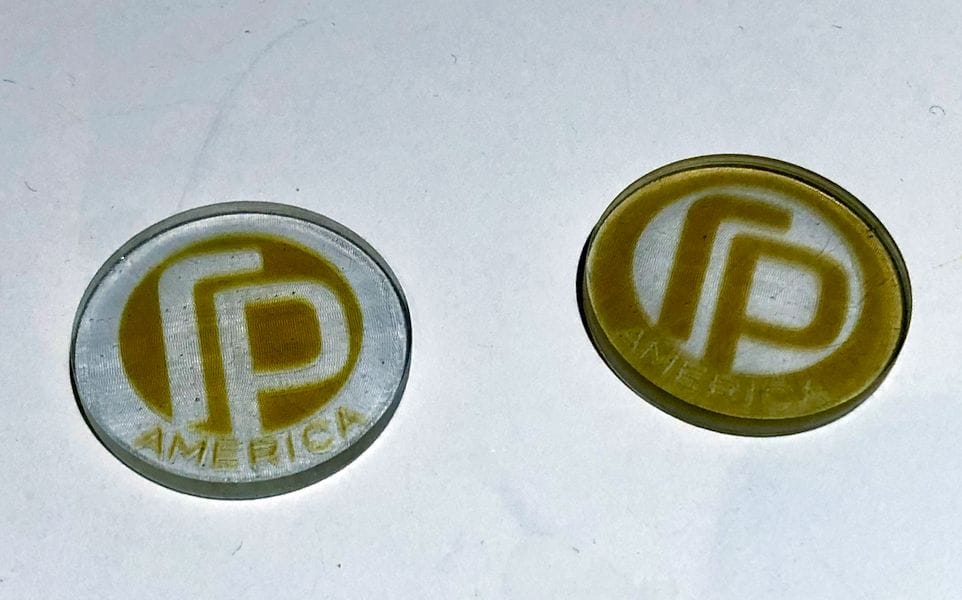
There seems to be rising interest in 3D print marking schemes.
First we saw Rize’s announcement of a system to enable formal marking on 3D printed parts produced by their equipment. The idea was to embed marks that indicate the serial number, model, version number, part name or other possibly critical information about the part.
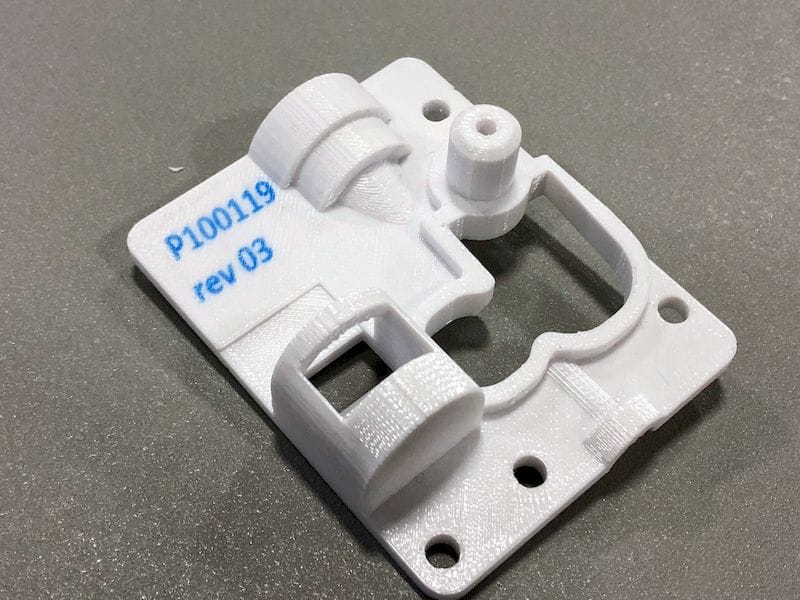
Now we see that another company is at least experimenting in this direction. Union Tech, the China-based company now opening operations in North America, has discovered a method for introducing marks with at least some of their equipment in certain situations.
While Rize literally uses ink to deposit a different color in their prints, Union Tech’s approach is quite different.
Their equipment uses the standard SLA process in which photopolymer resin is illuminated by a UV laser create solid objects. This means they have no opportunity to introduce other colors by ink or alternate materials: there’s only one liquid in the resin tank at a time.
So how did they produce the samples above?
It was apparently done by an ingenious software tweak that causes the laser to linger a bit longer over certain areas during printing. The longer exposure to energy essentially “over cures” the photopolymer, and produces this brown color effect.
They explained there are two approaches they can use. One involves using two separate STL files, one representing the overall model and the other representing the marking area. When printing the two overlain, the marking STL is assigned over curing parameters.
The other approach is to repeat burning on the marking area, in a manner similar to how laser cutters redo a spot if it hasn’t cut through.
This works because the material used in this case is otherwise transparent. In fact, the machine’s normal operation would be to tune the 3D printing parameters to ENSURE the result is transparent. However, this approach does the opposite, under control.
I’m not sure if they could use this approach with non-transparent materials, as the brown color seems to be easily seen through the transparent material. In this example there appears to be a layer or two of over exposed resin, surrounded by transparent material.
Non-transparent materials might be used in this way if the over exposure occurred on the surface layer.
Of course, a technical demonstration like this does not make a product. This would simply be the trigger for development of an entire system that might, for example, automatically generate and assign unique serial numbers for parts being printed, among other similar functions. I don’t believe Union Tech has gone that far, but there is no reason for them not to.
Via Union Tech and RP America