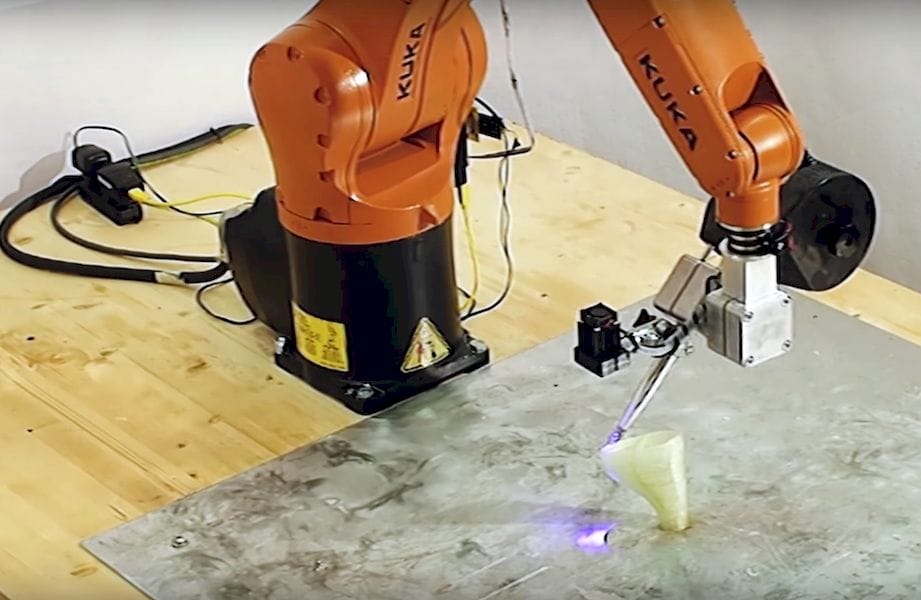
Italy-based Moi offers a unique style of 3D printing.
The company, which launched in 2013 with a new concept for 3D printing that involves continuous fiber, robotic motion and thermoset materials. After years of development, the company has refined their system into a highly usable technology that is able to produce object/material combinations few, if any, other technologies can achieve.
They seem to have combined several 3D printing techniques into one unified system. Robotic 3D printing has been used occasionally in other systems as an alternative to the common cartesian or delta motion systems.
Continuous fiber has also been deployed by several companies, most notably Markforged, who integrated continuous fiber into their cartesian thermoplastic extrusion equipment. While some materials providers have produced filaments containing chopped fibers, these somewhat stronger materials are no match for continuous fibers.
Finally, thermoset materials differ from thermoplastics that make up the filament family of 3D printing materials. Thermoplastics can be softened and reformed merely by raising them to the appropriate temperature. However, this means that they are often suitable for applications involving higher temperatures.
Thermosets, on the other hand, are quite different. They are liquid until stimulated, when they solidify permanently, and are thus more resistant to heat. There are various forms of thermosets, including radiation as is used in SLA-style 3D printers, or mixing two materials, like epoxies.
Moi uses all three of these technologies together, a combination I’ve not seen in any other approach.
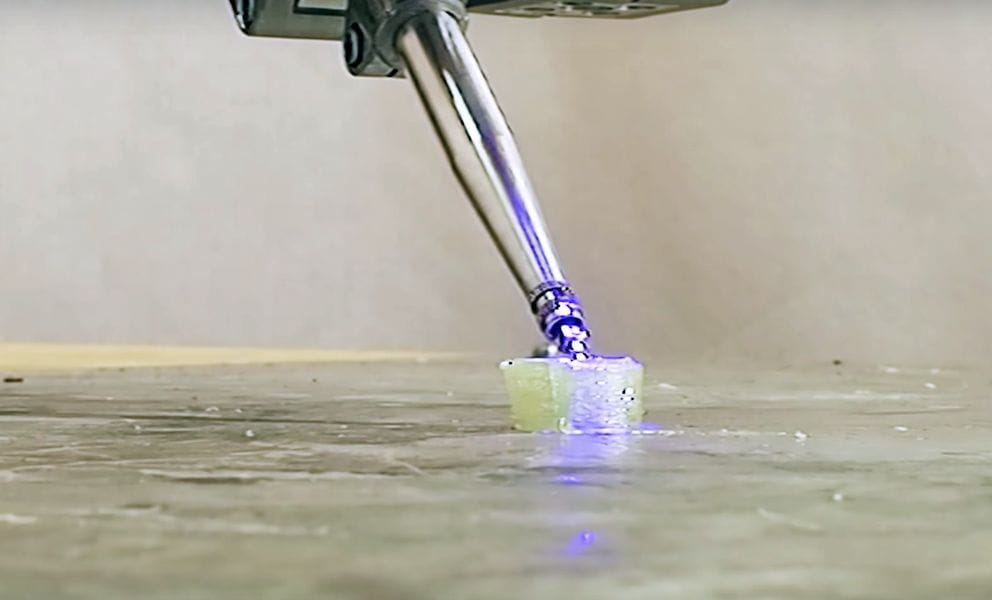
The result is a robotic system that can print arbitrary shapes in thermoset material, with embedded continuous fibers.
