also included an alert system for operators to be notified when prints are complete.
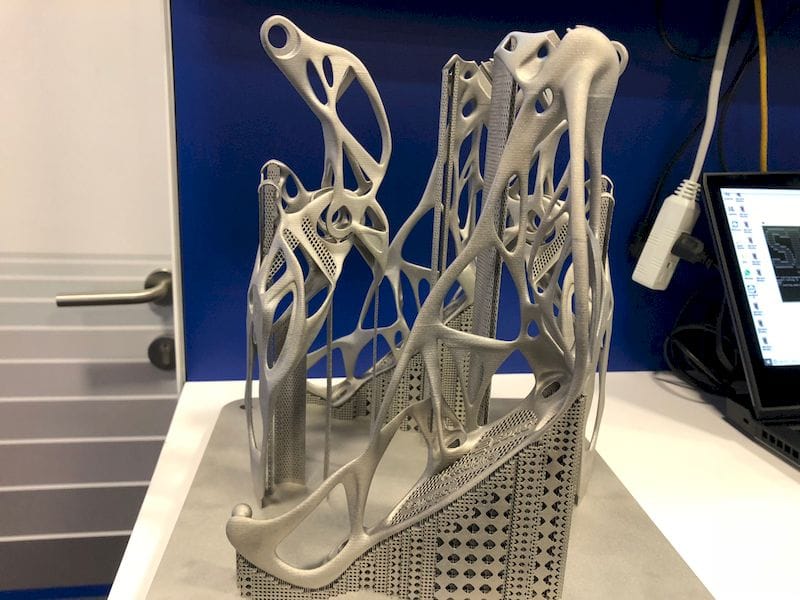
What’s quite fascinating is their software improvements, one of which is the development of new types of support structures. Here you can seen an example of their supports.
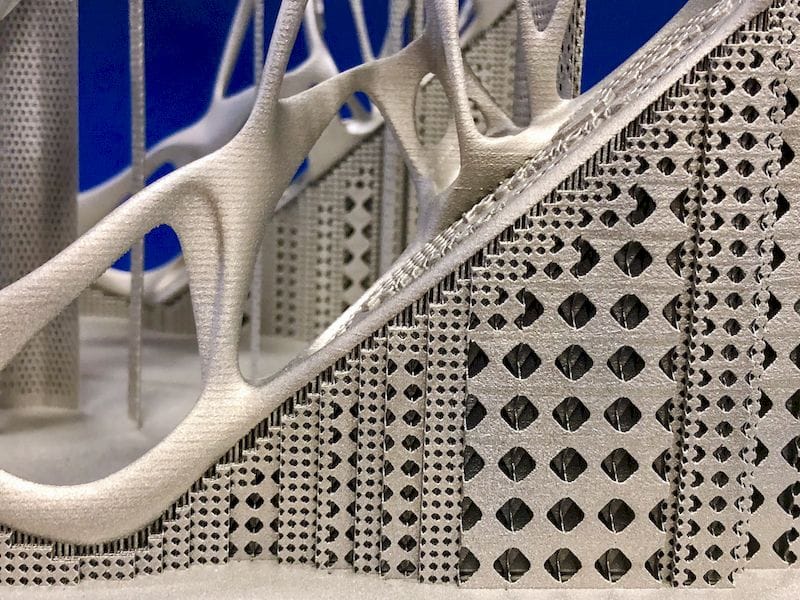
In this detailed image, you can see how the support structures vary in the amount of material used, as well as a very thin attachment layer on the actual object. This should make removal and post processing finishing much easier.
Part quality remains excellent, as you can see in this closeup image of the top of this sample print.
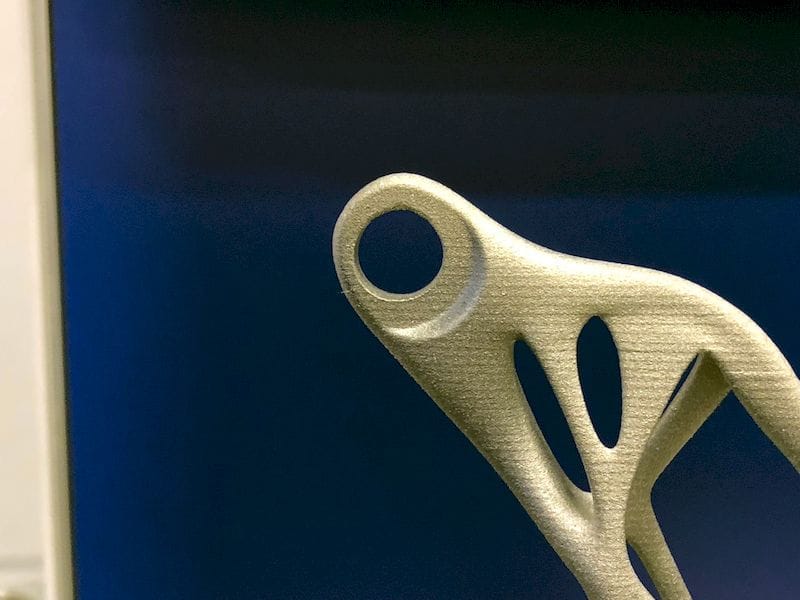
So it seems that SLM Solutions, like several other 3D metal printer manufacturers, is spending considerable effort to simplify the life of 3D printer operators. In the long run, this makes use of their equipment more economical and thus could lower prices for clients, potentially opening up the opportunity for more industries to make use of 3D metal printing.
Via SLM Solutions