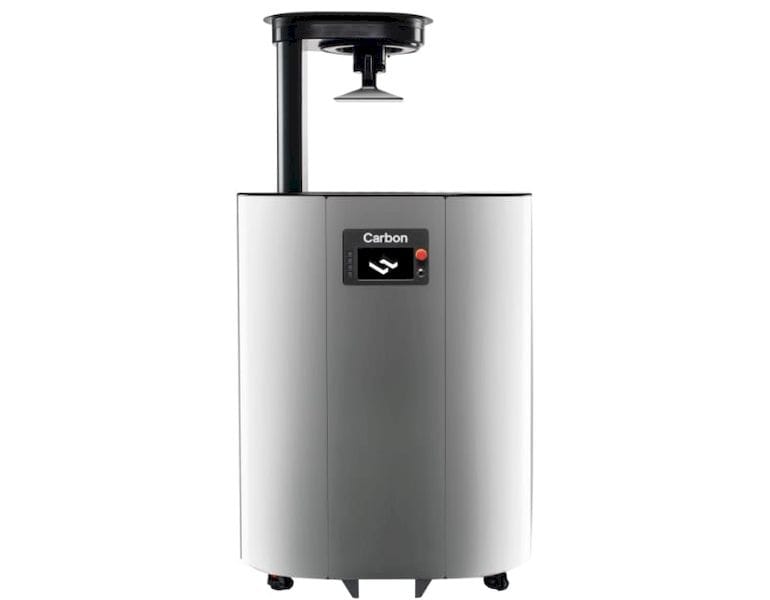
There’s a trend in 3D printing these days: accessories.
For many years this was not the case, as 3D printer manufactures focused on improving the 3D printer itself. Printing faster, with different materials or at a higher level of quality seemed to be where the energy was being spent in the R&D labs of most printer manufacturers.
But then it seems that at least some of the manufacturers began to focus on other aspects of the use of their equipment, perhaps through customer feedback.
It turns out, to the surprise of those unfamiliar with 3D printing, that the actual “3D printing” part of 3D printing was not the only activity required to complete the job. And in some cases, it was one of the less busy activities.
3D prints are definitely not “done” when they come out of the printer. They usually require post processing, and that can even be in multiple steps. Often these steps have been done manually.
Manual work is generally undesirable because it can be expensive, slow, unreliable and presents inconsistent results, particularly if multiple people are involved.
I suspect that many 3D printer manufacturers have received feedback from their clients on this phenomenon. In some cases it’s likely the manufacturer has lost sales because the client could not justify the expense of post processing.
To that end several companies have now introduced various types of automation systems to accompany their base 3D printer products. They have also been introduced by third party companies, some of which have re-purposed their equipment for use in the 3D printing realm.
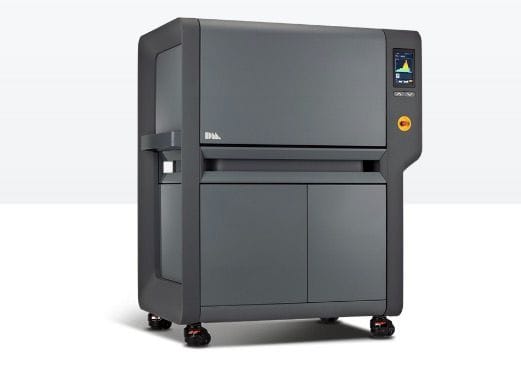
Desktop Metal has a sintering furnace to complete the process of printing metal objects on their Studio equipment. This is a required step that could be done by equipment from existing furnace providers, but instead the company has developed a slick sintering furnace that directly integrates into their build workflow, making a far less onerous experience for their users.