Moi says the fibers can be various types, including carbon fiber, glass or even bamboo.
And the thermosets offer far more choice. Moi offers materials with differing mechanical properties, heat and chemical resistance and weight. You can simply choose the materials that best match your application.
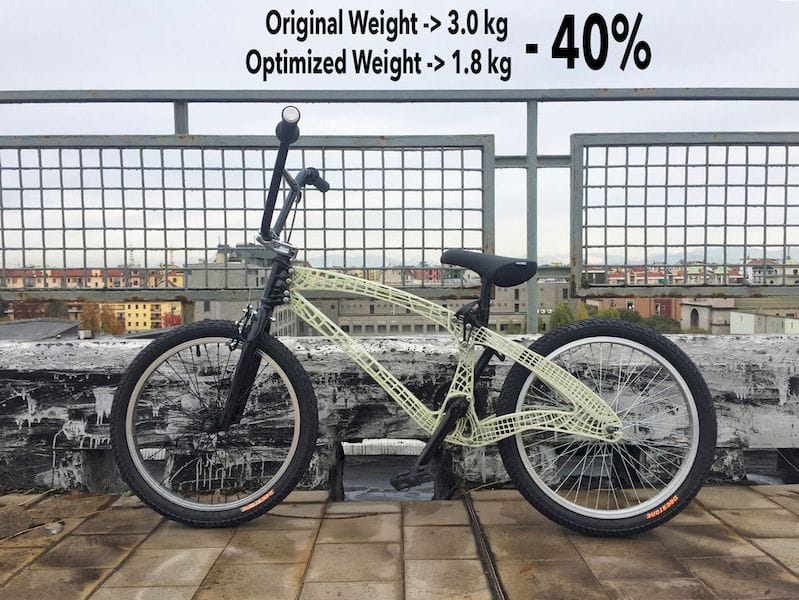
There are a number of advantages to this system as compared to traditional composite techniques. Traditional methods typically use molds or cores to lay fibers and resins on, but no such structures are required with Moi’s technology, as the parts are simply 3D printed directly.
This offers the possibility of creating composite objects with geometries that are quite impossible to make with other composite approaches. Beyond the basic shape of the object, it is also possible to orient the paths of the continuous fibers to best match your application’s needs.
There’s another advantage to Moi’s approach: the robotic motion system means the objects being printed can be of larger size. What size? The size of the robot’s reach, at least initially. A larger robot with longer reach could obviously 3D print bigger parts. In theory one could even move the robot to print even larger objects of arbitrary size. But I don’t think Moi is quite at that stage yet.
Their technology seems to be successful, if you count the partnerships they’ve managed to develop. They have a partnership with Kuka, one of the world’s largest manufacturers of robotic systems. I’m sure Kuka would like Moi’s technology to expand, as it could mean additional robot sales for them.
Moi has also partnered with Autodesk, the maker of 3D software. I believe this is a very important partnership for Moi, as Autodesk might be able to provide more sophisticated control systems for the robotic movement.
Moi provides an end-to-end experience, from consulting on the original model intent all the way to actual printing of the part.
Via Moi