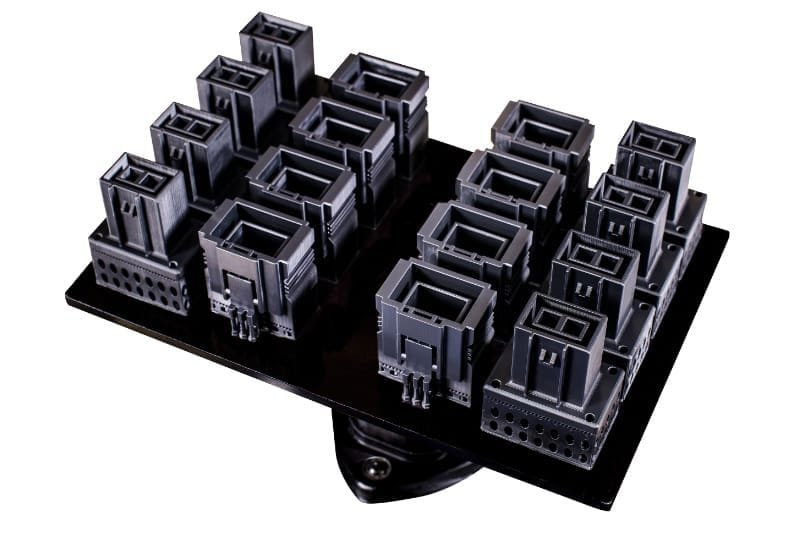
Carbon has a specialty washer, the Carbon SPW, that cleans stray resin from their 3D prints. The company says it can cut down cleaning time by “50%, maybe even 75%”.
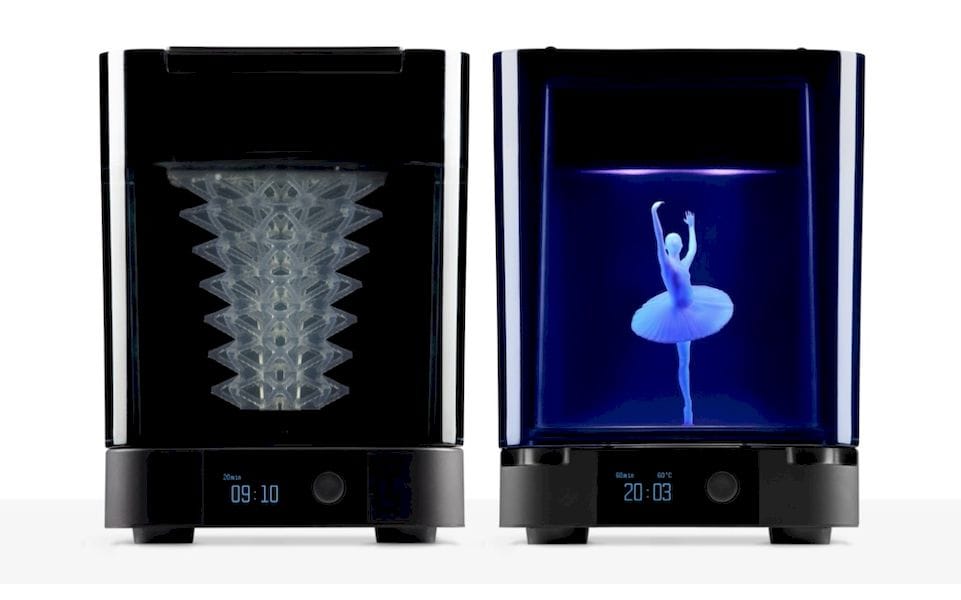
Formlabs introduced a pair of accessory machines: a resin washer and a UV curing station, both of which are highly automated and operate at the touch of a button.
And other companies have been doing similar things to simplify the workflow of using their equipment.
I believe this is a sign of a maturing industry, one where the thinking is not only for the base product, the one from which the company started, but far deeper into the minds and processes of their customers. They’re solving serious business issues by providing this type of automated equipment.
Such equipment tends to appear on the higher priced equipment, but in many cases the same types of workflows exist on desktop equipment at lower costs. It’s possible we may an increasing number of accessory devices start to appear in that market segment to join Formlabs’ inexpensive add-ons.
Via Carbon, Formlabs, Desktop Metal